Discover Premium Ceramic Products | Durability & Elegance United | Advanced Ceramics
PRODUCT PARAMETERS
Description
Introduction of Boron Carbide Ceramics
Boron carbide ceramics is an inorganic, non-metallic material with carbon and boron as its main components, and its chemical formula is B4C. Since its discovery in the early 20th century, this material has attracted a great deal of attention because of its unique physical and chemical properties. Boron carbide ceramics have an extremely high hardness, second only to diamond and cubic boron nitride, which makes it important in the field of wear-resistant materials. It also exhibits excellent corrosion resistance, high-temperature stability and low-density properties, attributes that make it ideal for the manufacture of bullet-proof vests, nozzles, bearings and other mechanical components that require high wear resistance. Boron carbide ceramics can also be prepared in a variety of shapes and sizes through different processes to meet the needs of different industries.
Characteristics of Boron Carbide Ceramics
Boron carbide ceramics are known for their excellent performance characteristics, starting with their ultra-high hardness and strength, which makes them resistant to severe abrasion and scratching, making them ideal for use in cutting tools and abrasives. Secondly, the material possesses excellent chemical stability and is less likely to react with chemicals such as acids and alkalis, even in extreme environments, making it widely used in certain key components in the chemical industry. In addition, the superior thermal stability of boron carbide ceramics and their ability to maintain structural and property stability at extremely high temperatures makes them one of the key materials in the aerospace and nuclear industries. Finally, it is worth mentioning its lightweight properties, which, due to its low density, make boron carbide ceramics an ideal option for application scenarios that require light weight but high strength. Together, these characteristics give boron carbide ceramics a wide range of applications.
(Customized High Hardness Boron Carbide B4C Ceramic Block for Sand Mill)
Specification of Customized High Hardness Boron Carbide B4C Ceramic Block for Sand Mill
Custom-made High Hardness Boron Carbide (B4C) Ceramic Blocks for Sand Mills are crafted for severe toughness and precision. These blocks are made from boron carbide, a product recognized for its outstanding firmness and resistance to wear. The item is perfect for industrial applications requiring durable performance under extreme conditions.
The ceramic blocks have a Vickers hardness score of over 30 GPa, making them among the hardest products offered. This hardness guarantees minimal wear throughout high-intensity grinding procedures. The density ranges in between 2.50 and 2.52 g/cm TWO, supplying a balance in between toughness and light-weight design. The composition is 99% pure boron carbide, with trace elements very carefully controlled to maintain consistency.
Modification alternatives consist of differing block sizes and shapes to fit particular sand mill machinery. Thickness can be changed from 10 mm to 100 mm. Surface area finishes are customized to satisfy functional requirements, from rough textures for bond to polished surfaces for decreased rubbing. Tolerances are kept within ± 0.5 mm to make certain smooth assimilation with existing systems.
Thermal stability is a key feature. The blocks stand up to temperatures approximately 600 ° C without shedding structural integrity. This makes them ideal for procedures involving heat generation. Chemical resistance is an additional advantage. Boron carbide does not respond with the majority of acids, alkalis, or organic solvents, guaranteeing dependability in destructive settings.
The blocks are made making use of advanced hot-pressing strategies. This method boosts thickness and gets rid of porosity, resulting in an uniform microstructure. Examining includes rigorous look for cracks, dimensional precision, and solidity consistency. Each batch undergoes quality recognition to satisfy market requirements.
Applications expand past sand mills. These ceramic blocks are made use of in shot blowing up nozzles, ballistic armor, and accuracy cutting devices. The emphasis continues to be on supplying an economical remedy for markets needing wear-resistant parts.
Benefits consist of prolonged service life, minimized downtime for substitutes, and improved operational performance. Compatibility with unpleasant media like silicon carbide or alumina boosts adaptability. Customized orders commonly have a preparation of 4-6 weeks, depending upon specs.
The product is packaged firmly to prevent damages throughout transportation. Technical support is available for assimilation guidance and performance optimization.
(Customized High Hardness Boron Carbide B4C Ceramic Block for Sand Mill)
Applications of Customized High Hardness Boron Carbide B4C Ceramic Block for Sand Mill
Customized high firmness boron carbide (B4C) ceramic blocks serve vital roles in sand mills. These devices grind and spread materials in sectors like paints, coatings, and electronic devices. Boron carbide sticks out for its extreme firmness. It ranks among the hardest materials internationally. This home makes B4C blocks very resistant to use. Sand mills process abrasive slurries. Typical metal parts wear down rapidly. B4C ceramic blocks last much longer. They reduce maintenance demands and downtime.
Boron carbide withstands chemical rust. Harsh processing settings usually involve acids or antacid. B4C remains secure. It preserves efficiency without deteriorating. This reliability ensures constant grinding results. Fragment size distribution stays attire. Item high quality improves.
Custom-made shapes and sizes fit particular sand mill layouts. Makers customize B4C blocks to match parts like blades, linings, or blades. Precision engineering makes sure tight tolerances. Elements incorporate smoothly right into existing systems. Compatibility issues reduce. Efficiency rises.
High-speed sand mills generate intense friction and warmth. B4C handles these problems. Its thermal stability prevents breaking or warping. Workflow run smoothly at greater speeds. Processing times reduce. Result rises. Power usage declines.
