Discover Premium Ceramic Products | Durability & Elegance United | Advanced Ceramics
PRODUCT PARAMETERS
Description
Introduction to Alumina Ceramics
Alumina ceramics are known for their high hardness, wear resistance, corrosion resistance, good electrical insulation and high temperature stability. According to the different alumina content, it can be divided into different grades, such as 95 porcelain, 99 porcelain, etc., among which 99 porcelain refers to ceramic materials with an alumina content of 99%. As the alumina content increases, its mechanical strength and electrical insulation properties will also increase accordingly.
Characteristics of Alumina Ceramics
High Hardness: Alumina ceramics have extremely high hardness, which makes it very wear-resistant and suitable for manufacturing abrasive tools and parts that require wear resistance.
Wear resistance: Due to its high hardness, alumina ceramics show excellent wear resistance and are suitable for manufacturing parts for long-term use.
Corrosion resistance: Alumina ceramics have good resistance to most acids and alkalis, making them widely used in the chemical industry.
Good electrical insulation: As an excellent electrical insulating material, alumina ceramics are widely used in electronic and electrical products.
High temperature stability: Ability to withstand extremely high temperatures without significant physical or chemical changes, which makes it an ideal choice for applications in high temperature environments.
Biocompatibility: In the medical field, certain grades of alumina ceramics are used to make medical devices such as artificial joints due to their good biocompatibility.
(Alumina Precision Ceramic Part Alumina Ceramic Roller)
Specifications of Alumina Precision Ceramic Part Alumina Ceramic Roller
Alumina precision ceramic rollers are made from high-purity aluminum oxide. They are designed for demanding industrial applications. The material contains over 99% alumina. This guarantees high stamina and put on resistance. These rollers deal with severe temperature levels. They operate in settings up to 1600 ° C. Thermal shock resistance is superb. Quick temperature level modifications trigger very little damage. The thickness varies between 3.8 to 3.9 g/cm FIVE. This contributes to their durability. Solidity degrees get to 80-90 HRA. They stand up to abrasion effectively. Surface surfaces are smooth. Regular roughness worths are below Ra 0.4 μm. This decreases friction throughout operation. Dimensional accuracy is tight. Tolerances stay within ± 0.1 mm. Customized sizes are offered. Typical diameters vary from 5 mm to 200 mm. Lengths can exceed 1000 mm. Electric insulation properties are strong. They protect against existing leak in delicate setups. Chemical resistance is one more vital feature. Acids and alkalis trigger little deterioration. These rollers suit high-speed processes. They keep stability under mechanical anxiety. Applications include glass production. They lead glass sheets through annealing heating systems. Semiconductor production uses them for wafer handling. Kilns utilize them for relocating ceramic products. Fabric machinery relies upon them for warmth treatment phases. Automotive systems make use of these rollers in coating processes. Benefits include longer life span. Substitute regularity goes down compared to steel rollers. Upkeep demands are reduced. No lubrication is required. Costs minimize over time as a result of very little downtime. Industries adopting this product period electronic devices, aerospace, and energy. Performance stays consistent in harsh problems. Personalized layouts fit details equipment layouts. Evaluating guarantees each roller fulfills quality criteria. Technical support is offered for integration challenges.
(Alumina Precision Ceramic Part Alumina Ceramic Roller)
Applications of Alumina Precision Ceramic Part Alumina Ceramic Roller
Alumina precision ceramic parts are commonly made use of in industries requiring long lasting and reputable elements. Alumina ceramic rollers attract attention for their high efficiency in hard conditions. These rollers manage extreme warmth. They work well in kilns and heating systems where temperature levels exceed 1500 ° C. Steel rollers fall short right here. Alumina rollers keep their shape and stamina. This makes them excellent for glass production and steel processing.
The electronics industry makes use of alumina ceramic rollers for handling fragile materials. They relocate silicon wafers and slim films without causing damage. Their smooth surface protects against scratches. Their electric insulation stops static build-up. This safeguards delicate parts throughout production.
In vehicle manufacturing, alumina rollers use coverings and paints uniformly. They stand up to use from unpleasant materials. This minimizes downtime for replacements. Their chemical security allows them work with rough solvents. This keeps processes efficient and regular.
Food and pharmaceutical sectors rely on alumina rollers for hygiene. They do not respond with liquids or chemicals. This protects against contamination. Their non-porous surface quits bacteria development. Cleaning them is simple. They satisfy stringent safety criteria.
Alumina ceramic rollers last longer than steel or rubber choices. They reduced maintenance costs. Their lightweight style reduces power usage in moving systems. Factories save money over time. These rollers adjust to personalized shapes and sizes. They fit details equipment demands.
High-precision applications take advantage of alumina’s stability. It does not expand or acquire much with temperature level modifications. This maintains dimensions exact in laboratories and screening setups. Medical tools utilize them for consistent efficiency in scans and diagnostics.
Alumina ceramic rollers deal with heavy lots without bending. They remain solid under pressure. Mining and building devices utilize them for relocating basic materials. Their sturdiness withstands fractures and chips. This reliability keeps production lines running smoothly.
