Discover Premium Ceramic Products | Durability & Elegance United | Advanced Ceramics
PRODUCT PARAMETERS
Description
Overview of Silicon Carbide Ceramics
Silicon Carbide (SiC) ceramics are renowned for their outstanding mechanical properties, including high hardness, strength at elevated temperatures, and excellent thermal shock resistance. These materials are pivotal in cutting-edge industrial applications, from abrasives to aerospace components, due to their unique combination of properties.
Features of Silicon Carbide Ceramics
High Hardness: Exceptional wear resistance.
Thermal Shock Resistance: Can withstand rapid temperature changes.
Chemical Stability: Resistant to most chemicals.
High Thermal Conductivity: Efficient heat dissipation.
Low Density: Lightweight for its strength.
(Precision High Strength Industrial Ceramic SIC Silicon Carbide Ceramic Plate Sheet Substrate Plate)
Specification of Precision High Strength Industrial Ceramic SIC Silicon Carbide Ceramic Plate Sheet Substrate Plate
The Accuracy High Toughness Industrial Ceramic SIC Silicon Carbide Ceramic Plate Sheet Substrate Plate is crafted for demanding commercial atmospheres. It makes use of silicon carbide (SiC) as the base product. This ceramic plate provides phenomenal toughness. It withstands severe temperature levels, corrosion, and mechanical stress and anxiety. The material purity surpasses 99.5%. This guarantees regular performance in important applications.
The plate includes high hardness. It measures 9.5 on the Mohs range. This makes it resistant to abrasion and wear. The density varies between 3.1 to 3.2 g/cm FOUR. This contributes to its architectural security. The thermal conductivity is 120 W/m · K. It effectively dissipates heat in high-temperature settings. The optimum operating temperature gets to 1650 ° C. It keeps honesty under prolonged heat exposure.
Thermal shock resistance is a crucial benefit. It withstands splitting throughout rapid temperature shifts. The reduced thermal expansion coefficient lessens dimensional adjustments. This is crucial for precision elements. Home plate stands up to chemical attack. It performs well in acidic, alkaline, and harsh atmospheres.
Requirement thickness alternatives consist of 1mm to 50mm. Personalized sizes are available. Common dimensions are 100mm x 100mm to 600mm x 600mm. Surface coatings differ. Choices include brightened, ground, or as-fired surface areas. Tolerances are firmly managed. They fulfill +/- 0.5% for thickness and +/- 1mm for size and size.
Applications cover several markets. Semiconductor manufacturing uses it for wafer processing. Aerospace relies on it for engine parts. Metallurgy utilizes it in heating system cellular linings. Chemical processing uses it for activator parts. It also offers in laser systems, wear-resistant equipment, and high-voltage insulation.
Modification is feasible. Machining solutions readjust openings, grooves, or sides. Examining protocols include density checks, firmness tests, and thermal property analysis. Quality control follows ISO standards. Each batch undertakes extensive examination.
This ceramic plate integrates strength, thermal durability, and chemical stability. It replaces standard metals in rough conditions. The item suits engineers requiring dependable performance. It decreases downtime and maintenance prices. Technical assistance is offered for material option and design optimization.
(Precision High Strength Industrial Ceramic SIC Silicon Carbide Ceramic Plate Sheet Substrate Plate)
Applications of Precision High Strength Industrial Ceramic SIC Silicon Carbide Ceramic Plate Sheet Substrate Plate
Accuracy high-strength commercial ceramic SIC silicon carbide ceramic plate sheet substrate plates serve critical functions across several sectors. These plates take care of extreme settings as a result of their unique homes like high thermal conductivity, extraordinary wear resistance, and chemical security. Semiconductor making depends on them for wafer processing devices. Their capability to stand up to heats and harsh gases makes them ideal for engraving and deposition chambers. They make sure marginal contamination, improving manufacturing performance and item top quality. In the aerospace field, these plates operate as safety elements in turbine engines and heat shields. Their light-weight nature and resistance to thermal shock enhance performance in high-speed, high-temperature problems. Automotive systems make use of silicon carbide plates in braking systems and hybrid vehicle power modules. The product’s durability lowers wear, expanding component lifespan under rubbing and warm. Power production take advantage of their application in solar panel production and nuclear reactor elements. They tolerate intense radiation and thermal tension, ensuring dependable operation in rough setups. Chemical processing plants make use of these plates for lining activators and pumps. Their resistance to acids and alkalis prevents corrosion, keeping equipment stability over time. Clinical tool suppliers employ silicon carbide substrates for sophisticated imaging and medical tools. The material’s biocompatibility and electrical insulation buildings fulfill strict safety standards. Electronic devices sectors incorporate these plates into heat sinks and circuit substrates. Efficient heat dissipation shields sensitive components from overheating. Mining and metallurgy operations make use of ceramic plates in wear-resistant cellular linings and reducing tools. Their hardness outperforms traditional metals, lowering downtime from constant replacements. Adjustable shapes and sizes enable customized remedies for specialized equipment. Advanced sintering strategies ensure constant density and surface coating, meeting accuracy design demands. Cost-effectiveness develops from reduced upkeep demands and prolonged service periods. Environmental resilience settings silicon carbide ceramics as a sustainable choice for high-performance applications.
