Discover Premium Ceramic Products | Durability & Elegance United | Advanced Ceramics
PRODUCT PARAMETERS
Description
Overview of Silicon Nitride Ceramics
Silicon Nitride Ceramics are high-performance materials known for their excellent mechanical properties, including strength, toughness, and resistance to wear, corrosion, and thermal shock, making them ideal for demanding applications in various industries.
Features of Silicon Nitride Ceramics
Exceptional hardness and wear resistance.
Superior mechanical strength and fracture toughness.
Excellent thermal stability and resistance to thermal shock.
High corrosion resistance in aggressive environments.
Low density contributing to lightweight components.
(High-Temperature Resistant 95% Alumina Ceramic Parts Silicon Nitride Molding Grinding Refractory Applications Custom Cutting)
Specifications of High-Temperature Resistant 95% Alumina Ceramic Parts Silicon Nitride Molding Grinding Refractory Applications Custom Cutting
Our high-temperature immune ceramic parts are made from 95% alumina and silicon nitride. These products deal with extreme heat and severe environments. The parts work in temperature levels approximately 1600 ° C. They maintain their toughness and shape under thermal tension. Alumina ceramic deals high solidity and use resistance. Silicon nitride includes sturdiness and thermal shock resistance. Both products are chemically stable. They stand up to rust from acids, antacid, and molten steels.
The products are formed and sintered for precision. Custom-made shapes and sizes are offered. Grinding makes sure tight tolerances and smooth surfaces. Components consist of tubes, plates, poles, and complicated geometries. They fit commercial devices needing warmth administration. Applications include heater cellular linings, kiln furnishings, and metal processing tools. They serve in aerospace, automobile, and electronics manufacturing.
These ceramics excel in refractory settings. They protect high-temperature areas and shield equipment. Their low thermal development reduces breaking throughout fast temperature level adjustments. Electrical insulation residential or commercial properties stop present leakage in heated systems. The material’s thickness obstructs gas and liquid infiltration. This expands component life expectancy in corrosive or unpleasant conditions.
Customized reducing allows adaptation to details machinery. Laser or diamond tools create precise sides and openings. Surface area therapies boost performance. Choices consist of sprucing up, finishing, or texturing. Parts are evaluated for toughness and thermal efficiency. Quality checks guarantee uniformity in every set.
The alumina-silicon nitride blend balances price and performance. It outshines metals and plastics in severe warmth. Upkeep requirements are low due to material durability. Downtime is decreased in commercial procedures. These porcelains are suitable for demanding applications. They supply trusted solution in environments where various other materials fail.
Industries use them for grinding parts. Their solidity decreases wear throughout material handling. High-temperature stability makes sure consistent operation. Custom develops fulfill one-of-a-kind tools demands. Engineers select these porcelains for long-lasting effectiveness. They work with automation and high-pressure systems.
The items satisfy worldwide standards for refractory products. They are devoid of impurities influencing performance. Basic material are sourced for pureness and uniformity. Production complies with strict protocols. Each part is deducible for quality assurance. These porcelains are a practical option for commercial obstacles. They take care of warm, wear, and corrosion without degrading.
(High-Temperature Resistant 95% Alumina Ceramic Parts Silicon Nitride Molding Grinding Refractory Applications Custom Cutting)
Applications of High-Temperature Resistant 95% Alumina Ceramic Parts Silicon Nitride Molding Grinding Refractory Applications Custom Cutting
High-temperature immune 95% alumina ceramic components are extensively made use of in sectors requiring sturdiness under extreme warm. These components include 95% alumina, making them excellent for high-stress atmospheres. They manage temperature levels over 1600 ° C without losing toughness. Usual applications include heater linings, warmth treatment devices, and steel handling devices. Their resistance to thermal shock protects against splitting during quick temperature modifications. This makes them reliable for long-term use in rough problems.
Silicon nitride molding includes another layer of efficiency. Silicon nitride ceramics excel in applications requiring both heat resistance and mechanical sturdiness. They are used in automotive engines, aerospace parts, and cutting devices. Their low thermal growth reduces wear under duplicated heating & cooling. This material is additionally lightweight, making it suitable for parts where weight savings issue.
Grinding applications gain from the firmness of alumina ceramics. They are made use of in grinding media, abrasive tools, and accuracy machining parts. Their wear resistance prolongs tools lifespan, lowering downtime and upkeep expenses. In sectors such as mining or electronic devices producing, consistent efficiency under rubbing is crucial. Alumina porcelains guarantee smooth operations even under hefty loads.
Refractory applications rely upon these ceramics for insulation and architectural support. They line kilns, reactors, and burners, protecting equipment from severe heat and chemical rust. Their stability at heats stops contamination in procedures like glass manufacturing or steelmaking. Custom shapes and sizes are attainable, making sure compatibility with intricate commercial setups.
Personalized reducing solutions allow tailored options for certain needs. Precision machining creates get rid of limited tolerances for electronics, medical devices, or energy systems. Advanced techniques like laser cutting or CNC grinding make certain precision. This flexibility fulfills needs for one-of-a-kind geometries or specialized surface finishes. Industries calling for precise specifications utilize these services to maximize performance.
The mix of high-temperature resistance, mechanical strength, and versatility makes 95% alumina and silicon nitride porcelains important in modern-day manufacturing. Their usage extends sectors from hefty industry to innovative modern technology, offering options where typical products fall short.
