Discover Premium Ceramic Products | Durability & Elegance United | Advanced Ceramics
PRODUCT PARAMETERS
Description
Overview of Silicon Nitride Ceramics
Silicon Nitride Ceramics are high-performance materials known for their excellent mechanical properties, including strength, toughness, and resistance to wear, corrosion, and thermal shock, making them ideal for demanding applications in various industries.
Features of Silicon Nitride Ceramics
Exceptional hardness and wear resistance.
Superior mechanical strength and fracture toughness.
Excellent thermal stability and resistance to thermal shock.
High corrosion resistance in aggressive environments.
Low density contributing to lightweight components.
(Advanced Custom Made Manufactory Silicon Nitride Si3N4 Ceramic Roller Wheel Tube)
Specifications of Advanced Custom Made Manufactory Silicon Nitride Si3N4 Ceramic Roller Wheel Tube
The Advanced Personalized Made Manufactory Silicon Nitride Si3N4 Ceramic Roller Wheel Tube is crafted for high-performance commercial applications. It is made from premium-grade silicon nitride ceramic, understood for remarkable mechanical residential properties. The material make-up makes certain high stamina, thermal shock resistance, and longevity in extreme problems. It operates properly in temperatures as much as 1200 ° C without shedding architectural integrity. This makes it ideal for high-temperature settings like heating systems, steel handling, and aerospace systems.
The ceramic roller features a density of 3.2-3.3 g/cm SIX, giving light-weight efficiency compared to steel options. Its hardness surpasses 85 HRA, guaranteeing minimal wear over time. The low thermal expansion coefficient lowers deformation dangers under fast temperature level adjustments. This security prolongs life span in applications with regular thermal biking.
Surface area surface choices consist of polished or precision-ground textures to satisfy specific friction or positioning requirements. Custom diameters, sizes, and bore dimensions are available to fit equipment requirements. The item is compatible with conventional roller systems in markets like glass production, automobile, and electronic devices.
Electrical insulation homes stop current leak in high-voltage settings. Chemical inertness allows usage in corrosive settings without degradation. It stands up to acids, alkalis, and molten metals, making it ideal for chemical processing or semiconductor manufacturing.
Load-bearing ability gets to 500 MPa, supporting durable operations. Precision design guarantees uniform wall thickness and concentricity for smooth turning. This minimizes resonance and sound in high-speed equipment.
The manufacturing process uses innovative sintering strategies to remove inner defects. Quality control includes X-ray evaluation and dimensional accuracy checks. Each unit satisfies ISO 9001 standards for uniformity.
Applications consist of conveyor systems, kiln rollers, and precision bearings. It replaces standard steel or alumina rollers in scenarios requiring higher heat resistance or lower maintenance. Reduced downtime and longer substitute intervals lower operational expenses.
Customization encompasses emerge layers or grooved styles for specialized dealing with tasks. Technical assistance is offered for combination into existing systems. The item ships with protective packaging to prevent transit damage.
Performance advantages include power effectiveness from minimized friction and warmth dissipation. Minimal lubrication needs straighten with environment-friendly industrial techniques. Compatibility with automated systems supports modern production lines.
(Advanced Custom Made Manufactory Silicon Nitride Si3N4 Ceramic Roller Wheel Tube)
Applications of Advanced Custom Made Manufactory Silicon Nitride Si3N4 Ceramic Roller Wheel Tube
Advanced personalized silicon nitride (Si3N4) ceramic roller wheels and tubes are crucial components in high-performance industrial applications. These products master severe conditions since silicon nitride supplies outstanding strength, thermal resistance, and rust resistance. Industries rely upon them for precision, toughness, and effectiveness.
In steel manufacturing, silicon nitride rollers take care of high-temperature rolling procedures. Conventional steel rollers degrade under warm and anxiety. Silicon nitride rollers keep stability at temperature levels exceeding 1000 ° C. This decreases downtime for replacements and improves production consistency. The product’s reduced thermal expansion protects against warping, making sure consistent item high quality.
Glass manufacturing advantages similarly. Molten glass handling needs materials immune to thermal shock. Silicon nitride rollers withstand rapid temperature adjustments without breaking. Their smooth surface area reduces rubbing, stopping flaws in glass sheets or fibers. This results in higher yields and reduced waste.
Automotive and aerospace sectors utilize these ceramics for precision grinding and machining. Silicon nitride’s solidity and wear resistance make it excellent for grinding wheels. Components like wind turbine blades or engine parts need tight tolerances. Ceramic rollers guarantee accurate shaping and finishing, prolonging tool life and lowering upkeep expenses.
Electronic devices producing relies upon silicon nitride tubes for semiconductor handling. The product’s electrical insulation and pureness prevent contamination in cleanroom atmospheres. High-speed handling of silicon wafers or motherboard needs elements that resist static buildup and chemical direct exposure. Personalized ceramic tubes satisfy these demands while making sure long-lasting integrity.
Mining and heavy machinery applications make use of ceramic rollers for conveyor systems. Unpleasant products and rough environments put on down metal parts rapidly. Silicon nitride’s toughness and resistance to abrasion minimize substitute regularity. This lowers functional prices and improves safety and security by minimizing devices failing threats.
