Discover Premium Ceramic Products | Durability & Elegance United | Advanced Ceramics
PRODUCT PARAMETERS
Description
Overview of Silicon Carbide Ceramics
Silicon Carbide (SiC) ceramics are renowned for their outstanding mechanical properties, including high hardness, strength at elevated temperatures, and excellent thermal shock resistance. These materials are pivotal in cutting-edge industrial applications, from abrasives to aerospace components, due to their unique combination of properties.
Features of Silicon Carbide Ceramics
High Hardness: Exceptional wear resistance.
Thermal Shock Resistance: Can withstand rapid temperature changes.
Chemical Stability: Resistant to most chemicals.
High Thermal Conductivity: Efficient heat dissipation.
Low Density: Lightweight for its strength.
(Abrasive Resistance Silicon Carbide SIC Ceramic Crucible)
Specification of Abrasive Resistance Silicon Carbide SIC Ceramic Crucible
The abrasive resistance silicon carbide (SiC) ceramic crucible is designed for high-temperature industrial applications. It handles harsh environments like metal melting, chemical processing, and abrasive material handling. The crucible is made from high-purity silicon carbide. It is formed through advanced sintering techniques. This ensures a dense structure with minimal porosity. The material’s inherent hardness (Mohs scale 9-9.5) provides exceptional resistance to wear, erosion, and mechanical impact.
The crucible’s composition includes silicon carbide grains bonded with a silicon nitride or reaction-sintered matrix. This enhances structural integrity. It maintains stability under rapid temperature changes. The thermal shock resistance prevents cracking during heating or cooling cycles. The working temperature range is up to 1600°C in oxidizing atmospheres. It withstands 1800°C in inert or reducing conditions.
Surface finish is optimized to reduce material adhesion. This simplifies cleaning and extends service life. The crucible’s low thermal expansion coefficient (4.0×10^-6/°C) minimizes dimensional changes under heat. High thermal conductivity (120 W/m·K) ensures even heat distribution. This improves process efficiency.
Chemical inertness makes it resistant to acids, alkalis, and molten metals. It avoids contamination of processed materials. The product is available in custom sizes. Standard capacities range from 50 mL to 20 liters. Wall thickness varies between 5 mm and 25 mm. Options include lids, handles, or reinforced rims for specific handling needs.
Testing confirms abrasion resistance through ASTM G65 standards. Results show minimal mass loss under high-stress conditions. Typical applications include foundries, laboratories, and semiconductor manufacturing. It replaces traditional materials like clay-graphite or alumina. Performance is consistent in repeated cycles. Maintenance requirements are low.
The crucible’s durability reduces replacement frequency. Operational costs decrease over time. Compatibility with induction heating systems is verified. No pre-treatment is needed before initial use. Storage guidelines recommend keeping it dry to prevent surface oxidation. Handling instructions emphasize avoiding mechanical impacts during transport.
(Abrasive Resistance Silicon Carbide SIC Ceramic Crucible)
Applications of Abrasive Resistance Silicon Carbide SIC Ceramic Crucible
Abrasion-resistant silicon carbide (SiC) ceramic crucibles are highly durable tools designed for extreme conditions. They handle high temperatures, chemical exposure, and mechanical wear effectively. These crucibles are widely used across industries requiring reliable performance in harsh environments.
Metallurgy relies on SiC crucibles for melting metals like iron, aluminum, and copper alloys. They withstand temperatures above 1600°C without degrading. Traditional materials like clay or graphite fail under similar stress. SiC crucibles last longer, reduce contamination risks, and improve process efficiency.
Chemical processing industries use these crucibles to manage corrosive substances. Acids, alkalis, and molten salts react minimally with SiC ceramics. This makes them ideal for synthesizing compounds or testing reactive materials. Labs and production plants benefit from their stability and low maintenance.
Jewelry manufacturers depend on SiC crucibles for precise alloy mixing. The material’s resistance to thermal shock prevents cracks during rapid heating or cooling. Gold, silver, and platinum processing becomes safer and more consistent. Small studios and large factories both use them for repeatable results.
Glass and ceramics production requires crucibles that endure molten materials. SiC ceramics handle molten glass and ceramic slurries without eroding. Their thermal conductivity ensures even heat distribution, critical for quality output. Furnace operators prefer them for reducing downtime and material waste.
Mining and material science applications involve grinding or analyzing abrasive samples. SiC crucibles resist wear from hard minerals or powders. Researchers use them to prepare samples for testing. Their longevity cuts replacement costs in labs handling abrasive substances.
