Discover Premium Ceramic Products | Durability & Elegance United | Advanced Ceramics
PRODUCT PARAMETERS
Description
Introduction to Alumina Ceramics
Alumina ceramics are known for their high hardness, wear resistance, corrosion resistance, good electrical insulation and high temperature stability. According to the different alumina content, it can be divided into different grades, such as 95 porcelain, 99 porcelain, etc., among which 99 porcelain refers to ceramic materials with an alumina content of 99%. As the alumina content increases, its mechanical strength and electrical insulation properties will also increase accordingly.
Characteristics of Alumina Ceramics
High Hardness: Alumina ceramics have extremely high hardness, which makes it very wear-resistant and suitable for manufacturing abrasive tools and parts that require wear resistance.
Wear resistance: Due to its high hardness, alumina ceramics show excellent wear resistance and are suitable for manufacturing parts for long-term use.
Corrosion resistance: Alumina ceramics have good resistance to most acids and alkalis, making them widely used in the chemical industry.
Good electrical insulation: As an excellent electrical insulating material, alumina ceramics are widely used in electronic and electrical products.
High temperature stability: Ability to withstand extremely high temperatures without significant physical or chemical changes, which makes it an ideal choice for applications in high temperature environments.
Biocompatibility: In the medical field, certain grades of alumina ceramics are used to make medical devices such as artificial joints due to their good biocompatibility.
(Aluminum Oxide Alumina Ceramic Setter Plate For Sintering Cathodes And Electrolytes)
Specifications of Aluminum Oxide Alumina Ceramic Setter Plate For Sintering Cathodes And Electrolytes
Aluminum oxide alumina ceramic setter plates handle high-temperature sintering for cathodes and electrolytes. These plates provide reputable efficiency in industrial procedures. The material consists of over 95% light weight aluminum oxide. This makes certain strong thermal security. The plates withstand temperatures approximately 1600 ° C. They keep their form under severe warm. This avoids warping during sintering. The thick framework decreases contamination. It prevents reactions with delicate products like lithium-based compounds.
The plates can be found in common sizes. Common thickness varieties from 5mm to 20mm. Custom-made dimensions fit details furnace setups. Surface area coatings are smooth. This decreases sticking of cathode or electrolyte materials. Precise flatness makes sure also warmth circulation. It supports consistent sintering results.
Thermal shock resistance is a key feature. The plates manage fast temperature adjustments. This avoids breaking during home heating or cooling cycles. Mechanical toughness remains high even after repeated use. The material withstands wear from frequent handling. Long life span decreases replacement expenses.
These setter plates job well for sintering lithium-ion battery elements. They suit strong oxide gas cell manufacturing. The inert nature of alumina avoids chemical interactions. It maintains the sintered products pure. Home plates likewise operate in air or managed ambiences. They do consistently in batch or continual processes.
Cleaning home plates is easy. Residue elimination requires standard approaches. This preserves surface top quality gradually. Storage needs no unique conditions. The plates stay steady in normal environments.
Utilizing these setter plates enhances manufacturing performance. They reduce downtime from plate failures. Their toughness supports high-volume production. The cost-efficient design equilibriums efficiency and budget. Industries gain reputable sintering solutions without compromising high quality.
(Aluminum Oxide Alumina Ceramic Setter Plate For Sintering Cathodes And Electrolytes)
Applications of Aluminum Oxide Alumina Ceramic Setter Plate For Sintering Cathodes And Electrolytes
Light weight aluminum oxide alumina ceramic setter plates play a crucial duty in sintering cathodes and electrolytes. These plates take care of heats and harsh problems during sintering. The procedure involves heating products to bond particles without melting them. Aluminum oxide ceramics work well below due to the fact that they resist warm, wear, and chemical reactions. This makes them reputable for commercial use.
In cathode manufacturing, setter plates offer a stable surface for resources. Cathodes are important parts of batteries, especially lithium-ion kinds. The plates guarantee even warm circulation throughout sintering. This prevents bending or unequal thickness in cathodes. Regular high quality improves battery performance and life-span.
For electrolytes, ceramic setter layers assistance sintering solid oxide gas cell elements. Electrolytes should perform ions effectively at high temperatures. Home plates keep architectural security under severe warm. This aids create thick, defect-free electrolytes. Reputable electrolytes increase fuel cell effectiveness and sturdiness.
Light weight aluminum oxide’s low thermal growth is one more advantage. Home plates remain steady in spite of quick temperature level changes. This lowers splits or damage throughout home heating or cooling cycles. Producers conserve prices by reusing plates several times without performance loss.
Chemical inertness matters in these applications. Home plates do not react with cathode or electrolyte products. This keeps the sintered products pure and devoid of contamination. Surface area quality of home plates additionally matters. A smooth surface area avoids sticking and makes certain very easy removal of finished components.
