Discover Premium Ceramic Products | Durability & Elegance United | Advanced Ceramics
PRODUCT PARAMETERS
Description
Overview of aluminum nitride ceramics
Aluminum Nitride Ceramic is an advanced ceramic material with aluminum nitride as the main component. It has been widely used in electronics, optics, and mechanics due to its unique properties.
Features of aluminum nitride ceramics
High thermal conductivity: Aluminum nitride ceramics have relatively high thermal conductivity, usually between 170-260 W/m·K, which makes it an excellent heat dissipation material. It is especially suitable for electronic devices that require efficient heat dissipation, such as substrate materials for power semiconductor devices.
Good electrical insulation: Despite its high thermal conductivity, aluminum nitride ceramics are excellent insulators of electricity, which can effectively prevent current leakage and ensure the safe operation of electronic components.
Low dielectric constant and dielectric loss: These characteristics make aluminum nitride ceramics very suitable for use in high-frequency circuits because it can reduce energy loss during signal transmission.
High temperature resistance: Aluminum nitride ceramics can maintain structural stability and strength at extremely high temperatures. Its melting point is about 2800°C, so it is suitable for applications in high temperature environments.
Low thermal expansion coefficient: Compared with semiconductor materials such as silicon, aluminum nitride has a lower thermal expansion coefficient, which means it has better dimensional stability when the temperature changes, which helps improve packaging reliability.
Corrosion resistance: Aluminum nitride ceramics have good chemical stability to most molten metals and are not easily oxidized or corroded, allowing them to perform well in harsh environments.
High mechanical strength: Although not as hard as some other types of ceramic materials, aluminum nitride ceramics still provide enough mechanical strength to allow them to be used in many structural applications.
(High thermal conductivity thick film aln aluminum nitride ceramic pcb and alumina pcb substrate)
Specifications of High thermal conductivity thick film aln aluminum nitride ceramic pcb and alumina pcb substrate
High thermal conductivity thick movie light weight aluminum nitride (AlN) ceramic PCBs and alumina (Al ₂ O TWO) PCB substrates serve crucial duties in advanced electronic devices. Both materials master managing warmth and guaranteeing reliability sought after atmospheres. AlN ceramic PCBs attract attention for their extraordinary thermal conductivity, usually ranging in between 170-200 W/mK. This makes them optimal for high-power applications where warm dissipation is essential. Alumina substrates supply reduced thermal conductivity, around 24-28 W/mK, yet stay widely used due to their cost-effectiveness and robust efficiency in standard problems.
Electrical insulation is a key attribute of both materials. AlN and alumina substrates give high dielectric strength, avoiding present leakage also under high voltage. This ensures secure procedure in circuits calling for specific electrical seclusion. Mechanical strength is another benefit. Alumina substrates are recognized for high sturdiness and resistance to physical anxiety, making them ideal for harsh settings. AlN, while a little much less mechanically durable than alumina, maintains sufficient stamina for most applications while outshining in thermal management.
Temperature level security is important. AlN substrates hold up against operating temperature levels as much as 850 ° C, while alumina manages slightly greater arrays, around 1600 ° C. Both materials resist thermal development inequalities, decreasing the danger of delamination or fracturing throughout rapid temperature changes. Thick movie modern technology boosts these substratums. Conductive traces are screen-printed making use of specialized pastes, allowing precise circuit patterns. This procedure makes sure compatibility with high-temperature soldering and wire bonding.
Surface surfaces vary. AlN PCBs typically use gold or silver finishes to boost conductivity and corrosion resistance. Alumina substratums may employ more affordable finishes like copper or nickel, balancing performance and expense. Applications differ based upon demands. AlN is preferred in high-power LED components, RF/microwave devices, and automotive power electronics. Alumina matches customer electronics, industrial sensing units, and less thermally intensive systems.
Price stays a determining element. Alumina substratums are much more cost effective, appealing for budget-sensitive projects. AlN’s superior thermal performance justifies its greater price in specialized applications. Both materials sustain miniaturization and high-density layouts, meeting the demands of contemporary electronics. Compatibility with automated setting up procedures makes certain simplicity of combination right into assembly line.
(High thermal conductivity thick film aln aluminum nitride ceramic pcb and alumina pcb substrate)
Applications of High thermal conductivity thick film aln aluminum nitride ceramic pcb and alumina pcb substrate
High thermal conductivity thick film light weight aluminum nitride (AlN) and alumina ceramic PCBs are essential in modern electronics. These products take care of heat successfully in high-power applications. AlN ceramic PCBs succeed because of their remarkable thermal conductivity. They move warmth away from components faster than traditional materials. This minimizes overheating dangers in gadgets. Alumina PCBs provide great thermal performance at a lower expense. They are commonly used where extreme warm dissipation is not needed. Both products make certain integrity sought after environments.
AlN ceramic PCBs are optimal for high-power LED lights systems. They handle intense heat produced by high-brightness LEDs. This extends the life-span of lighting options. Power electronic devices like inverters and motor drives also use AlN substrates. They keep security in high-voltage circuits. AlN is preferred in radio frequency (RF) and microwave devices. Its low electrical loss enhances signal integrity. Automotive electronic devices depend on AlN for electrical car power modules. It withstands high temperatures in portable rooms. Aerospace systems use AlN PCBs for thermal administration in avionics. The material’s resilience suits rough operating conditions. Medical tools gain from AlN’s capacity to take care of heat in imaging devices. It guarantees precise diagnostics over long periods.
