Discover Premium Ceramic Products | Durability & Elegance United | Advanced Ceramics
PRODUCT PARAMETERS
Description
Introduction to Alumina Ceramics
Alumina ceramics are known for their high hardness, wear resistance, corrosion resistance, good electrical insulation and high temperature stability. According to the different alumina content, it can be divided into different grades, such as 95 porcelain, 99 porcelain, etc., among which 99 porcelain refers to ceramic materials with an alumina content of 99%. As the alumina content increases, its mechanical strength and electrical insulation properties will also increase accordingly.
Characteristics of Alumina Ceramics
High Hardness: Alumina ceramics have extremely high hardness, which makes it very wear-resistant and suitable for manufacturing abrasive tools and parts that require wear resistance.
Wear resistance: Due to its high hardness, alumina ceramics show excellent wear resistance and are suitable for manufacturing parts for long-term use.
Corrosion resistance: Alumina ceramics have good resistance to most acids and alkalis, making them widely used in the chemical industry.
Good electrical insulation: As an excellent electrical insulating material, alumina ceramics are widely used in electronic and electrical products.
High temperature stability: Ability to withstand extremely high temperatures without significant physical or chemical changes, which makes it an ideal choice for applications in high temperature environments.
Biocompatibility: In the medical field, certain grades of alumina ceramics are used to make medical devices such as artificial joints due to their good biocompatibility.
(95 Alumina Ceramic Sheet Ceramic Substrate Alumina Plate)
Specifications of 95 Alumina Ceramic Sheet Ceramic Substrate Alumina Plate
The 95 Alumina Porcelain Sheet is a high-performance product developed for requiring commercial applications. It includes 95% aluminum oxide, guaranteeing excellent mechanical strength and thermal security. The remaining 5% consists of additives that improve sintering and architectural integrity. This ceramic substratum is perfect for atmospheres requiring resistance to heat, wear, and corrosion.
The standard thickness arrays from 0.5 mm to 15mm, accommodating varied design requirements. Customized sizes are readily available for specific tasks. The material preserves dimensional stability under extreme temperatures, running efficiently from -50 ° C to 1600 ° C. Its low thermal growth coefficient lessens warping or cracking during fast temperature adjustments.
High electrical insulation is an essential feature. The dielectric stamina goes beyond 10 kV/mm, making it suitable for digital parts and high-voltage systems. It withstands arc development, ensuring safety in electrical applications. The surface area coating is smooth, with a common roughness listed below 0.2 μm. This precision sustains applications needing tight resistances and dependable efficiency.
Mechanical longevity stands out. The flexural stamina gets to 300 MPa, and solidity procedures 80 HRA. These properties stop splitting under hefty loads or influence. Chemical resistance is an additional benefit. The sheet holds up against acids, antacid, and natural solvents, making it beneficial in harsh chemical atmospheres.
The alumina plate works with numerous processing approaches. Laser reducing, grinding, and drilling prevail methods for forming the product. It bonds well with metals and various other porcelains, allowing multilayer structures in advanced electronic devices.
Applications extend multiple industries. In electronic devices, it works as a substrate for circuits, sensors, and shielding elements. Industrial machinery utilizes it for wear-resistant parts like seals and bearings. The power field employs it in burner and thermal management systems. Clinical tools benefit from its biocompatibility and sterilization resistance.
Customization options consist of metallization for brazing or soldering. Surface area finishings or holes can be contributed to meet certain layout needs. The material adheres to RoHS and REACH criteria, ensuring ecological and safety and security conformity.
Product packaging choices vary from private items to bulk orders. Protective materials protect against damages throughout delivery. Technical assistance is offered for product selection and application advice.
(95 Alumina Ceramic Sheet Ceramic Substrate Alumina Plate)
Applications of 95 Alumina Ceramic Sheet Ceramic Substrate Alumina Plate
95% alumina ceramic sheets offer many objectives throughout industries due to their warmth resistance, electric insulation, and durability. These ceramic substrates take care of extreme temperature levels as much as 1600 ° C without damaging down. This makes them suitable for heating system cellular linings, kiln furnishings, and thermal barrier in industrial setups. They keep toughness under thermal tension, lowering wear and tear in high-heat processes.
In electronics, alumina plates work as substrates for circuits. Their electrical insulation avoids brief circuits while efficiently dissipating warm. They support parts like resistors, sensors, and silicon chips in gadgets ranging from smart devices to power grids. The material’s security guarantees trustworthy efficiency in rough conditions, including humidity or chemical exposure.
Industrial machinery uses alumina ceramic sheets as wear-resistant parts. They line pumps, valves, and nozzles taking care of unpleasant products. Their solidity expands devices life expectancy in mining, chemical processing, and production. Alumina’s deterioration resistance fits atmospheres with acids, alkalis, or solvents.
Medical applications include medical devices and implantable devices. The ceramic’s biocompatibility avoids negative reactions in the body. It additionally withstands repeated sterilization without degrading, making it helpful for dental braces or prosthetics.
Automotive and aerospace markets depend on alumina plates for sensing units and protecting components. They withstand engine warmth and resonance in autos. In aircraft, they safeguard electronic devices from severe temperature levels during flight.
