Discover Premium Ceramic Products | Durability & Elegance United | Advanced Ceramics
PRODUCT PARAMETERS
Description
Introduction to Alumina Ceramics
Alumina ceramics are known for their high hardness, wear resistance, corrosion resistance, good electrical insulation and high temperature stability. According to the different alumina content, it can be divided into different grades, such as 95 porcelain, 99 porcelain, etc., among which 99 porcelain refers to ceramic materials with an alumina content of 99%. As the alumina content increases, its mechanical strength and electrical insulation properties will also increase accordingly.
Characteristics of Alumina Ceramics
High Hardness: Alumina ceramics have extremely high hardness, which makes it very wear-resistant and suitable for manufacturing abrasive tools and parts that require wear resistance.
Wear resistance: Due to its high hardness, alumina ceramics show excellent wear resistance and are suitable for manufacturing parts for long-term use.
Corrosion resistance: Alumina ceramics have good resistance to most acids and alkalis, making them widely used in the chemical industry.
Good electrical insulation: As an excellent electrical insulating material, alumina ceramics are widely used in electronic and electrical products.
High temperature stability: Ability to withstand extremely high temperatures without significant physical or chemical changes, which makes it an ideal choice for applications in high temperature environments.
Biocompatibility: In the medical field, certain grades of alumina ceramics are used to make medical devices such as artificial joints due to their good biocompatibility.
( Customized High Temperature Resistance Glazed 95% 99% Al2O3 Insulator Alumina Ceramic Components Parts)
Specifications of Customized High Temperature Resistance Glazed 95% 99% Al2O3 Insulator Alumina Ceramic Components Parts
Personalized High Temperature Resistance Glazed 95% 99% Al2O3 Insulator Alumina Porcelain Parts are crafted for extreme atmospheres. These parts use high-purity alumina oxide (Al2O3) as the base material. 2 grades are offered: 95% and 99% Al2O3. The 99% grade offers higher thickness and much better efficiency under anxiety. Both qualities endure temperatures up to 1700 ° C. They keep structural security in constant high-heat applications.
The material supplies outstanding mechanical stamina. It resists wear, deterioration, and influence. These residential properties make the components long lasting in severe commercial setups. The glaze coating includes a smooth surface area finish. This minimizes friction and avoids contamination. The polish likewise boosts electrical insulation. Voltage resistance reaches 15 kV/mm. This makes certain risk-free usage in high-voltage systems.
Customization is a vital attribute. Components are made in various sizes and shapes. Common types consist of tubes, rods, plates, and complex geometries. Accuracy machining guarantees limited tolerances. Dimensional precision meets ± 0.5% of specified dimensions. Surface treatments or holes can be added per request.
Chemical resistance is strong. The parts deal with acids, antacid, and molten metals. They are excellent for chemical handling devices. Thermal shock resistance is superior. Rapid temperature level modifications cause very little damages. This dependability fits applications like heater cellular linings and semiconductor production.
Electrical insulation remains stable across temperature levels. Leak currents remain reduced also at high warmth. This matches electronic devices, power transmission, and aerospace elements. The product’s reduced thermal expansion protects against cracking under thermal biking.
These alumina ceramic parts are utilized in several industries. Examples consist of metallurgy, energy, vehicle, and electronic devices. They work as insulators, substratums, sensors, and safety elements. Custom-made creates match details machinery or systems.
The production process utilizes advanced sintering methods. This makes certain consistent high quality and performance. Each batch undertakes strict testing. Tests include thickness checks, hardness dimensions, and thermal security assessments. Compliance with international criteria is guaranteed.
Lengthy life span reduces replacement prices. Very little upkeep is required. Performance remains secure with time. These parts are a cost-efficient service for high-demand applications.
( Customized High Temperature Resistance Glazed 95% 99% Al2O3 Insulator Alumina Ceramic Components Parts)
Applications of Customized High Temperature Resistance Glazed 95% 99% Al2O3 Insulator Alumina Ceramic Components Parts
Customized high-temperature resistance glazed 95% and 99% Al2O3 insulator alumina ceramic components are essential in sectors needing toughness and performance under extreme problems. These components handle high temperatures, withstand wear, and offer electric insulation. The polished surface boosts smoothness, decreases contamination risks, and improves resistance to chemicals.
These alumina ceramic components are commonly used in electronic devices. They work as substratums and insulators in circuits and sensors. High purity (95% or 99% Al2O3) guarantees secure efficiency in high-voltage settings. The product’s thermal stability prevents contortion during rapid temperature level changes.
Industrial heating systems rely upon these components. They function as heating system cellular linings, thermocouple tubes, and heat exchangers. The high-temperature resistance enables constant procedure over 1600 ° C. The polished layer decreases friction, prolonging life span in rough settings.
Aerospace and automobile industries use these porcelains for engine elements and sensing units. They withstand combustion warmth and reduce component failure. The light-weight nature of alumina helps improve gas performance without compromising toughness.
Power manufacturing take advantage of these parts. They are used in insulation systems for power plants and renewable energy equipment. The electric insulation residential or commercial properties stop energy loss. Rust resistance ensures reliability in extreme settings like atomic power plants or solar thermal systems.