Company Introduction
Advanced Ceramics founded on October 17, 2014, is a high-tech enterprise committed to the research and development, production, processing, sales and technical services of ceramic relative materials and products.. Since its establishment in 2014, the company has been committed to providing customers with the best products and services, and has become a leader in the industry through continuous technological innovation and strict quality management.
Our products includes but not limited to Silicon carbide ceramic products, Boron Carbide Ceramic Products, Boron Nitride Ceramic Products, Silicon Carbide Ceramic Products, Silicon Nitride Ceramic Products, Zirconium Dioxide Ceramic Products, Quartz Products, etc. Please feel free to contact us.(nanotrun@yahoo.com)
Payment Methods
T/T, Western Union, Paypal, Credit Card etc.
Shipment Methods
By air, by sea, by express, as customers request.
5 FAQs of Precision High Strength Industrial Ceramic SIC Silicon Carbide Ceramic Plate Sheet Substrate Plate
What is a silicon carbide ceramic plate?
Silicon carbide (SiC) ceramic plates are industrial components made from a compound of silicon and carbon. They are known for high hardness, thermal stability, and resistance to wear. These plates handle extreme temperatures and harsh environments better than metals or plastics. They are used in applications needing durability and precision.
How heat-resistant are SiC ceramic plates?
SiC ceramic plates withstand temperatures up to 1650°C (3000°F) in oxidizing environments. They maintain strength and shape under rapid temperature changes. This makes them ideal for furnaces, aerospace parts, and high-heat machinery. Their low thermal expansion reduces cracking risks.
Why choose SiC plates over metal or plastic?
SiC plates last longer in abrasive or corrosive settings. They resist chemical reactions better than metals. Their lightweight nature reduces energy use in moving parts. They do not deform under pressure like plastics. They also conduct heat efficiently, improving performance in thermal applications.
Where are SiC ceramic plates commonly used?
These plates are used in semiconductor manufacturing for wafer handling. They serve as armor in military gear due to their bulletproof qualities. Industrial kilns use them as shelves or liners. They are found in pump seals, cutting tools, and high-temperature sensors. Their versatility suits industries needing reliability under stress.
Can SiC plates be customized for specific needs?
Yes. Manufacturers adjust size, thickness, and surface finish to meet requirements. Holes, grooves, or coatings are added for specialized functions. Custom shapes fit unique machinery or experimental setups. Technical specs like purity levels or porosity are tailored for performance. Orders typically require detailed specifications to ensure compatibility.
(Precision High Strength Industrial Ceramic SIC Silicon Carbide Ceramic Plate Sheet Substrate Plate)
REQUEST A QUOTE
RELATED PRODUCTS
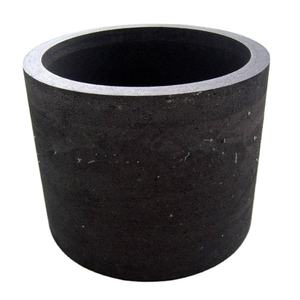
Silicon Carbide Saggar Ceramic Product Premium Ceramics Item
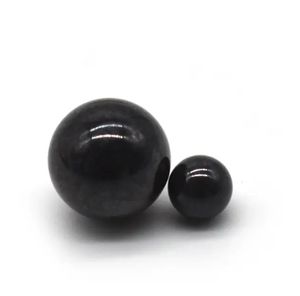
High Temperature Sic Pipe Roller Rod Heat Resistant Refractory Kiln Furniture Ceramic Silica Silicon Carbide Tube
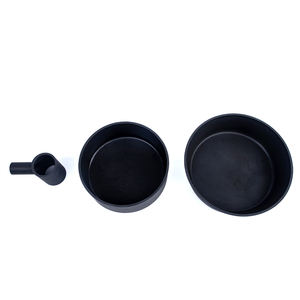
Factory Refractory Silicon Carbide Ceramic Products Sic Silicon Carbide Refractory Tube for Kiln Furniture,
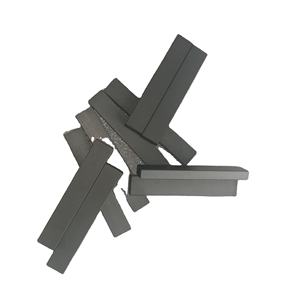
1kg/40pcs Silicon Carbide Ceramic Plate, Ceramic Plate, Bulletproof Plate, Customized Precision and High-temperature Resistance
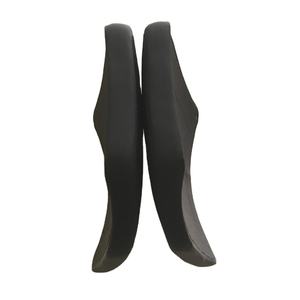
Alumina/Silicon Carbide/Zirconia Ceramic Foam Ceramic Plate
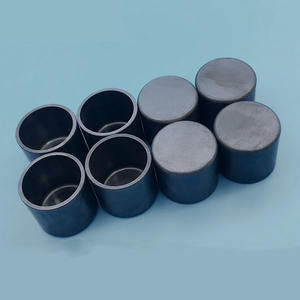