Alumina PCBs prevail in customer electronic devices. They supply ample heat dissipation for daily tools. Industrial heater make use of alumina substrates for their thermal security. They endure repeated heating cycles without destruction. Alumina is utilized in laser diodes and sensing units. It supports exact temperature level control. Cost-sensitive applications favor alumina for stabilizing performance and cost. Hybrid circuits often integrate alumina with steel layers. This enhances warmth dispersing in multilayer designs. Alumina substratums are common in published circuit card for power products. They protect against element failure under modest thermal stress. Both AlN and alumina PCBs adjust to custom styles. Makers pick based upon thermal needs and budget plan. Alumina remains a sensible choice for lots of mid-range applications.
Company Introduction
Advanced Ceramics founded on October 17, 2014, is a high-tech enterprise committed to the research and development, production, processing, sales and technical services of ceramic relative materials and products.. Since its establishment in 2014, the company has been committed to providing customers with the best products and services, and has become a leader in the industry through continuous technological innovation and strict quality management.
Our products includes but not limited to Silicon carbide ceramic products, Boron Carbide Ceramic Products, Boron Nitride Ceramic Products, Silicon Carbide Ceramic Products, Silicon Nitride Ceramic Products, Zirconium Dioxide Ceramic Products, Quartz Products, etc. Please feel free to contact us.(nanotrun@yahoo.com)
Payment Methods
T/T, Western Union, Paypal, Credit Card etc.
Shipment Methods
By air, by sea, by express, as customers request.
5 FAQs of High thermal conductivity thick film aln aluminum nitride ceramic pcb and alumina pcb substrate
1. What makes high thermal conductivity thick film AlN aluminum nitride ceramic PCB different from alumina PCB substrates?
Aluminum nitride (AlN) ceramic PCBs have higher thermal conductivity. AlN reaches 170-200 W/mK. Alumina (Al2O3) offers 18-30 W/mK. AlN moves heat faster. This suits high-power devices needing quick heat dissipation. Alumina works for standard applications. Cost is lower for alumina.
2. Where are AlN ceramic PCBs typically used compared to alumina substrates?
AlN PCBs handle high-power electronics. Examples include LED lighting, power modules, RF devices. High thermal conductivity prevents overheating. Alumina substrates fit less demanding uses. Examples are consumer electronics, sensors. Alumina balances performance and cost.
3. Are AlN ceramic PCBs reliable in high-temperature environments?
Yes. AlN resists thermal stress. It operates in temperatures up to 800°C. Alumina withstands higher temperatures near 1600°C. Both materials resist chemical corrosion. AlN is better for rapid heat transfer. Alumina suits steady high-heat conditions.
4. Why is AlN more expensive than alumina substrates?
AlN production involves complex processes. Raw materials cost more. Sintering AlN requires precise nitrogen atmospheres. Alumina uses simpler manufacturing. Raw materials are cheaper. High demand for alumina reduces costs further.
5. Can alumina substrates replace AlN in high-power applications?
Not always. Alumina’s lower thermal conductivity limits heat dissipation. High-power devices risk overheating with alumina. AlN is preferred for power semiconductors, laser diodes. Alumina works for medium-power uses. Cost savings matter here.
(High thermal conductivity thick film aln aluminum nitride ceramic pcb and alumina pcb substrate)
REQUEST A QUOTE
RELATED PRODUCTS
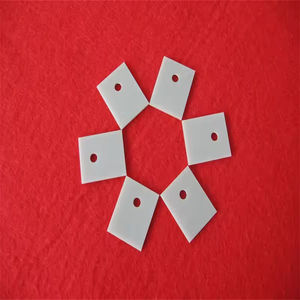
Refractory High Thermal Conductivity Aluminium Nitride Aln Insulating Ceramic Crucible for Electronic
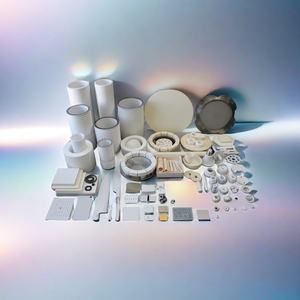
AlN ceramics hot pressed aluminium nitride plate
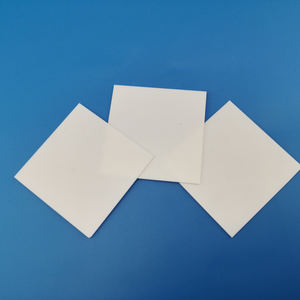
Industry Electrical CNC Machining Ceramic Parts Aluminum Nitride Ceramic ALN Heat Sink for CPU LED
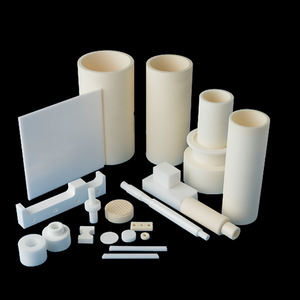
Double Sided Polished Aluminium Nitride Ceramic Plate ALN Sheet For LED
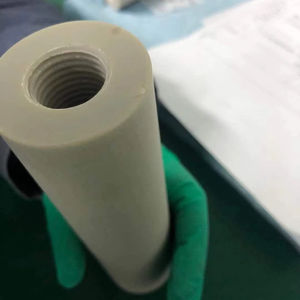
Round AlN Aluminum Nitride Ceramic Plate
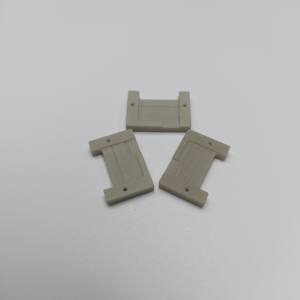