Chemical processing tools includes alumina ceramic components for pumps, shutoffs, and seals. The polished surface stands up to acid and alkali rust. This reduces downtime for maintenance and substitute.
Clinical devices make use of these components for high-precision devices. Sterility and heat resistance are crucial in autoclaves and surgical tools. The non-reactive nature of alumina makes certain safety and security in biomedical applications.
Customization alternatives include customized forms, dimensions, and polishing thicknesses. This adaptability satisfies certain operational requirements across sectors. Advanced manufacturing methods guarantee limited resistances and uniformity.
The combination of high alumina content, polishing modern technology, and precision design makes these parts a functional solution for requiring applications. They provide lasting efficiency, lower functional prices, and enhance system efficiency.
Company Introduction
Advanced Ceramics founded on October 17, 2014, is a high-tech enterprise committed to the research and development, production, processing, sales and technical services of ceramic relative materials and products.. Since its establishment in 2014, the company has been committed to providing customers with the best products and services, and has become a leader in the industry through continuous technological innovation and strict quality management.
Our products includes but not limited to Silicon carbide ceramic products, Boron Carbide Ceramic Products, Boron Nitride Ceramic Products, Silicon Carbide Ceramic Products, Silicon Nitride Ceramic Products, Zirconium Dioxide Ceramic Products, Quartz Products, etc. Please feel free to contact us.(nanotrun@yahoo.com)
Payment Methods
T/T, Western Union, Paypal, Credit Card etc.
Shipment Methods
By air, by sea, by express, as customers request.
5 FAQs of Customized High Temperature Resistance Glazed 95% 99% Al2O3 Insulator Alumina Ceramic Components Parts
What are customized high-temperature resistance glazed alumina ceramic components?
These parts are made from aluminum oxide (Al2O3). They handle extreme heat. The glazed surface adds protection. They come in 95% or 99% purity levels. They are used in industries needing heat resistance.
What makes these components suitable for high-temperature environments?
Alumina ceramic resists heat up to 1700°C (95% Al2O3) or 1750°C (99% Al2O3). The glaze layer prevents cracks. It stops chemicals or moisture from damaging the material. They keep strength even under thermal stress.
How do 95% and 99% Al2O3 grades differ?
The 99% grade has higher purity. It performs better in extreme heat. It is denser. It resists wear better. The 95% grade costs less. It works well for slightly lower temperatures. The choice depends on application needs.
Can these parts be customized for specific uses?
Yes. Sizes, shapes, and surface finishes are adjustable. Holes, threads, or special coatings are options. Technical drawings or samples help create precise designs. Customization ensures parts fit exact machinery or processes.
Where are these alumina ceramic components commonly used?
They work in furnaces, kilns, or reactors. Electronics, aerospace, and metal processing industries use them. They insulate electrical systems in high-heat zones. They serve as shields or supports in harsh conditions. They handle wear and corrosion over time.
( Customized High Temperature Resistance Glazed 95% 99% Al2O3 Insulator Alumina Ceramic Components Parts)
REQUEST A QUOTE
RELATED PRODUCTS
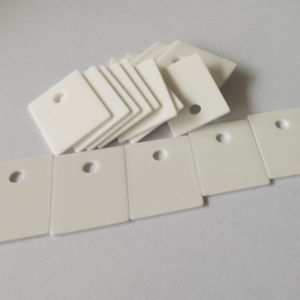
High Heat Resistance 99% Alumina Ceramic Rod
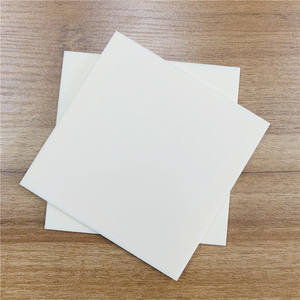
Hot Ceramic Factory Direct Alumina Ceramic Tiles
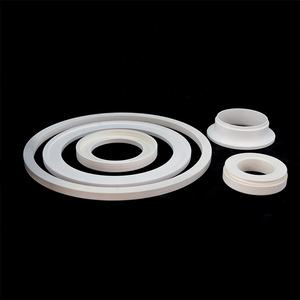
Best Superior Quality Alumina High Temperature Resistance Insulating Ceramic Fixture
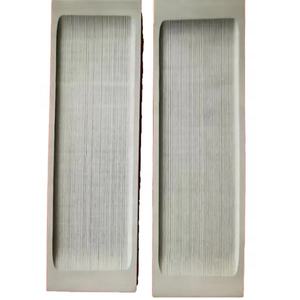
96% Metallization Tube Alumina Ceramics Parts Al2o3 Alumina Ceramic
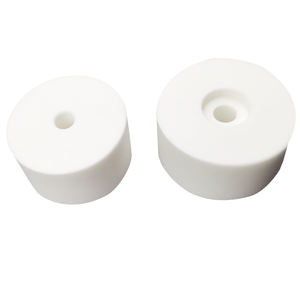
Industrial Heat Resistant 96% Aluminium Oxide Alumina Ceramic Plate
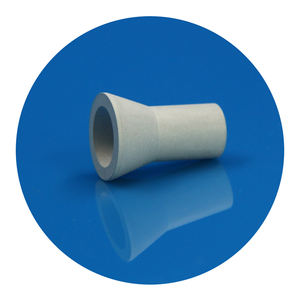