Discover Premium Ceramic Products | Durability & Elegance United | Advanced Ceramics
PRODUCT PARAMETERS
Description
Introduction to Alumina Ceramics
Alumina ceramics are known for their high hardness, wear resistance, corrosion resistance, good electrical insulation and high temperature stability. According to the different alumina content, it can be divided into different grades, such as 95 porcelain, 99 porcelain, etc., among which 99 porcelain refers to ceramic materials with an alumina content of 99%. As the alumina content increases, its mechanical strength and electrical insulation properties will also increase accordingly.
Characteristics of Alumina Ceramics
High Hardness: Alumina ceramics have extremely high hardness, which makes it very wear-resistant and suitable for manufacturing abrasive tools and parts that require wear resistance.
Wear resistance: Due to its high hardness, alumina ceramics show excellent wear resistance and are suitable for manufacturing parts for long-term use.
Corrosion resistance: Alumina ceramics have good resistance to most acids and alkalis, making them widely used in the chemical industry.
Good electrical insulation: As an excellent electrical insulating material, alumina ceramics are widely used in electronic and electrical products.
High temperature stability: Ability to withstand extremely high temperatures without significant physical or chemical changes, which makes it an ideal choice for applications in high temperature environments.
Biocompatibility: In the medical field, certain grades of alumina ceramics are used to make medical devices such as artificial joints due to their good biocompatibility.
(99% Alumina Metallized Ceramics for Bonding/Welding)
Specifications of 99% Alumina Metallized Ceramics for Bonding/Welding
99% alumina metallized ceramics fit bonding and welding applications requiring high performance. The material contains 99% aluminum oxide. This makes certain outstanding mechanical toughness and thermal security. The ceramics manage high temperatures well. They stand up to thermal shock and chemical rust efficiently. Metallization includes covering the ceramic surface with a metal layer. Usual metals used include molybdenum and manganese. These layers enable reputable bonding with steels like copper or steel. The metallized layer adheres securely to the ceramic substrate. This creates resilient joints under stress or temperature modifications.
Standard density ranges from 0.5 mm to 10 mm. Custom sizes are readily available. Surface roughness remains listed below 0.8 micrometers. This promotes smooth bonding. The metallized layer density typically determines 10-50 micrometers. Precise control makes certain uniformity. The ceramics work in settings approximately 1600 ° C. Their thermal conductivity reaches 30 W/m · K. Electric insulation stays strong even at heats. This prevents current leak in digital components.
Applications consist of vacuum cleaner tubes, laser components, and power electronic devices. They fit aerospace, automotive, and commercial heating unit. The ceramics join steel components in hermetic seals. These seals last in harsh conditions. Machining choices include laser cutting or grinding. Tolerances remain within ± 0.1 mm. This precision supports intricate assemblies. Testing covers density, porosity, and bond stamina. Each batch meets sector requirements like ASTM or ISO.
The metallized surface approves soldering, brazing, or welding. Nickel or gold plating boosts solderability. Joints preserve integrity under vibration or thermal biking. The product’s firmness exceeds 80 HRA. Use resistance maintains surface areas undamaged throughout handling. Customized metallization patterns are feasible. Display printing or thin-film methods produce accurate layouts. These ceramics reduce failure risks in crucial systems. They replace conventional materials requiring frequent maintenance. Compatibility with ultra-high vacuum settings makes them ideal for clinical tools.
(99% Alumina Metallized Ceramics for Bonding/Welding)
Applications of 99% Alumina Metallized Ceramics for Bonding/Welding
99% alumina metallized porcelains are commonly used in bonding and welding applications because they deal with high heat and stand up to wear. These ceramics function well in position where steels and other materials require strong links. The metallization process includes a metal layer to the ceramic surface area. This layer makes it less complicated to bond or bonded the ceramic to metals like copper or steel.
One common usage remains in vacuum systems. Alumina porcelains keep their form under extreme temperature levels. This makes them helpful for sealing parts in vacuum chambers. The metal layer on the ceramic permits soldering or brazing to steel components. This creates impermeable seals that last lengthy.
Power electronics also make use of these ceramics. Devices like insulators or substratums need materials that shield well however still move heat. Alumina ceramics do both. The metallized layer lets them affix to cooling systems or circuit parts. This aids electronic devices run cooler and last longer.
Medical devices relies upon alumina porcelains for components that have to stay sterile. Their smooth surface area withstands germs. Metallized ceramics can be welded to metal tools without breaking. This is essential for surgical instruments or imaging equipments that need accuracy.
Aerospace applications profit too. Alumina porcelains handle high tension and warm in engines or sensors. Metallized layers allow them bond with steel housings. This lowers failures in essential components during trip.
Automotive systems use these porcelains in sensing units or ignition parts. They endure engine heat and resonances. Welding them to steel connectors makes sure steady performance over time.
The metallization procedure can be customized. Various metals like nickel or gold are used based upon needs. This flexibility makes alumina ceramics fit lots of industries. Their high pureness (99%) ensures consistent cause harsh problems.