Custom production enables customizing measurements, finishes, and structural attributes to details needs. Whether boosting warmth dissipation or optimizing load ability, silicon nitride parts adapt to one-of-a-kind difficulties. Their light-weight nature contrasted to metals likewise decreases energy intake in turning systems.
Industries adopting innovative silicon nitride ceramic rollers and tubes see quantifiable improvements in efficiency and cost efficiency. The material’s distinct buildings deal with limitations of traditional steels and polymers, making it a favored selection for mission-critical applications.
Company Introduction
Advanced Ceramics founded on October 17, 2014, is a high-tech enterprise committed to the research and development, production, processing, sales and technical services of ceramic relative materials and products.. Since its establishment in 2014, the company has been committed to providing customers with the best products and services, and has become a leader in the industry through continuous technological innovation and strict quality management.
Our products includes but not limited to Silicon carbide ceramic products, Boron Carbide Ceramic Products, Boron Nitride Ceramic Products, Silicon Carbide Ceramic Products, Silicon Nitride Ceramic Products, Zirconium Dioxide Ceramic Products, Quartz Products, etc. Please feel free to contact us.(nanotrun@yahoo.com)
Payment Methods
T/T, Western Union, Paypal, Credit Card etc.
Shipment Methods
By air, by sea, by express, as customers request.
5 FAQs of Advanced Custom Made Manufactory Silicon Nitride Si3N4 Ceramic Roller Wheel Tube
Silicon nitride (Si3N4) ceramic roller wheels and tubes are used in high-temperature industrial applications. These parts handle extreme heat, wear, and corrosion. Below are common questions about custom-made Si3N4 ceramic rollers.
What makes silicon nitride ceramic suitable for roller wheels? Silicon nitride resists heat up to 1200°C. It survives rapid temperature changes without cracking. The material is harder than steel. It lasts longer in abrasive environments. This reduces downtime for replacements.
Where are Si3N4 ceramic rollers typically used? These rollers are common in metal processing. They work in furnaces, forging lines, and welding systems. They transport molten metal or hot glass. Electronics manufacturing uses them for precision handling. High-temperature kilns in ceramics production rely on them too.
How do Si3N4 rollers compare to alumina or steel rollers? Silicon nitride outperforms alumina in toughness. It handles impact better. Steel rollers warp under high heat. Si3N4 keeps its shape. It requires less lubrication. Maintenance costs drop.
Can these rollers be customized for specific machines? Yes. Manufacturers adjust dimensions, surface finish, and load capacity. Tolerances match exact machine specs. Grooves, flanges, or coatings are added. Custom sizes prevent compatibility issues.
How should Si3N4 rollers be handled during installation? Avoid sharp impacts. Use soft tools to prevent surface chips. Check alignment before securing. Uneven stress causes cracks. Clean surfaces regularly. Inspect for wear every 500 operating hours. Replace rollers if surface pitting or diameter loss exceeds 2%.
(Advanced Custom Made Manufactory Silicon Nitride Si3N4 Ceramic Roller Wheel Tube)
REQUEST A QUOTE
RELATED PRODUCTS
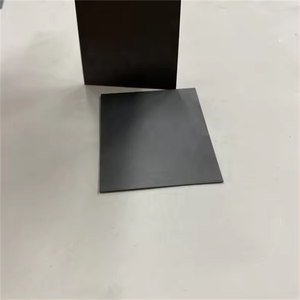
Advanced Ceramics Custom Silicon Nitride Ceramics Si3N4 Ceramic Part
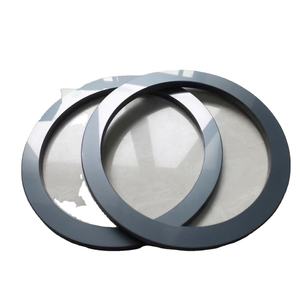
Industrial Square Silicon Nitride Ceramic Block Plate Si3N4 Sheet
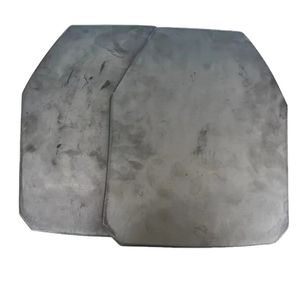
Customized Pressure-Resistant Black Silicon Nitride Ceramic Ring
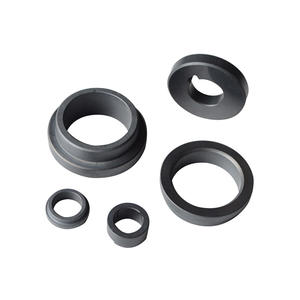
Zirconia and Silicon Nitride Ceramic Bearing 608 688 R188 6202
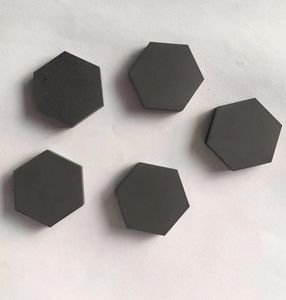
Customized Fine Polished G5 Silicon Nitride Si3N4 Ceramic Grinding Ball
