Discover Premium Ceramic Products | Durability & Elegance United | Advanced Ceramics
PRODUCT PARAMETERS
Description
Introduction to Alumina Ceramics
Alumina ceramics are known for their high hardness, wear resistance, corrosion resistance, good electrical insulation and high temperature stability. According to the different alumina content, it can be divided into different grades, such as 95 porcelain, 99 porcelain, etc., among which 99 porcelain refers to ceramic materials with an alumina content of 99%. As the alumina content increases, its mechanical strength and electrical insulation properties will also increase accordingly.
Characteristics of Alumina Ceramics
High Hardness: Alumina ceramics have extremely high hardness, which makes it very wear-resistant and suitable for manufacturing abrasive tools and parts that require wear resistance.
Wear resistance: Due to its high hardness, alumina ceramics show excellent wear resistance and are suitable for manufacturing parts for long-term use.
Corrosion resistance: Alumina ceramics have good resistance to most acids and alkalis, making them widely used in the chemical industry.
Good electrical insulation: As an excellent electrical insulating material, alumina ceramics are widely used in electronic and electrical products.
High temperature stability: Ability to withstand extremely high temperatures without significant physical or chemical changes, which makes it an ideal choice for applications in high temperature environments.
Biocompatibility: In the medical field, certain grades of alumina ceramics are used to make medical devices such as artificial joints due to their good biocompatibility.
(High-Performance 95% Alumina Ceramic Blocks)
Specifications of High-Performance 95% Alumina Ceramic Blocks
High-Performance 95% Alumina Ceramic Blocks are engineered for requiring industrial applications. These blocks consist of 95% aluminum oxide, ensuring superior toughness and resistance to severe problems. They preserve stable performance in high-temperature, harsh, or high-wear environments.
The material density ranges from 3.6 to 3.8 g/cm ³. This high density adds to phenomenal mechanical stamina. The blocks withstand compressive forces approximately 2200 MPa. They resist deformation under hefty tons. Surface solidity reaches 85 HRA, making them highly scratch-resistant. This residential or commercial property extends life span in rough setups.
Thermal security is a crucial function. The blocks handle temperatures approximately 1650 ° C without losing architectural integrity. Thermal shock resistance prevents fracturing throughout quick temperature modifications. Low thermal conductivity (20-30 W/m · K) permits effective heat insulation. This matches them for heating system linings or high-heat equipment components.
Electric insulation residential or commercial properties are exceptional. The dielectric strength goes beyond 15 kV/mm. This makes the blocks perfect for digital components needing insulation in high-voltage settings. They stand up to arc erosion and present leak. Chemical inertness makes sure compatibility with acids, antacid, and molten steels. They do not break down in responsive chemical arrangements.
Dimensional precision is guaranteed. Tolerances are controlled within ± 0.5% of specified measurements. Custom-made shapes and sizes are available. Machining alternatives consist of grinding, drilling, and polishing. Surface area coatings can be adjusted for certain friction or securing needs.
Applications extend multiple markets. They are utilized in semiconductor manufacturing for wafer-processing parts. Metallurgical plants employ them as crucibles or furnace bricks. Chemical processing units utilize them for pump seals and shutoff elements. Electronic devices count on them for protecting substrates and circuit service providers.
The blocks fulfill global top quality standards. Certifications include ISO 9001 and RoHS conformity. Set screening makes certain constant efficiency. Customized product blends are readily available for customized requirements. Packaging alternatives protect against damages during delivery. Technical support is provided for installment and maintenance.
These ceramic blocks offer an economical solution for high-stress applications. Their durability decreases replacement frequency. Minimal upkeep reduces functional downtime. Efficiency dependability sustains continuous commercial processes.
(High-Performance 95% Alumina Ceramic Blocks)
Applications of High-Performance 95% Alumina Ceramic Blocks
High-performance 95% alumina ceramic blocks are commonly used in markets needing resilience, heat resistance, and electrical insulation. These porcelains take care of extreme problems better than several metals or plastics. They are common in industrial equipment. Cutting tools, wear-resistant components, and components for heavy equipment rely on their solidity. They decrease downtime by lasting longer under rubbing and stress and anxiety.
The electronics market benefits from these ceramics. Circuit service providers, insulation layers, and sensing unit real estates utilize them. Their thermal stability avoids overheating in high-power devices. They preserve efficiency in environments with rapid temperature level changes. This makes them suitable for safeguarding delicate electronic parts.
Medical applications consist of surgical devices and implants. The product’s biocompatibility makes certain security in the human body. Prosthetic joints, dental implants, and imaging devices use alumina ceramics. They resist deterioration from bodily liquids and sanitation processes. This dependability supports lasting medical services.
Chemical handling plants make use of these blocks for pumps, shutoffs, and reactor cellular linings. They hold up against destructive acids and alkalis. Their non-reactive nature protects against contamination. This makes certain item purity in pharmaceuticals and chemicals.
Power industries like solar and battery systems utilize alumina porcelains. They protect high-voltage equipment and sustain extreme heat. Parts like thermal barrier and insulators in power plants rely on their security. This boosts security and effectiveness in energy production.
