Discover Premium Ceramic Products | Durability & Elegance United | Advanced Ceramics
PRODUCT PARAMETERS
Description
Overview of aluminum nitride ceramics
Aluminum Nitride Ceramic is an advanced ceramic material with aluminum nitride as the main component. It has been widely used in electronics, optics, and mechanics due to its unique properties.
Features of aluminum nitride ceramics
High thermal conductivity: Aluminum nitride ceramics have relatively high thermal conductivity, usually between 170-260 W/m·K, which makes it an excellent heat dissipation material. It is especially suitable for electronic devices that require efficient heat dissipation, such as substrate materials for power semiconductor devices.
Good electrical insulation: Despite its high thermal conductivity, aluminum nitride ceramics are excellent insulators of electricity, which can effectively prevent current leakage and ensure the safe operation of electronic components.
Low dielectric constant and dielectric loss: These characteristics make aluminum nitride ceramics very suitable for use in high-frequency circuits because it can reduce energy loss during signal transmission.
High temperature resistance: Aluminum nitride ceramics can maintain structural stability and strength at extremely high temperatures. Its melting point is about 2800°C, so it is suitable for applications in high temperature environments.
Low thermal expansion coefficient: Compared with semiconductor materials such as silicon, aluminum nitride has a lower thermal expansion coefficient, which means it has better dimensional stability when the temperature changes, which helps improve packaging reliability.
Corrosion resistance: Aluminum nitride ceramics have good chemical stability to most molten metals and are not easily oxidized or corroded, allowing them to perform well in harsh environments.
High mechanical strength: Although not as hard as some other types of ceramic materials, aluminum nitride ceramics still provide enough mechanical strength to allow them to be used in many structural applications.
(Aluminum Nitride (AlN) Ceramic Plate Direct-Bonded Copper (Al2O3) Alumina Electrical Ceramic Substrate)
Specifications of Aluminum Nitride (AlN) Ceramic Plate Direct-Bonded Copper (Al2O3) Alumina Electrical Ceramic Substrate
The Light Weight Aluminum Nitride (AlN) Ceramic Plate Direct-Bonded Copper (DBC) and Alumina (Al2O3) Electrical Ceramic Substratum are advanced products designed for high-performance electronic applications. Both substrates integrate ceramic layers with bonded copper to attain premium thermal management and electric insulation. Light weight aluminum Nitride provides phenomenal thermal conductivity, reaching 170-220 W/mK. Alumina gives reliable electrical insulation with a thermal conductivity of 24-28 W/mK. These residential properties make them suitable for power electronic devices, LED systems, and high-frequency tools.
The AlN and Al2O3 substratums feature a direct-bonded copper framework. A pure copper layer bonds to the ceramic surface via high-temperature oxidation. This procedure produces a strong mechanical link without adhesives. The copper layer density varies from 0.1 mm to 0.6 mm. The ceramic layer density varies between 0.25 mm and 2.0 mm. Individuals select dimensions based on voltage demands and warmth dissipation needs.
Light weight aluminum Nitride excels in high-power applications. Its reduced thermal development coefficient (4.5 ppm/K) matches silicon chips. This lowers stress and anxiety throughout temperature modifications. Alumina substrates are cost-efficient for typical applications. They maintain stable performance under voltages approximately 25 kV/mm. Both materials operate in temperatures from -50 ° C to +850 ° C. They withstand thermal shock and chemical deterioration.
Surface area roughness is critical for component accessory. AlN substratums generally show a surface coating of ≤ 0.4 μm Ra. Alumina substrates achieve ≤ 0.6 μm Ra. Smooth surface areas ensure reliable soldering and wire bonding. The copper layers are pre-oxidized for better attachment. Custom-made forms and opening patterns are offered for circuit design versatility.
Applications consist of power components, motor drives, and RF amplifiers. The substratums transfer warmth efficiently from semiconductors. This avoids getting too hot in compact devices. Automotive systems utilize them for electrical vehicle inverters. Renewable energy systems depend on their durability in rough atmospheres.
