Discover Premium Ceramic Products | Durability & Elegance United | Advanced Ceramics
PRODUCT PARAMETERS
Description
Overview of aluminum nitride ceramics
Aluminum Nitride Ceramic is an advanced ceramic material with aluminum nitride as the main component. It has been widely used in electronics, optics, and mechanics due to its unique properties.
Features of aluminum nitride ceramics
High thermal conductivity: Aluminum nitride ceramics have relatively high thermal conductivity, usually between 170-260 W/m·K, which makes it an excellent heat dissipation material. It is especially suitable for electronic devices that require efficient heat dissipation, such as substrate materials for power semiconductor devices.
Good electrical insulation: Despite its high thermal conductivity, aluminum nitride ceramics are excellent insulators of electricity, which can effectively prevent current leakage and ensure the safe operation of electronic components.
Low dielectric constant and dielectric loss: These characteristics make aluminum nitride ceramics very suitable for use in high-frequency circuits because it can reduce energy loss during signal transmission.
High temperature resistance: Aluminum nitride ceramics can maintain structural stability and strength at extremely high temperatures. Its melting point is about 2800°C, so it is suitable for applications in high temperature environments.
Low thermal expansion coefficient: Compared with semiconductor materials such as silicon, aluminum nitride has a lower thermal expansion coefficient, which means it has better dimensional stability when the temperature changes, which helps improve packaging reliability.
Corrosion resistance: Aluminum nitride ceramics have good chemical stability to most molten metals and are not easily oxidized or corroded, allowing them to perform well in harsh environments.
High mechanical strength: Although not as hard as some other types of ceramic materials, aluminum nitride ceramics still provide enough mechanical strength to allow them to be used in many structural applications.
(Al2O3 Alumina and AlN Aluminum Nitride Ceramic Substrates)
Specifications of Al2O3 Alumina and AlN Aluminum Nitride Ceramic Substrates
Al2O3 alumina ceramic substratums and AlN aluminum nitride ceramic substratums serve key functions in electronic devices and industrial applications. Alumina substrates contain aluminum oxide as the main component. Typical pureness levels include 96% and 99.5%. Greater pureness boosts efficiency but elevates costs. Alumina offers great thermal conductivity, normally in between 20-30 W/mK. It gives solid electrical insulation, high mechanical stamina, and resistance to wear. Running temperatures rise to 1600 ° C. This product works well in circuits, insulators, and high-temperature settings. Its cost-effectiveness makes it prominent for general-purpose usage.
Aluminum nitride substratums utilize light weight aluminum nitride as the main product. Thermal conductivity is a lot greater than alumina, ranging from 140-180 W/mK. This makes AlN perfect for applications needing reliable warmth dissipation. The thermal development coefficient matches silicon carefully. This decreases stress in semiconductor product packaging. AlN preserves security at temperature levels going beyond 2000 ° C. Electrical insulation stays strong even under extreme problems. The product resists chemical corrosion and plasma disintegration.
Alumina substrates are less expensive and much easier to generate. They suit standard digital elements like LED illumination, sensors, and power modules. AlN substratums cost more due to complicated production. They fit high-performance areas like high-power electronic devices, RF tools, and laser diodes. AlN’s thermal monitoring supports innovative innovations such as 5G base stations and electrical lorry systems.
Mechanical buildings vary between both. Alumina has higher flexural toughness, around 300-400 MPa. AlN standards 300-350 MPa. Surface finish options consist of brightened, unfinished, or metallized layers. Density arrays from 0.25 mm to numerous millimeters. Custom sizes and shapes are offered for both products.
Alumina substrates take care of modest thermal lots. AlN substrates manage intense warmth in portable layouts. Material choice depends upon thermal requirements, budget plan, and application specifics. Designers usually choose alumina for cost-sensitive projects. AlN comes to be required when warmth dissipation is critical. Both materials satisfy sector criteria for dependability. They allow long lasting services across consumer electronics, automotive systems, aerospace parts, and commercial machinery. Correct selection makes sure optimal performance and longevity.
(Al2O3 Alumina and AlN Aluminum Nitride Ceramic Substrates)
Applications of Al2O3 Alumina and AlN Aluminum Nitride Ceramic Substrates
Alumina (Al2O3) and aluminum nitride (AlN) ceramic substrates serve essential roles in innovative markets. Alumina ceramic substratums are commonly utilized in electronics. They supply solid electric insulation and high thermal security. Circuits and power modules count on them for effective heat dissipation. Alumina resists chemical rust and mechanical wear. Industrial devices uses alumina components in high-temperature or abrasive atmospheres. These parts last longer under tension. Medical tools utilize alumina for implants and surgical tools. The material is biocompatible and risk-free for contact with bodily cells. Automotive systems use alumina sensing units and ignition parts. These components perform dependably in severe engine conditions.
Aluminum nitride substrates excel in thermal conductivity. They move heat faster than alumina. High-power digital devices like LED chips and semiconductor modules use AlN. Warm buildup decreases device lifespan. AlN keeps temperatures stable. LED lights systems depend on AlN for heat administration. Brighter LEDs need reliable air conditioning. AlN substrates prevent getting too hot. Superhigh frequency (RF) components use AlN for signal stability. High-frequency applications create warmth. AlN maintains performance without signal loss. Aerospace systems use AlN for radar and communication hardware. The material holds up against fast temperature level changes and mechanical stress.
