Discover Premium Ceramic Products | Durability & Elegance United | Advanced Ceramics
PRODUCT PARAMETERS
Description
Overview of Zirconium Dioxide Ceramics
Zirconium Dioxide Ceramics, known for their toughness and ability to withstand extreme temperatures, are widely used in medical, automotive, and industrial applications due to their unique properties.
Features of Zirconium Dioxide Ceramics
Exceptional fracture toughness
High thermal expansion
Excellent resistance to wear and corrosion
Biocompatibility for medical implants
(Custom White ZrO2 Zirconia Ceramic Plate/Substrate/Sheet Refractory Insulation)
Specifications of Custom White ZrO2 Zirconia Ceramic Plate/Substrate/Sheet Refractory Insulation
Custom White ZrO2 Zirconia Ceramic Plates/Substrates/Sheets are created for high-performance applications calling for severe warmth resistance and insulation. These items are made from zirconium dioxide (ZrO2), an advanced ceramic material known for outstanding thermal stability and mechanical toughness. The material structure ensures trustworthy efficiency in atmospheres with temperatures up to 2200 ° C.
The ceramic plates are available in custom-made dimensions. Density ranges from 0.5 mm to 50mm. Width and size can be readjusted based on specific demands. Standard dimensions consist of 100mm x 100mm, 200mm x 200mm, and 500mm x 500mm. Custom-made forms or patterns are attainable through precision machining.
Secret thermal homes consist of reduced thermal conductivity (2-3 W/m · K) and high heat insulation efficiency. This makes them perfect for furnace cellular linings, kiln furniture, and thermal barriers. The material withstands thermal shock efficiently. Quick temperature level modifications do not create splitting or deformation.
Mechanical sturdiness is a vital feature. Home plates display a Vickers firmness of 1200-1300 HV. Density varieties in between 5.8-6.1 g/cm TWO. High bending stamina (800-1000 MPa) makes certain resistance to mechanical stress and anxiety. Surface coatings differ. Options include polished, ground, or as-sintered structures. Refined surface areas minimize friction and improve wear resistance.
Electrical insulation homes are superb. ZrO2 ceramics serve as insulators also at elevated temperature levels. This suits applications in electronics or high-voltage systems. Chemical inertness is one more advantage. The material stands up to corrosion from acids, antacid, and molten metals.
Applications cover multiple markets. Typical usages consist of aerospace elements, medical implants, lab equipment, and refractory cellular linings. Personalization encompasses features like openings, grooves, or layers. Alumina or yttria coverings enhance surface buildings for specialized demands.
Quality control follows strict requirements. Each batch goes through screening for dimensional accuracy, density, and thermal efficiency. Certifications meet ISO and ASTM guidelines. Preparations vary based upon order complexity. Standard production takes 2-4 weeks.
Customized White ZrO2 Zirconia Ceramic items supply a balance of longevity, warm resistance, and flexibility. They address obstacles in high-temperature and destructive atmospheres.
(Custom White ZrO2 Zirconia Ceramic Plate/Substrate/Sheet Refractory Insulation)
Applications of Custom White ZrO2 Zirconia Ceramic Plate/Substrate/Sheet Refractory Insulation
Customized white ZrO2 zirconia ceramic plates, substrates, and sheets are utilized extensively in sectors requiring solid warmth resistance and insulation. These materials deal with extreme temperature levels, making them suitable for high-heat environments. They work well in heating systems, kilns, and activators where routine materials fail. Their reduced thermal conductivity assists in saving energy by keeping warmth where it’s required.
In aerospace, zirconia ceramic components shield elements from intense warmth throughout trips. They protect engines and sensing units, making sure secure performance. Electronic devices manufacturers make use of these ceramics as substratums for circuits. They protect against overheating in devices like power components and LED systems. Their electric insulation maintains circuits safe from shorting.
Medical tools and implants often use zirconia ceramics. They resist rust and remain secure in sterilizers or imaging equipments. Dental implants benefit from their strength and biocompatibility. They last long and stay clear of responses in the body.
Metallurgy counts on zirconia sheets for lining heating systems and dealing with liquified metals. They sustain repeated home heating without fracturing. Their chemical security quits responses with steel alloys. This keeps manufacturing tidy and reliable. Power systems like gas cells utilize zirconia substrates to manage ion flow. They boost performance and lifespan in high-temperature configurations.
Industrial lasers and reducing devices use zirconia plates to focus warmth and shield parts. Their firmness lowers wear, reducing downtime. Labs utilize them as stable surfaces for experiments entailing warm or chemicals. Custom-made shapes and sizes fit certain devices needs.
Zirconia porcelains adapt to extreme setups much better than metals or plastics. They incorporate toughness, insulation, and warmth resistance. This makes them a practical option for advanced engineering obstacles.
