Discover Premium Ceramic Products | Durability & Elegance United | Advanced Ceramics
PRODUCT PARAMETERS
Description
Overview of Silicon Nitride Ceramics
Silicon Nitride Ceramics are high-performance materials known for their excellent mechanical properties, including strength, toughness, and resistance to wear, corrosion, and thermal shock, making them ideal for demanding applications in various industries.
Features of Silicon Nitride Ceramics
Exceptional hardness and wear resistance.
Superior mechanical strength and fracture toughness.
Excellent thermal stability and resistance to thermal shock.
High corrosion resistance in aggressive environments.
Low density contributing to lightweight components.
(High Hardness Black Zirconia Ceramic Indenter Silicon Nitride Parts for Bonding Machine Welding Cutting Punching Bending)
Specifications of High Hardness Black Zirconia Ceramic Indenter Silicon Nitride Parts for Bonding Machine Welding Cutting Punching Bending
High Firmness Black Zirconia Ceramic Indenter Silicon Nitride Components are engineered for precision jobs in bonding devices, welding, cutting, punching, and bending operations. These parts combine innovative ceramic products to supply phenomenal efficiency popular industrial atmospheres. The main products used are black zirconia and silicon nitride, understood for their extreme solidity and resistance to put on.
These parts are built to hold up against high mechanical tension. The black zirconia offers superior surface area toughness, reducing chipping or fracturing throughout repetitive usage. Silicon nitride includes thermal security, preserving architectural stability also under rapid temperature level changes. This mix ensures lasting resilience in applications like steel forming or precision welding.
Secret features include a hardness ranking surpassing 1500 HV (Vickers), making them resistant to abrasion and contortion. The low friction coefficient of silicon nitride decreases power loss throughout operations, improving performance. Surface surfaces are precision-polished to decrease fragment generation, important for cleanroom or high-purity production setups.
These ceramic indenters work with automated bonding devices. They offer regular pressure distribution during semiconductor pass away attachment or microelectronic setting up. For welding and reducing devices, the thermal shock resistance avoids warping, making sure exact results over extended cycles.
In boxing and bending applications, the components withstand lateral forces without fracturing. Dimensional precision is preserved within ± 0.002 mm, essential for tight-tolerance procedures. Chemical inertness allows usage in destructive environments, such as chemical handling or marine equipment.
Technical requirements include a thickness of 6.05 g/cm ³ for zirconia and 3.2 g/cm four for silicon nitride. Running temperature levels range from -200 ° C to +1400 ° C. Dielectric stamina exceeds 15 kV/mm, appropriate for electrical insulation jobs. Custom-made dimensions and geometries are offered, with typical sizes varying from 2 mm to 50 mm.
The materials undertake strenuous top quality checks, including XRD evaluation for phase purity and SEM inspections for microstructural consistency. Each batch is checked for load-bearing ability, with a lot of units ranked for over 500,000 cycles at 20 kN loads.
(High Hardness Black Zirconia Ceramic Indenter Silicon Nitride Parts for Bonding Machine Welding Cutting Punching Bending)
Applications of High Hardness Black Zirconia Ceramic Indenter Silicon Nitride Parts for Bonding Machine Welding Cutting Punching Bending
High solidity black zirconia ceramic and silicon nitride parts are critical in bonding makers for welding, cutting, boxing, and flexing jobs. These materials excel in high-stress settings as a result of their extreme toughness and wear resistance. The hardness of zirconia ceramic and silicon nitride minimizes surface area rubbing. This protects against material buildup during procedures. It makes sure consistent performance over extended periods.
In welding applications, these components take care of intense heat without weakening. Their thermal security keeps them undamaged under quick temperature level adjustments. This reduces downtime for replacements. Cutting devices made from these porcelains stay sharp much longer. They slice with challenging materials easily. This boosts precision and lowers waste.
Punching and flexing processes benefit from the strength of zirconia and silicon nitride. The products stand up to chipping or breaking under hefty tons. This is important for preserving limited resistances in manufacturing. Bonding machines utilizing these components achieve higher precision. They generate fewer issues in finished products.
The chemical inertness of these porcelains avoids reactions with steels or other materials. This is crucial in atmospheres with direct exposure to oils, solvents, or harsh compounds. Parts remain practical without constant cleansing or maintenance. Their smooth surface area coating lessens contamination threats. This is type in sectors like electronics or clinical gadget manufacturing.
These elements are lightweight compared to typical metal options. They reduce endure equipment by lowering functional stress and anxiety. Energy usage goes down as a result. Manufacturing facilities conserve costs on power and component substitutes.
Custom sizes and shapes are attainable with advanced ceramic production strategies. This versatility matches specialized bonding maker designs. Industries like vehicle, aerospace, and semiconductor production rely on these parts for high-precision tasks.
Black zirconia ceramic and silicon nitride components operate efficiently in extreme conditions. They manage high pressures, temperatures, and mechanical effects without failure. Their reliability ensures undisturbed production cycles. This enhances overall tools performance.