Automotive systems make use of these porcelains for sensors and engine components. They handle exhaust warmth and minimize emissions. Their electrical insulation secures onboard electronics. This adds to lorry integrity and efficiency.
These blocks additionally serve in aerospace for thermal barriers and engine elements. Their light-weight nature lowers fuel usage. They maintain toughness under high stress and resonance. This supports safer and much more efficient air travel.
Personalized shapes and sizes are feasible because of sophisticated production. Industries dressmaker alumina obstructs for certain needs. This flexibility increases their use across fields requiring precision and resilience. Their role in modern-day technology proceeds growing as needs for high-performance materials boost.
Company Introduction
Advanced Ceramics founded on October 17, 2014, is a high-tech enterprise committed to the research and development, production, processing, sales and technical services of ceramic relative materials and products.. Since its establishment in 2014, the company has been committed to providing customers with the best products and services, and has become a leader in the industry through continuous technological innovation and strict quality management.
Our products includes but not limited to Silicon carbide ceramic products, Boron Carbide Ceramic Products, Boron Nitride Ceramic Products, Silicon Carbide Ceramic Products, Silicon Nitride Ceramic Products, Zirconium Dioxide Ceramic Products, Quartz Products, etc. Please feel free to contact us.(nanotrun@yahoo.com)
Payment Methods
T/T, Western Union, Paypal, Credit Card etc.
Shipment Methods
By air, by sea, by express, as customers request.
5 FAQs of High-Performance 95% Alumina Ceramic Blocks
What are High-Performance 95% Alumina Ceramic Blocks? These blocks are made mainly from aluminum oxide. Around 95% of the material is alumina. The rest includes small amounts of other oxides. This mix creates a strong, dense ceramic. It works well in tough environments.
What benefits do these blocks offer? They handle high heat. They resist wear and chemicals. Their hardness makes them last longer under stress. They stay stable in extreme conditions. This reduces replacement needs.
What temperatures can they withstand? They work up to 1650°C. Going beyond this risks damage. They also manage sudden temperature changes. This avoids cracking from thermal shock.
Where are these blocks commonly used? They fit industries needing durability. Examples include metal processing, electronics, and chemical plants. They serve as liners, insulators, or parts in machinery. They protect equipment in harsh settings.
How should these blocks be maintained? Check them regularly for cracks or wear. Clean them with water or mild solvents. Avoid rough scrubbing. Replace blocks showing major damage. Proper care extends their lifespan.
(High-Performance 95% Alumina Ceramic Blocks)
REQUEST A QUOTE
RELATED PRODUCTS
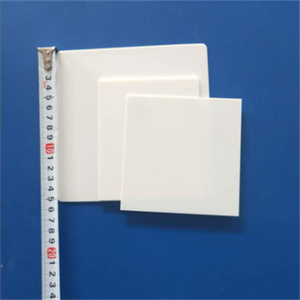
Alumina Ceramic Material and Industrial Ceramic Application Honeycomb Ceramic for RTO RCO
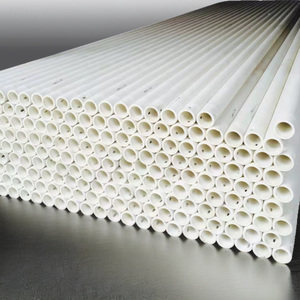
Heat Resistance Alumina Ceramic Sintering Plate Al2O3 Ceramic Block
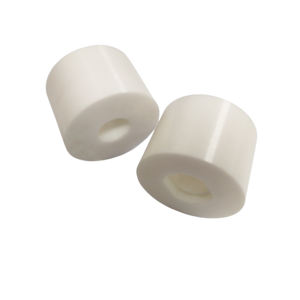
99% Alumina Ceramic Plate for Semiconductor/Medical/Electronics, High Purity, Wear Resistant, Insulating
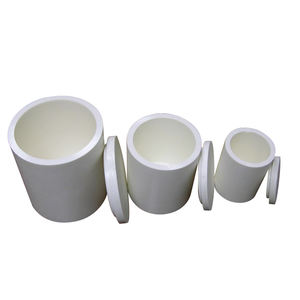
Large Diameter 99.7% Al2o3 High Alumina Ceramic Tube Factory
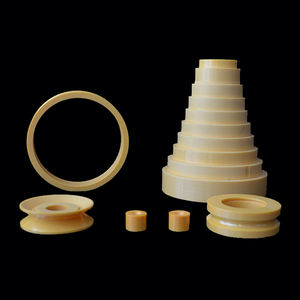
17%-19% AL2O3 Inert Alumina Ceramic Ball for Chemical Industry
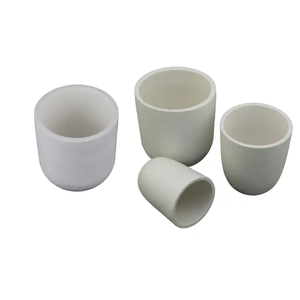