Discover Premium Ceramic Products | Durability & Elegance United | Advanced Ceramics
PRODUCT PARAMETERS
Description
Introduction to Alumina Ceramics
Alumina ceramics are known for their high hardness, wear resistance, corrosion resistance, good electrical insulation and high temperature stability. According to the different alumina content, it can be divided into different grades, such as 95 porcelain, 99 porcelain, etc., among which 99 porcelain refers to ceramic materials with an alumina content of 99%. As the alumina content increases, its mechanical strength and electrical insulation properties will also increase accordingly.
Characteristics of Alumina Ceramics
High Hardness: Alumina ceramics have extremely high hardness, which makes it very wear-resistant and suitable for manufacturing abrasive tools and parts that require wear resistance.
Wear resistance: Due to its high hardness, alumina ceramics show excellent wear resistance and are suitable for manufacturing parts for long-term use.
Corrosion resistance: Alumina ceramics have good resistance to most acids and alkalis, making them widely used in the chemical industry.
Good electrical insulation: As an excellent electrical insulating material, alumina ceramics are widely used in electronic and electrical products.
High temperature stability: Ability to withstand extremely high temperatures without significant physical or chemical changes, which makes it an ideal choice for applications in high temperature environments.
Biocompatibility: In the medical field, certain grades of alumina ceramics are used to make medical devices such as artificial joints due to their good biocompatibility.
(High Alumina Content Alumina Ceramic Tiles for Industrial Kilns Product Category Refractory)
Specifications of High Alumina Content Alumina Ceramic Tiles for Industrial Kilns Product Category Refractory
High alumina content alumina ceramic tiles for commercial kilns fall under the refractory product category. These ceramic tiles deal with severe heat and extreme conditions in high-temperature industrial setups. The key product is alumina (Al two O THREE), with web content ranging from 75% to 95%. Greater alumina degrees enhance thermal stability and resistance to use.
The ceramic tiles endure temperatures as much as 1750 ° C. This makes them appropriate for kiln cellular linings, furnace floors, and burner nozzles. They keep structural honesty under prolonged warm direct exposure. Their low thermal conductivity decreases heat loss, enhancing energy performance in procedures.
Density arrays in between 3.6 g/cm four and 3.9 g/cm four. High density improves mechanical strength and resistance to abrasion. The ceramic tiles withstand hefty lots and mechanical stress without fracturing. Cold crushing toughness surpasses 85 MPa, making certain toughness popular environments.
Thermal shock resistance is a vital attribute. The floor tiles stand up to fracturing when temperatures alter quickly. This is critical in kilns where home heating and cooling down cycles are frequent. Chemical security is one more advantage. They resist rust from acids, alkalis, and molten steels. This expands service life in aggressive chemical setups.
Criterion dimensions consist of rectangular shapes, squares, and custom shapes. Density varies from 10 mm to 50 mm. Customized measurements fit specific kiln styles. Installment methods include securing systems or sticky bonding. Proper installation ensures limited seams and decreases warmth leak.
Applications extend steelmaking, cement manufacturing, glass manufacturing, and non-ferrous metal handling. The ceramic tiles line rotary kilns, ladles, and combustion chambers. They secure equipment from thermal damages and minimize downtime for repairs.
Color ranges from white to ivory, relying on alumina purity. Surface surface is smooth to decrease friction with relocating components. Machining accuracy ensures constant measurements for easy suitable.
These floor tiles offer lasting price financial savings. High toughness decreases replacement regularity. Reduced maintenance requirements reduced operational expenses. Efficiency continues to be steady also after duplicated thermal cycles.
Quality assurance consists of testing for thickness, porosity, and thermal growth. Each set meets sector criteria for refractory products. Qualifications make certain dependability in critical high-temperature applications.
Customization options include alumina content changes, surface area therapies, and specific mechanical properties. Technical support assists choose the appropriate quality for one-of-a-kind operational requirements.
The product suits industries focusing on effectiveness, safety, and devices longevity. It addresses difficulties in high-heat processes while keeping operational consistency.
(High Alumina Content Alumina Ceramic Tiles for Industrial Kilns Product Category Refractory)
Applications of High Alumina Content Alumina Ceramic Tiles for Industrial Kilns Product Category Refractory
High alumina web content alumina ceramic floor tiles offer vital duties in commercial kilns. These ceramic tiles consist of over 70% alumina. This composition guarantees remarkable efficiency in high-temperature environments. They withstand extreme heat without warping. Their high melting factor exceeds 1700 ° C. This makes them perfect for lining kilns, heating systems, and activators. Industrial refines demand materials that resist thermal anxiety. These floor tiles manage quick temperature changes properly. Thermal shock resistance prevents fracturing. This prolongs the life-span of kiln linings.
Chemical stability is an additional essential advantage. The tiles withstand deterioration from acidic or alkaline substances. Molten steels and slag do not conveniently deteriorate them. This is crucial in steelmaking and glass production. They maintain architectural honesty under rough conditions. Dust and gas exposure in concrete plants position difficulties. These floor tiles minimize wear and maintenance needs.
Industries like porcelains, metallurgy, and petrochemicals rely on these tiles. They line kiln wall surfaces, floors, and roofs. Heater nozzles and thermal barrier utilize them for defense. Their insulation buildings improve power effectiveness. Warm loss reduces. Gas consumption decreases. Running expenses lower over time.
Manufacturing involves innovative sintering techniques. Basic material undergo high-pressure developing. High-temperature shooting makes sure density and strength. The outcome is an item with reduced porosity. This enhances sturdiness. Custom-made shapes and sizes fit specific kiln designs. Installment continues to be uncomplicated.