Alumina and AlN vary in cost and application focus. Alumina is a lot more budget-friendly. It suits general-purpose insulation and wear resistance. AlN prices a lot more but executes better in high thermal tons circumstances. Engineers pick based upon warmth monitoring requirements. Both materials are machined into precise shapes. Laser reducing and grinding create slim, complicated designs. Surface area coatings enhance bonding with steel layers or circuits. Ceramic substrates allow miniaturization in electronic devices. Smaller devices need products that take care of greater power thickness. Alumina and AlN satisfy these needs across markets. Their properties drive advancement in electronics, medical care, automotive, and aerospace technologies.
Company Introduction
Advanced Ceramics founded on October 17, 2014, is a high-tech enterprise committed to the research and development, production, processing, sales and technical services of ceramic relative materials and products.. Since its establishment in 2014, the company has been committed to providing customers with the best products and services, and has become a leader in the industry through continuous technological innovation and strict quality management.
Our products includes but not limited to Silicon carbide ceramic products, Boron Carbide Ceramic Products, Boron Nitride Ceramic Products, Silicon Carbide Ceramic Products, Silicon Nitride Ceramic Products, Zirconium Dioxide Ceramic Products, Quartz Products, etc. Please feel free to contact us.(nanotrun@yahoo.com)
Payment Methods
T/T, Western Union, Paypal, Credit Card etc.
Shipment Methods
By air, by sea, by express, as customers request.
5 FAQs of Al2O3 Alumina and AlN Aluminum Nitride Ceramic Substrates
Al2O3 alumina and AlN aluminum nitride ceramic substrates are widely used in electronics. Here are 5 FAQs about them. What is the main difference between Al2O3 and AlN substrates? Al2O3 has lower thermal conductivity but costs less. AlN offers higher thermal conductivity, making it better for high-power devices. AlN is also harder to manufacture, raising its price. Which industries use these substrates? Al2O3 is common in consumer electronics, LED lighting, and automotive sensors. AlN suits high-performance areas like aerospace, power modules, and RF components. Both handle harsh environments due to their heat and chemical resistance. How does thermal conductivity affect performance? Higher thermal conductivity moves heat away faster. AlN’s conductivity is 5-10 times higher than Al2O3. This prevents overheating in dense circuits or high-power setups. Al2O3 works for basic applications where heat buildup is manageable. Are these substrates customizable? Yes. Both come in various sizes, thicknesses, and surface finishes. Metal coatings like gold or copper can be added for soldering or wiring. Laser drilling creates precise holes for complex circuits. Custom shapes are possible but may increase costs. What handling precautions are needed? Avoid mechanical stress during installation. Both materials are brittle. Clean surfaces before attaching components to prevent bonding issues. Store in dry conditions to minimize moisture absorption. AlN is more sensitive to contamination—use gloves to protect its surface.
(Al2O3 Alumina and AlN Aluminum Nitride Ceramic Substrates)
REQUEST A QUOTE
RELATED PRODUCTS
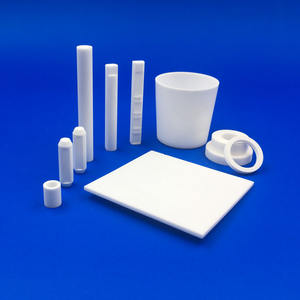
CNC Machining Aluminum Nitride Aln Ceramic Square Crucible Ring/Substrate/Parts
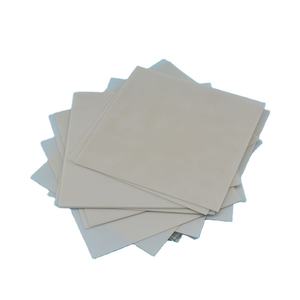
High Quality Porcelain Ceramic Substrate Sheet High Temperature Resistance Aluminum Nitride Heat Sink ALN Ceramic Plate
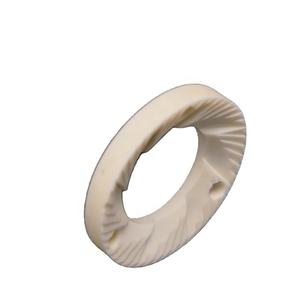
High Precision AlN Bar Aluminum Nitride Ceramic Rod
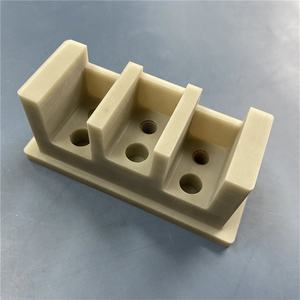
Aluminum Nitride Ceramic Disc AlN Substrate
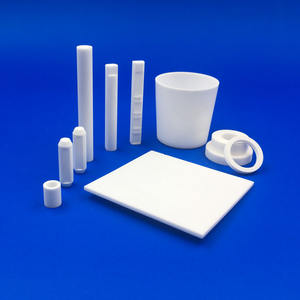
High Quality Thermal Conductive Sheet AlN Aluminum Nitride Ceramic Substrate
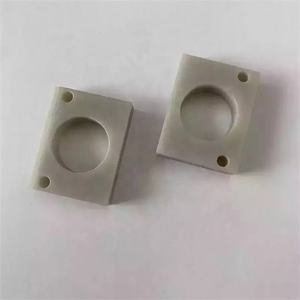