Discover Premium Ceramic Products | Durability & Elegance United | Advanced Ceramics
PRODUCT PARAMETERS
Description
Overview of Silicon Carbide Ceramics
Silicon Carbide (SiC) ceramics are renowned for their outstanding mechanical properties, including high hardness, strength at elevated temperatures, and excellent thermal shock resistance. These materials are pivotal in cutting-edge industrial applications, from abrasives to aerospace components, due to their unique combination of properties.
Features of Silicon Carbide Ceramics
High Hardness: Exceptional wear resistance.
Thermal Shock Resistance: Can withstand rapid temperature changes.
Chemical Stability: Resistant to most chemicals.
High Thermal Conductivity: Efficient heat dissipation.
Low Density: Lightweight for its strength.
(SiC Silicon Carbide Ceramic Foam Ceramic Foam Filter for Foundry)
Specification of SiC Silicon Carbide Ceramic Foam Ceramic Foam Filter for Foundry
The SiC Silicon Carbide Ceramic Foam Filter is created for shop applications. It gets rid of impurities from molten metals. This boosts casting high quality. The filter is constructed from silicon carbide. This material offers high-temperature resistance. It works in atmospheres up to 1600 ° C. The structure is open-cell foam. This enables smooth steel flow. It traps non-metallic incorporations successfully. The filter has a three-dimensional network. This makes sure uniform filtration.
The product comes in multiple pore dimensions. Usual options are 10 PPI, 20 PPI, and 30 PPI. PPI means pores per inch. Smaller pores capture finer contaminations. Larger pores manage greater circulation prices. Individuals pick based on steel type and casting needs. The filters are chemically secure. They withstand corrosion from molten aluminum, iron, and steel. This expands their service life.
Physical strength is an essential function. Silicon carbide gives high mechanical sturdiness. The filters hold up against thermal stress during quick temperature modifications. They prevent splitting or warping. This dependability reduces downtime in casting operations. The product has low thermal development. This keeps structural stability.
Setup is simple. The filter is positioned in eviction system. Molten steel travels through it before entering the mold. The process eliminates slag, oxides, and various other contaminants. This causes cleaner spreadings. Surface area issues are minimized. Mechanical buildings of end products boost.
The filters are recyclable in many cases. This relies on operating problems. They lower waste compared to disposable choices. Manufacturing costs reduce. Power intake is enhanced. Factories achieve higher performance.
Applications include light weight aluminum spreading, pliable iron manufacturing, and steel creating. Automotive and aerospace markets use these filters. They fulfill rigorous high quality criteria. Customized sizes and shapes are offered. Specifications line up with global factory needs. Performance is consistent throughout batches.
The product is packaged to prevent damages during delivery. Storage referrals consist of keeping it dry. Handling need to stay clear of harsh contact. This protects the foam structure. Technical assistance is attended to use guidance.
(SiC Silicon Carbide Ceramic Foam Ceramic Foam Filter for Foundry)
Applications of SiC Silicon Carbide Ceramic Foam Ceramic Foam Filter for Foundry
SiC silicon carbide ceramic foam filters play a vital role in foundry procedures. These filters tidy molten steel by capturing pollutants during casting. They are mostly used in aluminum, iron, and steel foundries to improve product quality. The permeable structure of the ceramic foam permits steel to flow efficiently while capturing undesirable fragments like oxides or slag. This decreases defects in final castings, making sure stronger, more reputable elements.
Light weight aluminum casting advantages greatly from SiC ceramic foam filters. Light weight aluminum conveniently reacts with oxygen, creating oxides that weaken metal structures. The filters remove these oxides, generating cleaner casts with much better surface finish. This is essential for vehicle parts or aerospace components where also small imperfections can trigger failings.
Iron and steel foundries use these filters to handle higher temperatures. SiC ceramic foam withstands severe warmth without breaking down. It efficiently removes non-metallic additions in molten steel, improving mechanical properties. The result is higher-grade steel for construction devices or machinery parts.
Financial investment casting relies on ceramic foam filters for precision. Facility mold and mildews require ultra-clean metal to catch great details. The filters avoid clogging in mold networks, making certain accurate duplication of elaborate designs. This is essential for fashion jewelry, wind turbine blades, or clinical gadgets.
The filters conserve money by expanding tools life. They protect nozzles, mold and mildews, and ladles from wear triggered by contaminations. Fewer replacements imply lower maintenance expenses. They also reduced waste by minimizing defective casts, saving basic materials and energy.
The filters are eco-friendly. They lessen slag and dross, reducing landfill waste. Efficient metal use decreases power intake throughout remelting. This straightens with sustainability objectives in manufacturing.
