Discover Premium Ceramic Products | Durability & Elegance United | Advanced Ceramics
PRODUCT PARAMETERS
Description
Introduction to Alumina Ceramics
Alumina ceramics are known for their high hardness, wear resistance, corrosion resistance, good electrical insulation and high temperature stability. According to the different alumina content, it can be divided into different grades, such as 95 porcelain, 99 porcelain, etc., among which 99 porcelain refers to ceramic materials with an alumina content of 99%. As the alumina content increases, its mechanical strength and electrical insulation properties will also increase accordingly.
Characteristics of Alumina Ceramics
High Hardness: Alumina ceramics have extremely high hardness, which makes it very wear-resistant and suitable for manufacturing abrasive tools and parts that require wear resistance.
Wear resistance: Due to its high hardness, alumina ceramics show excellent wear resistance and are suitable for manufacturing parts for long-term use.
Corrosion resistance: Alumina ceramics have good resistance to most acids and alkalis, making them widely used in the chemical industry.
Good electrical insulation: As an excellent electrical insulating material, alumina ceramics are widely used in electronic and electrical products.
High temperature stability: Ability to withstand extremely high temperatures without significant physical or chemical changes, which makes it an ideal choice for applications in high temperature environments.
Biocompatibility: In the medical field, certain grades of alumina ceramics are used to make medical devices such as artificial joints due to their good biocompatibility.
(Customized High Strength Industrial 95% Al2O3 Alumina Ceramic Block)
Specifications of Customized High Strength Industrial 95% Al2O3 Alumina Ceramic Block
Personalized High Strength Industrial 95% Al2O3 Alumina Ceramic Block is designed for demanding industrial applications. The product contains 95% alumina (Al2O3), making certain high performance in extreme settings. It supplies extraordinary mechanical stamina, wear resistance, and thermal security. The ceramic block handles severe temperature levels approximately 1600 ° C, maintaining architectural honesty under long term heat exposure. It stands up to chemical deterioration from acids, alkalis, and other aggressive compounds. This makes it appropriate for use in chemical handling, metallurgy, and high-temperature heaters.
The ceramic block features a dense microstructure, reducing porosity to below 0.5%. This improves its solidity, reaching 85 HRA on the Rockwell range. Its compressive toughness goes beyond 2200 MPa, perfect for heavy-load conditions. The low thermal growth coefficient minimizes dimensional adjustments during quick temperature shifts. This stops fracturing or contortion in applications including thermal biking.
Modification options consist of specific dimensional modifications. The block can be machined into different forms, such as plates, rods, tubes, or complex geometries. Surface area coatings are tailored to fulfill certain demands, consisting of sprucing up, grinding, or finish. Resistances are managed within ± 0.5% of the defined dimensions. This ensures compatibility with existing equipment and systems.
Electrical insulation residential or commercial properties are an additional essential benefit. The alumina ceramic block has a high dielectric strength, avoiding existing leak in high-voltage environments. It is commonly utilized in electronic devices, power transmission, and shielding components. Its non-magnetic nature makes it ideal for applications needing marginal electromagnetic interference.
Manufacturing adheres to stringent quality standards. Raw materials are cleansed to minimize impurities. Advanced sintering methods maximize thickness and stamina. Each set undergoes rigorous screening for hardness, thermal shock resistance, and chemical security. Qualifications consist of ISO 9001 and RoHS compliance.
Applications extend markets such as mining, aerospace, and semiconductor manufacturing. The ceramic block is utilized in wear-resistant liners, cutting devices, and precision components. It expands equipment lifespan, minimizes downtime, and decreases upkeep prices. Custom-made solutions are available for one-of-a-kind operational obstacles.
(Customized High Strength Industrial 95% Al2O3 Alumina Ceramic Block)
Applications of Customized High Strength Industrial 95% Al2O3 Alumina Ceramic Block
Customized high-strength commercial 95% Al2O3 alumina ceramic blocks serve essential functions throughout multiple industries. Their remarkable solidity and wear resistance make them perfect for harsh environments. These blocks are widely made use of in mining and mineral handling. They safeguard equipment like crushers and grinders from abrasive materials. This extends equipment life and minimizes downtime.
In steel manufacturing, alumina ceramic blocks deal with extreme temperatures and mechanical stress. They line heaters and kilns. They secure parts from molten steel and slag. This makes sure secure procedure in high-heat conditions. Their thermal stability avoids fracturing under fast temperature level modifications.
The power generation industry counts on these blocks for electrical insulation. They isolate high-voltage components in turbines and transformers. Their non-conductive homes protect against energy loss. They endure electrical arcing without degradation. This enhances safety and security and performance in power systems.
Chemical processing plants make use of alumina ceramics for rust resistance. The blocks resist acids, antacid, and solvents. They line reactors and piping systems. This protects against contamination and material break down. Their inert nature guarantees compatibility with hostile chemicals.
Manufacturing sectors use these blocks in accuracy cutting tools. Their firmness permits machining of difficult steels and alloys. They maintain sharp sides longer than typical materials. This decreases device substitute regularity.
Electronic devices benefit from alumina ceramic blocks in substrate and component production. They supply thermal monitoring in circuits. Their low thermal expansion protects against warping. This stabilizes digital performance under heat.
