Discover Premium Ceramic Products | Durability & Elegance United | Advanced Ceramics
PRODUCT PARAMETERS
Description
Introduction to Alumina Ceramics
Alumina ceramics are known for their high hardness, wear resistance, corrosion resistance, good electrical insulation and high temperature stability. According to the different alumina content, it can be divided into different grades, such as 95 porcelain, 99 porcelain, etc., among which 99 porcelain refers to ceramic materials with an alumina content of 99%. As the alumina content increases, its mechanical strength and electrical insulation properties will also increase accordingly.
Characteristics of Alumina Ceramics
High Hardness: Alumina ceramics have extremely high hardness, which makes it very wear-resistant and suitable for manufacturing abrasive tools and parts that require wear resistance.
Wear resistance: Due to its high hardness, alumina ceramics show excellent wear resistance and are suitable for manufacturing parts for long-term use.
Corrosion resistance: Alumina ceramics have good resistance to most acids and alkalis, making them widely used in the chemical industry.
Good electrical insulation: As an excellent electrical insulating material, alumina ceramics are widely used in electronic and electrical products.
High temperature stability: Ability to withstand extremely high temperatures without significant physical or chemical changes, which makes it an ideal choice for applications in high temperature environments.
Biocompatibility: In the medical field, certain grades of alumina ceramics are used to make medical devices such as artificial joints due to their good biocompatibility.
(Custom 99% Al2O3 Alumina Ceramic High Temperature Resistant Parts)
Specifications of Custom 99% Al2O3 Alumina Ceramic High Temperature Resistant Parts
Custom 99% Al2O3 alumina ceramic high-temperature resistant parts are engineered for demanding commercial applications. These parts are made from 99% pure light weight aluminum oxide, making sure premium performance in severe problems. The material’s high pureness guarantees superb thermal stability, mechanical strength, and resistance to use.
These ceramic components operate reliably in temperature levels as much as 1800 ° C. They keep architectural honesty under long term warmth exposure, making them optimal for heaters, kilns, and thermal handling equipment. The low thermal growth coefficient lessens fracturing or deformation during rapid temperature adjustments.
Mechanical buildings consist of high hardness, similar to sophisticated engineering ceramics. This makes certain longevity in abrasive environments. The components resist rust from acids, alkalis, and molten steels, extending life span in rough chemical settings. Electric insulation stays stable even at elevated temperatures, suitable for electronic and high-voltage applications.
Modification alternatives cover intricate forms and precise dimensions. Parts like tubes, plates, nozzles, and insulators are tailored to fulfill particular needs. Limited tolerances are attainable via innovative machining techniques, making sure compatibility with existing systems. Surface coatings can be adjusted for minimized rubbing or boosted sealing.
The alumina ceramic’s low thickness minimizes component weight without giving up stamina. This benefits aerospace, automotive, and power industries where weight financial savings matter. Compatibility with vacuum environments makes these components helpful in semiconductor manufacturing and vacuum cleaner heater systems.
Applications span multiple industries. Metallurgy utilizes them for crucibles and thermocouple defense tubes. Electronic devices depend on them for substrates and insulators. Chemical handling utilizes these ceramics for pump seals and reactor cellular linings. Their versatility and dependability make them crucial for high-performance systems.
Material testing includes checks for density, porosity, and thermal shock resistance. Quality control ensures each batch satisfies strict criteria. Personalized services are developed in cooperation with clients, addressing distinct functional difficulties. Technical support is readily available for integration and optimization.
These alumina ceramic parts are a cost-effective selection for long-lasting usage. Minimized upkeep and replacement needs lower general functional prices. Performance consistency makes sure marginal downtime in vital processes.
(Custom 99% Al2O3 Alumina Ceramic High Temperature Resistant Parts)
Applications of Custom 99% Al2O3 Alumina Ceramic High Temperature Resistant Parts
Customized 99% Al2O3 alumina ceramic parts take care of extreme warmth. They work in areas where metals or plastics stop working. These parts are made from high-purity light weight aluminum oxide. This provides superb warmth resistance. They stay steady at temperature levels over 1600 ° C. Their firmness and put on resistance make them last much longer than numerous materials.
These components are utilized in many sectors. In aerospace, they shield elements from engine warm. They protect sensing units and electronics in high-speed airplane. Automotive systems use them for engine components. They take care of exhaust warm and lower wear in braking systems. This enhances lorry efficiency and safety.
Semiconductor manufacturing relies on these porcelains. They hold wafers during high-temperature processes. Their pureness avoids contamination in cleanrooms. Medical gadgets utilize them also. They operate in sanitation devices and medical tools. Their resistance to chemicals guarantees integrity in harsh medical settings.
Power manufacturing take advantage of alumina ceramics. They line furnaces and reactors in steel processing. Photovoltaic panel manufacturing uses them to deal with molten products. They insulate elements in nuclear power plant. This helps systems run efficiently under tension.
Custom shapes and sizes are feasible. Suppliers mold and mildew alumina porcelains right into tubes, plates, or intricate designs. This adaptability meets details sector needs. The components stand up to deterioration and chemical damages. They carry out well in acidic or alkaline conditions.
Electric insulation is an additional advantage. Alumina ceramics avoid present leakage in high-voltage systems. They sustain circuits and sensing units in electronic devices. Their stability makes sure gadgets function safely under thermal or electric anxiety.