Light Weight Aluminum Nitride and Alumina substratums meet market criteria for dependability. They undertake rigorous testing for thermal biking and electrical breakdown. Dampness resistance and insulation stability make certain long-term performance. These materials support miniaturization trends in electronic devices. They stabilize high thermal transfer with electric security.
The copper-ceramic bond stays intact under mechanical stress and anxiety. This protects against delamination during procedure. Producers optimize layer thickness for certain power thickness. Adjustable designs accommodate complicated circuit layouts. These substrates are essential for advancing high-efficiency digital systems.
(Aluminum Nitride (AlN) Ceramic Plate Direct-Bonded Copper (Al2O3) Alumina Electrical Ceramic Substrate)
Applications of Aluminum Nitride (AlN) Ceramic Plate Direct-Bonded Copper (Al2O3) Alumina Electrical Ceramic Substrate
Aluminum Nitride (AlN) ceramic plates and Direct-Bonded Copper (DBC) alumina (Al2O3) ceramic substrates offer crucial duties in innovative electronics. These products incorporate high thermal conductivity with solid electric insulation. They handle severe temperatures and power degrees successfully. AlN ceramic plates excel in high-power applications. Their thermal conductivity goes beyond alumina. This makes them excellent for tools requiring efficient heat dissipation. Instances include LED lighting, power semiconductors, and radio-frequency elements. Alumina substrates use affordable solutions for less demanding atmospheres. They give dependable efficiency in standard digital circuits. Both products bond flawlessly with copper layers via the DBC process. This creates robust electric connections while managing warmth.
In the electronic devices industry, these substrates power high-frequency communication systems. They support 5G framework and radar technology. Their low signal loss makes sure secure efficiency. Automotive applications depend on them for electrical car power components. Harsh conditions under the hood demand products immune to thermal stress and anxiety. AlN and alumina substratums fulfill these demands. They improve battery management systems and onboard battery chargers.
Aerospace systems use these porcelains for their dependability in extreme atmospheres. Satellite parts and avionics benefit from their lightweight yet durable framework. Industrial devices incorporates them right into high-voltage insulators and laser diodes. Their capability to hold up against rapid temperature level adjustments stops system failings.
LED manufacturing relies on AlN and alumina substratums for warmth administration. High-brightness LEDs produce significant warm. Effective dissipation extends their life-span. Power electronics like IGBTs and MOSFETs use these porcelains to keep security under hefty loads.
Clinical gadgets utilize AlN substratums for imaging systems and surgical tools. Their electrical insulation makes sure client safety. Alumina substratums appear in consumer electronic devices for sensors and circuit card. Their affordability equilibriums performance requires.
Renewable resource systems utilize these materials in solar inverters and wind turbine converters. They manage high voltages and temperatures accurately. The DBC process enhances the bond in between copper and ceramic. This protects against delamination during procedure.
AlN and alumina substratums adjust to varied industrial needs. Their distinct homes attend to challenges in warmth administration and electric efficiency. Selecting between them depends upon thermal demands and spending plan constraints. AlN matches high-performance applications. Alumina offers functional services for day-to-day use. Both products proceed advancing modern-day technology throughout sectors.
Company Introduction
Advanced Ceramics founded on October 17, 2014, is a high-tech enterprise committed to the research and development, production, processing, sales and technical services of ceramic relative materials and products.. Since its establishment in 2014, the company has been committed to providing customers with the best products and services, and has become a leader in the industry through continuous technological innovation and strict quality management.
Our products includes but not limited to Silicon carbide ceramic products, Boron Carbide Ceramic Products, Boron Nitride Ceramic Products, Silicon Carbide Ceramic Products, Silicon Nitride Ceramic Products, Zirconium Dioxide Ceramic Products, Quartz Products, etc. Please feel free to contact us.(nanotrun@yahoo.com)
Payment Methods
T/T, Western Union, Paypal, Credit Card etc.
Shipment Methods
By air, by sea, by express, as customers request.
