Discover Premium Ceramic Products | Durability & Elegance United | Advanced Ceramics
PRODUCT PARAMETERS
Description
Introduction to Alumina Ceramics
Alumina ceramics are known for their high hardness, wear resistance, corrosion resistance, good electrical insulation and high temperature stability. According to the different alumina content, it can be divided into different grades, such as 95 porcelain, 99 porcelain, etc., among which 99 porcelain refers to ceramic materials with an alumina content of 99%. As the alumina content increases, its mechanical strength and electrical insulation properties will also increase accordingly.
Characteristics of Alumina Ceramics
High Hardness: Alumina ceramics have extremely high hardness, which makes it very wear-resistant and suitable for manufacturing abrasive tools and parts that require wear resistance.
Wear resistance: Due to its high hardness, alumina ceramics show excellent wear resistance and are suitable for manufacturing parts for long-term use.
Corrosion resistance: Alumina ceramics have good resistance to most acids and alkalis, making them widely used in the chemical industry.
Good electrical insulation: As an excellent electrical insulating material, alumina ceramics are widely used in electronic and electrical products.
High temperature stability: Ability to withstand extremely high temperatures without significant physical or chemical changes, which makes it an ideal choice for applications in high temperature environments.
Biocompatibility: In the medical field, certain grades of alumina ceramics are used to make medical devices such as artificial joints due to their good biocompatibility.
(Alumina Ceramic Wafer Excellent Electrical Al2O3 Insulation Disc Aluminum Oxide Disc)
Specifications of Alumina Ceramic Wafer Excellent Electrical Al2O3 Insulation Disc Aluminum Oxide Disc
Alumina Porcelain Wafers supply reputable electrical insulation and high-performance options for industrial and technical applications. Made largely from aluminum oxide (Al2O3), these discs provide excellent thermal stability and mechanical sturdiness. The material make-up guarantees solid resistance to wear, rust, and severe temperature levels.
These discs excel in electrical insulation due to light weight aluminum oxide’s non-conductive residential or commercial properties. They stop current leak in high-voltage settings. The high dielectric toughness makes them suitable for circuits, sensing units, and digital parts. Thermal conductivity stays low, lowering warm transfer dangers in sensitive gadgets.
Alumina ceramic wafers handle harsh problems. They run successfully in temperatures as much as 1600 ° C without weakening. Their solidity competitors steels, making certain very little surface area damage under stress. Chemical resistance safeguards against acids, antacid, and solvents. This expands their lifespan in corrosive settings.
Applications extend electronics, aerospace, automotive, and power markets. They work as protecting substratums in power electronics, circuit boards, and semiconductor tools. Industrial equipment uses them for wear-resistant parts and thermal obstacles. Clinical devices gain from their biocompatibility and accuracy.
Customized dimensions and thicknesses are offered. Standard sizes range from 5mm to 200mm. Thickness choices vary between 0.5 mm and 15mm. Surface area surfaces consist of polished, washed, or as-sintered to fulfill particular requirements.
Key specs consist of Al2O3 material at 96% or 99.5% purity. Thickness actions around 3.8 g/cm SIX. Flexural stamina exceeds 300 MPa. Thermal conductivity stays listed below 30 W/m · K. Dielectric toughness gets to 15 kV/mm. Maximum working temperature is 1600 ° C.
These discs are compatible with standard machining processes. Boring, reducing, and shaping can be done without compromising structural stability. Tight tolerances ensure precise integration right into complex systems.
Alumina ceramic wafers fulfill market criteria for reliability. They are checked for electrical, thermal, and mechanical performance. Quality assurance makes sure uniformity across batches. Packaging options consist of anti-static products to prevent contamination.
Customized services are readily available for specialized requirements. Product qualities, dimensions, and surface area treatments can be changed. Technical support aids with design and application challenges. Mass orders decrease prices for large jobs.
(Alumina Ceramic Wafer Excellent Electrical Al2O3 Insulation Disc Aluminum Oxide Disc)
Applications of Alumina Ceramic Wafer Excellent Electrical Al2O3 Insulation Disc Aluminum Oxide Disc
Alumina Porcelain Wafer (Al2O3) is a high-performance product known for outstanding electrical insulation and durability. It handles extreme temperature levels and harsh atmospheres. Industries depend on it for trustworthy performance popular applications.
In electronic devices, Alumina Ceramic Wafers work as insulating layers in motherboard. They obstruct electric leak successfully. High thermal conductivity assists dissipate warm in components like power transistors and LED components. This stabilizes digital systems and stops getting too hot. Silicon chips and capacitors frequently use these wafers for constant efficiency.
Industrial setups benefit from the product’s wear and chemical resistance. Alumina discs line parts revealed to corrosive chemicals in pumps and shutoffs. They stand up to mechanical tension in high-pressure systems. High-temperature heaters use them as safety layers or substrates. This makes sure equipment operates securely in challenging problems.
Clinical equipment manufacturers choose Alumina Porcelain for its biocompatibility. It is safe for use in surgical devices and dental implants. Electric insulation is important in devices like MRI machines and imaging systems. The product’s accuracy makes certain integrity in life-saving applications. Prosthetics and analysis devices additionally use its secure properties.
