Discover Premium Ceramic Products | Durability & Elegance United | Advanced Ceramics
PRODUCT PARAMETERS
Description
Introduction to Alumina Ceramics
Alumina ceramics are known for their high hardness, wear resistance, corrosion resistance, good electrical insulation and high temperature stability. According to the different alumina content, it can be divided into different grades, such as 95 porcelain, 99 porcelain, etc., among which 99 porcelain refers to ceramic materials with an alumina content of 99%. As the alumina content increases, its mechanical strength and electrical insulation properties will also increase accordingly.
Characteristics of Alumina Ceramics
High Hardness: Alumina ceramics have extremely high hardness, which makes it very wear-resistant and suitable for manufacturing abrasive tools and parts that require wear resistance.
Wear resistance: Due to its high hardness, alumina ceramics show excellent wear resistance and are suitable for manufacturing parts for long-term use.
Corrosion resistance: Alumina ceramics have good resistance to most acids and alkalis, making them widely used in the chemical industry.
Good electrical insulation: As an excellent electrical insulating material, alumina ceramics are widely used in electronic and electrical products.
High temperature stability: Ability to withstand extremely high temperatures without significant physical or chemical changes, which makes it an ideal choice for applications in high temperature environments.
Biocompatibility: In the medical field, certain grades of alumina ceramics are used to make medical devices such as artificial joints due to their good biocompatibility.
(Solid Nonporous Sintered Alumina Ceramic)
Specifications of Solid Nonporous Sintered Alumina Ceramic
Solid impermeable sintered alumina ceramic is a high-performance material developed for demanding commercial applications. It is made by sintering high-purity aluminum oxide powder at extreme temperatures. This process creates a thick framework with no pores. The product offers extraordinary solidity, put on resistance, and thermal stability.
The typical aluminum oxide content varies from 95% to 99.9%. Higher pureness grades give far better performance in harsh environments. Density is between 3.6 and 3.9 g/cm FOUR. The material has a Vickers solidity of 15-18 Grade point average. This makes it more challenging than the majority of steels and resistant to abrasion. Flexural stamina arrays from 300 to 400 MPa. Compressive toughness goes beyond 2000 MPa. These residential properties make sure sturdiness under heavy loads.
Running temperature levels rise to 1650 ° C. The reduced thermal growth coefficient reduces form adjustments throughout rapid heating or cooling. Thermal conductivity is 20-30 W/m · K. This assists take care of heat in high-temperature setups. The material withstands thermal shock much better than many ceramics.
Chemical inertness is an essential benefit. It holds up against acids, alkalis, and molten steels. It carries out well in environments with solid solvents or oxidizing agents. Electrical insulation residential properties are solid. Volume resistivity exceeds 10 ¹⁴ Ω · cm at area temperature. Dielectric stamina is around 15-20 kV/mm. These qualities suit it for electronic and high-voltage applications.
Surface area surfaces differ from typical to precision-polished. Flatness resistances can be regulated within 0.1 mm per 25 mm. Custom-made shapes and sizes are achievable via sophisticated machining. Typical types consist of plates, tubes, poles, and customized parts.
Applications extend several sectors. It is used in wear-resistant components, reducing devices, and furnace elements. Electronics depend on it for substrates and insulators. Medical equipment uses it for its biocompatibility. Semiconductor making employs it in wafer-handling systems.
The material is compatible with typical metalizing and brazing techniques. This allows combination right into complex settings up. Customized modifications like finishings or pierced openings are available. Efficiency continues to be constant in vacuum or high-pressure conditions.
Surface area roughness can be changed based upon application needs. Ordinary roughness values vary from 0.1 µm to 1.5 µm. Tight dimensional control makes certain compatibility with mechanical systems. Preparations differ by intricacy. Prototyping and bulk manufacturing choices exist.
(Solid Nonporous Sintered Alumina Ceramic)
Applications of Solid Nonporous Sintered Alumina Ceramic
Strong nonporous sintered alumina ceramic is a high-performance product utilized in many industries. Its dense structure makes it strong, wear-resistant, and able to take care of extreme warm and chemicals. These residential properties make it perfect for requiring applications.
In industrial machinery, it is made use of for parts like seals, bearings, and reducing tools. These parts encounter high friction and pressure. The ceramic’s hardness decreases wear and extends tools life. It functions well in extreme problems without splitting or weakening.
The electronic devices sector utilizes it for insulators and circuit substratums. It does not carry out electrical power and stays steady at heats. This assists avoid getting too hot in devices like power components and sensing units. Its smooth surface additionally supports accurate production procedures.
Medical applications consist of surgical devices and implants. The material stands up to germs development since it has no pores. It can be sanitized continuously without damage. This makes it safe for long-term usage in the body, such as in joint substitutes or oral parts.
Chemical handling devices relies upon this ceramic for storage tanks, shutoffs, and pumps. It does not respond with acids or solvents. The nonporous surface area stops chemicals from permeating in, preventing contamination and corrosion. This guarantees reputable efficiency in aggressive atmospheres.
Aerospace and automobile industries use it in high-temperature zones. Parts like engine sensors and exhaust systems benefit from its warmth resistance. It preserves toughness even under thermal anxiety, enhancing security and efficiency.