5 FAQs of Aluminum Nitride (AlN) Ceramic Plate Direct-Bonded Copper (Al2O3) Alumina Electrical Ceramic Substrate
1. What is an Aluminum Nitride Ceramic Plate Direct-Bonded Copper used for? It is used in high-power electronics. It helps move heat away from devices like LED lights, radio-frequency systems, and power modules. The copper layer allows electrical connections. The ceramic layer insulates and manages heat. This combination improves performance in demanding applications.
2. Why pick Aluminum Nitride over Alumina for the ceramic layer? Aluminum Nitride moves heat better than Alumina. Aluminum Nitride conducts heat 10 times faster. This makes it ideal for devices needing fast cooling. Alumina works for less demanding uses. Aluminum Nitride costs more but handles high heat better.
3. How is the copper bonded to the ceramic plate? The copper is melted onto the ceramic at high temperatures. This creates a strong bond without glue. The process ensures good heat transfer. The bond stays stable even under thermal stress. This method avoids gaps between materials.
4. What makes Aluminum Nitride Ceramic good for thermal management? It has high thermal conductivity. It matches silicon’s thermal expansion. This reduces stress when used with silicon chips. It resists electricity and heat damage. These traits prevent overheating in circuits.
5. Are there handling issues with these substrates? Avoid dropping or bending them. They are hard but can crack under force. Clean surfaces before assembly. Dust or oil weakens the bond. Store them dry to prevent moisture damage. Follow manufacturer guidelines for installation.
(Aluminum Nitride (AlN) Ceramic Plate Direct-Bonded Copper (Al2O3) Alumina Electrical Ceramic Substrate)
REQUEST A QUOTE
RELATED PRODUCTS
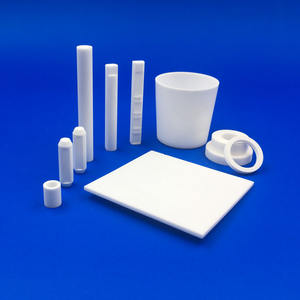
CNC Machining Aluminum Nitride Aln Ceramic Square Crucible Ring/Substrate/Parts
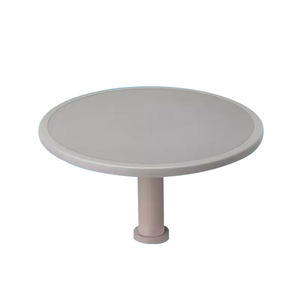
High Precision AlN Bar Aluminum Nitride Ceramic Rod
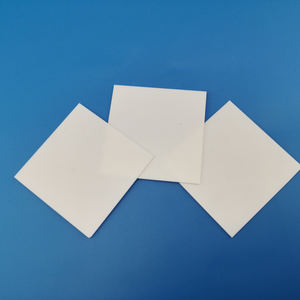
AlN Heating Element Aluminum Nitride Ceramic Heater for Semiconductor Instrument
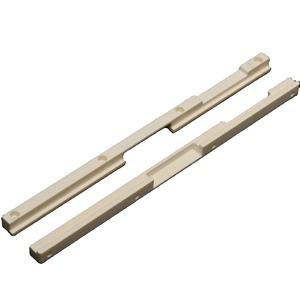
SINTYRON High Thermal Conductivity ALN Aluminium Nitride Ceramic Insulating Tube
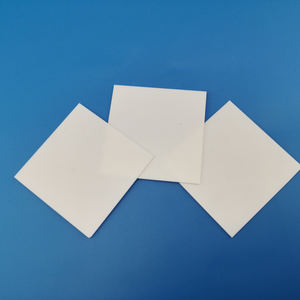
Industry Electrical CNC Machining Ceramic Parts Aluminum Nitride Ceramic ALN Heat Sink for CPU LED
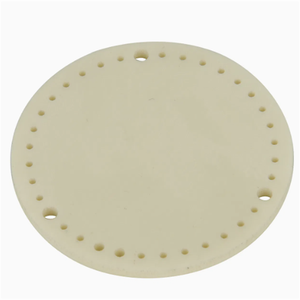