These rollers work in environments with solid acids or alkalis. They do not wear away. Chemical plants use them for transferring destructive materials. Their resistance guarantees long-term use without deterioration. This decreases waste and replacement frequency.
Alumina accuracy ceramic parts address troubles where other products stop working. Their adaptability makes them essential throughout numerous fields. They enhance efficiency and item top quality. Organizations pick them for reliable efficiency popular settings.
Company Introduction
Advanced Ceramics founded on October 17, 2014, is a high-tech enterprise committed to the research and development, production, processing, sales and technical services of ceramic relative materials and products.. Since its establishment in 2014, the company has been committed to providing customers with the best products and services, and has become a leader in the industry through continuous technological innovation and strict quality management.
Our products includes but not limited to Silicon carbide ceramic products, Boron Carbide Ceramic Products, Boron Nitride Ceramic Products, Silicon Carbide Ceramic Products, Silicon Nitride Ceramic Products, Zirconium Dioxide Ceramic Products, Quartz Products, etc. Please feel free to contact us.(nanotrun@yahoo.com)
Payment Methods
T/T, Western Union, Paypal, Credit Card etc.
Shipment Methods
By air, by sea, by express, as customers request.
5 FAQs of Alumina Precision Ceramic Part Alumina Ceramic Roller
Alumina ceramic is a technical ceramic material made mainly from aluminum oxide. It offers high hardness, excellent heat resistance, and strong chemical stability. These properties make it ideal for industrial applications requiring durability under extreme conditions. Alumina ceramic rollers are commonly used in machinery, electronics, and high-temperature processing equipment.
Alumina ceramic rollers are chosen for their ability to resist wear and reduce friction. They perform well in high-temperature environments and withstand exposure to corrosive chemicals. This makes them suitable for manufacturing processes involving heat, pressure, or aggressive substances.
Alumina ceramic rollers typically handle temperatures up to 1600°C (2912°F). Their thermal stability prevents cracking or degradation under extreme heat. This makes them reliable for applications like metal forming, glass production, or kiln operations.
The material’s high surface hardness minimizes wear from friction or abrasive materials. Alumina rollers maintain smooth operation over time, even with continuous use. They outlast metal or polymer rollers in harsh conditions, reducing replacement frequency and maintenance costs.
Alumina ceramic rollers can be customized in size, shape, and surface texture. Manufacturers adjust dimensions to fit specific machinery or production needs. Surface treatments like polishing or grooving improve performance for tasks like material handling or precision alignment. Custom designs ensure compatibility with unique industrial requirements.
(Alumina Precision Ceramic Part Alumina Ceramic Roller)
REQUEST A QUOTE
RELATED PRODUCTS
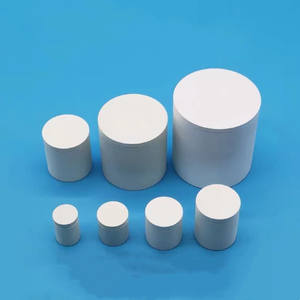
Excellent Performance Alumina Ceramic China Factory Customized Size Refractory
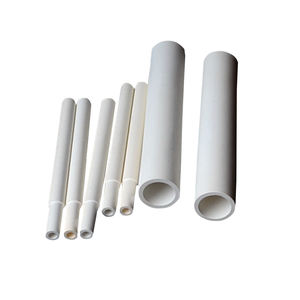
Advance Ceramic Large Size Aluminium Oxide Ceramic Plates and Discs Alumina Ceramic Round Plate
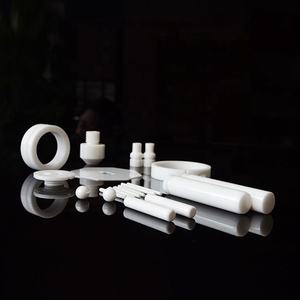
Custom 99% Al2O3 Alumina Ceramic High Temperature Resistant Parts
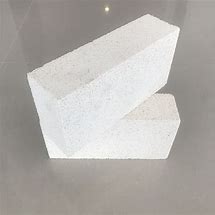
Al2O3 Ceramic Hot Selling Refractory Alumina Brick Kiln Rotary Kiln Building Making Clay Brick For Oven
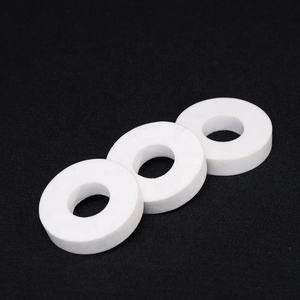
Steatite Ceramic Insulated Ceramic Structural Components Alumina Ceramic Assembly Parts
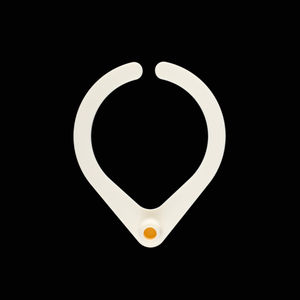