Discover Premium Ceramic Products | Durability & Elegance United | Advanced Ceramics
PRODUCT PARAMETERS
Description
Introduction to Alumina Ceramics
Alumina ceramics are known for their high hardness, wear resistance, corrosion resistance, good electrical insulation and high temperature stability. According to the different alumina content, it can be divided into different grades, such as 95 porcelain, 99 porcelain, etc., among which 99 porcelain refers to ceramic materials with an alumina content of 99%. As the alumina content increases, its mechanical strength and electrical insulation properties will also increase accordingly.
Characteristics of Alumina Ceramics
High Hardness: Alumina ceramics have extremely high hardness, which makes it very wear-resistant and suitable for manufacturing abrasive tools and parts that require wear resistance.
Wear resistance: Due to its high hardness, alumina ceramics show excellent wear resistance and are suitable for manufacturing parts for long-term use.
Corrosion resistance: Alumina ceramics have good resistance to most acids and alkalis, making them widely used in the chemical industry.
Good electrical insulation: As an excellent electrical insulating material, alumina ceramics are widely used in electronic and electrical products.
High temperature stability: Ability to withstand extremely high temperatures without significant physical or chemical changes, which makes it an ideal choice for applications in high temperature environments.
Biocompatibility: In the medical field, certain grades of alumina ceramics are used to make medical devices such as artificial joints due to their good biocompatibility.
(Factory Al2O3 Alumina Oxide Powder Calcined Alumina for Ceramics)
Specifications of Factory Al2O3 Alumina Oxide Powder Calcined Alumina for Ceramics
Factory Al2O3 Alumina Oxide Powder Calcined Alumina is a high-purity material designed for ceramic applications. The powder has an aluminum oxide (Al2O3) content of 99.5% or higher. This ensures reliable performance in industrial and technical ceramics. The product is produced through a high-temperature calcination process. This process improves its thermal stability and mechanical strength. The average particle size ranges between 1-5 microns. Fine particle distribution allows uniform mixing in ceramic formulations. This results in consistent density and structure in finished products.
The powder features a high surface area. This enhances reactivity during sintering. It promotes better bonding between particles in ceramic matrices. The material has a melting point above 2000°C. This makes it suitable for high-temperature applications like refractory linings or kiln furniture. Its low alkali metal content minimizes unwanted reactions during firing. This helps maintain ceramic integrity.
Factory Al2O3 Alumina Oxide Powder is chemically inert. It resists corrosion from acids and alkalis. This property extends the lifespan of ceramic components in harsh environments. The powder’s high hardness improves wear resistance in finished products. It is ideal for cutting tools, abrasives, and structural ceramics.
The product is available in multiple grades. Particle size and purity can be customized based on customer needs. It is compatible with various shaping methods. These include dry pressing, extrusion, and slip casting. The powder’s low moisture absorption ensures stable processing conditions. This reduces defects during production.
Packaging options include 25 kg bags or bulk containers. Storage recommendations emphasize keeping the material dry and away from contaminants. Proper handling prevents clumping and preserves flowability.
Factory Al2O3 Alumina Oxide Powder meets international quality standards. It undergoes strict testing for particle size, purity, and chemical composition. This guarantees consistency across batches. Manufacturers rely on it for high-performance ceramics in electronics, aerospace, and industrial sectors.
(Factory Al2O3 Alumina Oxide Powder Calcined Alumina for Ceramics)
Applications of Factory Al2O3 Alumina Oxide Powder Calcined Alumina for Ceramics
Factory Al2O3 Alumina Oxide Powder Calcined Alumina is a key material in ceramic production. It is made by heating alumina at high temperatures. This process improves its strength and heat resistance. Ceramic manufacturers rely on it to boost product quality.
The powder is widely used in structural ceramics. It strengthens tiles, sanitaryware, and tableware. Adding it to ceramic mixes increases durability. This makes finished products resistant to cracks and wear. High-purity alumina ensures consistent performance in demanding environments.
Technical ceramics benefit greatly from calcined alumina. It is essential for making electrical insulators and cutting tools. These parts need high thermal stability. The powder provides it. It also improves hardness in industrial components. This extends their lifespan under heavy use.
In ceramic glazes and coatings, alumina acts as a stabilizer. It prevents uneven melting during firing. The result is smooth, glossy surfaces. It also controls glaze viscosity. This helps achieve precise application on complex shapes.
Refractory ceramics use alumina for high-temperature applications. Linings for kilns and furnaces depend on it. The powder withstands extreme heat without breaking down. This maintains structural integrity in industrial heating systems.
Advanced ceramics like bioceramics and aerospace parts use alumina. It is biocompatible for medical implants. Its lightweight nature suits aerospace needs. The powder ensures reliability in critical applications.
