Discover Premium Ceramic Products | Durability & Elegance United | Advanced Ceramics
PRODUCT PARAMETERS
Description
Introduction to Alumina Ceramics
Alumina ceramics are known for their high hardness, wear resistance, corrosion resistance, good electrical insulation and high temperature stability. According to the different alumina content, it can be divided into different grades, such as 95 porcelain, 99 porcelain, etc., among which 99 porcelain refers to ceramic materials with an alumina content of 99%. As the alumina content increases, its mechanical strength and electrical insulation properties will also increase accordingly.
Characteristics of Alumina Ceramics
High Hardness: Alumina ceramics have extremely high hardness, which makes it very wear-resistant and suitable for manufacturing abrasive tools and parts that require wear resistance.
Wear resistance: Due to its high hardness, alumina ceramics show excellent wear resistance and are suitable for manufacturing parts for long-term use.
Corrosion resistance: Alumina ceramics have good resistance to most acids and alkalis, making them widely used in the chemical industry.
Good electrical insulation: As an excellent electrical insulating material, alumina ceramics are widely used in electronic and electrical products.
High temperature stability: Ability to withstand extremely high temperatures without significant physical or chemical changes, which makes it an ideal choice for applications in high temperature environments.
Biocompatibility: In the medical field, certain grades of alumina ceramics are used to make medical devices such as artificial joints due to their good biocompatibility.
(Alumina Ceramic Wafer Parts Mechanical Ceramic Parts Alumina Wafer High Temperature Insulating Ceramics)
Specifications of Alumina Ceramic Wafer Parts Mechanical Ceramic Parts Alumina Wafer High Temperature Insulating Ceramics
Alumina ceramic wafer parts are mechanical parts made from high-purity light weight aluminum oxide. These parts master high-temperature settings. They keep stability under extreme heat. The material make-up typically varies in between 95% and 99% light weight aluminum oxide. This makes certain solid mechanical residential properties. Alumina porcelains use high hardness. They resist wear effectively. This makes them appropriate for abrasive problems. Their thermal conductivity is reduced. Warm dissipation continues to be controlled. This is essential for insulation applications.
These parts run dependably at temperatures approximately 1650 ° C. Thermal shock resistance is a crucial feature. Rapid temperature level changes trigger marginal stress. This stops cracking. Applications consist of heating system components and semiconductor processing devices. Electrical insulation buildings are exceptional. Alumina wafers block existing leak even at heats. This is crucial for electronic and electrical systems.
Mechanical stamina is another benefit. Alumina ceramics withstand heavy lots. Compressive toughness goes beyond most steels. They are excellent for structural assistance in machinery. Chemical resistance is solid. Acids and antacid trigger little damages. This makes certain toughness in harsh atmospheres. Surface area smoothness is exact. Limited resistances meet design needs. Components fit flawlessly in complex settings up.
Dimensional security is consistent. Alumina parts do not warp under warmth. This preserves efficiency accuracy over time. Custom shapes are possible. Machining options include grinding and brightening. This allows tailored remedies for commercial requirements.
The material is non-porous. Moisture absorption is negligible. This prevents deterioration in damp settings. Alumina wafers outshine polymers and steels in rough problems. Lengthy life span lowers replacement prices. Upkeep needs are marginal.
Applications span multiple industries. Automotive systems make use of these components for sensing units and ignition elements. Aerospace relies upon them for thermal obstacles. Medical tools gain from their biocompatibility. Electronics integrate alumina wafers for circuit insulation.
Price efficiency equilibriums performance. First investment is offset by sturdiness. Power cost savings result from efficient thermal administration. Alumina ceramics fulfill strict sector requirements. Quality accreditations make sure dependability. Modification choices address details technological needs.
(Alumina Ceramic Wafer Parts Mechanical Ceramic Parts Alumina Wafer High Temperature Insulating Ceramics)
Applications of Alumina Ceramic Wafer Parts Mechanical Ceramic Parts Alumina Wafer High Temperature Insulating Ceramics
Alumina ceramic wafer components are extensively made use of in sectors requiring high performance under severe conditions. These parts handle high temperatures successfully. They work as shielding components in furnaces and kilns. Their capacity to withstand thermal shock makes them suitable for aerospace applications. They keep architectural security in settings exceeding 1500 ° C. This home is vital for thermal barrier and engine parts.
Mechanical ceramic parts made from alumina offer phenomenal wear resistance. They are used in equipment where steel components would break down rapidly. Instances consist of pump seals and bearings. Their firmness decreases rubbing, expanding equipment lifespan. Alumina’s chemical inertness stops rust from acids or alkalis. This makes them appropriate for chemical processing devices.
Alumina wafers are necessary in electronic devices. They work as substratums for circuits because of their electric insulation. They take care of heat in high-power devices like LED lighting. Their smooth surface area allows accurate printing of digital patterns. Semiconductor making counts on alumina wafers for wafer-handling elements. These components prevent polluting delicate products during production.
High-temperature protecting ceramics made from alumina are vital in metallurgy. They line commercial heaters and liquified steel containers. Their reduced thermal conductivity reduces energy loss. This boosts efficiency in steel spreading and glass manufacturing. Alumina ceramics likewise protect electrical systems in high-heat areas. Power plants utilize them to secure electrical wiring and sensors.
