Discover Premium Ceramic Products | Durability & Elegance United | Advanced Ceramics
PRODUCT PARAMETERS
Description
Introduction to Alumina Ceramics
Alumina ceramics are known for their high hardness, wear resistance, corrosion resistance, good electrical insulation and high temperature stability. According to the different alumina content, it can be divided into different grades, such as 95 porcelain, 99 porcelain, etc., among which 99 porcelain refers to ceramic materials with an alumina content of 99%. As the alumina content increases, its mechanical strength and electrical insulation properties will also increase accordingly.
Characteristics of Alumina Ceramics
High Hardness: Alumina ceramics have extremely high hardness, which makes it very wear-resistant and suitable for manufacturing abrasive tools and parts that require wear resistance.
Wear resistance: Due to its high hardness, alumina ceramics show excellent wear resistance and are suitable for manufacturing parts for long-term use.
Corrosion resistance: Alumina ceramics have good resistance to most acids and alkalis, making them widely used in the chemical industry.
Good electrical insulation: As an excellent electrical insulating material, alumina ceramics are widely used in electronic and electrical products.
High temperature stability: Ability to withstand extremely high temperatures without significant physical or chemical changes, which makes it an ideal choice for applications in high temperature environments.
Biocompatibility: In the medical field, certain grades of alumina ceramics are used to make medical devices such as artificial joints due to their good biocompatibility.
(Catalyst Support Media Alumina Ceramic Packing Ball)
Specifications of Catalyst Support Media Alumina Ceramic Packing Ball
Catalyst support media alumina ceramic packing balls are designed for high-performance applications in industrial processes. These balls are made from high-purity aluminum oxide (Al₂O₃) with a composition ranging between 92% and 99.5%. This ensures excellent chemical stability and resistance to harsh environments. The material’s high thermal stability allows operation in temperatures up to 1600°C. They handle rapid temperature changes without cracking, making them suitable for processes involving sudden heating or cooling.
Alumina ceramic packing balls provide strong mechanical properties. They have a high crush strength, typically above 130 MPa, which prevents deformation under heavy loads. Their hardness measures around 9 on the Mohs scale, ensuring minimal wear over time. This durability reduces the need for frequent replacements.
The balls resist chemical corrosion from acids, alkalis, and organic solvents. This makes them ideal for use in reactors, towers, and columns where aggressive chemicals are present. Their low surface area and controlled porosity prevent unwanted interactions with catalysts or reactants. This maintains process efficiency and product purity.
Standard sizes range from 3mm to 50mm in diameter. Custom sizes and shapes like rings or cylinders are available for specific needs. The smooth surface of the balls ensures even distribution of catalysts and gases, improving reaction rates.
These packing balls are widely used in petroleum refining, chemical synthesis, and environmental engineering. They serve as support beds for catalysts in hydrogen production, sulfur recovery, and emission control systems. Their inert nature prevents contamination of sensitive reactions.
Benefits include extended catalyst life, reduced energy consumption, and lower maintenance costs. The high-temperature performance and chemical resistance ensure reliable operation in demanding conditions. Their uniform size and shape promote consistent flow dynamics within reactors.
Alumina ceramic packing balls meet industry standards for quality and safety. They are tested for thermal shock resistance, compressive strength, and chemical inertness. Manufacturers provide technical support for selecting the right grade based on application requirements.
(Catalyst Support Media Alumina Ceramic Packing Ball)
Applications of Catalyst Support Media Alumina Ceramic Packing Ball
Catalyst support media alumina ceramic packing balls are widely used in industrial processes. These balls provide a stable structure for catalysts. They help improve reaction efficiency. Their high surface area allows even distribution of catalysts. This ensures optimal contact between reactants and catalysts. Alumina ceramic packing balls work well in high-temperature environments. They resist thermal shock. They maintain structural integrity under extreme conditions. This makes them suitable for demanding applications.
The chemical industry relies on alumina ceramic packing balls. They are common in catalytic reactors. These reactors produce chemicals like ammonia and methanol. The balls support catalysts during reactions. They prevent catalyst particles from moving or clumping. This ensures consistent reaction rates. The petrochemical industry also uses these balls. They are found in refining processes. Examples include hydrocracking and hydrogenation. The balls help convert heavy hydrocarbons into lighter fuels. They handle aggressive chemicals without degrading.
Environmental engineering applications benefit from alumina ceramic packing balls. They are used in emission control systems. Examples include catalytic converters and flue gas treatment. The balls support catalysts that break down pollutants. They help reduce harmful emissions from industrial exhaust. Their durability ensures long-term performance. This lowers maintenance costs.
Power generation uses alumina ceramic packing balls in gas purification. They remove impurities from syngas before combustion. This improves energy efficiency. The balls also function in hydrogen production. They support catalysts during steam methane reforming. Their thermal stability is critical here.
