Discover Premium Ceramic Products | Durability & Elegance United | Advanced Ceramics
PRODUCT PARAMETERS
Description
Overview of aluminum nitride ceramics
Aluminum Nitride Ceramic is an advanced ceramic material with aluminum nitride as the main component. It has been widely used in electronics, optics, and mechanics due to its unique properties.
Features of aluminum nitride ceramics
High thermal conductivity: Aluminum nitride ceramics have relatively high thermal conductivity, usually between 170-260 W/m·K, which makes it an excellent heat dissipation material. It is especially suitable for electronic devices that require efficient heat dissipation, such as substrate materials for power semiconductor devices.
Good electrical insulation: Despite its high thermal conductivity, aluminum nitride ceramics are excellent insulators of electricity, which can effectively prevent current leakage and ensure the safe operation of electronic components.
Low dielectric constant and dielectric loss: These characteristics make aluminum nitride ceramics very suitable for use in high-frequency circuits because it can reduce energy loss during signal transmission.
High temperature resistance: Aluminum nitride ceramics can maintain structural stability and strength at extremely high temperatures. Its melting point is about 2800°C, so it is suitable for applications in high temperature environments.
Low thermal expansion coefficient: Compared with semiconductor materials such as silicon, aluminum nitride has a lower thermal expansion coefficient, which means it has better dimensional stability when the temperature changes, which helps improve packaging reliability.
Corrosion resistance: Aluminum nitride ceramics have good chemical stability to most molten metals and are not easily oxidized or corroded, allowing them to perform well in harsh environments.
High mechanical strength: Although not as hard as some other types of ceramic materials, aluminum nitride ceramics still provide enough mechanical strength to allow them to be used in many structural applications.
(Aluminum Nitride / Boron Nitride Composite BN-AlN Ceramic Parts for Ion Source)
Specifications of Aluminum Nitride / Boron Nitride Composite BN-AlN Ceramic Parts for Ion Source
Aluminum Nitride/Boron Nitride (BN-AlN) composite ceramic components are engineered for high-performance ion resource applications. These components combine aluminum nitride (AlN) and boron nitride (BN) to provide remarkable thermal, electric, and mechanical properties. The material structure equilibriums AlN’s high thermal conductivity with BN’s lubricity and thermal shock resistance. This makes BN-AlN compounds ideal for atmospheres needing reliable warmth dissipation and security under extreme problems.
The thermal conductivity of BN-AlN compounds varies in between 80-120 W/m · K. This makes certain rapid heat move far from critical ion source elements. The reduced thermal development coefficient (4.5-5.5 × 10 ⁻⁶/ K) decreases dimensional adjustments during temperature changes. Running temperatures can exceed 800 ° C without considerable degradation. Electrical insulation continues to be strong, with volume resistivity over 10 ¹⁴ Ω · centimeters. This stops existing leak in high-voltage ion source systems.
Mechanical stamina is a crucial function. Flexural toughness procedures 300-400 MPa, guaranteeing sturdiness under mechanical tension. The composite’s hardness (Hv 1200-1500) resists wear from ion bombardment and unpleasant bits. BN’s split framework gives self-lubricating buildings. This lowers rubbing in moving components within ion resources.
Chemical inertness is one more benefit. BN-AlN composites resist rust from reactive gases, molten steels, and plasma atmospheres. This extends component life expectancy in hostile operational setups. The product’s machinability allows accurate construction of intricate forms. Tight tolerances ( ± 0.1 mm) ensure compatibility with ion source assembly requirements.
Applications include ion thrusters, semiconductor handling tools, and particle accelerators. The compound’s capability to take care of high warmth, electric stress, and mechanical lots makes it dependable for accuracy systems. Customizable grades are readily available to satisfy details thermal or mechanical efficiency demands.
BN-AlN ceramic components are examined carefully for quality. Tests consist of thermal biking, electrical break down resistance, and mechanical tons simulations. Conformity with industry requirements makes certain consistency and dependability. These elements are packaged securely to avoid damages during shipping. Technical support is offered product choice and integration.
(Aluminum Nitride / Boron Nitride Composite BN-AlN Ceramic Parts for Ion Source)
Applications of Aluminum Nitride / Boron Nitride Composite BN-AlN Ceramic Parts for Ion Source
Light weight aluminum nitride (AlN) and boron nitride (BN) composite ceramic components combine the strengths of both materials. These BN-AlN porcelains deal with high warm well. They withstand chemical damages. They function reliably in challenging problems. These attributes make them excellent for ion sources. Ion sources require products that do under extreme warm and responsive environments. BN-AlN ceramics satisfy these needs.
Ion resources create billed bits for usages like semiconductor production, clinical study, and industrial procedures. BN-AlN parts below work as insulators or architectural parts. Their high thermal conductivity moves warmth away fast. This stops overheating in high-power systems. The low electrical conductivity of BN adds insulation. This stops energy loss. It maintains ion beam of lights stable.
BN-AlN ceramics take care of responsive gases and plasmas. Ion resources commonly use hostile chemicals. The compound’s chemical stability avoids disintegration. This extends component life. Upkeep prices drop. Downtime reduces.
The material’s mechanical stamina matters. Ion resources operate under vacuum cleaner or high pressure. BN-AlN ceramics remain strong under stress. They withstand cracks. Performance remains consistent gradually.