These porcelains minimize downtime and maintenance costs. Their toughness cuts the requirement for frequent replacements. Industries save money while improving functional safety and security. Custom services deal with unique challenges. Engineers tailor properties like thickness or surface area coating for certain applications.
Alumina porcelains are crucial for modern-day high-temperature procedures. They integrate warmth resistance with mechanical toughness. Their versatility makes them useful across fields.
Company Introduction
Advanced Ceramics founded on October 17, 2014, is a high-tech enterprise committed to the research and development, production, processing, sales and technical services of ceramic relative materials and products.. Since its establishment in 2014, the company has been committed to providing customers with the best products and services, and has become a leader in the industry through continuous technological innovation and strict quality management.
Our products includes but not limited to Silicon carbide ceramic products, Boron Carbide Ceramic Products, Boron Nitride Ceramic Products, Silicon Carbide Ceramic Products, Silicon Nitride Ceramic Products, Zirconium Dioxide Ceramic Products, Quartz Products, etc. Please feel free to contact us.(nanotrun@yahoo.com)
Payment Methods
T/T, Western Union, Paypal, Credit Card etc.
Shipment Methods
By air, by sea, by express, as customers request.
5 FAQs of Custom 99% Al2O3 Alumina Ceramic High Temperature Resistant Parts
What makes Custom 99% Al2O3 alumina ceramic parts suitable for high-temperature environments? These parts contain 99% aluminum oxide. This material has excellent thermal stability. It can handle temperatures up to 1800°C. It resists heat better than metals or plastics. It keeps its shape and strength even under extreme heat.
Where are these alumina ceramic parts commonly used? They work in industries needing heat-resistant materials. Examples include furnace linings, semiconductor manufacturing, and aerospace components. They are also used in kilns and lab equipment. Their ability to resist corrosion and wear makes them ideal for harsh conditions.
Can these parts be customized for specific needs? Yes. Manufacturers shape and size alumina ceramic parts based on customer requirements. Processes like pressing, extrusion, or machining create precise designs. Customization ensures parts fit unique industrial applications. Technical drawings or samples help guide production.
How long do alumina ceramic parts last compared to metal parts? They outlast metals in high-temperature or corrosive settings. Metals degrade faster under thermal stress or chemical exposure. Alumina ceramics resist wear, oxidation, and deformation. This reduces replacement frequency. Proper use extends their lifespan further.
Do these parts need special care during installation or use? Avoid sudden temperature changes during installation. Rapid cooling or heating can cause cracks. Handle them carefully to prevent chipping. Use tools compatible with ceramic materials. Follow manufacturer guidelines for maintenance. Regular checks ensure optimal performance.
(Custom 99% Al2O3 Alumina Ceramic High Temperature Resistant Parts)
REQUEST A QUOTE
RELATED PRODUCTS
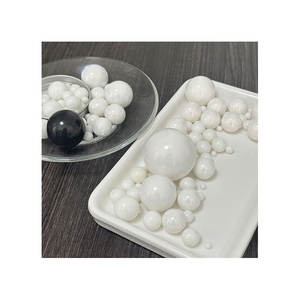
Factory Manufactured 3mm~50mm 99%95%92%alumina Inert Ceramic Ball/sphere
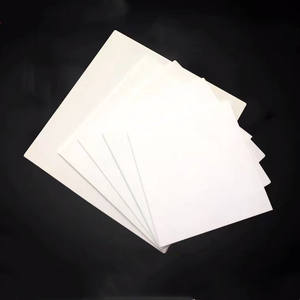
99 Ceramic Machining Parts 95 96 99 99.8 Al2O3 Alumina Ceramic
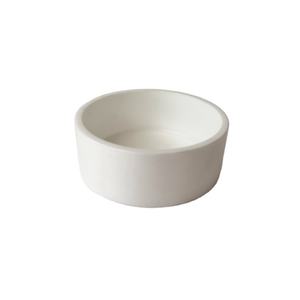
CNC Machining High Strength 99% Alumina Ceramic Spacer Al2O3 Ceramic Part
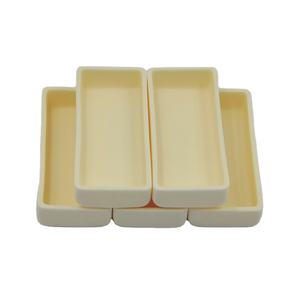
Centerless Grinding High-accuracy 99% 99.5% Al2O3 Alumina Ceramic Polished Rods
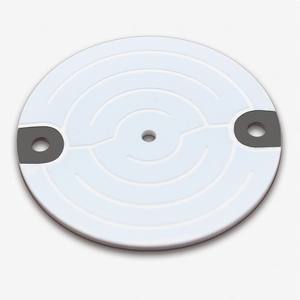
Customized Square Alumina Ceramic Plate Refractory Aluminum Oxide with Melting Crucible Premium Quality Spares Parts
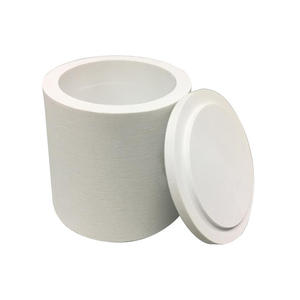