Aerospace and defense markets depend on Alumina Ceramic for extreme conditions. It survives extreme warmth and mechanical tension in engine sensing units and satellite components. Communication systems and radar technology utilize these discs for signal stability. The product’s lightweight nature and toughness make it ideal for air-borne and area applications.
Alumina Porcelain Wafers adapt to varied demands across fields. Their electrical insulation, thermal management, and chemical resistance address modern industrial obstacles. From customer electronics to advanced aerospace systems, these discs supply remedies where efficiency and reliability are non-negotiable.
Company Introduction
Advanced Ceramics founded on October 17, 2014, is a high-tech enterprise committed to the research and development, production, processing, sales and technical services of ceramic relative materials and products.. Since its establishment in 2014, the company has been committed to providing customers with the best products and services, and has become a leader in the industry through continuous technological innovation and strict quality management.
Our products includes but not limited to Silicon carbide ceramic products, Boron Carbide Ceramic Products, Boron Nitride Ceramic Products, Silicon Carbide Ceramic Products, Silicon Nitride Ceramic Products, Zirconium Dioxide Ceramic Products, Quartz Products, etc. Please feel free to contact us.(nanotrun@yahoo.com)
Payment Methods
T/T, Western Union, Paypal, Credit Card etc.
Shipment Methods
By air, by sea, by express, as customers request.
5 FAQs of Alumina Ceramic Wafer Excellent Electrical Al2O3 Insulation Disc Aluminum Oxide Disc
What is an alumina ceramic wafer? Alumina ceramic wafers are thin, flat discs made from aluminum oxide (Al2O3). They provide strong electrical insulation. These wafers handle high temperatures. They resist wear and chemicals. Industries use them in electronics and machinery.
Why choose alumina ceramic for electrical insulation? Aluminum oxide has high dielectric strength. It stops electricity from passing through. This makes it safe for circuits and high-voltage parts. It works in extreme heat. Other materials might melt or fail. Alumina stays stable.
Where are alumina ceramic wafers commonly used? These discs appear in electronics like circuit boards and sensors. They shield parts from heat and electricity. Factories use them in heaters or lasers. Labs use them for testing equipment. They fit anywhere needing insulation and durability.
Do alumina wafers break easily? They are hard but can crack under strong force. Handle them carefully. Avoid dropping or hitting them. They handle daily wear well. Proper installation prevents damage. Their strength depends on thickness and quality.
Can alumina discs be customized? Yes. Sizes and shapes vary. Common forms are circles or squares. Holes or grooves can be added. Thickness ranges from under 1mm to several millimeters. Custom orders match specific needs. Manufacturers adjust based on use.
How do alumina wafers compare to plastic insulators? Alumina beats plastic in heat resistance. Plastics melt or deform. Alumina stays intact. It lasts longer under stress. Plastic costs less but suits low-heat jobs. Alumina is better for tough conditions.
(Alumina Ceramic Wafer Excellent Electrical Al2O3 Insulation Disc Aluminum Oxide Disc)
REQUEST A QUOTE
RELATED PRODUCTS
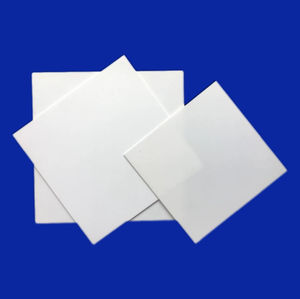
High Quality Alumina Ceramic Al2o3 Plate
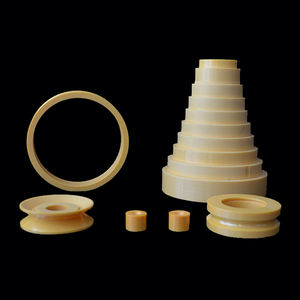
Wear-resistant Alumina Ceramic Plate for Mechanical Seals, Anti-wear, OEM Customized Production
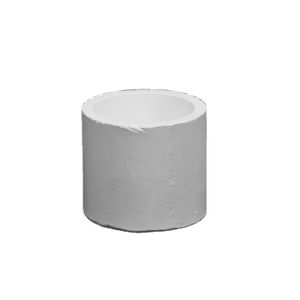
Customized 99% 95% Alumina Textile Ceramics
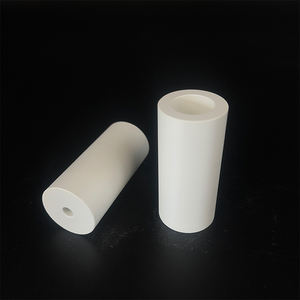
95 Polishing Al2o3 Alumina Ceramic Machined Ceramic Special Part
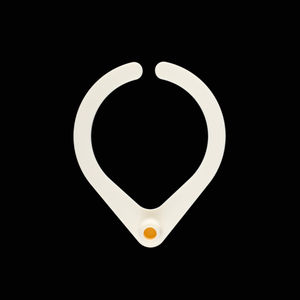
96 Alumina Ceramic Substrate
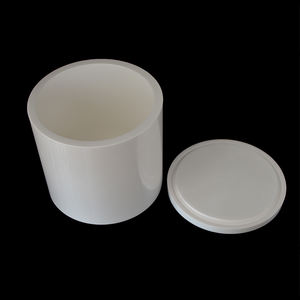