These porcelains additionally device specifically. Complicated forms fit limited style specs. This is vital for ion source components needing precise alignment. Custom parts adapt to various systems.
BN-AlN works in mass spectrometers, fragment accelerators, and thin-film finishing tools. In mass spectrometers, the product’s pureness avoids contamination. This makes sure accurate analysis. In accelerators, thermal management keeps light beams focused. Thin-film tools depend on stable plasmas. BN-AlN aids attain this.
The mix of AlN and BN develops an equilibrium. It combines thermal efficiency, electrical insulation, and longevity. Industries needing reliable ion sources benefit. The ceramics boost effectiveness and cut costs. They handle challenges various other materials can not.
Company Introduction
Advanced Ceramics founded on October 17, 2014, is a high-tech enterprise committed to the research and development, production, processing, sales and technical services of ceramic relative materials and products.. Since its establishment in 2014, the company has been committed to providing customers with the best products and services, and has become a leader in the industry through continuous technological innovation and strict quality management.
Our products includes but not limited to Silicon carbide ceramic products, Boron Carbide Ceramic Products, Boron Nitride Ceramic Products, Silicon Carbide Ceramic Products, Silicon Nitride Ceramic Products, Zirconium Dioxide Ceramic Products, Quartz Products, etc. Please feel free to contact us.(nanotrun@yahoo.com)
Payment Methods
T/T, Western Union, Paypal, Credit Card etc.
Shipment Methods
By air, by sea, by express, as customers request.
5 FAQs of Aluminum Nitride / Boron Nitride Composite BN-AlN Ceramic Parts for Ion Source
What are BN-AlN ceramic parts used for in ion sources? These parts handle heat, prevent electrical currents, and protect against plasma damage. Ion sources create charged particles for machines like mass spectrometers. BN-AlN parts keep systems stable under extreme heat and electrical stress. They last longer than metals or regular ceramics in these conditions.
Why pick BN-AlN composites over other materials? The mix of boron nitride and aluminum nitride gives high heat transfer and stops electricity from flowing. Metals move heat well but conduct electricity, causing shorts. Regular ceramics block electricity but crack under rapid temperature changes. BN-AlN solves both problems.
How do BN-AlN parts survive high temperatures? The materials resist breaking down even at extreme heat levels. Their structure stays stable during heating or cooling cycles. This reduces cracks or warping, which happen with other ceramics.
Do BN-AlN parts resist chemical damage? Yes. They work well in plasma environments with reactive gases. Boron nitride in the composite blocks corrosion from aggressive chemicals. This keeps parts working longer without degrading.
Are BN-AlN parts strong enough for heavy use? They handle physical stress better than many ceramics. The composite structure spreads pressure evenly, reducing cracks from impacts or vibrations. This makes them reliable in high-wear applications like ion sources.
(Aluminum Nitride / Boron Nitride Composite BN-AlN Ceramic Parts for Ion Source)
REQUEST A QUOTE
RELATED PRODUCTS
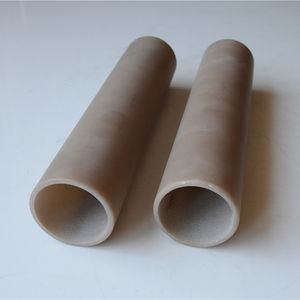
Custom Aluminum Nitride AlN Insulating Ceramic Ring
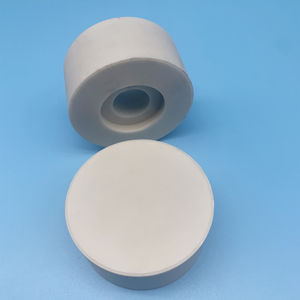
High Heat Conductivity AlN Aluminum Nitride Ceramic Sheet
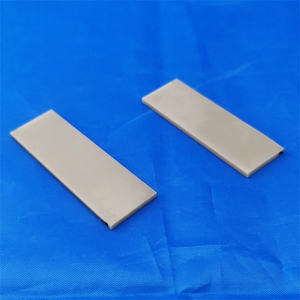
SINTYRON Semiconductor Ceramic Single Crystal 170 180w High Thermal Conductivity Aln Aluminum Nitride Ceramic Substrate
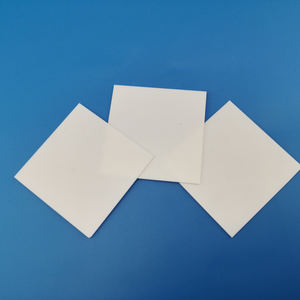
0.635mm Thickness Aluminum Nitride Ceramic Plate AlN Ceramic PCB Substrate Sheet
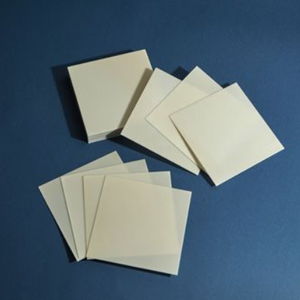
Custom Shape Aln Aluminium Nitride Ceramic Sheet Plate Substrates
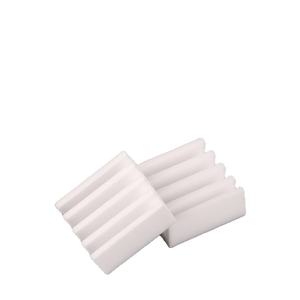