Discover Premium Ceramic Products | Durability & Elegance United | Advanced Ceramics
PRODUCT PARAMETERS
Description
Overview of Silicon Carbide Ceramics
Silicon Carbide (SiC) ceramics are renowned for their outstanding mechanical properties, including high hardness, strength at elevated temperatures, and excellent thermal shock resistance. These materials are pivotal in cutting-edge industrial applications, from abrasives to aerospace components, due to their unique combination of properties.
Features of Silicon Carbide Ceramics
High Hardness: Exceptional wear resistance.
Thermal Shock Resistance: Can withstand rapid temperature changes.
Chemical Stability: Resistant to most chemicals.
High Thermal Conductivity: Efficient heat dissipation.
Low Density: Lightweight for its strength.
(Aluminum Oxide Ceramic Silicon Carbide Ceramic for Plate)
Specification of Aluminum Oxide Ceramic Silicon Carbide Ceramic for Plate
Aluminum oxide ceramic and silicon carbide ceramic plates offer high performance in industrial applications. Aluminum oxide ceramic (Al2O3) provides excellent hardness and thermal stability. It withstands temperatures up to 1600°C. Its mechanical strength remains consistent under stress. This material resists wear and corrosion effectively. It is suitable for components exposed to harsh environments. Silicon carbide ceramic (SiC) delivers superior thermal conductivity. It handles extreme temperatures up to 1650°C. Its low thermal expansion reduces cracking risks during rapid temperature changes. This material excels in high-load conditions. Both materials are chemically inert. They resist acids, alkalis, and molten metals. This ensures durability in aggressive chemical settings. Aluminum oxide ceramic has a density of approximately 3.9 g/cm³. Silicon carbide ceramic is lighter at around 3.1 g/cm³. The lower weight of SiC benefits applications requiring reduced mass. Aluminum oxide ceramic acts as an electrical insulator. It is ideal for electronic and electrical systems. Silicon carbide ceramic is semi-conductive. It is used in applications needing controlled electrical conductivity. Both ceramics are machinable to precise dimensions. They can be shaped into plates, discs, or custom geometries. Surface finishes are adjustable for specific friction or wear requirements. Aluminum oxide ceramic plates are common in machinery components. Examples include seals, bearings, and cutting tools. Silicon carbide ceramic plates are preferred in high-abrasion settings. Examples include pump parts, nozzles, and furnace linings. The manufacturing process for aluminum oxide involves sintering at high temperatures. This creates a dense, uniform structure. Silicon carbide is produced through reaction bonding or sintering. This results in a tough, fine-grained material. Custom thicknesses and sizes are available. Standard plate thicknesses range from 1 mm to 50 mm. Sizes vary based on application needs. Both materials are compatible with metal or polymer substrates. Adhesive or mechanical fastening methods secure them in place. Cost varies by material grade and complexity. Aluminum oxide is generally more cost-effective for standard applications. Silicon carbide offers higher performance for demanding conditions. Proper handling avoids chipping or cracking during installation. These ceramics require minimal maintenance. They maintain performance over long service periods.
(Aluminum Oxide Ceramic Silicon Carbide Ceramic for Plate)
Applications of Aluminum Oxide Ceramic Silicon Carbide Ceramic for Plate
Aluminum oxide ceramic and silicon carbide ceramic plates serve many industries. They are hard. They handle high temperatures. They resist wear and corrosion. These traits make them ideal for demanding environments.
In industrial settings, these plates protect machinery. Grinding mills and crushers use them as liners. Abrasive materials cause less damage. Equipment lasts longer. Maintenance costs drop. Factories save money over time.
Electronics manufacturing relies on these plates. They form part of semiconductor production equipment. High-temperature processes need stable materials. The plates ensure consistent results. They prevent contamination. This boosts product quality.
Aerospace applications benefit from these ceramics. Engine components and heat shields use them. Extreme heat occurs during flight. The plates manage thermal stress. They keep systems safe. Performance stays reliable.
Defense sectors use the plates for armor. Bulletproof vests and vehicle armor incorporate them. They stop projectiles effectively. Traditional metal armor is heavier. Ceramic plates offer protection without extra weight. Soldiers move more freely.
Cutting tools use these ceramics. Blades stay sharp longer. They cut through tough materials easily. Wear resistance reduces replacement frequency. Users save on tool costs.
Medical devices use the plates. Surgical tools and implants need biocompatibility. These ceramics meet safety standards. They resist body fluids. Patients face fewer risks.
