Discover Premium Ceramic Products | Durability & Elegance United | Advanced Ceramics
PRODUCT PARAMETERS
Description
Introduction to Alumina Ceramics
Alumina ceramics are known for their high hardness, wear resistance, corrosion resistance, good electrical insulation and high temperature stability. According to the different alumina content, it can be divided into different grades, such as 95 porcelain, 99 porcelain, etc., among which 99 porcelain refers to ceramic materials with an alumina content of 99%. As the alumina content increases, its mechanical strength and electrical insulation properties will also increase accordingly.
Characteristics of Alumina Ceramics
High Hardness: Alumina ceramics have extremely high hardness, which makes it very wear-resistant and suitable for manufacturing abrasive tools and parts that require wear resistance.
Wear resistance: Due to its high hardness, alumina ceramics show excellent wear resistance and are suitable for manufacturing parts for long-term use.
Corrosion resistance: Alumina ceramics have good resistance to most acids and alkalis, making them widely used in the chemical industry.
Good electrical insulation: As an excellent electrical insulating material, alumina ceramics are widely used in electronic and electrical products.
High temperature stability: Ability to withstand extremely high temperatures without significant physical or chemical changes, which makes it an ideal choice for applications in high temperature environments.
Biocompatibility: In the medical field, certain grades of alumina ceramics are used to make medical devices such as artificial joints due to their good biocompatibility.
((ceramic+rubber+steel Composite Liner) 92% 95% Alumina Ceramic Wear-Protection Plate For Mining Industry)
Specifications of (ceramic+rubber+steel Composite Liner) 92% 95% Alumina Ceramic Wear-Protection Plate For Mining Industry
The ceramic+rubber+steel composite liner offers high-performance wear defense for the mining market. It incorporates 92% and 95% alumina ceramic with resilient rubber and enhanced steel. This style makes certain resistance to severe abrasion, hefty impacts, and chemical rust. The liner is developed to extend equipment life in rough mining atmospheres.
The alumina ceramic component provides outstanding firmness. It decreases surface area wear triggered by unpleasant products like ore and gravel. The rubber layer serves as a shock absorber. It minimizes damages from effects and vibrations throughout operation. The rubber additionally dampens sound, boosting work environment safety. The steel backing includes architectural strength. It makes sure the lining remains safely in position under high stress and anxiety.
This composite lining operates in numerous mining applications. It safeguards equipment such as chutes, hoppers, and conveyor systems. Its modular layout enables very easy setup and replacement. Maintenance prices remain low as a result of the lining’s long life span. The materials resist fracturing and delamination also under constant use.
Secret specs consist of alumina material choices of 92% or 95%. The ceramic tiles are 10-20mm thick, with dimensions personalized to fit tools. The rubber layer is 5-15mm thick, using adaptability and influence resistance. The steel support plate is 2-6mm thick, supplying a steady base. Running temperature levels range from -50 ° C to 150 ° C, appropriate for most mining conditions. Surface smoothness stops product build-up, making sure consistent flow.
The composite liner minimizes downtime and fixing costs. Its light-weight design streamlines dealing with during installment. The materials are non-reactive, making them risk-free for use with different minerals. Custom sizes and shapes are readily available to match details devices needs. This item fulfills sector requirements for wear protection in mining procedures.
((ceramic+rubber+steel Composite Liner) 92% 95% Alumina Ceramic Wear-Protection Plate For Mining Industry)
Applications of (ceramic+rubber+steel Composite Liner) 92% 95% Alumina Ceramic Wear-Protection Plate For Mining Industry
The ceramic+rubber+steel composite lining incorporates 92-95% alumina ceramic with rubber and steel layers. This layout provides high resistance to wear, influence, and deterioration. It is widely used in the mining sector to secure equipment from damages brought on by heavy products, abrasive fragments, and rough atmospheres.
The composite lining functions well in conveyor systems. Mining operations relocate huge quantities of ore, coal, and rocks. These products scuff against surface areas during transportation. The ceramic layer resists abrasion. The rubber layer absorbs shocks. The steel support includes stamina. This combination decreases tools downtime and upkeep expenses.
Chutes and hoppers face constant material circulation. Influence from dropping rocks or minerals can use down surface areas quickly. The composite lining’s ceramic tiles manage unpleasant wear. The rubber layer cushions influences. The steel base protects against contortion. This setup expands the life-span of chutes and hoppers.
Crushers and grinding mills experience extreme wear. Conventional steel linings wear fast. The composite liner lasts much longer. The alumina ceramic withstands grinding forces. The rubber layer reduces sound and vibration. The steel framework keeps the liner stable under heavy lots. This decreases replacement frequency and enhances safety and security.
Transfer points in mining operations face material splilling and friction. The composite liner lines these locations to prevent wear. The smooth ceramic surface minimizes product build-up. The rubber soaks up vibrations from machinery. The steel layer makes certain the liner remains dealt with throughout procedure.
The composite lining is simple to mount. Its modular design allows quick replacement of broken areas. Upkeep staffs save time. Mining procedures stay clear of lengthy shutdowns. The materials are light-weight however long lasting. Dealing with and suitable the liner requires much less initiative contrasted to solid steel plates.
Mining atmospheres consist of wetness, dirt, and chemicals. The composite lining withstands corrosion and chemical deterioration. The ceramic does not respond with the majority of substances. The rubber seals gaps to block wetness. The steel is dealt with for extra protection. This makes the lining ideal for damp or destructive settings.