Compared to standard refractory materials, these ceramic tiles last longer. Fireclay or silica bricks deteriorate faster. Regular replacements interfere with operations. High alumina tiles minimize downtime. They supply a cost-effective solution regardless of higher initial prices. Efficiency justifies the financial investment.
Industries prioritize security and efficiency. These floor tiles fulfill both requirements. They handle mechanical stress from heavy loads. Abrasion resistance prevents surface damages. Consistent efficiency under tons makes certain trusted operation.
High alumina ceramic floor tiles adjust to various commercial needs. Their versatility makes them a preferred choice. They address difficulties in severe atmospheres effectively.
Company Introduction
Advanced Ceramics founded on October 17, 2014, is a high-tech enterprise committed to the research and development, production, processing, sales and technical services of ceramic relative materials and products.. Since its establishment in 2014, the company has been committed to providing customers with the best products and services, and has become a leader in the industry through continuous technological innovation and strict quality management.
Our products includes but not limited to Silicon carbide ceramic products, Boron Carbide Ceramic Products, Boron Nitride Ceramic Products, Silicon Carbide Ceramic Products, Silicon Nitride Ceramic Products, Zirconium Dioxide Ceramic Products, Quartz Products, etc. Please feel free to contact us.(nanotrun@yahoo.com)
Payment Methods
T/T, Western Union, Paypal, Credit Card etc.
Shipment Methods
By air, by sea, by express, as customers request.
5 FAQs of High Alumina Content Alumina Ceramic Tiles for Industrial Kilns Product Category Refractory
High alumina content alumina ceramic tiles for industrial kilns handle extreme heat and harsh conditions. Here are 5 common questions about them.
What are high alumina ceramic tiles made of? These tiles contain over 75% alumina. The rest includes silica and trace additives. High alumina boosts strength and heat resistance. This makes them ideal for kilns and furnaces.
Why pick high alumina tiles over regular refractory materials? Regular materials crack under rapid temperature shifts. High alumina tiles handle thermal shock better. They resist chemical corrosion and wear. This cuts downtime and replacement costs in industrial settings.
What temperatures can these tiles withstand? They work in environments up to 1750°C. Their structure stays stable under prolonged heat. This prevents warping or breaking. Consistent performance ensures kilns operate safely for longer.
How are these tiles installed in kilns? Installation uses anchoring systems or adhesive bonding. Proper fitting avoids gaps. Experts recommend professional installation. This ensures even heat distribution and prevents damage during use.
Do high alumina tiles need special maintenance? Minimal maintenance is required. Inspect tiles regularly for cracks or erosion. Replace damaged sections quickly. Avoid sudden temperature drops after shutdowns. Clean surfaces with non-abrasive tools to preserve integrity.
These tiles suit industries like steel, cement, and glass manufacturing. Their durability and heat resistance make them a reliable choice for heavy-duty applications.
(High Alumina Content Alumina Ceramic Tiles for Industrial Kilns Product Category Refractory)
REQUEST A QUOTE
RELATED PRODUCTS
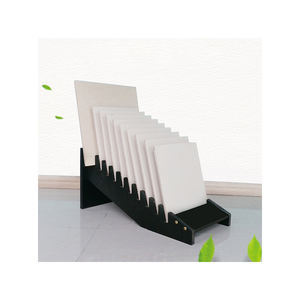
92% Alumina Ceramic Grinding Ball 92% Alumina Grinding Balls Alumina Ball For Ceramic
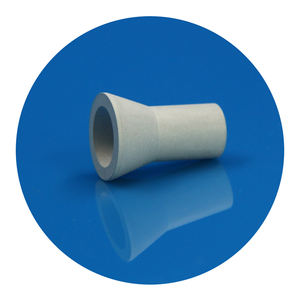
High Purity Alumina Ceramic Oem Custom CNC Machining Technical White Zirconium Oxide Product Zirconia Ceramic
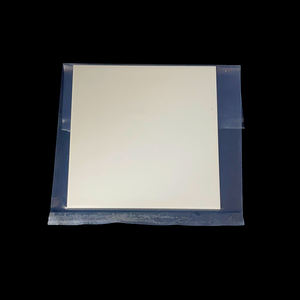
High-Performance 95% Alumina Ceramic Blocks
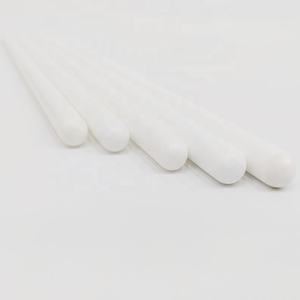
Square / Hexagon Al2o3 Alumina Ceramic Tiles and Plates
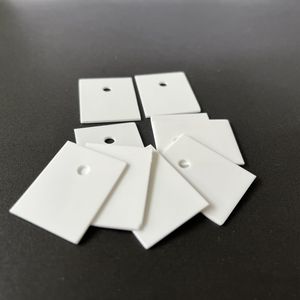
Wear Resistant Alumina Ceramic Thin Sheets Zirconia Tounghness Alumina ZTA Ceramic Plate
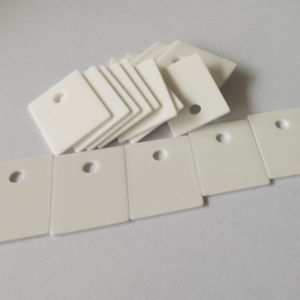