Industries like lithium battery manufacturing advantage. B4C blocks grind electrode products carefully. Battery efficiency improves. In pigment production, regular fragment size improves color toughness. Pharmaceuticals utilize B4C mills for ultra-fine powders. Medication bioavailability rises.
Cost financial savings originated from durability. B4C blocks outlive steel or alumina parts. Replacement regularity falls. Functional costs decline. Efficiency expands.
Custom-made boron carbide ceramic blocks offer a functional service for requiring sand mill applications. Their firmness, longevity, and flexibility satisfy industrial demands. Efficiency remains reliable under stress. Quality and effectiveness gain an increase.
Company Introduction
Advanced Ceramics founded on October 17, 2014, is a high-tech enterprise committed to the research and development, production, processing, sales and technical services of ceramic relative materials and products.. Since its establishment in 2014, the company has been committed to providing customers with the best products and services, and has become a leader in the industry through continuous technological innovation and strict quality management.
Our products includes but not limited to Silicon carbide ceramic products, Boron Carbide Ceramic Products, Boron Nitride Ceramic Products, Silicon Carbide Ceramic Products, Silicon Nitride Ceramic Products, Zirconium Dioxide Ceramic Products, Quartz Products, etc. Please feel free to contact us.(nanotrun@yahoo.com)
Payment Methods
T/T, Western Union, Paypal, Credit Card etc.
Shipment Methods
By air, by sea, by express, as customers request.
5 FAQs of Customized High Hardness Boron Carbide B4C Ceramic Block for Sand Mill
What are customized high hardness boron carbide B4C ceramic blocks
Boron carbide ceramic blocks are industrial materials made for heavy-duty applications. They combine boron and carbon to create extreme hardness. These blocks are customized to fit specific sand mill designs. They handle intense friction and wear during grinding processes.
Why use boron carbide blocks in sand mills
Boron carbide ceramic blocks resist wear better than metals. They last longer under harsh conditions. Sand mills grind materials non-stop. Boron carbide reduces downtime caused by part replacements. It keeps operations efficient and cost-effective over time.
Can boron carbide blocks be shaped for unique sand mill setups
Yes. Manufacturers cut boron carbide into exact sizes and shapes. Customization ensures perfect fit for different mill models. This flexibility supports varied industrial needs. Complex geometries or specific thicknesses are achievable.
How to maintain boron carbide ceramic blocks in sand mills
Maintenance is minimal. Clean blocks regularly to remove grinding residue. Check surfaces for chips or cracks during routine inspections. Replace damaged blocks quickly to avoid mill inefficiency. Proper handling during installation prevents early damage.
Do boron carbide blocks outperform other ceramics in sand mills
Boron carbide is harder than alumina or silicon carbide. It withstands higher stress and abrasion. This makes it ideal for grinding tough materials like minerals or coatings. Its durability lowers long-term costs despite higher initial prices.
(Customized High Hardness Boron Carbide B4C Ceramic Block for Sand Mill)
REQUEST A QUOTE
RELATED PRODUCTS
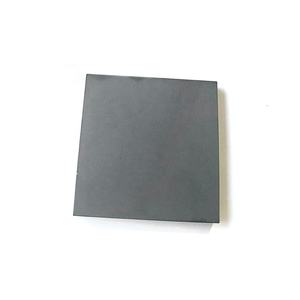
Hot Press Boron Carbide Ceramic Plate and Isostatic Press B4C Ceramics Plate
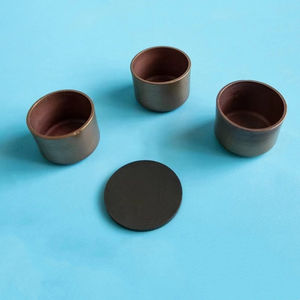
Wear Resistance Boron Carbide B4C Ceramic Sandblasting Spray Nozzles for Cleaning Equipment
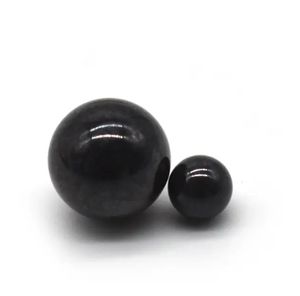
Customized Black Industrial B4C Sheet Boron Carbide Ceramic Plate
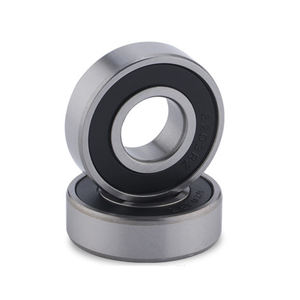
High Hardness Ceramics Silicon Boron Carbide B4c Vest Plate
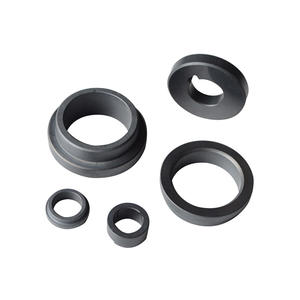
Superfine Abrasive Material Boron Carbide F400 F800 B4C Powder China Boron Carbide for Wear Resistance Boron Carbide Ceramic Rod
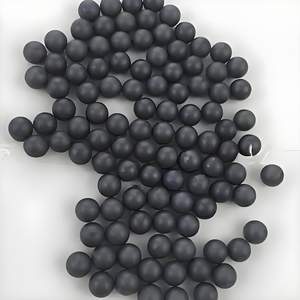