Discover Premium Ceramic Products | Durability & Elegance United | Advanced Ceramics
PRODUCT PARAMETERS
Description
Introduction to Alumina Ceramics
Alumina ceramics are known for their high hardness, wear resistance, corrosion resistance, good electrical insulation and high temperature stability. According to the different alumina content, it can be divided into different grades, such as 95 porcelain, 99 porcelain, etc., among which 99 porcelain refers to ceramic materials with an alumina content of 99%. As the alumina content increases, its mechanical strength and electrical insulation properties will also increase accordingly.
Characteristics of Alumina Ceramics
High Hardness: Alumina ceramics have extremely high hardness, which makes it very wear-resistant and suitable for manufacturing abrasive tools and parts that require wear resistance.
Wear resistance: Due to its high hardness, alumina ceramics show excellent wear resistance and are suitable for manufacturing parts for long-term use.
Corrosion resistance: Alumina ceramics have good resistance to most acids and alkalis, making them widely used in the chemical industry.
Good electrical insulation: As an excellent electrical insulating material, alumina ceramics are widely used in electronic and electrical products.
High temperature stability: Ability to withstand extremely high temperatures without significant physical or chemical changes, which makes it an ideal choice for applications in high temperature environments.
Biocompatibility: In the medical field, certain grades of alumina ceramics are used to make medical devices such as artificial joints due to their good biocompatibility.
(92% 95% Alumina Ceramic Wear Lining Bricks/Ceramic Liners for Ball Mill)
Specifications of 92% 95% Alumina Ceramic Wear Lining Bricks/Ceramic Liners for Ball Mill
Alumina ceramic wear lining blocks are made for ball mills and various other industrial devices. These liners protect machinery from deterioration. They prolong service life. The material has 92% or 95% alumina content. High alumina degrees boost hardness and resilience. These blocks stand up to abrasion efficiently. They manage severe problems in mining, concrete, and chemical sectors.
The 92% alumina ceramic liners have a thickness of 3.6 g/cm TWO. The 95% version gets to 3.7 g/cm ³. Higher density means better resistance to impact. Both kinds provide solid compressive toughness. The 92% quality surpasses 850 MPa. The 95% quality goes beyond 900 MPa. This guarantees stability under hefty loads. Surface area level of smoothness minimizes rubbing during procedure. Energy consumption stays reduced.
Alumina liners endure high temperatures. They operate in settings up to 1600 ° C. Thermal shock resistance prevents fracturing during fast temperature level changes. Chemical security avoids rust from acids or antacid. These properties make them ideal for hostile products.
Installation is simple. The bricks can be found in standard dimensions like 50x50x20 mm. Custom forms are available. They fit rounded or level surfaces. Interlacing layouts produce smooth protection. Spaces in between bricks are reduced. Product leakage is decreased.
These liners reduced maintenance prices. Replacement regularity drops. Downtime lowers. Manufacturing effectiveness enhances. They are cost-efficient contrasted to steel options. Metal liners rust and use quicker. Ceramic alternatives last 5-10 times much longer.
Applications include sphere mill grinding chambers, hoppers, chutes, and pipes. They protect equipment from unpleasant products like ores, coal, and concrete clinker. Custom services match details machinery demands. Technical support guarantees proper choice and setup.
The alumina ceramic linings are delivered firmly. Product packaging stops breakage. Distribution times differ by order size. Samples are offered for testing. Performance information helps consumers verify suitability.
(92% 95% Alumina Ceramic Wear Lining Bricks/Ceramic Liners for Ball Mill)
Applications of 92% 95% Alumina Ceramic Wear Lining Bricks/Ceramic Liners for Ball Mill
Alumina ceramic wear lining bricks, also called ceramic liners, are extensively utilized in ball mills. These linings safeguard the mill’s inner surface areas from wear caused by grinding media and raw materials. The 92% and 95% alumina content variations are preferred for their equilibrium of efficiency and price.
The high alumina material provides these ceramics superb hardness. They resist abrasion much better than steel or rubber linings. This lowers downtime for upkeep. Their corrosion resistance matches severe settings like mining or chemical handling. Thermal security enables them to handle high temperatures without splitting.
In mining, ceramic liners expand the life-span of ball mills grinding ores. Concrete plants utilize them to process clinker and raw materials. Power generation facilities apply these linings in coal pulverizers. The smooth surface of alumina porcelains decreases material sticking, enhancing grinding efficiency.
92% alumina liners work well in medium-duty applications. They offer great wear resistance at a reduced price. 95% alumina linings are harder and denser. They execute better in durable procedures with greater influence or abrasion. Both kinds are available in shapes like rectangles, trapezoids, or mosaics for very easy installment.
Mounting ceramic liners involves bonding them to the mill covering with epoxy or mechanical bolts. Correct alignment guarantees also wear and stays clear of voids. Normal assessments check for fractures or loose liners. Changing harmed sections very early avoids bigger failings.