Clinical tools gain from alumina’s biocompatibility. It is made use of in medical devices and implants. The product resists sanitation procedures without deteriorating. Oral implants use alumina for its strength and compatibility with body cells.
Alumina porcelains are chosen for their convenience. They incorporate thermal stability, mechanical strength, and electrical insulation. Industries from aerospace to health care depend on these residential properties. Makers tailor alumina parts to satisfy particular functional demands. This makes certain dependable performance in extreme or precision-driven atmospheres.
Company Introduction
Advanced Ceramics founded on October 17, 2014, is a high-tech enterprise committed to the research and development, production, processing, sales and technical services of ceramic relative materials and products.. Since its establishment in 2014, the company has been committed to providing customers with the best products and services, and has become a leader in the industry through continuous technological innovation and strict quality management.
Our products includes but not limited to Silicon carbide ceramic products, Boron Carbide Ceramic Products, Boron Nitride Ceramic Products, Silicon Carbide Ceramic Products, Silicon Nitride Ceramic Products, Zirconium Dioxide Ceramic Products, Quartz Products, etc. Please feel free to contact us.(nanotrun@yahoo.com)
Payment Methods
T/T, Western Union, Paypal, Credit Card etc.
Shipment Methods
By air, by sea, by express, as customers request.
5 FAQs of Alumina Ceramic Wafer Parts Mechanical Ceramic Parts Alumina Wafer High Temperature Insulating Ceramics
Alumina ceramic wafer parts handle extreme heat. They work in temperatures up to 1800°C. This makes them ideal for furnaces or engines. They stay stable under thermal stress. Oxidation or corrosion rarely affects them. These parts last longer in harsh conditions.
People use alumina wafers in electronics and machinery. They act as insulators in circuits or sensors. Metallurgy and aerospace industries rely on them. They serve as substrates, crucibles, or protective layers. High-purity alumina resists chemical reactions. This suits labs or semiconductor manufacturing.
Alumina beats metals or plastics in many ways. It resists wear better than steel. It handles higher voltages without breaking down. It stays stiff under heavy loads. Alumina doesn’t melt or warp easily. This cuts replacement costs over time.
Custom shapes and sizes are possible. Manufacturers mold alumina into discs, tubes, or plates. Precision grinding ensures exact dimensions. Tight tolerances meet specific machine needs. Surface finishes reduce friction or improve insulation. Holes, grooves, or threads are added as required.
Clean alumina parts with non-abrasive tools. Use mild soap and soft cloths. Avoid scrubbing with steel wool or harsh chemicals. Check for cracks or chips regularly. Store them in dry areas to prevent moisture damage. Replace parts showing visible wear to avoid failures.
(Alumina Ceramic Wafer Parts Mechanical Ceramic Parts Alumina Wafer High Temperature Insulating Ceramics)
REQUEST A QUOTE
RELATED PRODUCTS
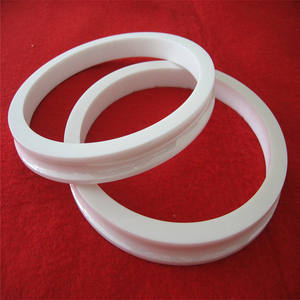
High Heat Resistant Steatite 95% Alumina Ceramic Beads for Tubular Heating Elements
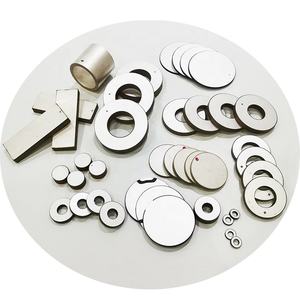
High Quality Alumina Ceramic Package Housing for Chip and Semiconductor
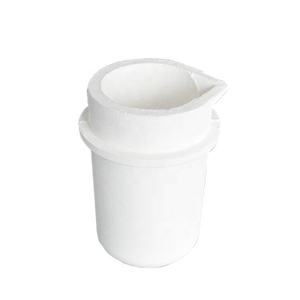
High Quality Factory Custom Alumina PE Plate Silicon Carbide Hard PE Ceramic Plate 10×12” III&IV Armor Plate
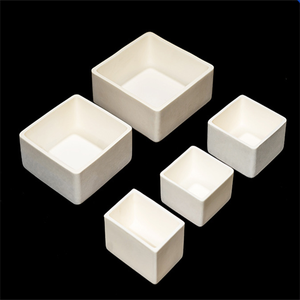
Custom Alumina Ceramic Al2o3 Boats
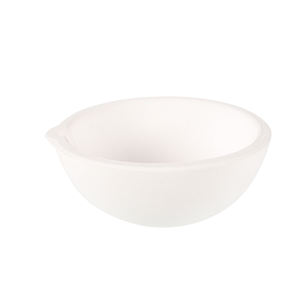
OEM Refractory Industrial High Temperature Resistance 99% Al2O3 Rod Cylinder Alumina Ceramic Tube
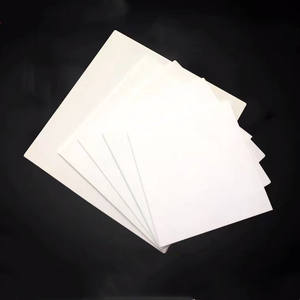