Company Introduction
Advanced Ceramics founded on October 17, 2014, is a high-tech enterprise committed to the research and development, production, processing, sales and technical services of ceramic relative materials and products.. Since its establishment in 2014, the company has been committed to providing customers with the best products and services, and has become a leader in the industry through continuous technological innovation and strict quality management.
Our products includes but not limited to Silicon carbide ceramic products, Boron Carbide Ceramic Products, Boron Nitride Ceramic Products, Silicon Carbide Ceramic Products, Silicon Nitride Ceramic Products, Zirconium Dioxide Ceramic Products, Quartz Products, etc. Please feel free to contact us.(nanotrun@yahoo.com)
Payment Methods
T/T, Western Union, Paypal, Credit Card etc.
Shipment Methods
By air, by sea, by express, as customers request.
5 FAQs of Custom White ZrO2 Zirconia Ceramic Plate/Substrate/Sheet Refractory Insulation
1. What are Custom White ZrO2 Zirconia Ceramic Plates used for? These plates handle extreme heat. They work in furnaces, aerospace parts, or lab equipment. They insulate against high temperatures. They also resist wear and chemicals. Industries like metal processing or electronics rely on them for stable performance under stress.
2. How high a temperature can ZrO2 Ceramic Sheets withstand? ZrO2 ceramic sheets handle up to 2400°C. They keep their shape and strength. This makes them better than metals or plastics in extreme heat. They resist thermal shock too. Sudden temperature changes won’t crack them easily.
3. Can these ceramic plates be customized? Yes. Sizes, thicknesses, and shapes are adjustable. Holes, grooves, or special surfaces are possible. Manufacturers cut or mold ZrO2 to fit exact needs. Provide specs like dimensions or surface finish requirements. Production times vary based on complexity.
4. Why pick ZrO2 over other ceramics? ZrO2 has higher heat resistance. It lasts longer in harsh conditions. It conducts less heat than alumina or silicon carbide. This improves insulation. It’s tougher too. It resists cracks from pressure or impact better than many ceramics.
5. How to handle and store ZrO2 Ceramic Sheets? Avoid moisture and dirt. Use clean gloves to prevent oil stains. Store in dry areas away from chemicals. Stack them flat with padding between layers. Don’t drop them. Even though they’re strong, rough handling can chip edges.
(Custom White ZrO2 Zirconia Ceramic Plate/Substrate/Sheet Refractory Insulation)
REQUEST A QUOTE
RELATED PRODUCTS
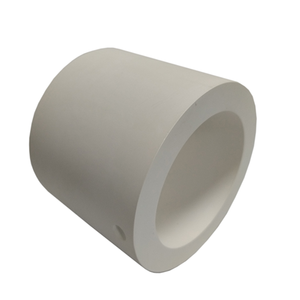
Refractory 3Y 5Y 8Y Zirconia Zros Zirconium Oxide Zirconia Ceramic Circular Ring
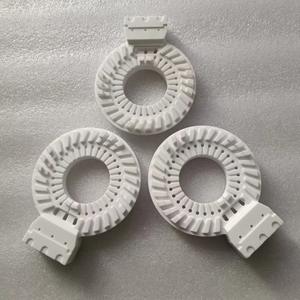
Factory Custom High Hardness ZrO2 Zirconia Ceramic Rods

Yttria Stabilized 95 ZrO2 Zirconium Oxide Zirconia Ceramic
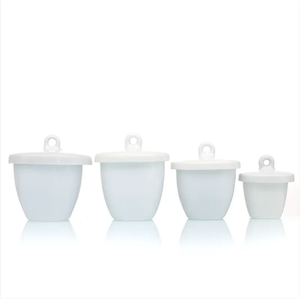
Whole 0.2mm 0.3mm 3mm 10mm 12mm G10 Zirconium Dioxide Ceramic Grinding Ball Zirconia Beads
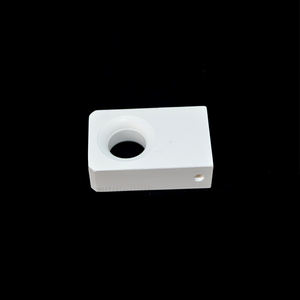
Zirconia Powder Zro2 Ceramic Nano Zirconia Powder Ultrafine Nano Zirconia Zro2 Zirconium Oxide Nano Powder
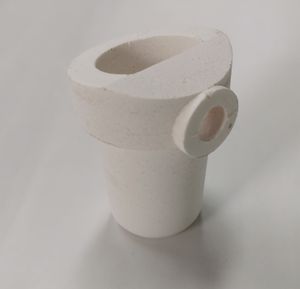