Customization is an essential benefit. Blocks are customized in size, form, and surface area finish. This meets particular devices requirements. Designers enhance designs for load distribution and anxiety points. Adaptability makes certain smooth assimilation right into existing systems.
These blocks incorporate durability with cost-effectiveness. Very little upkeep decreases long-lasting costs. Industries prioritize them for important applications requiring dependability. Efficiency in extreme conditions makes them a sensible service for commercial difficulties.
Company Introduction
Advanced Ceramics founded on October 17, 2014, is a high-tech enterprise committed to the research and development, production, processing, sales and technical services of ceramic relative materials and products.. Since its establishment in 2014, the company has been committed to providing customers with the best products and services, and has become a leader in the industry through continuous technological innovation and strict quality management.
Our products includes but not limited to Silicon carbide ceramic products, Boron Carbide Ceramic Products, Boron Nitride Ceramic Products, Silicon Carbide Ceramic Products, Silicon Nitride Ceramic Products, Zirconium Dioxide Ceramic Products, Quartz Products, etc. Please feel free to contact us.(nanotrun@yahoo.com)
Payment Methods
T/T, Western Union, Paypal, Credit Card etc.
Shipment Methods
By air, by sea, by express, as customers request.
5 FAQs of Customized High Strength Industrial 95% Al2O3 Alumina Ceramic Block
What are Customized High Strength Industrial 95% Al2O3 Alumina Ceramic Blocks used for?
These blocks are mainly used in industries needing wear-resistant, high-temperature-resistant materials. They work in mining, chemical plants, power generation, machinery. They protect equipment like pipelines, chutes, cyclones. They handle abrasion, corrosion, extreme heat. They also insulate electrical systems.
Why choose 95% alumina content?
Higher alumina content means better performance. 95% Al2O3 gives high density, hardness, mechanical strength. It resists wear, chemicals, heat up to 1600°C. Lower alumina ceramics wear faster. This grade balances cost and durability for heavy industrial use.
Can these blocks be customized?
Yes. Sizes, shapes, thicknesses are adjustable. They fit specific machinery or parts. Common forms include tiles, plates, liners. Holes, grooves, surface finishes like polishing or glazing are possible. Custom designs meet exact operational needs.
How are these blocks installed?
Installation depends on the application. Methods include adhesive bonding, mechanical fastening, welding. High-strength epoxy or bolts secure blocks to metal surfaces. Follow the supplier’s guidelines. Professional help ensures proper fit and performance.
What is the lifespan of these blocks?
Lifespan varies with use. Factors include load, temperature, abrasion level. They last longer than steel or plastic in harsh conditions. Regular checks for cracks or wear help. Clean with mild detergents. Avoid impacts or sudden temperature changes. Proper care extends service life.
(Customized High Strength Industrial 95% Al2O3 Alumina Ceramic Block)
REQUEST A QUOTE
RELATED PRODUCTS
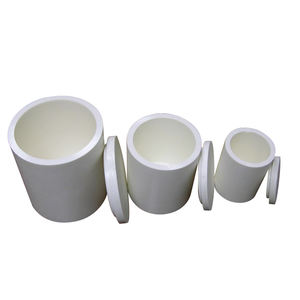
High Temperature Corrosion Resistant 95% Al2O3 Alumina Ceramic Thin Sheet Substrate
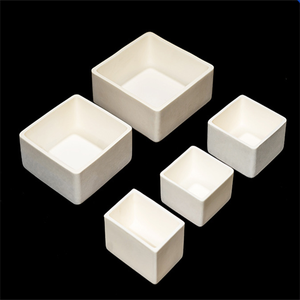
Whole High Alumina Ball 99 Ceramic Ball Alumina Oxide Ceramic Ball Spheres
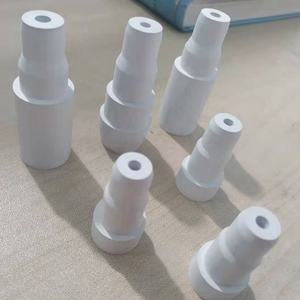
96% Alumina Al2o3 Ceramic Substrate Laser Cutting Customized Ceramic Disc
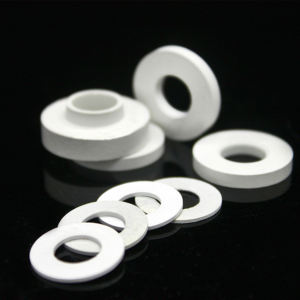
Hot 95% 99% 99.7% Alumina Ceramic Tube for Thermocouple Ceramic Tube for Thermocouple
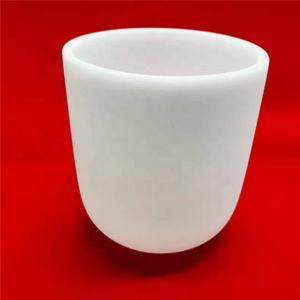
White Alumina Ceramic Heat Sink Isolated Ceramic 95 For Promotion
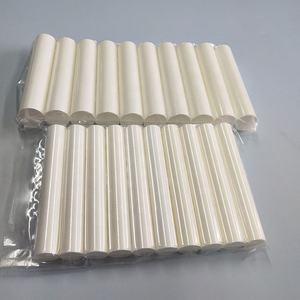