Discover Premium Ceramic Products | Durability & Elegance United | Advanced Ceramics
PRODUCT PARAMETERS
Description
Overview of aluminum nitride ceramics
Aluminum Nitride Ceramic is an advanced ceramic material with aluminum nitride as the main component. It has been widely used in electronics, optics, and mechanics due to its unique properties.
Features of aluminum nitride ceramics
High thermal conductivity: Aluminum nitride ceramics have relatively high thermal conductivity, usually between 170-260 W/m·K, which makes it an excellent heat dissipation material. It is especially suitable for electronic devices that require efficient heat dissipation, such as substrate materials for power semiconductor devices.
Good electrical insulation: Despite its high thermal conductivity, aluminum nitride ceramics are excellent insulators of electricity, which can effectively prevent current leakage and ensure the safe operation of electronic components.
Low dielectric constant and dielectric loss: These characteristics make aluminum nitride ceramics very suitable for use in high-frequency circuits because it can reduce energy loss during signal transmission.
High temperature resistance: Aluminum nitride ceramics can maintain structural stability and strength at extremely high temperatures. Its melting point is about 2800°C, so it is suitable for applications in high temperature environments.
Low thermal expansion coefficient: Compared with semiconductor materials such as silicon, aluminum nitride has a lower thermal expansion coefficient, which means it has better dimensional stability when the temperature changes, which helps improve packaging reliability.
Corrosion resistance: Aluminum nitride ceramics have good chemical stability to most molten metals and are not easily oxidized or corroded, allowing them to perform well in harsh environments.
High mechanical strength: Although not as hard as some other types of ceramic materials, aluminum nitride ceramics still provide enough mechanical strength to allow them to be used in many structural applications.
(High thermal conductivity thick film aln aluminum nitride ceramic pcb and alumina pcb substrate)
Specifications of High thermal conductivity thick film aln aluminum nitride ceramic pcb and alumina pcb substrate
High thermal conductivity thick film aluminum nitride (AlN) ceramic PCBs and alumina (Al2O3) PCB substrates serve critical roles in advanced electronics. These materials excel in demanding applications due to their unique properties. Aluminum nitride ceramic PCBs offer exceptional thermal conductivity, typically ranging from 170 to 200 W/mK. This allows efficient heat dissipation in high-power devices. Alumina substrates provide lower thermal conductivity, around 24-30 W/mK. They remain popular for cost-sensitive applications requiring moderate thermal management.
AlN ceramic PCBs feature low thermal expansion coefficients, closely matching silicon chips. This reduces mechanical stress during temperature fluctuations. Alumina substrates have higher thermal expansion coefficients. They still perform reliably in environments with stable thermal conditions. Both materials maintain strong electrical insulation, preventing current leakage. Aluminum nitride stands out in high-frequency applications due to its low dielectric loss. Alumina substrates are widely used in standard circuits for their balance of performance and affordability.
Thick film technology enhances these substrates. It enables precise printing of conductive, resistive, or insulating layers. Aluminum nitride supports fine-line circuitry, ideal for miniaturized electronics. Alumina substrates accommodate thicker traces, suitable for robust industrial equipment. Surface finishes like gold, silver, or copper improve solderability and corrosion resistance. Aluminum nitride’s non-reactive surface ensures stability in harsh chemical environments. Alumina resists wear and oxidation, extending component lifespan.
Mechanical strength differs between materials. Alumina substrates exhibit higher flexural strength, reducing breakage risks during handling. Aluminum nitride is more brittle but compensates with superior thermal performance. Both materials operate effectively across wide temperature ranges. AlN withstands extreme heat up to 850°C. Alumina handles temperatures up to 1600°C, fitting high-temperature sintering processes.
Applications vary by material. Aluminum nitride PCBs dominate high-power LED systems, RF modules, and automotive power electronics. Alumina substrates appear in consumer electronics, sensor systems, and heating elements. Selecting between them depends on thermal needs, budget, and operational conditions. Aluminum nitride suits cutting-edge applications prioritizing heat dissipation. Alumina remains a practical choice for standard thermal management.
(High thermal conductivity thick film aln aluminum nitride ceramic pcb and alumina pcb substrate)
Applications of High thermal conductivity thick film aln aluminum nitride ceramic pcb and alumina pcb substrate
High thermal conductivity thick film aluminum nitride (AlN) ceramic PCBs and alumina PCB substrates serve critical roles in advanced electronics. These materials manage heat effectively in high-power applications. AlN ceramic PCBs have excellent thermal conductivity, around 170-200 W/mK. This makes them ideal for devices needing rapid heat dissipation. Alumina PCB substrates offer lower thermal conductivity, about 20-30 W/mK, but remain cost-effective for many standard uses.
LED lighting systems benefit from both materials. High-power LEDs generate significant heat. AlN ceramic PCBs transfer heat away quickly, preventing overheating. Alumina substrates handle lower-power LED setups efficiently. Power electronics rely on these substrates too. Devices like inverters and motor controllers use AlN PCBs to maintain stable performance under high temperatures. Alumina substrates support less demanding circuits while keeping costs low.
Automotive electronics use AlN and alumina PCBs for reliability. Electric vehicles require components that endure high heat in compact spaces. AlN substrates manage heat in battery management systems and power modules. Alumina substrates support sensors and control units. Aerospace applications demand materials resistant to extreme conditions. AlN’s thermal stability ensures performance in satellites and avionics. Alumina substrates are used in communication systems for their electrical insulation.
