Discover Premium Ceramic Products | Durability & Elegance United | Advanced Ceramics
PRODUCT PARAMETERS
Description
Introduction to Alumina Ceramics
Alumina ceramics are known for their high hardness, wear resistance, corrosion resistance, good electrical insulation and high temperature stability. According to the different alumina content, it can be divided into different grades, such as 95 porcelain, 99 porcelain, etc., among which 99 porcelain refers to ceramic materials with an alumina content of 99%. As the alumina content increases, its mechanical strength and electrical insulation properties will also increase accordingly.
Characteristics of Alumina Ceramics
High Hardness: Alumina ceramics have extremely high hardness, which makes it very wear-resistant and suitable for manufacturing abrasive tools and parts that require wear resistance.
Wear resistance: Due to its high hardness, alumina ceramics show excellent wear resistance and are suitable for manufacturing parts for long-term use.
Corrosion resistance: Alumina ceramics have good resistance to most acids and alkalis, making them widely used in the chemical industry.
Good electrical insulation: As an excellent electrical insulating material, alumina ceramics are widely used in electronic and electrical products.
High temperature stability: Ability to withstand extremely high temperatures without significant physical or chemical changes, which makes it an ideal choice for applications in high temperature environments.
Biocompatibility: In the medical field, certain grades of alumina ceramics are used to make medical devices such as artificial joints due to their good biocompatibility.
(92% 95% Al2o3 Alumina Ceramic Plates / Ceramic Mosaic Tiles)
Specifications of 92% 95% Al2o3 Alumina Ceramic Plates / Ceramic Mosaic Tiles
Alumina ceramic plates and mosaic floor tiles made from 92% and 95% Al2O3 deal high-performance remedies for industrial and engineering applications. These ceramics are known for their exceptional hardness, wear resistance, and thermal stability. The key material is light weight aluminum oxide, which makes sure resilience under severe problems.
The 92% alumina quality provides strong mechanical stamina and resistance to abrasion. It deals with temperature levels as much as 1600 ° C, making it appropriate for high-heat atmospheres. The 95% alumina quality uses higher thickness and enhanced performance in harsh or high-stress settings. Both qualities withstand chemical corrosion, acids, and antacid efficiently.
These ceramic plates and floor tiles are commonly used as protective cellular linings in devices like chutes, receptacles, and pipes. They lower wear in mining, steel production, and power generation sectors. Their smooth or textured surface areas allow modification based on friction or product circulation requirements. Dimensions and densities differ, with typical measurements ranging from 50x50mm to 150x150mm. Density options period 5mm to 25mm for different lots capacities.
Installment techniques consist of adhesive bonding or mechanical fastening. The light-weight design simplifies dealing with compared to metal options. Electrical insulation homes make them safe for use in digital or high-voltage atmospheres. Non-magnetic functions make sure compatibility in sensitive applications.
Quality assurance adheres to stringent criteria, with each set evaluated for solidity, density, and thermal shock resistance. Personalized shapes, openings, or patterns can be produced to fit certain equipment or formats. The ceramic tiles’ interlocking mosaic style allows simple replacement of broken sections without revamping whole systems.
Cost performance comes from prolonged service life, minimizing downtime and maintenance expenditures. These ceramics outmatch conventional materials like steel or rubber in harsh operating conditions. They keep structural integrity under hefty impact, vibration, or rapid temperature modifications.
Surface area finishes range from brightened for low-friction applications to rough structures for enhanced grasp. Shade generally appears white or ivory, with minimal variant in between batches. Compatibility with epoxy resins or cement-based adhesives makes certain protected setup throughout substratums.
(92% 95% Al2o3 Alumina Ceramic Plates / Ceramic Mosaic Tiles)
Applications of 92% 95% Al2o3 Alumina Ceramic Plates / Ceramic Mosaic Tiles
92% and 95% Al2O3 alumina ceramic plates and ceramic mosaic ceramic tiles are commonly utilized in markets requiring high wear resistance, thermal security, and longevity. These materials master rough settings due to their solidity, chemical inertness, and ability to stand up to extreme temperatures.
In mining and mineral handling, alumina ceramic plates line tools like chutes, receptacles, and pipelines. They safeguard surface areas from abrasion caused by heavy products such as ores, gravel, or coal. The high alumina web content makes certain lengthy life span, lowering downtime and maintenance prices.
Chemical plants make use of these ceramics in pumps, shutoffs, and activators. They resist corrosion from acids, alkalis, and solvents. This makes them optimal for taking care of hostile chemicals without breaking down. The non-reactive nature of alumina prevents contamination, making sure product pureness.
Power generation facilities use ceramic mosaic ceramic tiles in central heating boilers and cyclones. They secure frameworks from high-velocity ash particles and thermal shock. The floor tiles preserve architectural stability even under fast temperature changes, avoiding cracks or failures.
In electronics, alumina ceramic plates function as substrates for circuits and insulators. Their electrical insulation residential or commercial properties and thermal conductivity aid manage warmth in gadgets like LEDs or power modules. This boosts efficiency and reliability in high-power applications.
The 95% alumina ceramic offers higher firmness and toughness compared to the 92% grade. It matches applications requiring maximum wear resistance, such as shot blast devices or sand handling systems. The 92% variant gives an economical option for less extreme conditions while keeping solid efficiency.
