Discover Premium Ceramic Products | Durability & Elegance United | Advanced Ceramics
PRODUCT PARAMETERS
Description
Introduction to Quartz Ceramic Products
Quartz ceramic, also known as fused quartz ceramic or pure silicon ceramic, is an advanced ceramic material made of pure silicon dioxide (SiO₂). It is made by melting high-purity quartz sand at high temperature and then cooling and solidifying it. It has unique physical and chemical properties, making it an ideal choice for many high-tech applications. Quartz ceramic products are widely used in semiconductor manufacturing, optics, electronics, chemical industry and high-temperature industries.
Characteristics and advantages of quartz ceramics
Extremely high thermal stability: Quartz ceramics can remain stable under extreme temperature conditions. They are not only resistant to high temperatures, but also show excellent thermal shock resistance in rapid temperature changes.
Low thermal expansion coefficient: Due to its low thermal expansion coefficient, quartz ceramics have good dimensional stability when the temperature changes and are not easy to deform or crack.
Excellent electrical insulation: Provides excellent electrical insulation performance and is suitable for applications requiring high voltage isolation.
High transparency: It has good light transmittance in a wide band from ultraviolet to infrared, and is particularly suitable for applications such as optical windows and lenses.
Chemical stability: Excellent resistance to most acids, alkalis and other corrosive substances, and almost unaffected by other chemicals except hydrofluoric acid and phosphoric acid.
Mechanical strength: Although quartz ceramic is not as hard as some other types of ceramics, it still has enough mechanical strength to meet the needs of many application scenarios.
High UV transmittance: It has high transmittance in the ultraviolet region, which makes it very useful in UV curing equipment and UV spectrometers.
(Factory Quartz Limestone Coal Ceramic Dry Cement Mill,Industrial Wet Gold Ore Mining Ball Mill for )
Specifications of Factory Quartz Limestone Coal Ceramic Dry Cement Mill,Industrial Wet Gold Ore Mining Ball Mill for
The Factory Quartz Limestone Coal Ceramic Dry Cement Mill handles hard materials like quartz, limestone, coal, ceramic, and cement clinker. It works in dry conditions. The mill processes materials into fine powders. It has a large capacity, handling up to 150 tons per hour. The motor power ranges from 18.5 kW to 4500 kW. The machine’s drum measures between 2.1×4.5 meters and 4.2×13 meters. Steel balls or rods inside grind materials efficiently. The mill’s strong build ensures long-term use. It resists wear and heat. The design focuses on low energy use. Maintenance is simple. Operators adjust the grinding speed as needed. The machine suits large-scale production lines. It fits cement plants, mining sites, and chemical factories.
The Industrial Wet Gold Ore Mining Ball Mill processes gold, copper, and other ores. It works in wet conditions. Water mixes with raw ore during grinding. This creates a slurry for easier processing. The mill handles up to 200 tons per hour. The motor power ranges from 22 kW to 6300 kW. The drum size varies from 1.5×3 meters to 4.5×8 meters. Steel balls inside crush ore into fine particles. The mill uses corrosion-resistant materials. It performs steadily under heavy loads. Safety features prevent leaks or overloads. The design allows easy control of particle size. Operators adjust water and ore ratios for optimal results. This machine works in mining operations, metallurgy plants, and ore-processing facilities. Both mills use advanced technology for reliable output. They reduce downtime and operational costs.
(Factory Quartz Limestone Coal Ceramic Dry Cement Mill,Industrial Wet Gold Ore Mining Ball Mill for )
Applications of Factory Quartz Limestone Coal Ceramic Dry Cement Mill,Industrial Wet Gold Ore Mining Ball Mill for
The Factory Quartz Limestone Coal Ceramic Dry Cement Mill handles dry grinding tasks for materials like quartz, limestone, coal, ceramic, and cement clinker. It crushes raw materials into fine powders for construction, ceramics, and industrial products. Built with strong steel or wear-resistant alloys, it works in tough conditions. High grinding efficiency comes from advanced liners and grinding media. Adjustable rotation speeds let users control particle size. The design minimizes heat during grinding to protect material quality. Low energy use cuts operating costs. Automated systems monitor performance and adjust settings for consistent output. Customizable sizes and capacities fit small factories or large plants.
The Industrial Wet Gold Ore Mining Ball Mill processes wet materials like gold ore. It mixes water with ore to form a slurry, improving mineral extraction. This method suits metals like gold, copper, and silver. The mill’s drum uses rubber or metal liners to resist corrosion and wear. Steel balls inside grind ore into fine particles for easier separation. It handles high moisture content without clogging. Robust motors ensure steady operation in mining sites. Simple maintenance reduces downtime. Safety features include overload protection and secure seals to prevent leaks.
Both mills suit industries needing precise material processing. The dry mill focuses on non-metallic materials for construction and manufacturing. The wet mill targets metal ore processing for mining. Durable parts extend service life. Energy-saving designs meet environmental standards. Automation lowers labor costs. Custom setups adapt to specific material needs. Easy installation and operation save time. Regular inspections keep performance stable. Low noise and vibration improve workplace safety.
These mills serve cement plants, mining companies, ceramic factories, and chemical industries. They boost production rates while maintaining quality. Reliable performance ensures long-term partnerships with clients. Cost-effective solutions help businesses grow. Technical support is available for setup and troubleshooting. Global standards guarantee safe, efficient operations.