Other industries use alumina ceramic packing balls. Examples include pharmaceuticals and food processing. They assist in catalytic reactions needed for product synthesis. Their inert nature prevents contamination. This ensures product purity.
Alumina ceramic packing balls offer mechanical strength. They resist wear and corrosion. Their uniform size and shape promote even fluid flow. This prevents channeling in packed beds. These properties make them a reliable choice for catalyst support.
Company Introduction
Advanced Ceramics founded on October 17, 2014, is a high-tech enterprise committed to the research and development, production, processing, sales and technical services of ceramic relative materials and products.. Since its establishment in 2014, the company has been committed to providing customers with the best products and services, and has become a leader in the industry through continuous technological innovation and strict quality management.
Our products includes but not limited to Silicon carbide ceramic products, Boron Carbide Ceramic Products, Boron Nitride Ceramic Products, Silicon Carbide Ceramic Products, Silicon Nitride Ceramic Products, Zirconium Dioxide Ceramic Products, Quartz Products, etc. Please feel free to contact us.(nanotrun@yahoo.com)
Payment Methods
T/T, Western Union, Paypal, Credit Card etc.
Shipment Methods
By air, by sea, by express, as customers request.
5 FAQs of Catalyst Support Media Alumina Ceramic Packing Ball
Catalyst support media alumina ceramic packing balls are used in chemical reactors. They provide a stable surface for catalysts. They help spread gases or liquids evenly. This improves reaction efficiency. They handle high temperatures and pressure. They work in harsh chemical environments.
People choose alumina ceramic balls for their durability. They last longer than other materials. They resist wear and corrosion. They keep catalysts stable over time. This reduces replacement costs. They also handle thermal shocks well. Sudden temperature changes do not damage them.
The main benefits include better heat distribution. They stop catalysts from clumping. This keeps reactions consistent. They lower energy use by improving flow. Their strength cuts downtime. Maintenance becomes simpler. They are cost-effective for industrial processes.
These balls are used in oil refining. They appear in petrochemical plants. Gas processing units need them. Chemical synthesis relies on them. They suit ammonia production. Any high-temperature catalytic reaction can use them. Both new setups and old systems benefit.
Regular checks ensure they work well. Look for cracks or chips. Clean them if blocked by debris. Replace damaged balls quickly. Follow the maker’s guidelines for upkeep. Proper care extends their lifespan. It keeps the reactor running smoothly.
(Catalyst Support Media Alumina Ceramic Packing Ball)
REQUEST A QUOTE
RELATED PRODUCTS
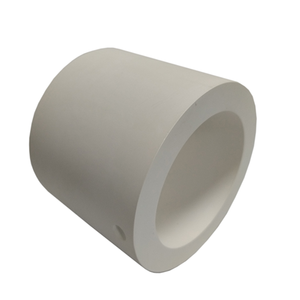
Porous Alumina Ceramic Ball Premium Ceramics Product
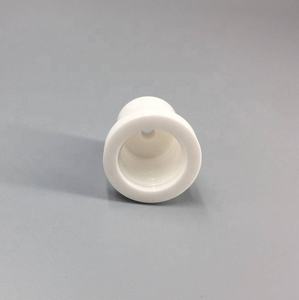
High Temperature Resistance Alumina Ceramic Crucible for Industry Application
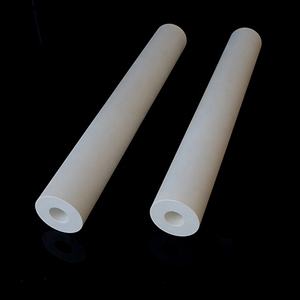
95-Alumina pipes ceramic tube
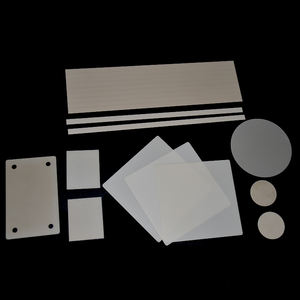
High Pressure 95 Alumina Ceramic Socket Beads Whole Parts
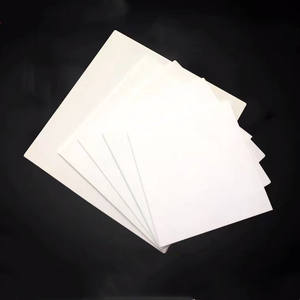
99 Ceramic Machining Parts 95 96 99 99.8 Al2O3 Alumina Ceramic
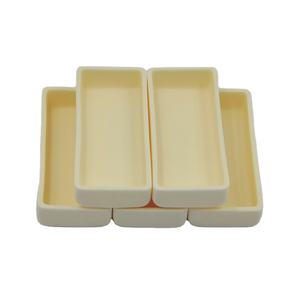