Discover Premium Ceramic Products | Durability & Elegance United | Advanced Ceramics
PRODUCT PARAMETERS
Description
Introduction to Alumina Ceramics
Alumina ceramics are known for their high hardness, wear resistance, corrosion resistance, good electrical insulation and high temperature stability. According to the different alumina content, it can be divided into different grades, such as 95 porcelain, 99 porcelain, etc., among which 99 porcelain refers to ceramic materials with an alumina content of 99%. As the alumina content increases, its mechanical strength and electrical insulation properties will also increase accordingly.
Characteristics of Alumina Ceramics
High Hardness: Alumina ceramics have extremely high hardness, which makes it very wear-resistant and suitable for manufacturing abrasive tools and parts that require wear resistance.
Wear resistance: Due to its high hardness, alumina ceramics show excellent wear resistance and are suitable for manufacturing parts for long-term use.
Corrosion resistance: Alumina ceramics have good resistance to most acids and alkalis, making them widely used in the chemical industry.
Good electrical insulation: As an excellent electrical insulating material, alumina ceramics are widely used in electronic and electrical products.
High temperature stability: Ability to withstand extremely high temperatures without significant physical or chemical changes, which makes it an ideal choice for applications in high temperature environments.
Biocompatibility: In the medical field, certain grades of alumina ceramics are used to make medical devices such as artificial joints due to their good biocompatibility.
(1260/1430 HZ Alumina Silicate Thermal Insulation Ceramic Fiber Module For Industrial Furnace Use)
Specifications of 1260/1430 HZ Alumina Silicate Thermal Insulation Ceramic Fiber Module For Industrial Furnace Use
The 1260/1430 HZ Alumina Silicate Thermal Insulation Ceramic Fiber Module is designed for industrial furnace applications. This product offers high-temperature resistance, durability, and energy efficiency. The module operates effectively in environments up to 1260°C (2300°F) or 1430°C (2606°F), depending on the grade. Its primary material is alumina silicate ceramic fiber, known for low thermal conductivity and minimal heat storage. This ensures consistent insulation, reducing heat loss and improving furnace efficiency.
The ceramic fiber module features a pre-compressed, folded structure. This design simplifies installation and allows the material to expand evenly when exposed to high temperatures. The expansion creates a seamless insulation layer, preventing gaps and enhancing thermal stability. The modules are lightweight, reducing structural load on industrial furnaces.
Applications include lining steelmaking furnaces, glass kilns, petrochemical heaters, and other high-temperature equipment. The material resists thermal shock, chemical corrosion, and mechanical stress. It maintains performance in fluctuating temperatures, ensuring long-term reliability.
Technical specifications include a density range of 220-240 kg/m³. Standard module dimensions are 300x300x250 mm or 300x300x300 mm. Thickness options vary from 200-300 mm. Custom sizes are available for specific furnace designs. The modules comply with industrial safety standards, containing no asbestos or corrosive elements.
Energy savings result from reduced heat transfer, lowering fuel consumption and operational costs. The material’s low heat storage allows faster furnace heating and cooling cycles, improving productivity. Maintenance requirements are minimal due to the product’s resistance to degradation.
The ceramic fiber module is non-toxic and chemically stable. It withstands exposure to most acids, alkalis, and organic solvents. Shrinkage rates remain below 3% after prolonged high-temperature use. This ensures insulation integrity over time.
Installation involves anchoring the modules to the furnace shell using alloy pins or welding. The process requires minimal labor and tools. Compatibility with existing furnace structures simplifies retrofitting. Custom configurations support complex geometries.
The product meets ISO and ASTM standards for thermal insulation materials. Testing confirms fire resistance, thermal stability, and environmental safety. Performance consistency is verified across batch productions.
Industrial users prioritize this module for its balance of cost efficiency and technical performance. It addresses challenges like energy waste, furnace downtime, and maintenance costs. Customizable solutions adapt to diverse operational needs.
(1260/1430 HZ Alumina Silicate Thermal Insulation Ceramic Fiber Module For Industrial Furnace Use)
Applications of 1260/1430 HZ Alumina Silicate Thermal Insulation Ceramic Fiber Module For Industrial Furnace Use
The 1260/1430 HZ alumina silicate thermal insulation ceramic fiber module serves as a high-performance solution for industrial furnace applications. Made from alumina-silicate materials, it withstands extreme temperatures up to 1260°C or 1430°C, depending on the grade. This makes it ideal for furnaces in industries like metallurgy, petrochemicals, and ceramics. The material’s low thermal conductivity minimizes heat loss, improving energy efficiency and reducing operational costs.
These ceramic fiber modules are widely used in heat treatment furnaces, forging furnaces, and steelmaking furnaces. Their lightweight structure allows easy installation compared to traditional refractory bricks. The modules fit tightly into furnace walls, roofs, and doors, ensuring uniform insulation. This design prevents heat leaks and maintains stable internal temperatures, critical for consistent product quality.
The modules resist thermal shock and chemical corrosion, extending furnace lifespan. They handle rapid temperature changes without cracking, a common issue with rigid insulation materials. This durability reduces maintenance frequency, lowering downtime in production cycles. Their flexibility also compensates for furnace expansion during heating, preventing structural damage.
Energy savings are a key advantage. By reducing heat loss, the modules cut fuel consumption, supporting cost-effective operations. This aligns with environmental regulations by lowering carbon emissions. Industries aiming for sustainable practices benefit from the material’s eco-friendly profile.