SiC ceramic foam filters last longer than conventional choices. Their resistance to thermal shock and chemical disintegration makes sure regular efficiency. Factories obtain reliable purification over numerous cycles, enhancing performance. Making use of these filters enhances casting quality while streamlining procedures across industries.
Company Introduction
Advanced Ceramics founded on October 17, 2014, is a high-tech enterprise committed to the research and development, production, processing, sales and technical services of ceramic relative materials and products.. Since its establishment in 2014, the company has been committed to providing customers with the best products and services, and has become a leader in the industry through continuous technological innovation and strict quality management.
Our products includes but not limited to Silicon carbide ceramic products, Boron Carbide Ceramic Products, Boron Nitride Ceramic Products, Silicon Carbide Ceramic Products, Silicon Nitride Ceramic Products, Zirconium Dioxide Ceramic Products, Quartz Products, etc. Please feel free to contact us.(nanotrun@yahoo.com)
Payment Methods
T/T, Western Union, Paypal, Credit Card etc.
Shipment Methods
By air, by sea, by express, as customers request.
5 FAQs of SiC Silicon Carbide Ceramic Foam Ceramic Foam Filter for Foundry
1. What is a SiC silicon carbide ceramic foam filter used for in foundries?
It removes impurities from molten metal during casting. The filter traps non-metallic particles like slag or oxides. This improves metal quality. It reduces defects in final cast products. Foundries use it for aluminum, iron, and steel casting.
2. How does the ceramic foam filter work?
The filter has a porous structure with interconnected cells. Molten metal flows through these pores. Solid impurities get caught in the filter’s network. Clean metal passes through. This ensures smoother casting and fewer cracks or voids.
3. What makes silicon carbide better than other filter materials?
Silicon carbide handles extreme heat without breaking. It resists thermal shock better than alumina or carbon-based filters. It lasts longer in high-temperature environments. The material doesn’t react with most molten metals. This keeps the metal pure.
4. What temperatures can the SiC ceramic foam filter withstand?
It works in temperatures up to 1600°C (2912°F). This covers most foundry applications. It stays stable even with rapid heating or cooling. The structure stays intact under stress. This reliability prevents filter failure during casting.
5. How long does one filter last? Can it be reused?
Filters are single-use. They degrade slightly after contact with molten metal. Reusing them risks contamination or structural failure. Each filter works for one pour. The cost is low compared to improved product quality. Replace filters for each casting batch.
(SiC Silicon Carbide Ceramic Foam Ceramic Foam Filter for Foundry)
REQUEST A QUOTE
RELATED PRODUCTS
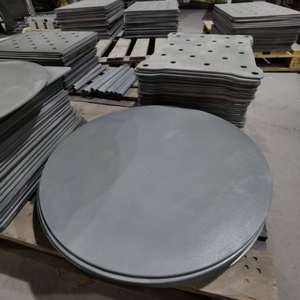
Custom Made Refractory Black Sic High Temperature Resistant Silicon Carbide Ceramic Tube
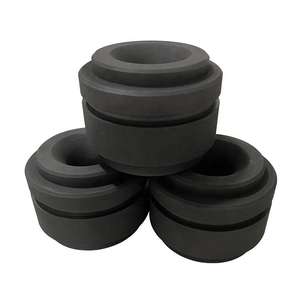
Factory Custom F4-F6000 Industrial Grit Blasting Silicon Carbide for Precision Ceramics Black Silicon Carbide Grit for Blasting
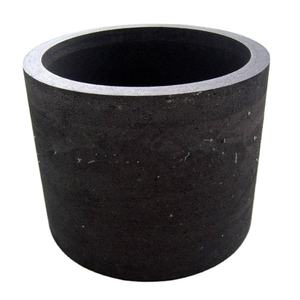
Electric Oven Igniter with Silicon Carbide Ceramic Hot Surface 5303935066 Accessory for Household Ovens
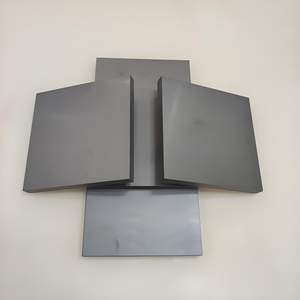
Silicon Carbide Foam Ceramic Sheet Silicon Carbide Foam Ceramic Filter for Cast Iron Various Cassette Stoves
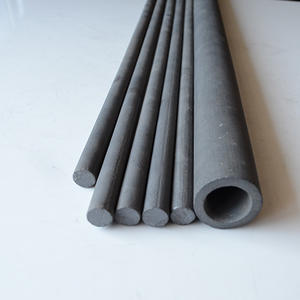
SIC Silicon Carbide Powder Ceramic Abrasives in Grit Shape for Grinding Blasting Cutting
