Discover Premium Ceramic Products | Durability & Elegance United | Advanced Ceramics
PRODUCT PARAMETERS
Description
Introduction to Alumina Ceramics
Alumina ceramics are known for their high hardness, wear resistance, corrosion resistance, good electrical insulation and high temperature stability. According to the different alumina content, it can be divided into different grades, such as 95 porcelain, 99 porcelain, etc., among which 99 porcelain refers to ceramic materials with an alumina content of 99%. As the alumina content increases, its mechanical strength and electrical insulation properties will also increase accordingly.
Characteristics of Alumina Ceramics
High Hardness: Alumina ceramics have extremely high hardness, which makes it very wear-resistant and suitable for manufacturing abrasive tools and parts that require wear resistance.
Wear resistance: Due to its high hardness, alumina ceramics show excellent wear resistance and are suitable for manufacturing parts for long-term use.
Corrosion resistance: Alumina ceramics have good resistance to most acids and alkalis, making them widely used in the chemical industry.
Good electrical insulation: As an excellent electrical insulating material, alumina ceramics are widely used in electronic and electrical products.
High temperature stability: Ability to withstand extremely high temperatures without significant physical or chemical changes, which makes it an ideal choice for applications in high temperature environments.
Biocompatibility: In the medical field, certain grades of alumina ceramics are used to make medical devices such as artificial joints due to their good biocompatibility.
(Alumina Foam Ceramic Filter Plate For Molten Aluminum Casting Filtration)
Specifications of Alumina Foam Ceramic Filter Plate For Molten Aluminum Casting Filtration
Alumina foam ceramic filter plates are designed for filtering molten aluminum during casting. These filters remove impurities like oxides and slag to improve metal quality. The main material is high-purity aluminum oxide (Al₂O₃), which ensures chemical stability and heat resistance. The typical Al₂O₃ content ranges from 75% to 85%, balancing strength and thermal shock resistance.
The filter plate has a porous structure with uniform cell distribution. Pore sizes vary between 10 to 30 pores per inch (PPI), allowing precise control over filtration efficiency. Larger pores handle higher flow rates, while smaller pores trap finer particles. This adaptability suits different casting speeds and alloy types.
Operating temperatures reach up to 1600°C (2912°F), making the plates suitable for molten aluminum applications. They maintain structural integrity under repeated thermal cycles, reducing cracking or deformation risks. The open-cell foam design minimizes turbulence in the molten metal, preventing gas entrapment and improving casting surface finish.
Standard dimensions include thicknesses from 20mm to 50mm and lengths up to 500mm. Custom sizes are available for specific machinery or casting setups. The plates are lightweight yet durable, with compressive strengths exceeding 1.5 MPa. This ensures they withstand the pressure of molten metal without collapsing.
Installation is straightforward. The filter fits into existing filtration systems, placed in the launder or gating system. Preheating to 500-800°C before use prevents thermal shock. After casting, residual aluminum easily separates from the filter due to non-wetting properties, simplifying recycling.
These filters reduce defects like inclusions and porosity in final products, enhancing mechanical properties. They are used in automotive, aerospace, and construction industries for parts requiring high precision. Service life depends on operating conditions, but typical usage allows multiple cycles before replacement.
Cost savings come from lower scrap rates and extended equipment lifespan. The filters are compatible with most aluminum alloys, including those with high magnesium or silicon content. Storage requires a dry environment to avoid moisture absorption, which could affect performance during preheating.
Customizable options include varying PPI grades, shapes, and coatings for specialized applications. Testing standards meet industry requirements like ASTM or ISO, ensuring consistent quality. Technical support is available for selecting the optimal filter configuration based on specific casting parameters.
(Alumina Foam Ceramic Filter Plate For Molten Aluminum Casting Filtration)
Applications of Alumina Foam Ceramic Filter Plate For Molten Aluminum Casting Filtration
Alumina foam ceramic filter plates play a key role in molten aluminum casting. These filters clean molten aluminum by trapping impurities like oxides, slag, and solid particles. The process ensures higher-quality final products. The filter plates are made from aluminum oxide, a material known for heat resistance and durability. Their porous structure allows molten metal to flow smoothly while capturing unwanted debris.
Using alumina foam ceramic filters improves the mechanical properties of cast aluminum parts. Defects like cracks, pores, or weak spots are reduced. This leads to stronger, more reliable components. Industries such as automotive, aerospace, and electronics rely on these filters for critical applications. Consistent filtration ensures parts meet strict performance standards.
The filters withstand extreme temperatures during molten metal processing. They remain stable in harsh conditions without breaking down. This makes them cost-effective over time. Frequent replacements are unnecessary. Factories save money on maintenance and downtime.
Installation is straightforward. The filters fit into existing casting systems without major changes. Workers place them in launder systems or casting machines. Molten aluminum passes through the filter before entering molds. No extra steps or delays are added to production.
Alumina foam ceramic filters come in different pore sizes. Options match specific purity requirements. Fine pores capture tiny particles. Coarser pores handle faster flow rates. Manufacturers choose based on their needs.