Ceramic mosaic tiles are prominent in floor covering for manufacturing facilities, stockrooms, and laboratories. Their slip-resistant surface area enhances safety and security. They endure heavy foot website traffic, impacts, and spills without discoloration or wearing down. Easy cleaning and low upkeep include in their functionality.
These porcelains are offered in basic or customized sizes. They can be bound to steel or other substratums for composite remedies. Their convenience makes them a dependable selection across markets prioritizing efficiency, safety, and longevity.
Company Introduction
Advanced Ceramics founded on October 17, 2014, is a high-tech enterprise committed to the research and development, production, processing, sales and technical services of ceramic relative materials and products.. Since its establishment in 2014, the company has been committed to providing customers with the best products and services, and has become a leader in the industry through continuous technological innovation and strict quality management.
Our products includes but not limited to Silicon carbide ceramic products, Boron Carbide Ceramic Products, Boron Nitride Ceramic Products, Silicon Carbide Ceramic Products, Silicon Nitride Ceramic Products, Zirconium Dioxide Ceramic Products, Quartz Products, etc. Please feel free to contact us.(nanotrun@yahoo.com)
Payment Methods
T/T, Western Union, Paypal, Credit Card etc.
Shipment Methods
By air, by sea, by express, as customers request.
5 FAQs of 92% 95% Al2o3 Alumina Ceramic Plates / Ceramic Mosaic Tiles
What are 92% 95% Al2O3 alumina ceramic plates? These plates are high-purity ceramic tiles made from aluminum oxide. They come in two grades: 92% alumina content for general industrial use, 95% for higher-performance applications. The material is sintered at high temperatures to create dense, hard surfaces. This makes them ideal for wear resistance, insulation, or high-temperature environments.
Why choose alumina ceramic plates over other materials? Alumina ceramics outperform metals or plastics in extreme conditions. They resist corrosion from chemicals, handle temperatures over 1500°C, and last longer under abrasion. Their hardness is close to diamonds, reducing wear in machinery. They don’t conduct electricity, making them safe for electrical insulation.
Where are these ceramic plates commonly used? They are used in mining equipment, power plants, chemical processing, and steel manufacturing. They line pipelines, chutes, or hoppers to protect against abrasive materials. In electronics, they serve as insulators. They also work in kilns or furnaces as heat shields.
How do you maintain alumina ceramic plates? Clean them with mild soap and water. Avoid harsh chemicals or abrasive tools. Check for cracks or chips during routine inspections. Replace damaged tiles quickly to prevent system failures. Proper installation ensures even stress distribution, reducing breakage risks.
Can these tiles be customized for specific projects? Yes. Manufacturers cut them into shapes like squares, rectangles, or hexagons. They drill holes or add grooves for bolts, screws, or alignment. Thickness ranges from 5mm to 50mm. Custom sizes or surface finishes are available for unique industrial needs.
(92% 95% Al2o3 Alumina Ceramic Plates / Ceramic Mosaic Tiles)
REQUEST A QUOTE
RELATED PRODUCTS
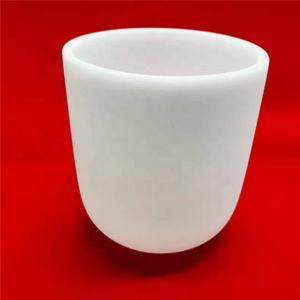
High Purity Al2o3 Alumina Ceramic Lining Alumina Ceramic Mosaic Square Lining
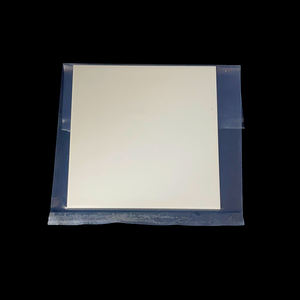
High Voltage Ceramics X Ray Ceramics Low Dielectric Loss-the Dielectric Constant Alumina Metallized Ceramics
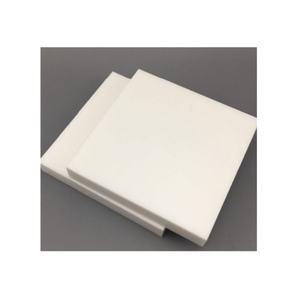
High Polished 99% Alumina Zirconia Machinable Ceramic Bars Plungers Rods
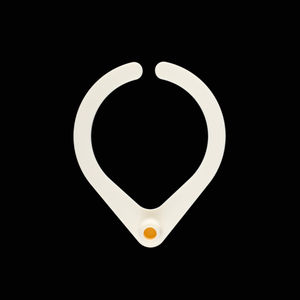
High Alumina 99.5% Oxide Alumina Ceramic Tubes
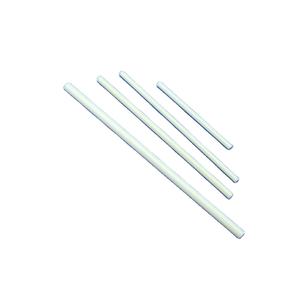
Wear-resistant 99% Alumina Ceramic Rack Customized According to Drawings
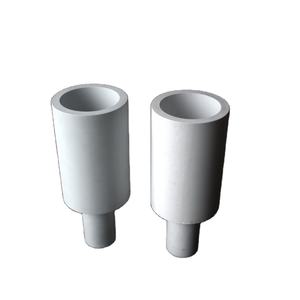