These porcelains also decrease prices. They last much longer than many alternatives. Much less maintenance is required. This makes them a sensible choice for industries focused on reliability.
Alumina metallized porcelains address issues where other materials stop working. Their stamina, warm resistance, and adaptability make them vital for advanced bonding and welding tasks.
Company Introduction
Advanced Ceramics founded on October 17, 2014, is a high-tech enterprise committed to the research and development, production, processing, sales and technical services of ceramic relative materials and products.. Since its establishment in 2014, the company has been committed to providing customers with the best products and services, and has become a leader in the industry through continuous technological innovation and strict quality management.
Our products includes but not limited to Silicon carbide ceramic products, Boron Carbide Ceramic Products, Boron Nitride Ceramic Products, Silicon Carbide Ceramic Products, Silicon Nitride Ceramic Products, Zirconium Dioxide Ceramic Products, Quartz Products, etc. Please feel free to contact us.(nanotrun@yahoo.com)
Payment Methods
T/T, Western Union, Paypal, Credit Card etc.
Shipment Methods
By air, by sea, by express, as customers request.
5 FAQs of 99% Alumina Metallized Ceramics for Bonding/Welding
What is 99% alumina metallized ceramic used for bonding or welding? This material is mainly used in high-temperature or high-voltage environments where strong, reliable joints are needed. It combines the heat resistance of ceramics with the conductivity of metals. The metallized layer allows direct welding to metals, creating durable connections in demanding applications.
Why choose metallized alumina ceramics over other materials? These ceramics handle extreme heat better than most metals or plastics. They resist corrosion, wear, and electrical breakdown. The metallized surface bonds tightly to metals like copper or steel. This makes them ideal for vacuum systems, power electronics, or aerospace parts needing stable performance under stress.
What industries use these ceramics? They are common in electronics for insulating parts in circuits or sensors. Aerospace uses them in engine components or satellite systems. Energy sectors apply them in high-voltage equipment or nuclear reactors. Medical devices use them for imaging machines or surgical tools needing sterile, non-reactive materials.
How does the metallization process work? A thin layer of molybdenum-manganese paste is applied to the ceramic. It is heated in a controlled furnace, fusing the metal to the surface. This creates a rough, active layer that bonds well during welding. The result is a hybrid material with ceramic insulation and metal-like joinability.
What should users avoid when handling these ceramics? Avoid mechanical shocks or sudden temperature changes. The material is hard but brittle. Use proper tools for cutting or drilling to prevent cracks. Clean surfaces before welding to ensure strong bonds. Store in dry conditions to keep the metallized layer free from oxidation or contamination. Follow manufacturer guidelines for welding temperatures and techniques.
(99% Alumina Metallized Ceramics for Bonding/Welding)
REQUEST A QUOTE
RELATED PRODUCTS
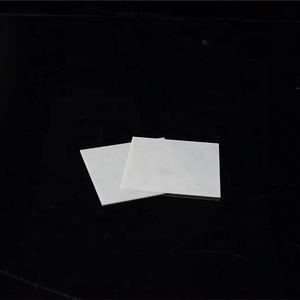
Hot ing Alumina Ceramic Tubes Used in Mining Metallurgy Chemical Industry and Electric Power
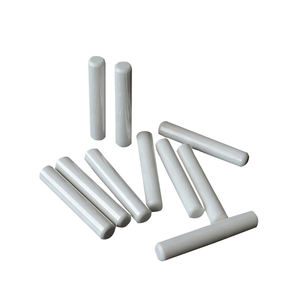
Custom High Hardness 99% Nonporous Alumina Ceramic Tubes Alumina Tube Furnace
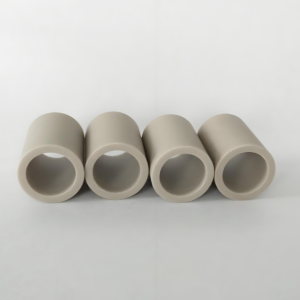
Al2O3 Ceramic mutiple size aluminium oxide ceramic tubes
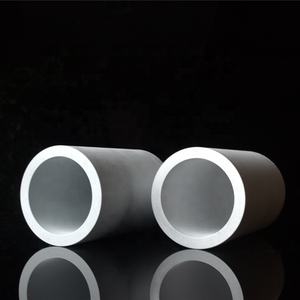
High Temperature Resistant Al2O3 Alumina Ceramic Crucible
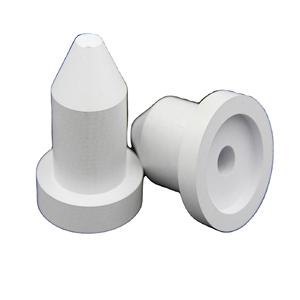
Customized Alumina Ceramic Part High Temperature Resistant Industrial Ceramic Part
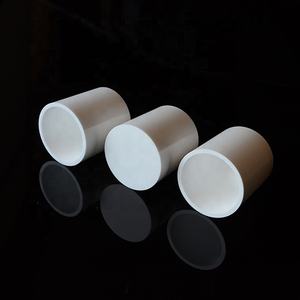