Company Introduction
Advanced Ceramics founded on October 17, 2014, is a high-tech enterprise committed to the research and development, production, processing, sales and technical services of ceramic relative materials and products.. Since its establishment in 2014, the company has been committed to providing customers with the best products and services, and has become a leader in the industry through continuous technological innovation and strict quality management.
Our products includes but not limited to Silicon carbide ceramic products, Boron Carbide Ceramic Products, Boron Nitride Ceramic Products, Silicon Carbide Ceramic Products, Silicon Nitride Ceramic Products, Zirconium Dioxide Ceramic Products, Quartz Products, etc. Please feel free to contact us.(nanotrun@yahoo.com)
Payment Methods
T/T, Western Union, Paypal, Credit Card etc.
Shipment Methods
By air, by sea, by express, as customers request.
5 FAQs of High-Temperature Resistant 95% Alumina Ceramic Parts Silicon Nitride Molding Grinding Refractory Applications Custom Cutting
High-temperature resistant 95% alumina ceramic parts are advanced components designed for extreme environments. Below are answers to common questions about these products.
What are high-temperature resistant 95% alumina ceramic parts?
These parts are made from alumina ceramic material containing 95% aluminum oxide. They handle intense heat, resist wear, and work in harsh chemical conditions. Industries like aerospace, metallurgy, and electronics use them for their durability and stability.
How much heat can these parts withstand?
They operate continuously at temperatures up to 1650°C (3000°F). Short-term exposure allows higher limits. This makes them ideal for furnaces, kilns, and machinery exposed to extreme heat.
Where are these ceramic parts typically used?
Applications include linings for industrial heaters, insulators in electrical systems, and components in metal processing equipment. They also serve in grinding tools due to their hardness and in refractory setups requiring thermal shock resistance.
Can these parts be customized for specific needs?
Yes. Manufacturers offer custom cutting, shaping, and sizing. Precision grinding ensures tight tolerances. Holes, threads, or complex geometries are achievable to match unique machinery or process requirements.
Why choose alumina ceramic over other materials?
Metals melt or corrode under high heat. Plastics degrade. Alumina ceramics keep strength and shape even in extreme conditions. They resist chemical erosion, reduce energy loss through insulation, and last longer than alternatives.
Silicon nitride molding is another option for high-performance applications. It offers higher toughness than alumina but costs more. The choice depends on budget and specific technical needs.
Proper handling during installation is crucial. Avoid mechanical impact before use. Follow guidelines for thermal cycling to prevent cracks. Regular inspections ensure long-term performance.
(High-Temperature Resistant 95% Alumina Ceramic Parts Silicon Nitride Molding Grinding Refractory Applications Custom Cutting)
REQUEST A QUOTE
RELATED PRODUCTS
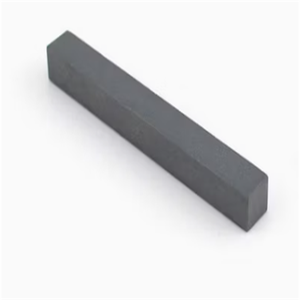
0.4mm-100mm G5-G40 Ceramic Balls Silicon Nitride Ball Si3n4 For Bearings Silicon Carbide Beads
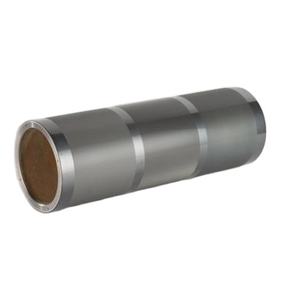
High Strength Black High Temperature Resistance Si3n4 Silicon Nitride Tube Silicon Nitride Ceramic
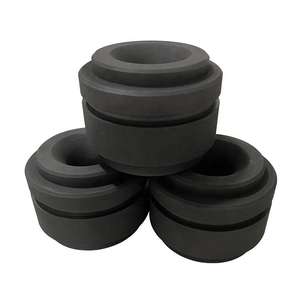
Welding Silicon Nitride Si3N4 Ceramic Dowel Location Pin
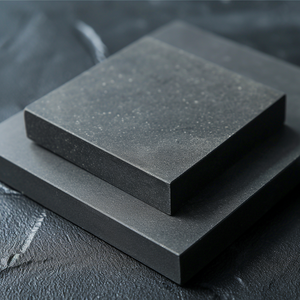
Customized Silicon Nitride Ceramic Ball Silicon Nitride Ceramic SI3N4 Ball Bearing Ball 0.8-25mm
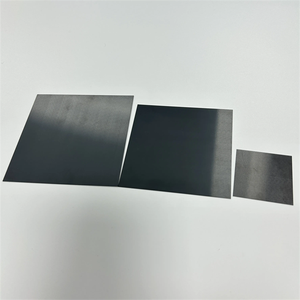
High Temperature Material Si3n4 Powder High Purity Nano Silicon Nitride for Refractory Ceramic
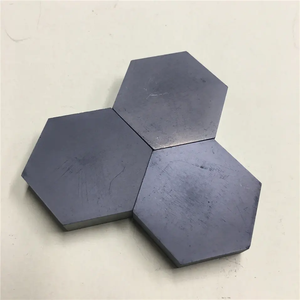