Discover Premium Ceramic Products | Durability & Elegance United | Advanced Ceramics
PRODUCT PARAMETERS
Description
Introduction to Alumina Ceramics
Alumina ceramics are known for their high hardness, wear resistance, corrosion resistance, good electrical insulation and high temperature stability. According to the different alumina content, it can be divided into different grades, such as 95 porcelain, 99 porcelain, etc., among which 99 porcelain refers to ceramic materials with an alumina content of 99%. As the alumina content increases, its mechanical strength and electrical insulation properties will also increase accordingly.
Characteristics of Alumina Ceramics
High Hardness: Alumina ceramics have extremely high hardness, which makes it very wear-resistant and suitable for manufacturing abrasive tools and parts that require wear resistance.
Wear resistance: Due to its high hardness, alumina ceramics show excellent wear resistance and are suitable for manufacturing parts for long-term use.
Corrosion resistance: Alumina ceramics have good resistance to most acids and alkalis, making them widely used in the chemical industry.
Good electrical insulation: As an excellent electrical insulating material, alumina ceramics are widely used in electronic and electrical products.
High temperature stability: Ability to withstand extremely high temperatures without significant physical or chemical changes, which makes it an ideal choice for applications in high temperature environments.
Biocompatibility: In the medical field, certain grades of alumina ceramics are used to make medical devices such as artificial joints due to their good biocompatibility.
(CNC Machining 95% Al2O3 99.7% Alumina Ceramic Insulator Used in Electrical and Semiconductor)
Specifications of CNC Machining 95% Al2O3 99.7% Alumina Ceramic Insulator Used in Electrical and Semiconductor
CNC Machining 95% Al2O3 99.7% Alumina Ceramic Insulator serves electrical and semiconductor industries. The material composition includes 95% aluminum oxide (Al2O3) and 99.7% high-purity alumina. This combination ensures excellent performance in demanding environments. The insulator withstands temperatures up to 1600°C. It maintains stability under thermal stress. High electrical insulation properties prevent current leakage. The dielectric strength exceeds 15 kV/mm. This makes it ideal for high-voltage applications.
Mechanical durability is a key feature. The material has a hardness rating of 9 on the Mohs scale. It resists wear and abrasion effectively. The flexural strength ranges between 300-400 MPa. This ensures resistance to breaking under pressure. Chemical resistance is strong. The insulator remains unaffected by acids, alkalis, and corrosive gases. This extends its lifespan in harsh conditions.
Precision manufacturing matters. CNC machining creates complex shapes with tight tolerances. Dimensional accuracy reaches ±0.01 mm. Surface finishes achieve Ra 0.4 μm or lower. Smooth surfaces reduce friction and contamination risks. Custom designs are possible. Threads, holes, and intricate geometries are machined to meet specific needs.
Applications cover multiple fields. The insulator works in circuit breakers, spark plugs, and semiconductor processing equipment. It acts as a barrier in high-temperature furnace components. Semiconductor manufacturing relies on its purity. The material avoids contaminating sensitive processes. Its thermal conductivity (24-28 W/m·K) helps dissipate heat efficiently. This prevents overheating in electronic devices.
Long-term reliability is critical. The insulator resists thermal shock. Rapid temperature changes cause minimal damage. Low porosity (below 0.5%) enhances density. Moisture absorption stays under 0.02%. These traits ensure consistent performance over time.
Customization options exist. Thickness, diameter, and shape adapt to client requirements. Testing protocols include checks for cracks, dimensional accuracy, and electrical performance. Quality control meets international standards like ISO 9001.
This alumina ceramic insulator suits industries needing high-performance materials. Its properties address challenges in electrical insulation, thermal management, and chemical exposure. The product delivers durability and precision for critical applications.
(CNC Machining 95% Al2O3 99.7% Alumina Ceramic Insulator Used in Electrical and Semiconductor)
Applications of CNC Machining 95% Al2O3 99.7% Alumina Ceramic Insulator Used in Electrical and Semiconductor
CNC machining produces 95% Al2O3 99.7% alumina ceramic insulators for electrical and semiconductor industries. These insulators handle extreme conditions due to high purity and stable properties. Alumina ceramic resists high temperatures, corrosion, and wear. It maintains strength under thermal stress, making it reliable for demanding applications.
Electrical systems use these insulators in power distribution and transmission. They isolate conductive parts in transformers, circuit breakers, and high-voltage switches. Alumina’s low electrical conductivity prevents energy loss. It ensures safety by blocking unintended current flow. Semiconductor manufacturing relies on alumina parts for precise processes. The material’s non-reactive nature avoids contaminating sensitive components. It works in wafer processing, etching chambers, and chemical vapor deposition systems.
CNC machining creates complex shapes with tight tolerances. This precision suits custom designs for specific equipment. Engineers choose alumina for its mechanical durability. It withstands vibration and mechanical shock in industrial environments. The material’s thermal stability handles rapid temperature changes. This is critical in applications like high-power electronics and laser systems.
Alumina insulators support automation and miniaturization trends. Their compact size fits modern devices without sacrificing performance. Manufacturers reduce downtime by using long-lasting ceramic parts. Semiconductor tools require minimal maintenance when using alumina components. The material’s resistance to plasma erosion extends equipment lifespan.
Customized alumina insulators meet unique industry needs. CNC technology adjusts dimensions, holes, and surface finishes. This flexibility speeds up prototyping and mass production. Alumina’s compatibility with metals and polymers allows hybrid assemblies. It bonds well with sealing materials in vacuum systems.
These insulators serve renewable energy sectors like solar and wind power. They protect inverters and converters from electrical interference. Alumina ceramics ensure stable performance in harsh outdoor conditions. The material meets international standards for electrical insulation. It complies with safety regulations across global markets.