Calcined alumina serves as a cost-effective filler. It reduces production costs without sacrificing quality. Fine particle size allows even distribution in ceramic mixes. This avoids weak spots in final products.
The powder supports eco-friendly manufacturing. It requires less energy during processing. Waste is minimized due to high efficiency. Factories reduce their environmental impact by using it.
Custom grain sizes and purity levels are available. This lets manufacturers tailor the powder to specific needs. Quality control ensures each batch meets industry standards.
Factory Al2O3 Alumina Oxide Powder remains vital across ceramic sectors. It addresses performance challenges. It drives innovation in product design. Its versatility makes it a preferred choice for modern ceramic engineering.
Company Introduction
Advanced Ceramics founded on October 17, 2014, is a high-tech enterprise committed to the research and development, production, processing, sales and technical services of ceramic relative materials and products.. Since its establishment in 2014, the company has been committed to providing customers with the best products and services, and has become a leader in the industry through continuous technological innovation and strict quality management.
Our products includes but not limited to Silicon carbide ceramic products, Boron Carbide Ceramic Products, Boron Nitride Ceramic Products, Silicon Carbide Ceramic Products, Silicon Nitride Ceramic Products, Zirconium Dioxide Ceramic Products, Quartz Products, etc. Please feel free to contact us.(nanotrun@yahoo.com)
Payment Methods
T/T, Western Union, Paypal, Credit Card etc.
Shipment Methods
By air, by sea, by express, as customers request.
5 FAQs of Factory Al2O3 Alumina Oxide Powder Calcined Alumina for Ceramics
What is calcined alumina powder? Calcined alumina powder is a type of aluminum oxide treated at high temperatures. This process removes impurities and increases stability. It is commonly used in ceramics due to its hardness and heat resistance. The powder is white and fine-grained, making it easy to mix into ceramic materials.
Why use calcined alumina in ceramics? Calcined alumina improves ceramic strength and durability. It resists high temperatures without cracking or breaking. This makes ceramics suitable for industrial applications like kiln linings or electrical insulators. The powder also enhances surface finish, giving ceramics a smooth, polished look.
What temperature can calcined alumina withstand? Calcined alumina handles temperatures up to 1800°C. This makes it ideal for high-heat environments. Ceramics made with this powder maintain structure under extreme conditions. It prevents warping or melting during firing processes.
How does particle size affect performance? Smaller particles create denser ceramics with fewer gaps. This improves mechanical strength and wear resistance. Larger particles may reduce shrinkage during drying. Manufacturers choose sizes based on the desired ceramic properties.
Is calcined alumina safe to handle? The powder is non-toxic but requires careful handling. Inhalation can irritate lungs. Wear masks and gloves when working with it. Store in dry areas to prevent clumping. Follow safety guidelines to avoid accidents.
(Factory Al2O3 Alumina Oxide Powder Calcined Alumina for Ceramics)
REQUEST A QUOTE
RELATED PRODUCTS
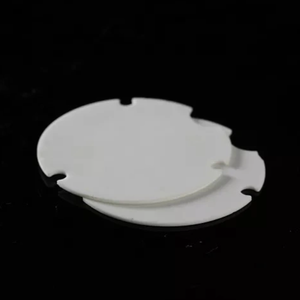
Fine Ceramic 99% Alumina Ceramic Tube
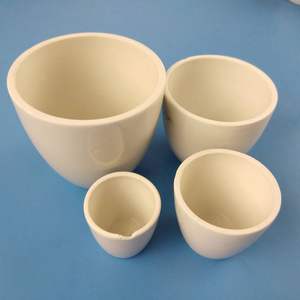
Black 99% Alumina Ceramic Honeycomb Ceramic for Electric Appliance

96% Metallization Tube Alumina Ceramics Parts Al2o3 Alumina Ceramic
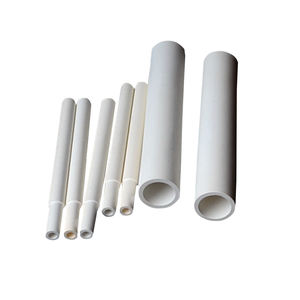
Advance Ceramic Large Size Aluminium Oxide Ceramic Plates and Discs Alumina Ceramic Round Plate
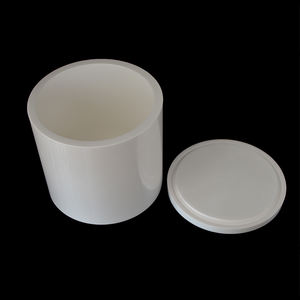
High Purity Ceramic Box Alumina Ceramic Sagger
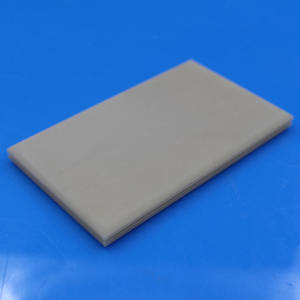