The product’s convenience includes laser modern technology and semiconductor production. Alumina sheets function as steady bases for laser parts because of their reduced thermal growth. They additionally house semiconductor aspects, ensuring precision in microelectronics manufacturing.
Cost-effectiveness adds to their allure. While outshining steels or plastics in extreme problems, alumina porcelains supply lasting financial savings through reduced upkeep and substitutes. Personalized shapes and thicknesses adjust to certain industrial needs.
95% alumina ceramic sheets equilibrium efficiency and functionality. Their flexibility throughout areas originates from a mix of thermal, electric, and mechanical homes. Industries prioritize them for tasks demanding reliability under stress and anxiety.
Company Introduction
Advanced Ceramics founded on October 17, 2014, is a high-tech enterprise committed to the research and development, production, processing, sales and technical services of ceramic relative materials and products.. Since its establishment in 2014, the company has been committed to providing customers with the best products and services, and has become a leader in the industry through continuous technological innovation and strict quality management.
Our products includes but not limited to Silicon carbide ceramic products, Boron Carbide Ceramic Products, Boron Nitride Ceramic Products, Silicon Carbide Ceramic Products, Silicon Nitride Ceramic Products, Zirconium Dioxide Ceramic Products, Quartz Products, etc. Please feel free to contact us.(nanotrun@yahoo.com)
Payment Methods
T/T, Western Union, Paypal, Credit Card etc.
Shipment Methods
By air, by sea, by express, as customers request.
5 FAQs of 95 Alumina Ceramic Sheet Ceramic Substrate Alumina Plate
What is a 95 alumina ceramic sheet? This material is a ceramic substrate made mostly of aluminum oxide. It contains around 95% alumina. People use it in electronics, machinery, and high-temperature environments. It works well because it is hard, insulates electricity, and stays stable under heat.
What are the main benefits of using this ceramic sheet? It resists high temperatures and does not conduct electricity. It lasts long because it does not wear down easily. Chemicals rarely damage it. These features make it good for industrial machines, circuit boards, and heating systems.
Can this ceramic sheet handle high temperatures? Yes. It works in temperatures up to 1600°C. It does not expand much when heated. This makes it reliable for furnaces, engines, and other hot environments. It keeps its shape and strength even with repeated heating.
How does this ceramic compare to metal or plastic materials? Metals can melt or corrode under high heat. Plastics often break down or burn. This ceramic stays stable. It insulates better than metals. It is stronger than regular ceramics. It costs less than some advanced materials but performs well in tough conditions.
How do I clean and handle 95 alumina ceramic sheets? Use mild soap and water. Avoid rough scrubbing tools. Dry it completely after cleaning. Handle it carefully to prevent cracks or chips. Store it in a dry place. Keep it away from hard impacts. Check for damage before using it in equipment. Replace it if cracks or deep scratches appear.
(95 Alumina Ceramic Sheet Ceramic Substrate Alumina Plate)
REQUEST A QUOTE
RELATED PRODUCTS
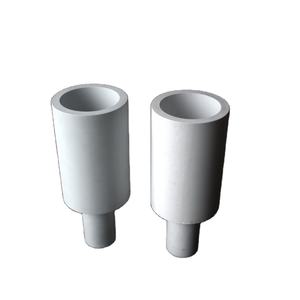
Wear Resistant High Purity White Ceramic Custom Alumina Ceramic Plunger
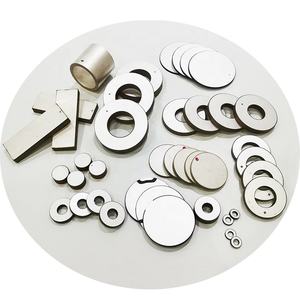
99.7% Alumina Ceramic Tube High Temperature Resistant for Industrial Ceramic Furnace Kiln Use
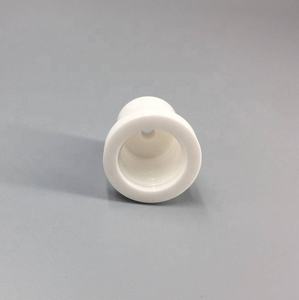
High Precision 99 Alumina Polishing Industry Mechanical Alumina Ceramic Parts Ceramic Bushing
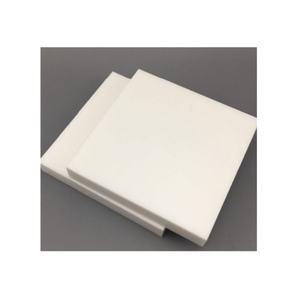
Refractory Grade Calcined Bauxite Fine Powder High Alumina for Metallurgical Casting Flux Material Good Quality for Ceramic Kiln
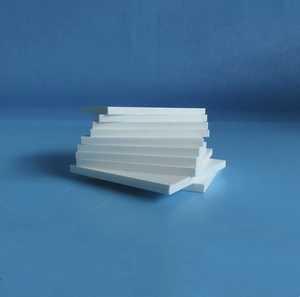
Wear Resistant Alumina Ceramic Hexagonal Tile 12mm
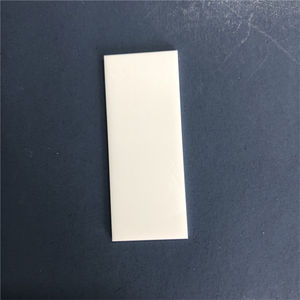