Chemical plants use the plates in pumps and valves. Harsh chemicals cause corrosion. The ceramics endure aggressive substances. Leaks become less likely. Operations stay efficient.
Mining equipment uses ceramic plates. Drills and conveyors face constant abrasion. The plates extend component life. Downtime decreases. Productivity improves.
These ceramics work in energy sectors. Solar panels and nuclear reactors use them. High heat and radiation exist. The plates maintain integrity. Energy systems run smoothly.
Aluminum oxide and silicon carbide ceramic plates solve many challenges. Industries trust their durability. They adapt to extreme conditions. Performance stays consistent. Costs stay manageable.
Company Introduction
Advanced Ceramics founded on October 17, 2014, is a high-tech enterprise committed to the research and development, production, processing, sales and technical services of ceramic relative materials and products.. Since its establishment in 2014, the company has been committed to providing customers with the best products and services, and has become a leader in the industry through continuous technological innovation and strict quality management.
Our products includes but not limited to Silicon carbide ceramic products, Boron Carbide Ceramic Products, Boron Nitride Ceramic Products, Silicon Carbide Ceramic Products, Silicon Nitride Ceramic Products, Zirconium Dioxide Ceramic Products, Quartz Products, etc. Please feel free to contact us.(nanotrun@yahoo.com)
Payment Methods
T/T, Western Union, Paypal, Credit Card etc.
Shipment Methods
By air, by sea, by express, as customers request.
5 FAQs of Aluminum Oxide Ceramic Silicon Carbide Ceramic for Plate
What is aluminum oxide ceramic silicon carbide ceramic plate. It combines aluminum oxide and silicon carbide. These materials are heat-resistant and durable. The plate handles extreme temperatures and resists wear. It works in industrial settings needing tough components.
What are key properties of this ceramic plate. It has high hardness and thermal stability. It resists corrosion and chemical damage. The plate conducts heat well. It stays strong under mechanical stress. These traits make it last longer in harsh environments.
Where is this ceramic plate commonly used. Factories use it in machinery parts like seals and bearings. Electronics use it for insulating components. It serves in high-temperature furnaces and cutting tools. Automotive industries apply it for engine parts. Its durability fits heavy-duty applications.
How does this ceramic compare to other ceramics. It handles higher temperatures than alumina ceramics. It is harder than zirconia ceramics. Silicon carbide adds extra thermal conductivity. It outperforms many metals in wear resistance. It costs more but lasts longer in tough conditions.
How to maintain and clean this ceramic plate. Avoid sudden temperature changes to prevent cracks. Use mild detergents and soft cloths for cleaning. Do not expose to strong acids or alkalis. Check for surface damage regularly. Proper care keeps performance stable over time.
(Aluminum Oxide Ceramic Silicon Carbide Ceramic for Plate)
REQUEST A QUOTE
RELATED PRODUCTS

Customized Heat Resistance Silicon Carbide SIC Ceramic Plate Board Special Shape Part
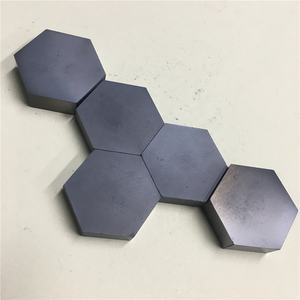
Non-pressure Silicon Carbide Ceramics
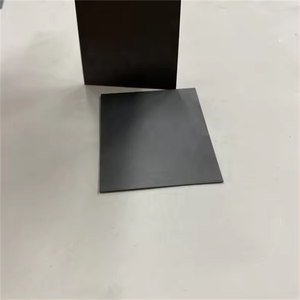
Silicon Carbide SiC Porous Ceramic Plate Pore Size 50μm
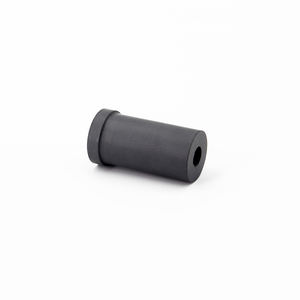
Tactical Vest Alumina Plate Silicon Carbide Plate PE Ceramic Plate 10×12 Strike Face Rectangular Cut
Silicon Carbide Ceramic Plate Protective Appliance High Hardness Customized
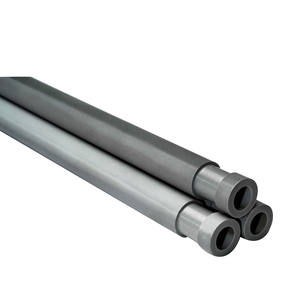