Using these sophisticated ceramics straightens with contemporary demands for sustainability. Longer-lasting parts reduce product waste. Less replacements indicate lower source intake with time. Services satisfy environmental objectives while maintaining productivity.
Company Introduction
Advanced Ceramics founded on October 17, 2014, is a high-tech enterprise committed to the research and development, production, processing, sales and technical services of ceramic relative materials and products.. Since its establishment in 2014, the company has been committed to providing customers with the best products and services, and has become a leader in the industry through continuous technological innovation and strict quality management.
Our products includes but not limited to Silicon carbide ceramic products, Boron Carbide Ceramic Products, Boron Nitride Ceramic Products, Silicon Carbide Ceramic Products, Silicon Nitride Ceramic Products, Zirconium Dioxide Ceramic Products, Quartz Products, etc. Please feel free to contact us.(nanotrun@yahoo.com)
Payment Methods
T/T, Western Union, Paypal, Credit Card etc.
Shipment Methods
By air, by sea, by express, as customers request.
5 FAQs of High Hardness Black Zirconia Ceramic Indenter Silicon Nitride Parts for Bonding Machine Welding Cutting Punching Bending
What are high hardness black zirconia ceramic indenter silicon nitride parts? These parts are made from advanced ceramic materials. They combine silicon nitride and zirconia. They are designed for bonding machines used in welding, cutting, punching, and bending. Their high hardness ensures they withstand extreme pressure and wear.
Why choose ceramic indenters over metal ones? Ceramic indenters last longer. They resist wear better than metal. They handle high temperatures without deforming. They stay stable during repeated use. This reduces downtime and replacement costs.
What applications suit these parts? They work in industrial processes needing precision. Examples include electronics assembly, automotive manufacturing, and metal forming. They perform well in tasks requiring sharp edges or smooth surfaces. Their toughness prevents chipping or cracking under stress.
How do these parts handle chemical exposure? They resist most chemicals. Acids and alkalis do not damage them. This makes them ideal for harsh environments. Regular cleaning keeps them free from contaminants. No special coatings are needed.
Can these parts be customized? Yes. Sizes and shapes match specific machine requirements. Custom designs ensure compatibility with existing tools. Surface finishes are adjusted for different materials. Technical support helps select the right configuration.
What maintenance do they require? Maintenance is minimal. Inspect them periodically for surface wear. Clean with non-abrasive materials. Avoid impacts to prevent micro-cracks. Proper storage prevents accidental damage. Their durability ensures consistent performance over time.
(High Hardness Black Zirconia Ceramic Indenter Silicon Nitride Parts for Bonding Machine Welding Cutting Punching Bending)
REQUEST A QUOTE
RELATED PRODUCTS
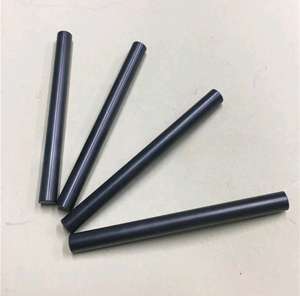
Factory Direct Wear Resistance Ceramic Beads 0.4-0.6mm Silicon Nitride Industrial Ceramic Balls
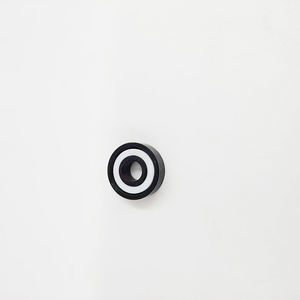
Silicon Nitride Ceramic Plug-in Custom Ceramic Plug-in Ceramic Insulation Positioning Pin Silicon Nitride Custom Parts
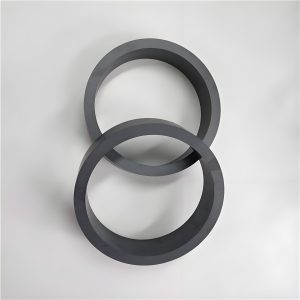
Silicon Nitride Ring High Hardness And High Strength Si3N4 Ring
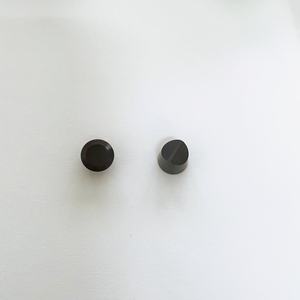
Alumina/Zirconia/Silicon Nitride Ceramic Pin
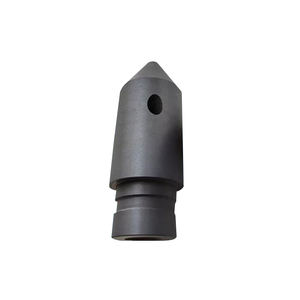
Good Heat Transfer Performance Si3N4 Ceramic Plate Silicon Nitride Ceramic Substrate for Semiconductor
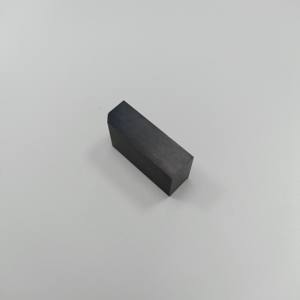