Company Introduction
Advanced Ceramics founded on October 17, 2014, is a high-tech enterprise committed to the research and development, production, processing, sales and technical services of ceramic relative materials and products.. Since its establishment in 2014, the company has been committed to providing customers with the best products and services, and has become a leader in the industry through continuous technological innovation and strict quality management.
Our products includes but not limited to Silicon carbide ceramic products, Boron Carbide Ceramic Products, Boron Nitride Ceramic Products, Silicon Carbide Ceramic Products, Silicon Nitride Ceramic Products, Zirconium Dioxide Ceramic Products, Quartz Products, etc. Please feel free to contact us.(nanotrun@yahoo.com)
Payment Methods
T/T, Western Union, Paypal, Credit Card etc.
Shipment Methods
By air, by sea, by express, as customers request.
5 FAQs of Factory Quartz Limestone Coal Ceramic Dry Cement Mill,Industrial Wet Gold Ore Mining Ball Mill for
What is the Factory Quartz Limestone Coal Ceramic Dry Cement Mill used for?
This mill grinds materials like quartz, limestone, coal, ceramic, and cement clinker into fine powder. It works in dry conditions. It is common in construction and mining industries. The machine ensures consistent particle size. It boosts production efficiency in large-scale operations.
How does the Industrial Wet Gold Ore Mining Ball Mill work?
This mill processes gold ore with water. The rotating drum contains steel balls. The ore and water mix inside. The balls crush the ore into smaller particles. This method is effective for extracting gold. It works well in wet grinding conditions.
What is the difference between dry and wet mills?
Dry mills process materials without water. They suit moisture-sensitive substances like cement. Wet mills use water. They handle materials needing slurry formation, like gold ore. Wet milling prevents dust. Dry milling saves energy.
How do I maintain these mills for long-term use?
Check parts regularly. Lubricate bearings and gears to reduce friction. Replace worn-out liners and grinding media. Clean the mill after use. Inspect motors and belts for wear. Follow the manufacturer’s guidelines. Proper maintenance avoids breakdowns.
Can these mills handle other materials?
They are designed for specific materials listed. The dry mill handles quartz, limestone, coal, ceramic, and cement. The wet mill focuses on gold ore. Using unapproved materials risks damage. Confirm compatibility before testing new substances.
What safety precautions are needed?
Operators must wear protective gear. Secure loose clothing near moving parts. Follow lockout procedures during maintenance. Keep the work area clean. Monitor temperature and pressure during operation. Train staff on emergency protocols. Never bypass safety features.
(Factory Quartz Limestone Coal Ceramic Dry Cement Mill,Industrial Wet Gold Ore Mining Ball Mill for )
REQUEST A QUOTE
RELATED PRODUCTS
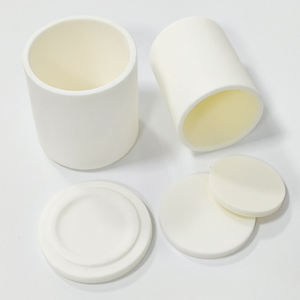
Hot Pressed Diamond Saw Blade Cutting Disc 4” 105mm 110mm Wet Dry Ceramic Homogeneous Tile Granite Marble Quartz
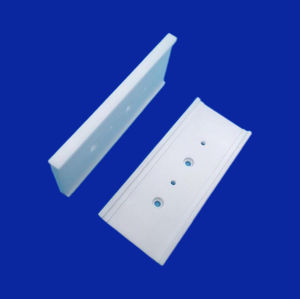
Ceramic Liner Ball Mill for Quartz (CE Certification)
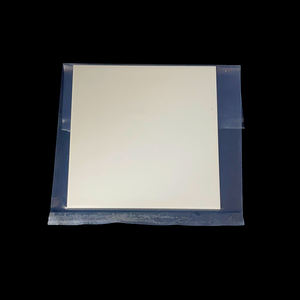
Good Product Custom Ceramics Quartz Stone Press Machine for Marble Granite
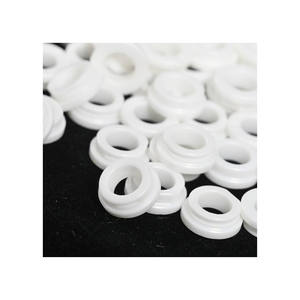
Quartz Sand Swing Sieve Fine Powder Gyratory Sifter Ceramic Powder Square Tumbler Screen
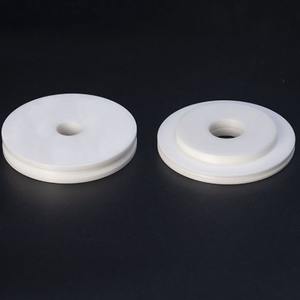
Factory Dry & Wet Ball Mill 900*3000 Quartz Limestone Coal Ceramic Cement Dry Grinding Mill Machine for
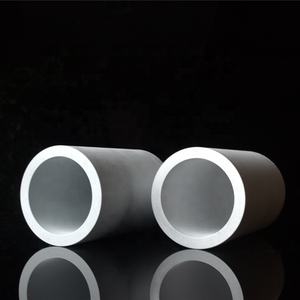