Discover Premium Ceramic Products | Durability & Elegance United | Advanced Ceramics
PRODUCT PARAMETERS
Description
Introduction to Alumina Ceramics
Alumina ceramics are known for their high hardness, wear resistance, corrosion resistance, good electrical insulation and high temperature stability. According to the different alumina content, it can be divided into different grades, such as 95 porcelain, 99 porcelain, etc., among which 99 porcelain refers to ceramic materials with an alumina content of 99%. As the alumina content increases, its mechanical strength and electrical insulation properties will also increase accordingly.
Characteristics of Alumina Ceramics
High Hardness: Alumina ceramics have extremely high hardness, which makes it very wear-resistant and suitable for manufacturing abrasive tools and parts that require wear resistance.
Wear resistance: Due to its high hardness, alumina ceramics show excellent wear resistance and are suitable for manufacturing parts for long-term use.
Corrosion resistance: Alumina ceramics have good resistance to most acids and alkalis, making them widely used in the chemical industry.
Good electrical insulation: As an excellent electrical insulating material, alumina ceramics are widely used in electronic and electrical products.
High temperature stability: Ability to withstand extremely high temperatures without significant physical or chemical changes, which makes it an ideal choice for applications in high temperature environments.
Biocompatibility: In the medical field, certain grades of alumina ceramics are used to make medical devices such as artificial joints due to their good biocompatibility.
(96% Alumina Al2o3 Ceramic Substrate Laser Cutting Customized Ceramic Disc)
Specifications of 96% Alumina Al2o3 Ceramic Substrate Laser Cutting Customized Ceramic Disc
The 96% Alumina Al2O3 Ceramic Substrate Laser Cutting Custom-made Ceramic Disc is made for high-performance commercial applications. This product utilizes advanced laser cutting innovation to guarantee specific forms and measurements. The product contains 96% alumina, providing outstanding mechanical toughness and thermal stability. It runs successfully in temperature levels approximately 1600 ° C, making it suitable for severe settings. The ceramic disc withstands chemical deterioration and wear, making certain long-term dependability.
Customization options include various sizes, densities, and geometric patterns. Laser cutting permits tight resistances, with minimum feature dimensions as tiny as 0.1 mm. The surface area coating is smooth, minimizing the demand for post-processing. This substrate is compatible with metallization processes, making it possible for simple combination into electronic circuits. Its high dielectric stamina sustains applications in high-frequency and high-voltage systems.
The ceramic disc is excellent for electronic devices, working as a base for circuit boards, sensors, and insulators. It is made use of in automotive systems for ignition parts and exhaust sensors. Medical devices take advantage of its biocompatibility and resistance to sterilization methods. Industrial equipment relies upon its durability in unpleasant or high-heat problems.
Key specifications include a density of 3.7 g/cm six and a hardness of 15 Grade point average. The thermal development coefficient is 7.2 x 10 ⁻⁶/ ° C, decreasing anxiety under temperature level adjustments. Electrical insulation exceeds 10 ¹² Ω · cm, preventing leakage currents. The material’s flexural toughness reaches 350 MPa, lowering damage threat during handling.
Custom-made orders accommodate specific opening patterns, ports, or edge accounts. Laser cutting ensures tidy sides without micro-cracks, maintaining architectural integrity. Preparations vary based on design complexity, with typical alternatives offered for quick shipment. Product packaging options protect the discs throughout delivery, stopping damage.
This product meets market requirements for top quality and efficiency. Testing includes look for dimensional accuracy, surface issues, and thermal shock resistance. Set uniformity is preserved via extensive quality control. Technical support is readily available to assist with design optimization and material selection.
The 96% Alumina Porcelain Disc combines accuracy engineering with robust product buildings. It addresses challenges sought after applications where standard materials stop working. Its flexibility makes it a preferred choice across numerous industries.
(96% Alumina Al2o3 Ceramic Substrate Laser Cutting Customized Ceramic Disc)
Applications of 96% Alumina Al2o3 Ceramic Substrate Laser Cutting Customized Ceramic Disc
The 96% alumina Al2O3 ceramic substratum laser-cut customized ceramic disc is a high-performance material utilized in several markets. It offers excellent thermal stability, high mechanical toughness, and solid electrical insulation. These residential or commercial properties make it optimal for demanding applications.
In electronic devices, the ceramic disc functions as a dependable base for circuit card. It deals with high temperatures without deforming. This is essential in power electronic devices. Devices like LED modules and semiconductor bundles utilize it. The product’s low thermal expansion makes sure parts stay aligned. Laser cutting enables accurate forms for complicated circuits.
The auto market utilizes these discs in sensors and ignition systems. They stand up to severe heat and resonance. Engine control systems count on their security. Personalized dimensions fit tight spaces in modern-day cars.
Medical devices gain from the product’s biocompatibility. It is made use of in imaging tools and surgical devices. Its electrical insulation prevents disturbance in sensitive tools. Laser-cut edges are smooth, reducing contamination dangers.
Industrial machinery uses ceramic discs as insulators in high-temperature procedures. They safeguard equipment in furnaces or welding systems. Their wear resistance prolongs element life. Customized shapes adapt to certain equipment designs.
Telecommunications tools makes use of these discs for signal honesty. They support high-frequency circuits in antennas and transmitters. The product’s low dielectric loss boosts performance.