Resilience is a major benefit. These plates last much longer than metal or other ceramic options. They resist put on from duplicated heating and handling. This decreases downtime and replacement prices. Thermal conductivity is stabilized to make sure consistent sintering. Consistent outcomes throughout batches make manufacturing processes predictable.
These plates match markets requiring accuracy and reliability. They meet demands for high-performance products in energy storage and conversion. Their design focuses on sensible needs like warm administration, longevity, and cost-efficiency.
Company Introduction
Advanced Ceramics founded on October 17, 2014, is a high-tech enterprise committed to the research and development, production, processing, sales and technical services of ceramic relative materials and products.. Since its establishment in 2014, the company has been committed to providing customers with the best products and services, and has become a leader in the industry through continuous technological innovation and strict quality management.
Our products includes but not limited to Silicon carbide ceramic products, Boron Carbide Ceramic Products, Boron Nitride Ceramic Products, Silicon Carbide Ceramic Products, Silicon Nitride Ceramic Products, Zirconium Dioxide Ceramic Products, Quartz Products, etc. Please feel free to contact us.(nanotrun@yahoo.com)
Payment Methods
T/T, Western Union, Paypal, Credit Card etc.
Shipment Methods
By air, by sea, by express, as customers request.
5 FAQs of Aluminum Oxide Alumina Ceramic Setter Plate For Sintering Cathodes And Electrolytes
Aluminum oxide alumina ceramic setter plates help sinter cathodes and electrolytes in battery production. Below are common questions about these plates.
What are these setter plates used for?
These plates hold cathode and electrolyte materials during high-temperature sintering. They ensure even heat distribution. They prevent material warping or sticking. Their stable structure supports consistent production quality.
Why pick aluminum oxide for this job?
Aluminum oxide resists extreme heat without cracking. It stays chemically inert. This avoids reactions with sensitive battery materials. It lasts longer than other ceramics. This cuts replacement costs over time.
How hot can these plates get?
They handle temperatures up to 1700°C. They keep strength and shape even under repeated heating cycles. This makes them fit for industrial sintering furnaces.
Do these plates need special care?
Avoid sudden temperature changes. Let them cool slowly after sintering. Clean them with non-abrasive tools. Remove debris to prevent surface damage. Check for cracks regularly. Replace plates if flaws appear.
Can the plates be customized?
Yes. Sizes and thicknesses adjust to fit different furnace setups. Some users request grooves or holes for better airflow. Custom shapes help optimize space in production lines. Always confirm specs with suppliers before ordering.
These plates play a key role in making reliable batteries. Their heat resistance and durability support efficient manufacturing. Proper use and maintenance extend their service life.
(Aluminum Oxide Alumina Ceramic Setter Plate For Sintering Cathodes And Electrolytes)
REQUEST A QUOTE
RELATED PRODUCTS
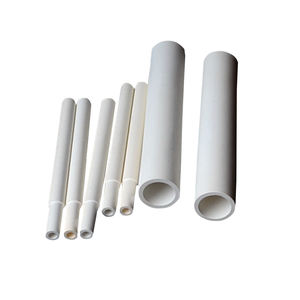
99.5% Aluminum Oxide Al2o3 Alumina Ceramic Saggar Box for Industrial Furnace
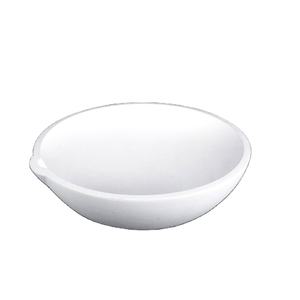
High Purity 99.99% Calcined Gamma Alumina for Ceramics
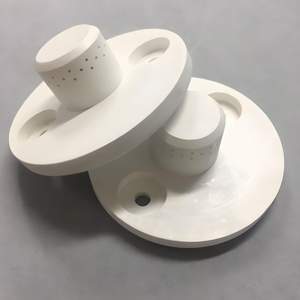
Wear Resistance 99 Alumina Ceramic Tube Porcelain Insulators For
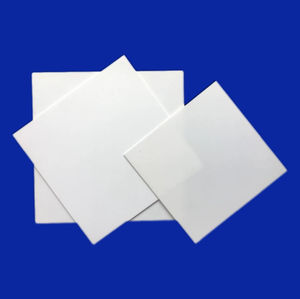
High Quality Alumina Ceramic Al2o3 Plate
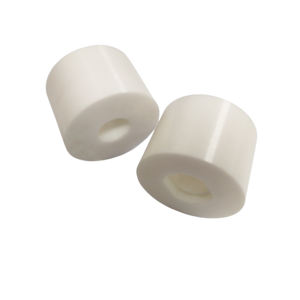
alumina ceramic tube 99% al2o3
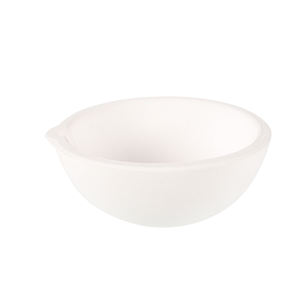