Discover Premium Ceramic Products | Durability & Elegance United | Advanced Ceramics
PRODUCT PARAMETERS
Description
Introduction to Alumina Ceramics
Alumina ceramics are known for their high hardness, wear resistance, corrosion resistance, good electrical insulation and high temperature stability. According to the different alumina content, it can be divided into different grades, such as 95 porcelain, 99 porcelain, etc., among which 99 porcelain refers to ceramic materials with an alumina content of 99%. As the alumina content increases, its mechanical strength and electrical insulation properties will also increase accordingly.
Characteristics of Alumina Ceramics
High Hardness: Alumina ceramics have extremely high hardness, which makes it very wear-resistant and suitable for manufacturing abrasive tools and parts that require wear resistance.
Wear resistance: Due to its high hardness, alumina ceramics show excellent wear resistance and are suitable for manufacturing parts for long-term use.
Corrosion resistance: Alumina ceramics have good resistance to most acids and alkalis, making them widely used in the chemical industry.
Good electrical insulation: As an excellent electrical insulating material, alumina ceramics are widely used in electronic and electrical products.
High temperature stability: Ability to withstand extremely high temperatures without significant physical or chemical changes, which makes it an ideal choice for applications in high temperature environments.
Biocompatibility: In the medical field, certain grades of alumina ceramics are used to make medical devices such as artificial joints due to their good biocompatibility.
(Tabular Alumina /high Alumina Refractory Steel Casting Ceramic Slab Corundum Sintered Slab Alumina)
Specifications of Tabular Alumina /high Alumina Refractory Steel Casting Ceramic Slab Corundum Sintered Slab Alumina
Tabular Alumina and high Alumina Refractory Steel Spreading Ceramic Slab are specialized products created for high-temperature industrial applications. These items provide remarkable performance in extreme conditions. Tabular Alumina is made from high-purity alumina resources. It undergoes regulated sintering to form a secure crystalline framework. This product reveals superb thermal security. It resists thermal shock and chemical rust. Its porosity is low. This ensures high mechanical stamina and toughness. It is generally made use of in steel casting, kiln linings, and refractory ceramics.
Diamond Sintered Slab consists of integrated alumina grains bonded at heats. The production procedure creates a thick, uniform structure. This piece has high wear resistance. It deals with rough environments well. Its alumina web content exceeds 99%. This makes it suitable for furnace cellular linings, burners, and steel processing devices. The piece keeps honesty under fast temperature adjustments.
High Alumina Refractory Steel Casting Ceramic Slab contains alumina degrees between 70% and 90%. It balances expense and performance. This material provides solid thermal insulation. It withstands molten steel infiltration. It is ideal for foundry applications. Steel mills utilize it for ladles, tundishes, and molds. The slab reduces warmth loss. This boosts energy efficiency in metal spreading processes.
Alumina Sintered Piece is generated by pushing and shooting alumina powder. It has a fine-grained appearance. This improves its load-bearing ability. The piece operates effectively in temperature levels as much as 1700 ° C. It resists oxidation and chemical erosion. Industries use it for heat treatment heating systems and activator cellular linings. Its dimensional stability makes sure lengthy service life.
Secret features throughout these items consist of high purity, thermal shock resistance, and mechanical stamina. They adjust to harsh industrial settings. Personalized shapes and sizes are offered. These materials fulfill strict quality criteria. They are checked for efficiency under real-world conditions. Proper installment makes certain optimal effectiveness. Individuals need to follow dealing with guidelines to avoid damage. These pieces lower downtime in high-temperature procedures. They are critical for industries requiring reliable refractory services.
(Tabular Alumina /high Alumina Refractory Steel Casting Ceramic Slab Corundum Sintered Slab Alumina)
Applications of Tabular Alumina /high Alumina Refractory Steel Casting Ceramic Slab Corundum Sintered Slab Alumina
Tabular alumina and high-alumina refractory products play vital duties in commercial applications. These products are made from high-purity alumina. They show exceptional warm resistance, toughness, and sturdiness. Steel casting relies on them for lining ladles, tundishes, and crucibles. Their ability to deal with extreme temperatures avoids liquified steel from destructive equipment. They additionally withstand rust brought on by slag and metal oxides. This prolongs the life-span of steelmaking devices.
In ceramic manufacturing, alumina slabs act as kiln furniture. They sustain ceramic items during shooting. Their low thermal growth maintains them stable under rapid temperature adjustments. This reduces cracks or bending in both the slabs and the products being terminated. Manufacturing facilities save expenses by reusing these pieces sometimes.
Chemical processing plants make use of sintered corundum pieces in activators and pipes. The product’s chemical inertness stops acids and antacids from degrading tools. High-alumina refractory cellular linings shield against abrasion in grinding systems. This is vital for handling harsh powders or granules.
Power generation systems like coal gasifiers depend on these materials. They line combustion chambers subjected to extreme heat and ash. Their thermal insulation enhances energy performance by retaining warmth. Foundries make use of alumina slabs in mold and mildews for casting metal components. The slabs stand up to metal penetration, making certain smooth surface areas on end products.
Glass manufacturing makes use of tabular alumina in melting containers. It withstands liquified glass deterioration without infecting the material. This maintains glass items clear and defect-free. Aerospace and auto sectors apply alumina-based ceramics in high-stress parts. Examples include generator elements and thermal barrier.
