Discover Premium Ceramic Products | Durability & Elegance United | Advanced Ceramics
PRODUCT PARAMETERS
Description
Overview of Zirconium Dioxide Ceramics
Zirconium Dioxide Ceramics, known for their toughness and ability to withstand extreme temperatures, are widely used in medical, automotive, and industrial applications due to their unique properties.
Features of Zirconium Dioxide Ceramics
Exceptional fracture toughness
High thermal expansion
Excellent resistance to wear and corrosion
Biocompatibility for medical implants
(Calcium Stabilized Zirconium Oxide ZrO2 Zirconia Ceramic Flat Sheet Setters for Furnace)
Specifications of Calcium Stabilized Zirconium Oxide ZrO2 Zirconia Ceramic Flat Sheet Setters for Furnace
Calcium-Stabilized Zirconium Oxide (ZrO2) Zirconia Porcelain Apartment Sheet Setters are made for high-temperature furnace applications. The material incorporates calcium oxide (CaO) with zirconia to improve thermal stability. This stops stage changes during heating, making certain structural honesty approximately 1600 ° C. The setters are optimal for sintering, annealing, or heat-treating sensitive materials like advanced porcelains or digital elements.
Standard sizes range from 100×100 mm to 300×300 mm, with densities in between 3 mm and 10 mm. Customized measurements are readily available. The flat sheets feature a smooth surface coating (Ra ≤ 0.4 μm) to reduce get in touch with marks on workpieces. High density (≥ 5.8 g/cm FOUR) decreases porosity, improving toughness under repeated thermal cycles.
These zirconia setters resist thermal shock far better than alumina or silicon carbide alternatives. Quick temperature level adjustments (as much as 1000 ° C/hour) trigger very little stress buildup. The reduced thermal conductivity of zirconia makes certain also heat circulation, decreasing energy waste. Chemical inertness stops reactions with the majority of metals, oxides, or destructive ambiences in heater environments.
Applications include powder metallurgy, oral ceramic processing, and semiconductor part production. The sheets sustain specific positioning of components during firing, maintaining monotony under tons. Maximum tons capability depends on density, varying from 15 kg/cm TWO (3 mm) to 50 kg/cm TWO (10 mm). Running temperatures span 20 ° C to 1600 ° C in oxidizing or inert ambiences.
Upkeep is easy. Trendy the setters to area temperature level before managing. Clean with non-abrasive devices to prevent surface area damages. Normal assessments for micro-cracks or buckling ensure lasting performance. Replacement intervals differ based upon usage regularity and heating system problems.
The material’s low wear rate lessens particle contamination in high-purity processes. Compatibility with vacuum heating systems increases usability in specialized markets. Customized opening patterns or grooves can be added for details fixture demands. Lead times for customized orders commonly range from 2-4 weeks.
Calcium-stabilized zirconia uses price performance over yttria-stabilized qualities while maintaining comparable performance in a lot of common heating system setups. Bulk pricing is available for massive commercial individuals. Technical support helps with selecting optimal setter configurations based on heating system parameters and procedure objectives.
(Calcium Stabilized Zirconium Oxide ZrO2 Zirconia Ceramic Flat Sheet Setters for Furnace)
Applications of Calcium Stabilized Zirconium Oxide ZrO2 Zirconia Ceramic Flat Sheet Setters for Furnace
Calcium-stabilized zirconium oxide (ZrO2) zirconia ceramic level sheet setters are crucial in high-temperature furnace applications. These elements deal with extreme warmth while keeping architectural integrity. Industries like metallurgy, electronics, and aerospace count on them for processes calling for thermal stability.
These setters sustain products throughout sintering, annealing, and heat treatment. They avoid warping or contamination of delicate products like electronic parts or advanced alloys. Their reduced thermal conductivity makes sure even warmth circulation. This decreases energy waste and enhances procedure effectiveness.
Zirconia ceramic setters exceed typical materials like alumina or silicon carbide. Calcium stabilization enhances their resistance to thermal shock. They stand up to rapid temperature level adjustments without splitting. This makes them suitable for repeated home heating and cooling down cycles. Their chemical inertness stops responses with molten steels or aggressive ambiences.
In electronic devices manufacturing, these setters are made use of for shooting multilayer ceramic capacitors or circuit card. They maintain exact measurements under tension. This guarantees regular product top quality. Aerospace applications consist of forming wind turbine blades or other high-performance parts. The setters’ longevity allows prolonged use in demanding atmospheres.
Dental and clinical sectors utilize zirconia setters for generating implants or prosthetics. The material’s biocompatibility and stability meet strict health requirements. Heater operators benefit from minimized downtime. The setters need marginal maintenance and withstand wear.
Contamination dangers are reduced because of the non-porous surface area. This avoids pollutants moving to processed materials. The smooth coating protects against sticking. It streamlines post-process cleansing.
Expense financial savings come from extended life span. Zirconia setters outlast choices. Less replacements imply reduced functional prices. Their light-weight design eases handling. This reduces labor strain during heater loading.