SiC ceramic crucibles adapt to diverse industrial needs. Their toughness, thermal properties, and chemical inertness make them indispensable. Industries prioritize them for tasks demanding precision, durability, and cost-effectiveness.
Company Introduction
Advanced Ceramics founded on October 17, 2014, is a high-tech enterprise committed to the research and development, production, processing, sales and technical services of ceramic relative materials and products.. Since its establishment in 2014, the company has been committed to providing customers with the best products and services, and has become a leader in the industry through continuous technological innovation and strict quality management.
Our products includes but not limited to Silicon carbide ceramic products, Boron Carbide Ceramic Products, Boron Nitride Ceramic Products, Silicon Carbide Ceramic Products, Silicon Nitride Ceramic Products, Zirconium Dioxide Ceramic Products, Quartz Products, etc. Please feel free to contact us.(nanotrun@yahoo.com)
Payment Methods
T/T, Western Union, Paypal, Credit Card etc.
Shipment Methods
By air, by sea, by express, as customers request.
5 FAQs of Abrasive Resistance Silicon Carbide SIC Ceramic Crucible
What is an abrasive resistance silicon carbide ceramic crucible? This crucible is made from silicon carbide. It handles high heat and resists wear. It is used in labs and industries for melting metals or holding chemicals. The material is strong and lasts longer than other ceramics.
What temperature can it handle? The crucible works in temperatures up to 1600°C. Short-term use can go higher. Avoid sudden temperature changes. These changes might cause cracks. The crucible works well in furnaces or high-heat processes.
How long does it last? It depends on usage. High temperatures or harsh chemicals reduce lifespan. Proper care makes it last longer. Handle it gently. Avoid dropping or hitting it. Check for cracks or wear regularly. Replace it if damage is visible.
What industries use this crucible? Metallurgy uses it for melting metals like gold or aluminum. Chemical labs use it for reactions needing heat. Glassmaking and ceramics rely on it for high-heat steps. Research labs use it for experiments. It suits any process needing heat resistance and durability.
How to clean and maintain it? Let it cool after use. Remove leftover material with a soft brush. Soak in mild detergent if residue sticks. Avoid harsh chemicals or scraping. Store it in a dry place. Keep it separate from harder materials to prevent scratches. Handle with care to avoid cracks.
(Abrasive Resistance Silicon Carbide SIC Ceramic Crucible)
REQUEST A QUOTE
RELATED PRODUCTS
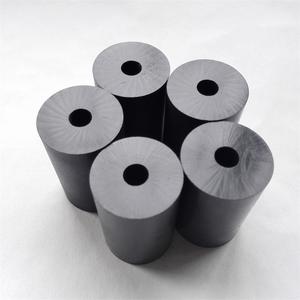
Hot ing Cheap F4-F6000 Honeycomb Ceramic Filter Dust Removal Powder Siliconcarbide Black Silicon Carbide Powder for Blasting
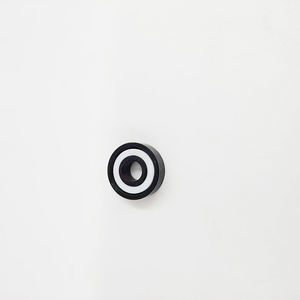
Light Weight Ceramic Silicon Carbide Plate
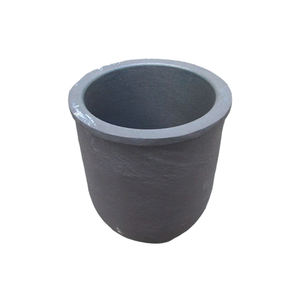
Silicon Carbide Ceramic Refractory Plate
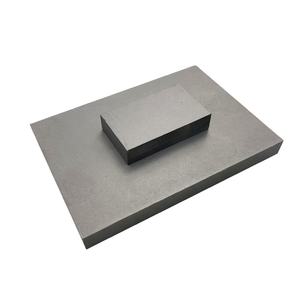
Silicon Carbide Ceramic Plates Hexagonal Customizable
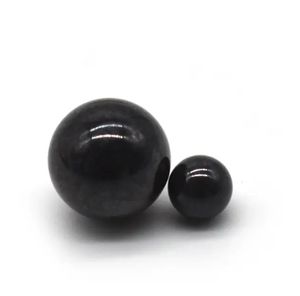
High Thermal Conductivity Silicon Carbide SiC Ceramic Tube
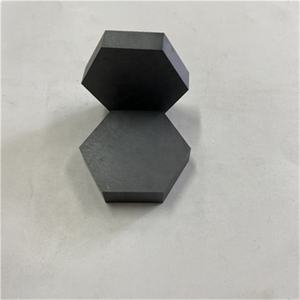