Laser reducing allows fast, accurate personalization. Complicated geometries are feasible without endangering stamina. This flexibility meets distinct job demands.
The 96% alumina ceramic disc is economical for high-volume manufacturing. It reduces downtime by lasting longer than typical products. Industries select it for dependability and flexibility.
Its chemical resistance fits severe atmospheres. It carries out well in corrosive setups like chemical plants. This minimizes upkeep and replacement prices.
The mix of sturdiness and precision makes it a leading option for innovative modern technologies. Designers trust it for crucial applications where failing is not a choice.
Company Introduction
Advanced Ceramics founded on October 17, 2014, is a high-tech enterprise committed to the research and development, production, processing, sales and technical services of ceramic relative materials and products.. Since its establishment in 2014, the company has been committed to providing customers with the best products and services, and has become a leader in the industry through continuous technological innovation and strict quality management.
Our products includes but not limited to Silicon carbide ceramic products, Boron Carbide Ceramic Products, Boron Nitride Ceramic Products, Silicon Carbide Ceramic Products, Silicon Nitride Ceramic Products, Zirconium Dioxide Ceramic Products, Quartz Products, etc. Please feel free to contact us.(nanotrun@yahoo.com)
Payment Methods
T/T, Western Union, Paypal, Credit Card etc.
Shipment Methods
By air, by sea, by express, as customers request.
5 FAQs of 96% Alumina Al2o3 Ceramic Substrate Laser Cutting Customized Ceramic Disc
What is 96% alumina Al2O3 ceramic substrate?
96% alumina Al2O3 ceramic substrate is a high-performance material made mostly from aluminum oxide. It offers high thermal stability, strong mechanical strength, and excellent electrical insulation. This makes it ideal for applications needing durability under extreme temperatures or harsh environments.
How accurate is laser cutting for ceramic discs?
Laser cutting provides high precision. It achieves tight tolerances, often within ±0.05 mm. The process ensures clean edges without chipping or cracking. Complex shapes and fine details are possible. This method works well for custom designs needing exact specifications.
Can the ceramic discs be customized in size and shape?
Yes. Custom sizes and shapes are available. Laser cutting allows flexibility in design. Common shapes include circles, rectangles, and complex geometries. Thickness and diameter can be adjusted based on project needs. Specifications are tailored to fit specific industrial or electronic uses.
What industries use these laser-cut ceramic discs?
These discs are used in electronics, automotive, aerospace, and medical fields. They serve as circuit carriers, insulators, sensor components, or heat-resistant parts. Their reliability in high-temperature and high-stress environments makes them suitable for demanding applications.
Why pick laser cutting over other methods for alumina ceramics?
Laser cutting is faster and more precise than mechanical or manual methods. It reduces material waste and avoids tool wear. The non-contact process minimizes damage to the ceramic. This ensures consistent quality and reduces post-processing steps. It is cost-effective for both small and large production runs.
(96% Alumina Al2o3 Ceramic Substrate Laser Cutting Customized Ceramic Disc)
REQUEST A QUOTE
RELATED PRODUCTS
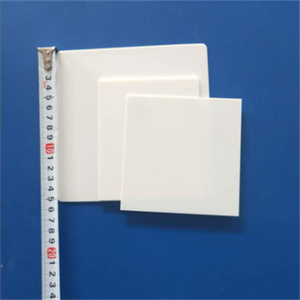
Alumina Ceramic Material and Industrial Ceramic Application Honeycomb Ceramic for RTO RCO
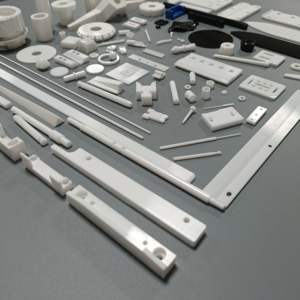
Alumina Ceramics Have Strong Chemical Stability and Resist Erosion in the Harsh Environment of Lime Kilns
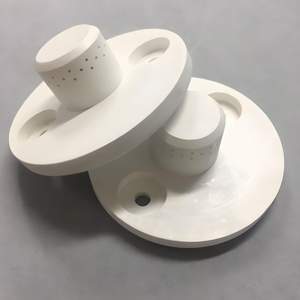
Industrial Alumina Ceramic Tube 99 Al2o3 Fireproof Alumina Tube Circle Alumina Tube
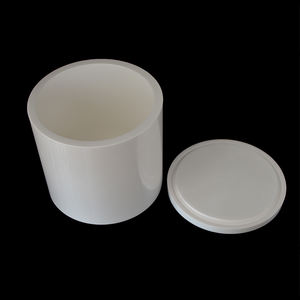
High Quality Steatite Ceramics for Industries Alumina Industrial Ceramics
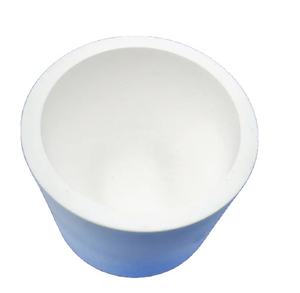
High Temperature Alumina Ceramic Sagger
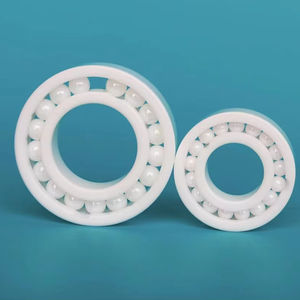