Mining and construction tools usage alumina ceramic for wear-resistant components. Crushers, drills, and conveyor systems face unpleasant materials. The ceramic’s sturdiness reduces downtime and upkeep costs.
Consumer items like high-end watches and kitchen area tools use it for sturdiness and appearances. It stays scratch-free and retains its refined look over time. This incorporates practicality with visual allure.
The product’s convenience originates from its ability to adjust to extreme problems. It resolves issues in fields where metals or plastics stop working. Its dependability makes it a leading selection for designers and designers worldwide.
Company Introduction
Advanced Ceramics founded on October 17, 2014, is a high-tech enterprise committed to the research and development, production, processing, sales and technical services of ceramic relative materials and products.. Since its establishment in 2014, the company has been committed to providing customers with the best products and services, and has become a leader in the industry through continuous technological innovation and strict quality management.
Our products includes but not limited to Silicon carbide ceramic products, Boron Carbide Ceramic Products, Boron Nitride Ceramic Products, Silicon Carbide Ceramic Products, Silicon Nitride Ceramic Products, Zirconium Dioxide Ceramic Products, Quartz Products, etc. Please feel free to contact us.(nanotrun@yahoo.com)
Payment Methods
T/T, Western Union, Paypal, Credit Card etc.
Shipment Methods
By air, by sea, by express, as customers request.
5 FAQs of Solid Nonporous Sintered Alumina Ceramic
Solid nonporous sintered alumina ceramic is a high-performance material. It is made from aluminum oxide powder. The powder is compressed and heated at very high temperatures. This process creates a dense structure without pores. The material is hard and resistant to wear.
1. What is solid nonporous sintered alumina ceramic used for?
It is used in industrial parts like seals and bearings. It works in pumps and valves. Electronics use it for insulating components. Medical tools use it for its non-reactive properties.
2. How does it handle high temperatures?
It can withstand temperatures up to 1700°C. It keeps its strength even in extreme heat. It resists thermal shock. Sudden temperature changes do not crack it easily.
3. Is it chemically resistant?
Yes. It does not react with acids or alkalis. It works in corrosive environments. Harsh chemicals do not damage it. This makes it ideal for chemical processing equipment.
4. Why choose this over other ceramics?
It has higher hardness. It is more wear-resistant than materials like zirconia. Its nonporous structure stops liquids or gases from passing through. It lasts longer under stress.
5. Can it be customized for specific shapes?
Yes. It is shaped before sintering. Complex designs are possible. Precision parts are made using molds. Final dimensions are accurate after heating.
The material is cost-effective for demanding applications. It reduces downtime in machinery. Maintenance costs stay low. Performance remains stable over time.
(Solid Nonporous Sintered Alumina Ceramic)
REQUEST A QUOTE
RELATED PRODUCTS
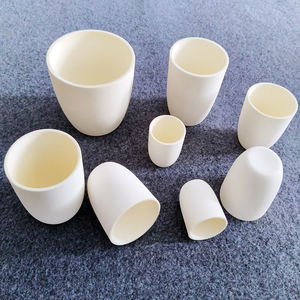
99.5% Industrial Grade CC-1 Ready to Press Granulated Alumina Special Ceramics
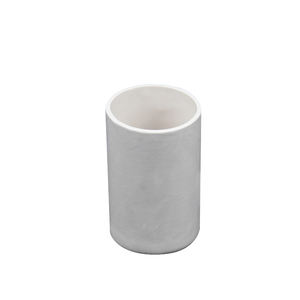
Refractory Industrial Electrical Insulation 95% Al2O3 Alumina Ceramic Tubes Aluminum Oxide Insulator
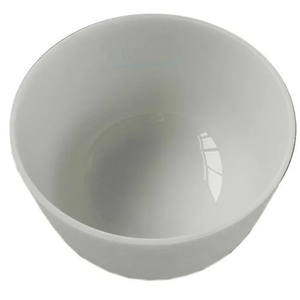
Alumina Industrial Ceramics Alumina for Water Treatment
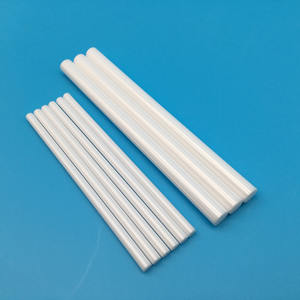
Customization Plate 99% Alumina Ceramic Plate High Quality Ceramic Product with 205*140*4mm
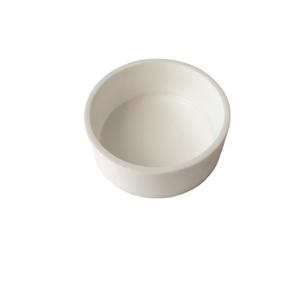
High-quality 99.7% Al2o3 Alumina Ceramic Products
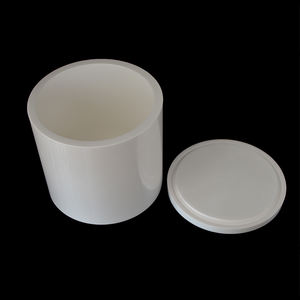