The ceramic+rubber+steel composite lining boosts tools reliability. It handles severe conditions while maintaining performance. Mining companies reduce expenses linked to constant repair services. Efficiency enhances as machines operate much longer without interruptions.
Company Introduction
Advanced Ceramics founded on October 17, 2014, is a high-tech enterprise committed to the research and development, production, processing, sales and technical services of ceramic relative materials and products.. Since its establishment in 2014, the company has been committed to providing customers with the best products and services, and has become a leader in the industry through continuous technological innovation and strict quality management.
Our products includes but not limited to Silicon carbide ceramic products, Boron Carbide Ceramic Products, Boron Nitride Ceramic Products, Silicon Carbide Ceramic Products, Silicon Nitride Ceramic Products, Zirconium Dioxide Ceramic Products, Quartz Products, etc. Please feel free to contact us.(nanotrun@yahoo.com)
Payment Methods
T/T, Western Union, Paypal, Credit Card etc.
Shipment Methods
By air, by sea, by express, as customers request.
5 FAQs of (ceramic+rubber+steel Composite Liner) 92% 95% Alumina Ceramic Wear-Protection Plate For Mining Industry
What materials make up the composite liner? The liner combines 92% to 95% alumina ceramic, rubber, and steel. These layers work together. The ceramic resists wear. The rubber absorbs impact. The steel adds strength. This mix ensures durability in tough mining conditions.
Why choose this liner over standard steel plates? The ceramic layer provides higher wear resistance. It lasts up to ten times longer than steel. The rubber layer reduces noise and vibration. The steel backing prevents bending. This design cuts replacement costs and downtime.
How does the liner handle heavy impacts? The rubber layer absorbs shock. The ceramic blocks abrasion. The steel supports the structure. Even under heavy loads, the layers stay bonded. This prevents cracking or peeling.
Can the liner be customized for different equipment? Yes. The liner is cut to fit conveyors, chutes, or hoppers. Holes or slots are added for bolts. Thickness adjusts based on wear levels. Custom sizes ensure compatibility with existing setups.
What mining applications suit this liner best? It works in high-wear zones like transfer points or crushers. It protects equipment from abrasive materials like ore or coal. Mines using bulk handling systems benefit most. Reduced maintenance and longer service life improve operational efficiency.
The liner resists corrosion from moisture or chemicals. Installation uses bolts or welding. Regular checks ensure tight bonding. Cleaning prevents material buildup. No special tools are needed for upkeep.
Industries beyond mining also use it. Cement plants, power stations, and ports face similar wear issues. The composite design adapts to multiple heavy-duty environments. Performance stays consistent under extreme temperatures or pressure.
Testing confirms the liner meets industry standards. It handles temperatures from -50°C to 150°C. The ceramic’s hardness exceeds most mined materials. Real-world trials show a 60% drop in replacement frequency. Operators report lower maintenance costs and longer equipment life.
((ceramic+rubber+steel Composite Liner) 92% 95% Alumina Ceramic Wear-Protection Plate For Mining Industry)
REQUEST A QUOTE
RELATED PRODUCTS
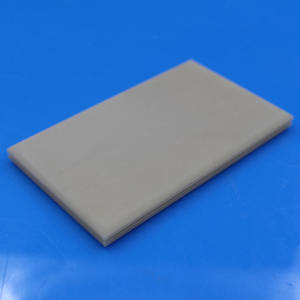
Al2o3 Crucible Alumina Ceramic High Refractoriness Alumina Al2O3 Ceramic Crucible
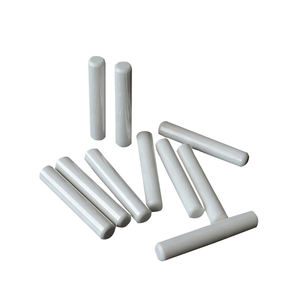
High Alumina Content Alumina Ceramic Tiles for Industrial Kilns Product Category Refractory
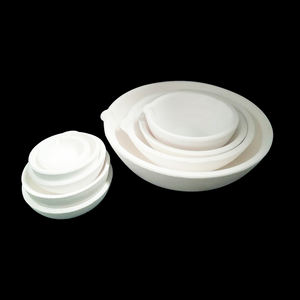
Customized Industrial High Purity Customized 99% Alumina Oxide Ceramic Assembly
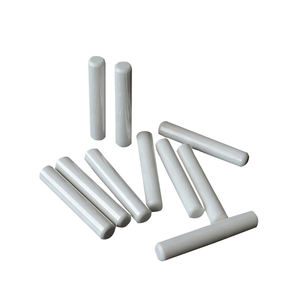
3m Xtract Cubitron Ii Net Disc 710w 80# 120# 180# 240# 320# 5-inch Anti-blocking Ceramic Alumina Grid Sanding Discs
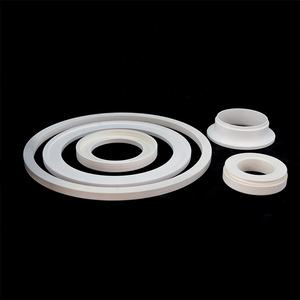
High Density 99 Alumina Ceramic Parts.
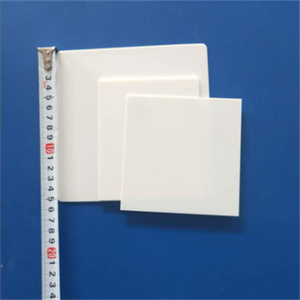