These materials adjust to diverse commercial needs. Their performance in extreme problems makes them irreplaceable. Industries prioritize them for reliability and cost-effectiveness.
Company Introduction
Advanced Ceramics founded on October 17, 2014, is a high-tech enterprise committed to the research and development, production, processing, sales and technical services of ceramic relative materials and products.. Since its establishment in 2014, the company has been committed to providing customers with the best products and services, and has become a leader in the industry through continuous technological innovation and strict quality management.
Our products includes but not limited to Silicon carbide ceramic products, Boron Carbide Ceramic Products, Boron Nitride Ceramic Products, Silicon Carbide Ceramic Products, Silicon Nitride Ceramic Products, Zirconium Dioxide Ceramic Products, Quartz Products, etc. Please feel free to contact us.(nanotrun@yahoo.com)
Payment Methods
T/T, Western Union, Paypal, Credit Card etc.
Shipment Methods
By air, by sea, by express, as customers request.
5 FAQs of Tabular Alumina /high Alumina Refractory Steel Casting Ceramic Slab Corundum Sintered Slab Alumina
What is tabular alumina? Tabular alumina is a high-purity sintered material made from calcined alumina. It undergoes high-temperature heating to form a dense, stable structure. The process creates strong, heat-resistant slabs ideal for extreme conditions. These slabs resist thermal shock, corrosion, and wear. They are common in steelmaking, furnaces, and kilns.
Why choose high alumina refractory materials for steel casting? High alumina materials handle intense heat better than regular refractories. They keep strength at temperatures above 1700°C. Steel casting involves molten metal, demanding materials that last under stress. High alumina slabs reduce cracks and erosion. This cuts downtime and repair costs in foundries.
Where are ceramic corundum slabs typically used? These slabs work in industries needing heat and chemical resistance. Examples include steel plants, glass factories, and cement kilns. They line furnaces, ladles, and reactors. Their hardness protects against abrasion from molten metals or slag. They also insulate equipment, improving energy efficiency.
How do sintered alumina slabs compare to other refractory materials? Sintered alumina slabs outperform fireclay or silica bricks in high-heat settings. They have higher alumina content, boosting thermal stability. They resist spalling better, maintaining structure through temperature swings. Their low porosity prevents chemical penetration. This makes them last longer in harsh environments.
What maintenance ensures long life for alumina refractory slabs? Proper installation avoids gaps or weak spots. Use compatible mortars and follow heating schedules to prevent cracks. Check slabs regularly for damage like chips or erosion. Replace worn sections early to avoid failures. Keep the operating environment stable—sudden temperature changes stress the material.
(Tabular Alumina /high Alumina Refractory Steel Casting Ceramic Slab Corundum Sintered Slab Alumina)
REQUEST A QUOTE
RELATED PRODUCTS
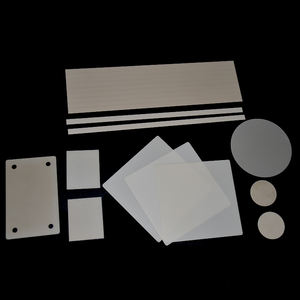
Alumina Ceramics High Frequency Porcelain Ceramic Head Talc Porcelain 99%Alumina Insulation Ceramics Tube Part
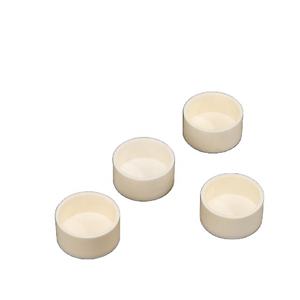
Corrosion Resistance Insulating Al2O3 Alumina Ceramic Plunger Shaft Ceramic Rod Zirconia Ceramic Pipe
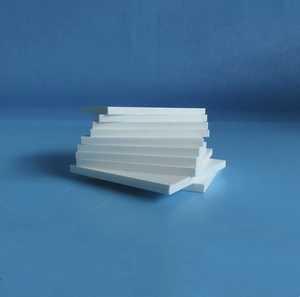
99% Alumina Electric Ceramics
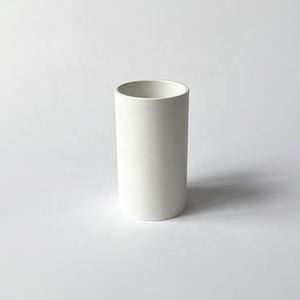
Alumina Precision Ceramic Part Alumina Ceramic Roller
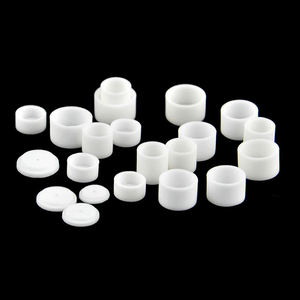
Steatite Ceramic Insulated Ceramic Structural Components Alumina Ceramic Assembly Parts
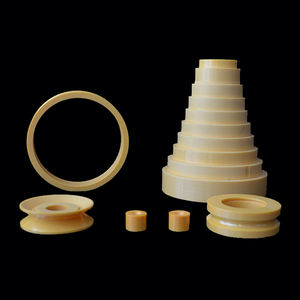