Environmental benefits exist too. Cleaner aluminum reduces waste from defective castings. Less material is discarded. Energy use drops because remelting flawed products is minimized.
These filters extend the lifespan of downstream equipment. Fewer impurities mean less wear on molds and machinery. Maintenance costs decrease. Production efficiency rises.
Alumina foam ceramic filters are essential for modern aluminum casting. They enhance product quality, cut costs, and support sustainable practices. Industries benefit from reliable, high-performance filtration solutions.
Company Introduction
Advanced Ceramics founded on October 17, 2014, is a high-tech enterprise committed to the research and development, production, processing, sales and technical services of ceramic relative materials and products.. Since its establishment in 2014, the company has been committed to providing customers with the best products and services, and has become a leader in the industry through continuous technological innovation and strict quality management.
Our products includes but not limited to Silicon carbide ceramic products, Boron Carbide Ceramic Products, Boron Nitride Ceramic Products, Silicon Carbide Ceramic Products, Silicon Nitride Ceramic Products, Zirconium Dioxide Ceramic Products, Quartz Products, etc. Please feel free to contact us.(nanotrun@yahoo.com)
Payment Methods
T/T, Western Union, Paypal, Credit Card etc.
Shipment Methods
By air, by sea, by express, as customers request.
5 FAQs of Alumina Foam Ceramic Filter Plate For Molten Aluminum Casting Filtration
Alumina foam ceramic filter plates remove impurities from molten aluminum during casting. These filters improve metal quality. Here are common questions about them. What is an alumina foam ceramic filter plate? It is a porous ceramic made mainly from alumina. The foam structure traps particles in molten aluminum. The material handles high temperatures well. It works in foundries and casting processes. Why use this filter? Aluminum often contains oxides and slag. These defects weaken final products. The filter catches harmful particles. Cleaner aluminum means stronger casts. It reduces waste and improves product performance. How does the filter work? Molten aluminum flows through the filter. The foam structure acts like a sieve. Solid impurities get stuck inside. Pure metal passes through. The process happens quickly. It does not slow production. How to choose the right filter? Consider pore size and thickness. Smaller pores catch finer particles. Thicker filters last longer. Match the filter specs to your metal grade and casting speed. Check the operating temperature range. Confirm the filter fits your mold design. How to install the filter? Place it in the mold’s gating system. Secure it to prevent movement. Preheat the filter before use. This avoids thermal shock. Position it where metal flow is steady. Replace the filter after each casting cycle. Proper installation ensures consistent results.
(Alumina Foam Ceramic Filter Plate For Molten Aluminum Casting Filtration)
REQUEST A QUOTE
RELATED PRODUCTS
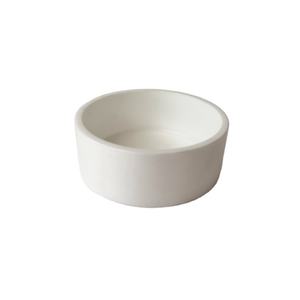
Heat-insulated Fine Ceramic Al2O3 High Purity Alumina Ceramic Products Mechanical Parts OEM Factory
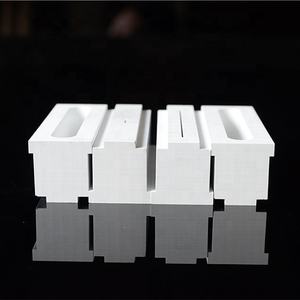
Wear Resistant Al2o3 Alumina Encapsulated Ceramic Package Ceramic Enclosure Ceramic
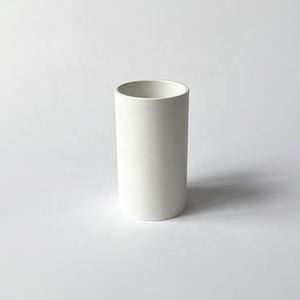
Precision 99% Al2o3 Alumina Ceramic Pellet
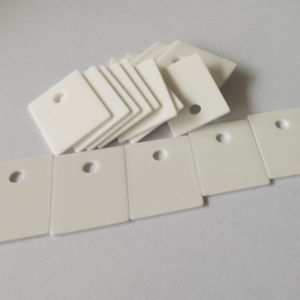
High Heat Resistance 99% Alumina Ceramic Rod
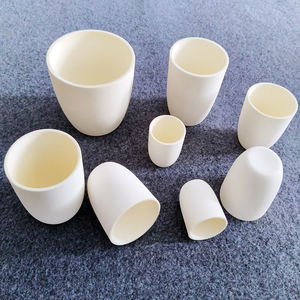
99.5% Industrial Grade CC-1 Ready to Press Granulated Alumina Special Ceramics
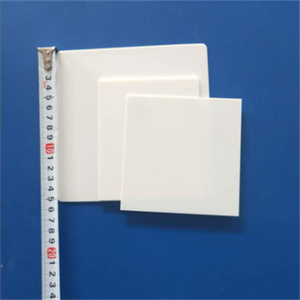