RF and microwave devices use alumina substrates for signal integrity. The material’s low electrical loss suits high-frequency circuits. AlN substrates are chosen for high-power RF applications needing heat management. Medical equipment requires precision and durability. AlN PCBs are used in imaging systems and laser diodes where temperature control is vital. Alumina substrates appear in diagnostic tools and monitoring devices for reliable operation.
Industrial equipment uses both materials for power handling. AlN substrates cool high-performance semiconductor modules. Alumina supports control systems and sensors in harsh environments. These substrates ensure devices operate safely under thermal stress. Their versatility makes them essential across industries prioritizing heat management and electrical performance.
Company Introduction
Advanced Ceramics founded on October 17, 2014, is a high-tech enterprise committed to the research and development, production, processing, sales and technical services of ceramic relative materials and products.. Since its establishment in 2014, the company has been committed to providing customers with the best products and services, and has become a leader in the industry through continuous technological innovation and strict quality management.
Our products includes but not limited to Silicon carbide ceramic products, Boron Carbide Ceramic Products, Boron Nitride Ceramic Products, Silicon Carbide Ceramic Products, Silicon Nitride Ceramic Products, Zirconium Dioxide Ceramic Products, Quartz Products, etc. Please feel free to contact us.(nanotrun@yahoo.com)
Payment Methods
T/T, Western Union, Paypal, Credit Card etc.
Shipment Methods
By air, by sea, by express, as customers request.
5 FAQs of High thermal conductivity thick film aln aluminum nitride ceramic pcb and alumina pcb substrate
High thermal conductivity thick film AlN aluminum nitride ceramic PCB and alumina PCB substrate are used in electronics needing efficient heat management. Here are 5 FAQs about these products.
What makes AlN ceramic PCB better than alumina for thermal management? AlN has higher thermal conductivity, around 170-200 W/mK. Alumina’s thermal conductivity is lower, about 18-30 W/mK. AlN spreads heat faster, reducing hot spots. This suits high-power devices like LED modules or power converters.
Where are these substrates commonly used? AlN PCBs work in high-power electronics, laser diodes, and aerospace systems. Alumina PCBs are cheaper, used in consumer electronics, automotive sensors, and basic circuits. Both handle high temperatures, but AlN fits extreme environments better.
Why is AlN more expensive than alumina? AlN materials cost more. The production process is complex. Raw aluminum nitride is harder to process than alumina. High-performance applications justify the price. Alumina remains popular for budget-friendly projects.
How reliable are these substrates in harsh conditions? Both resist corrosion and high temperatures. AlN performs better under rapid thermal cycling. It handles temperature swings without cracking. Alumina is stable but may degrade faster under stress. Proper design ensures long-term reliability for both.
Can these PCBs be customized for specific needs? Yes. Thickness, layer count, and metal coatings are adjustable. AlN supports finer circuits due to smoother surfaces. Alumina allows thicker traces for high-current uses. Manufacturers tailor dimensions and finishes to match device requirements.
These substrates address different needs. AlN excels in high-end thermal management. Alumina offers cost efficiency for standard applications. Choosing depends on thermal needs, budget, and operating conditions.
(High thermal conductivity thick film aln aluminum nitride ceramic pcb and alumina pcb substrate)
REQUEST A QUOTE
RELATED PRODUCTS
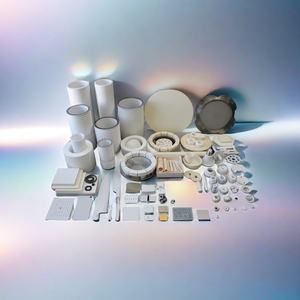
Spherical AlN Ceramic Microsphere Aluminum Nitride Powder AlN Granules
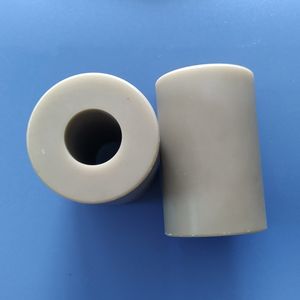
CNC Machined ALN Aluminum Nitride Ceramic Disc
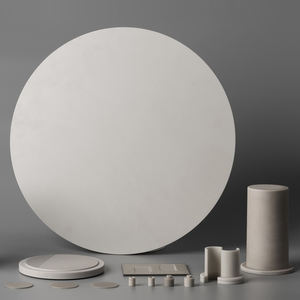
High Thermal Conductivity Aluminum Nitride AlN Ceramic Discs
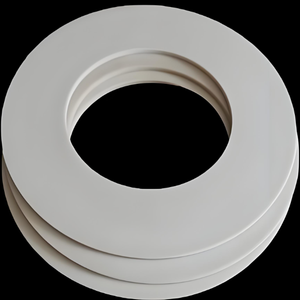
High Purity 99.95% Aluminum Nitride AlN Spherical Powder 3-5um Ceramic Microspheres Durable Heat Conductive Material
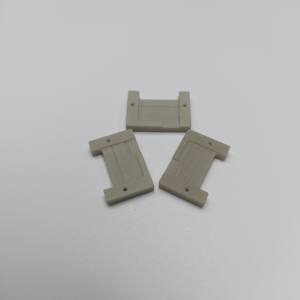
High Thermal Conductivity / Aluminum Nitride / AlN Ceramic Substrate/ Plate / Block
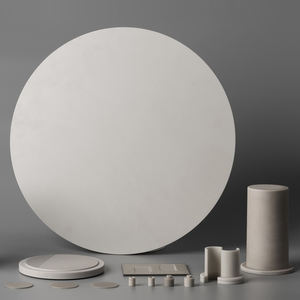