Using alumina ceramic linings cuts replacement costs. They last 5-10 times much longer than steel linings. Energy consumption drops since their lightweight layout reduces mill load. Much less frequent upkeep increases manufacturing uptime.
These liners are environment-friendly. They produce no steel contamination in processed materials. Recycling old ceramic linings is feasible by squashing them for reuse in lower-grade applications.
Round mill drivers select alumina porcelains for reliability. The 92% and 95% alternatives fit various spending plans and operational needs. Customized dimensions and thicknesses adjust to particular machinery. Suppliers check each set for thickness, solidity, and influence toughness to make certain high quality.
Company Introduction
Advanced Ceramics founded on October 17, 2014, is a high-tech enterprise committed to the research and development, production, processing, sales and technical services of ceramic relative materials and products.. Since its establishment in 2014, the company has been committed to providing customers with the best products and services, and has become a leader in the industry through continuous technological innovation and strict quality management.
Our products includes but not limited to Silicon carbide ceramic products, Boron Carbide Ceramic Products, Boron Nitride Ceramic Products, Silicon Carbide Ceramic Products, Silicon Nitride Ceramic Products, Zirconium Dioxide Ceramic Products, Quartz Products, etc. Please feel free to contact us.(nanotrun@yahoo.com)
Payment Methods
T/T, Western Union, Paypal, Credit Card etc.
Shipment Methods
By air, by sea, by express, as customers request.
5 FAQs of 92% 95% Alumina Ceramic Wear Lining Bricks/Ceramic Liners for Ball Mill
What are the main benefits of 92% and 95% alumina ceramic wear lining bricks? These liners protect ball mills from damage caused by grinding materials. Their high hardness reduces wear from friction. They last longer than metal liners. This cuts replacement costs. They handle high heat and chemicals well. Maintenance needs drop. Production stays steady with less downtime.
How does 92% alumina differ from 95% alumina ceramic liners? The key difference is alumina content. Higher alumina means better performance. 95% liners are denser. They resist wear better. They suit harsher conditions like heavy grinding. 92% liners work for lighter loads. They cost less. Both types outlast steel. Pick based on your mill’s workload.
How are ceramic liners installed in ball mills? Fix them with bolts or adhesives. Bolt-on methods use metal brackets. Adhesive bonding needs strong glue. Align tiles tightly. Leave no gaps. Wrong installation causes cracks or loosening. Follow the maker’s guide. Hire experts if unsure. Proper setup ensures full protection.
What is the lifespan of alumina ceramic liners? Lifespan depends on use. Factors include material hardness, mill speed, and particle size. Average life is 2-5 years. Harsher conditions shorten it. Softer materials extend it. Check liners regularly. Replace worn or broken tiles quickly. This stops further damage.
Where are alumina ceramic liners commonly used? They fit industries like mining, cement, and chemicals. Use them in ball mills grinding ores, coal, or cement. They also line chutes, hoppers, or pipelines. Avoid heavy impact areas unless reinforced. Pair with rubber or steel backing for extra support.
(92% 95% Alumina Ceramic Wear Lining Bricks/Ceramic Liners for Ball Mill)
REQUEST A QUOTE
RELATED PRODUCTS
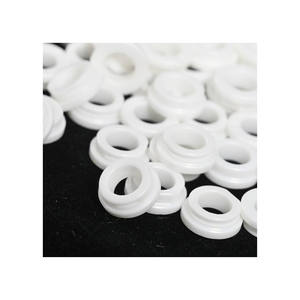
White Porcelain Insulators 95 Alumina Ceramic Tube Promotional

95/99.7 Percentage High Alumina Ceramic Tube
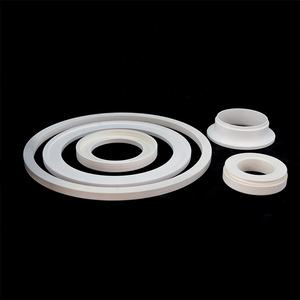
High Density 99 Alumina Ceramic Parts.
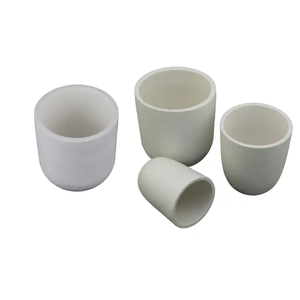
High Temperature Porous Ceramics Alumina Ceramic Semicircle
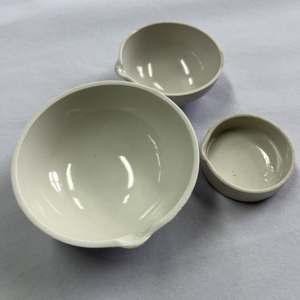
High Purity Electronic Insulation Alumina Ceramic Part
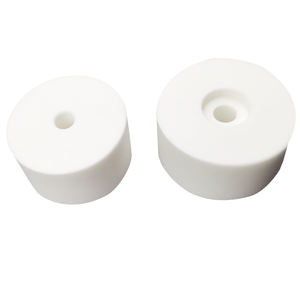