Custom shapes and sizes are offered for specialized setups. Compatibility with numerous heating system types ensures wide usability. Makers prioritize these setters for vital high-temperature jobs. Performance reliability supports continual commercial procedures.
Company Introduction
Advanced Ceramics founded on October 17, 2014, is a high-tech enterprise committed to the research and development, production, processing, sales and technical services of ceramic relative materials and products.. Since its establishment in 2014, the company has been committed to providing customers with the best products and services, and has become a leader in the industry through continuous technological innovation and strict quality management.
Our products includes but not limited to Silicon carbide ceramic products, Boron Carbide Ceramic Products, Boron Nitride Ceramic Products, Silicon Carbide Ceramic Products, Silicon Nitride Ceramic Products, Zirconium Dioxide Ceramic Products, Quartz Products, etc. Please feel free to contact us.(nanotrun@yahoo.com)
Payment Methods
T/T, Western Union, Paypal, Credit Card etc.
Shipment Methods
By air, by sea, by express, as customers request.
5 FAQs of Calcium Stabilized Zirconium Oxide ZrO2 Zirconia Ceramic Flat Sheet Setters for Furnace
What is calcium-stabilized zirconium oxide ZrO2 zirconia ceramic flat sheet setters for furnaces? These setters are high-temperature tools made from zirconia ceramic. Calcium stabilizes the zirconia. This prevents cracks during heating or cooling. They hold materials in furnaces during processes like sintering. They ensure even heat transfer. They last longer than other materials.
Why use zirconia ceramic setters in high-temperature furnaces? Zirconia ceramic handles extreme heat well. It stays stable up to 1600°C. It resists thermal shock. This means it won’t break when temperatures change fast. It doesn’t react with most chemicals. This keeps materials pure during firing. It also saves money by lasting many cycles.
What temperatures can zirconia ceramic setters withstand? These setters work continuously up to 1600°C. Short-term use allows higher peaks. The exact limit depends on the furnace atmosphere. In oxidizing conditions, performance stays strong. Reducing environments might lower the limit slightly. Always check manufacturer guidelines for specific setups.
How do zirconia setters compare to alumina or silicon carbide setters? Zirconia has better fracture toughness. It resists cracks better than alumina. It handles thermal stress better than silicon carbide. It’s lighter than both. This reduces furnace load. It also wears slower. This means fewer replacements. Costs might be higher initially, but long-term savings offset this.
What maintenance do zirconia ceramic setters need? Clean setters after each use. Remove debris with a soft brush. Avoid abrasive tools. Check for chips or cracks before reuse. Small defects can grow under heat. Store them flat or stacked evenly. Don’t drop them. Zirconia is tough but brittle. Handle carefully to prevent breakage.
(Calcium Stabilized Zirconium Oxide ZrO2 Zirconia Ceramic Flat Sheet Setters for Furnace)
REQUEST A QUOTE
RELATED PRODUCTS
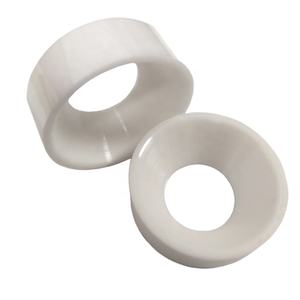
ZrO2 Zirconium Oxide Powder Ceramic Material for the Production of Dental Zirconia Powder
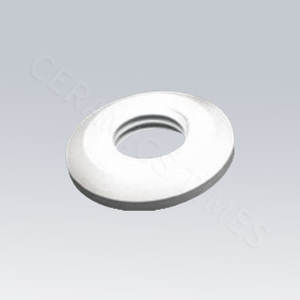
Pure Chemical Zirconium Nano Grade Ceramic Zirconia Powder Non-metal ZrO2 Zirconium Powder
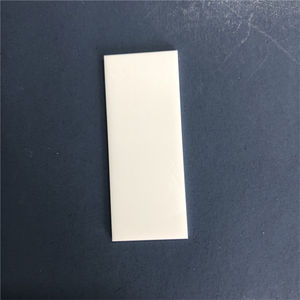
Factory Production Zirconia Ceramic
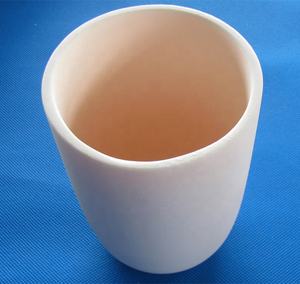
CNC Machining Zirconia Ceramic Components Structural Machining Ceramic Parts
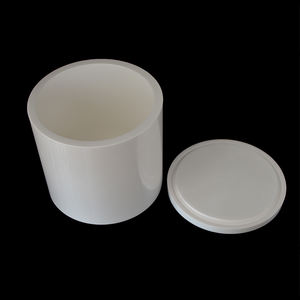
Dental Ceramic Zirconia Block CAD/CAM Open System 98mm Disk Dental Laboratory Materials
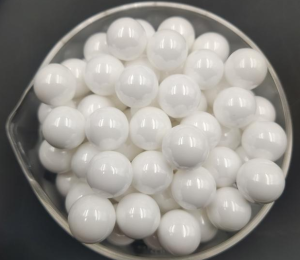