In high-temperature environments like glass melting furnaces or aluminum processing units, the modules provide reliable insulation. They stabilize internal conditions, ensuring efficient melting and processing. Their low heat storage capacity allows faster furnace heating and cooling, boosting productivity.
Installation is straightforward. The modules come pre-compressed, expanding to fill gaps when heated. This eliminates complex fitting processes. Workers save time, reducing labor costs. The material’s non-toxic nature ensures safety during handling.
Compatibility with existing furnace designs makes the modules a versatile upgrade. They integrate seamlessly with linings, anchors, and other components. Customizable shapes and sizes cater to specific furnace layouts, enhancing adaptability.
Performance remains consistent under prolonged exposure to harsh conditions. The ceramic fibers retain structural integrity, avoiding degradation common in traditional materials. This reliability ensures long-term insulation efficiency, supporting uninterrupted industrial operations.
Company Introduction
Advanced Ceramics founded on October 17, 2014, is a high-tech enterprise committed to the research and development, production, processing, sales and technical services of ceramic relative materials and products.. Since its establishment in 2014, the company has been committed to providing customers with the best products and services, and has become a leader in the industry through continuous technological innovation and strict quality management.
Our products includes but not limited to Silicon carbide ceramic products, Boron Carbide Ceramic Products, Boron Nitride Ceramic Products, Silicon Carbide Ceramic Products, Silicon Nitride Ceramic Products, Zirconium Dioxide Ceramic Products, Quartz Products, etc. Please feel free to contact us.(nanotrun@yahoo.com)
Payment Methods
T/T, Western Union, Paypal, Credit Card etc.
Shipment Methods
By air, by sea, by express, as customers request.
5 FAQs of 1260/1430 HZ Alumina Silicate Thermal Insulation Ceramic Fiber Module For Industrial Furnace Use
What are 1260/1430 Hz alumina silicate ceramic fiber modules made of?
These modules use alumina silicate ceramic fibers. The material includes aluminum oxide and silicon dioxide. It gets processed into lightweight, flexible modules. These handle high heat and resist thermal shock.
What temperature can these modules withstand?
The 1260 Hz type works up to 1260°C (2300°F). The 1430 Hz type handles 1430°C (2606°F). Both suit industrial furnaces. They keep heat inside efficiently. This reduces energy loss.
How are these modules installed in industrial furnaces?
They come pre-compressed. Installers fix them to furnace walls or roofs using anchors. The modules expand after installation. This creates a tight insulation layer. No gaps form. The process is quick. It requires fewer workers than traditional methods.
Why pick ceramic fiber modules over traditional insulation like firebricks?
Ceramic fibers weigh less. This cuts structural stress. They install faster. Their low thermal mass means furnaces heat up quicker. Energy use drops. They also last longer under repeated heating cycles. Firebricks crack over time. These modules stay stable.
Do these modules need regular maintenance?
They need minimal upkeep. Check for physical damage during furnace shutdowns. Replace worn modules if needed. They resist chemical corrosion. Dust buildup is rare. Clean them with compressed air if necessary. Proper installation ensures long service life.
(1260/1430 HZ Alumina Silicate Thermal Insulation Ceramic Fiber Module For Industrial Furnace Use)
REQUEST A QUOTE
RELATED PRODUCTS
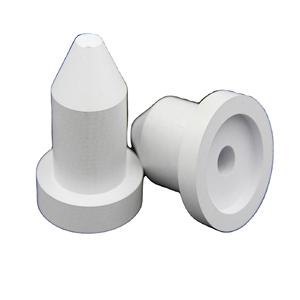
China Factory 99% Al2O3 Crucible Corundum Crucible Alumina Ceramics
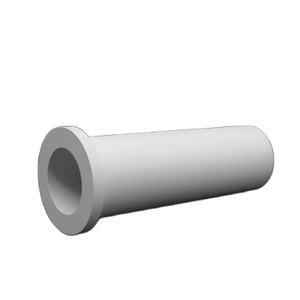
Zirconia Toughened Alumina Ceramics Powder ZTA Ceramic Powder for Precision Ceramics
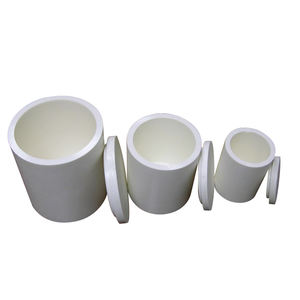
Large Diameter 99.7% Al2o3 High Alumina Ceramic Tube Factory
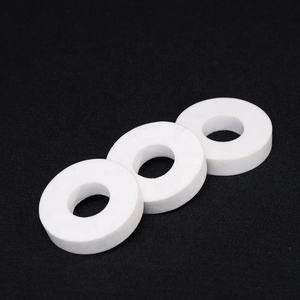
Custom Design Size High Quality Alumina Transparent Ceramic Tube
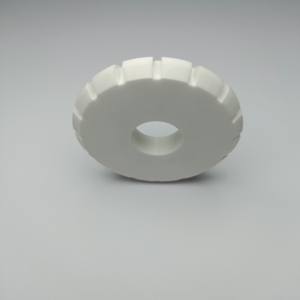
Made In China Industrial Heater Insulators Alumina/Zirconia Ceramic Ring/Tube/Rod/Plate Thread Part
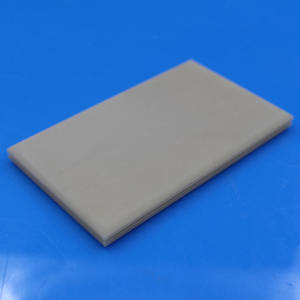