95% Al2O3 alumina offers a cost-effective solution. It balances performance and affordability for high-volume production. Industries trust its consistency across batches. Quality control during CNC machining guarantees defect-free parts. The process ensures smooth surfaces to prevent arcing or short circuits.
Alumina ceramic insulators enable advancements in electronics and semiconductor technology. Their role in efficient energy transfer and precision manufacturing remains vital. Manufacturers prioritize materials that enhance reliability and efficiency. Alumina ceramics meet these demands across multiple sectors.
Company Introduction
Advanced Ceramics founded on October 17, 2014, is a high-tech enterprise committed to the research and development, production, processing, sales and technical services of ceramic relative materials and products.. Since its establishment in 2014, the company has been committed to providing customers with the best products and services, and has become a leader in the industry through continuous technological innovation and strict quality management.
Our products includes but not limited to Silicon carbide ceramic products, Boron Carbide Ceramic Products, Boron Nitride Ceramic Products, Silicon Carbide Ceramic Products, Silicon Nitride Ceramic Products, Zirconium Dioxide Ceramic Products, Quartz Products, etc. Please feel free to contact us.(nanotrun@yahoo.com)
Payment Methods
T/T, Western Union, Paypal, Credit Card etc.
Shipment Methods
By air, by sea, by express, as customers request.
5 FAQs of CNC Machining 95% Al2O3 99.7% Alumina Ceramic Insulator Used in Electrical and Semiconductor
FAQ 1: What is CNC machining used for in making 95% Al2O3 alumina ceramic insulators?
CNC machining shapes alumina ceramic insulators with high precision. The process cuts, drills, or grinds the material into exact sizes. This ensures parts meet tight tolerances needed in electrical and semiconductor devices. CNC works well for complex designs. It avoids cracks or flaws common in traditional methods.
FAQ 2: Why choose 95% Al2O3 alumina ceramic for electrical insulation?
This material resists high heat and electricity. It handles temperatures up to 1600°C without breaking down. Its high purity (99.7%) stops current leakage. This makes it safe for circuits and semiconductors. It also lasts longer than plastics or lower-grade ceramics.
FAQ 3: Can CNC-machined alumina insulators handle harsh environments?
Yes. They resist chemical corrosion, wear, and extreme heat. Moisture or acids don’t damage them. This stability suits semiconductor manufacturing or high-voltage systems. The material stays strong under stress. It won’t warp or degrade over time.
FAQ 4: How precise are CNC-machined alumina ceramic parts?
Tolerances can reach ±0.01 mm. CNC machines follow digital designs exactly. This precision fits parts into devices like circuit breakers or sensors. Smooth surfaces reduce friction. Tight fits prevent electrical failures. Custom shapes are possible without extra costs.
FAQ 5: Are there limits to the size or shape of CNC-machined alumina insulators?
CNC handles most sizes, from tiny components to larger industrial parts. Thin walls or small holes are possible. Very complex shapes might need special tools. Material hardness can slow machining. Discuss design details with suppliers to avoid issues.
(CNC Machining 95% Al2O3 99.7% Alumina Ceramic Insulator Used in Electrical and Semiconductor)
REQUEST A QUOTE
RELATED PRODUCTS
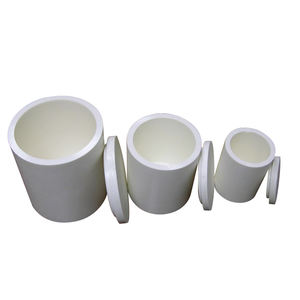
Industrial Catalyst Carrier 10mm 13mm 16mmHollow Perforated Porous Alumina Ceramic Balls
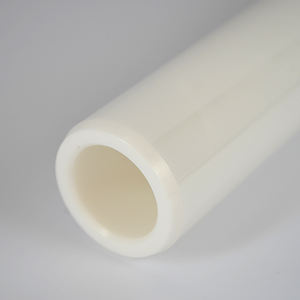
Custom White 95% Alumina Ceramic Nozzle Injection Molding for Industrial Ceramic Polishing Cutting Welding Grinding Applications
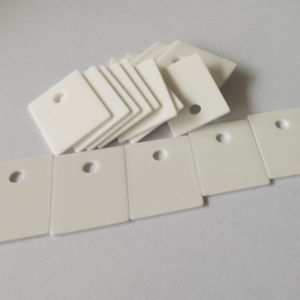
High Quality Alumina Ceramic Tiles 99.9% Purity
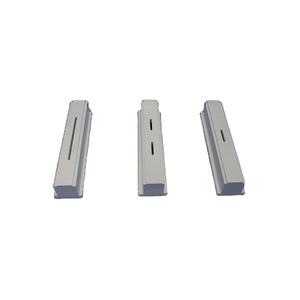
Precision Insulated Alumina Ceramic Heating Tube Heat Resistant Alumina Ceramic Tube Refractories
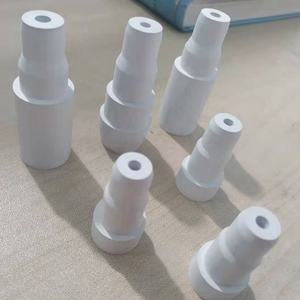
99%Al2O3 High Temperature Alumina Ceramic Sagger Tray Square Ceramic Crucible
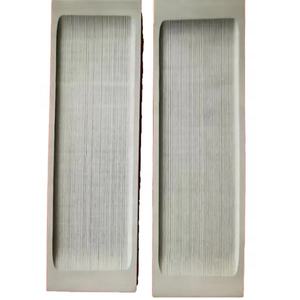