Discover Premium Ceramic Products | Durability & Elegance United | Advanced Ceramics
PRODUCT PARAMETERS
Description
Introduction to Alumina Ceramics
Alumina ceramics are known for their high hardness, wear resistance, corrosion resistance, good electrical insulation and high temperature stability. According to the different alumina content, it can be divided into different grades, such as 95 porcelain, 99 porcelain, etc., among which 99 porcelain refers to ceramic materials with an alumina content of 99%. As the alumina content increases, its mechanical strength and electrical insulation properties will also increase accordingly.
Characteristics of Alumina Ceramics
High Hardness: Alumina ceramics have extremely high hardness, which makes it very wear-resistant and suitable for manufacturing abrasive tools and parts that require wear resistance.
Wear resistance: Due to its high hardness, alumina ceramics show excellent wear resistance and are suitable for manufacturing parts for long-term use.
Corrosion resistance: Alumina ceramics have good resistance to most acids and alkalis, making them widely used in the chemical industry.
Good electrical insulation: As an excellent electrical insulating material, alumina ceramics are widely used in electronic and electrical products.
High temperature stability: Ability to withstand extremely high temperatures without significant physical or chemical changes, which makes it an ideal choice for applications in high temperature environments.
Biocompatibility: In the medical field, certain grades of alumina ceramics are used to make medical devices such as artificial joints due to their good biocompatibility.
(Customizable High Temperature Alumina Ceramic Tube Wear-Resistant Ceramic Parts for Manufacturing Include Cutting Welding)
Specifications of Customizable High Temperature Alumina Ceramic Tube Wear-Resistant Ceramic Parts for Manufacturing Include Cutting Welding
Customizable High Temperature Alumina Ceramic Tube Wear-Resistant Ceramic Parts for Manufacturing Include Cutting Welding are made for commercial applications needing resilience under severe problems. These components are made from high-purity alumina ceramic, ensuring exceptional resistance to wear, corrosion, and thermal shock. The material runs successfully in temperatures up to 1800 ° C, preserving structural honesty in high-heat atmospheres like furnaces, kilns, and welding systems.
The ceramic tubes are customizable in measurements, shapes, and thicknesses to fit specific machinery or tooling needs. Standard sizes vary from 5mm to 500mm in size, with sizes adjustable based upon consumer requirements. Surface finishes can be polished or matte, depending upon application needs. Accuracy machining makes certain limited resistances, vital for components used in cutting, welding, or product handling processes.
These components excel in rough environments because of their solidity, rated at 9 on the Mohs scale. This lowers wear in systems entailing grinding, sandblasting, or slurry transportation. The non-reactive nature of alumina ceramic stops contamination in chemical processing or food-grade applications. Electrical insulation residential or commercial properties make them appropriate for high-voltage tools or electronic manufacturing.
Installment is uncomplicated, with compatibility for steel housings or composite structures. Threaded ends, flanges, or custom installations can be included for secure setting up. The light-weight style reduces stress on equipment contrasted to standard metal parts. Long life span decreases substitute frequency, cutting downtime and upkeep costs.
Applications include laser reducing nozzles, welding rollers, heater linings, and safety sleeves for thermocouples. Industries like aerospace, vehicle, metallurgy, and energy manufacturing gain from their warm resistance and mechanical toughness. Custom designs fit special difficulties, such as irregular forms or incorporated air conditioning channels.
Technical assistance is readily available for material choice and design optimization. Samples can be checked to verify performance under operational conditions. Mass orders consist of high quality certifications, making certain conformity with worldwide requirements for industrial porcelains. Production lead times vary based upon intricacy, with conventional orders finished within 2-4 weeks.
The product is packaged firmly to stop damage during shipping. International logistics options ensure prompt shipment to making facilities. Customer support helps with post-purchase queries or substitute requirements.
(Customizable High Temperature Alumina Ceramic Tube Wear-Resistant Ceramic Parts for Manufacturing Include Cutting Welding)
Applications of Customizable High Temperature Alumina Ceramic Tube Wear-Resistant Ceramic Parts for Manufacturing Include Cutting Welding
Customizable high-temperature alumina ceramic tubes and wear-resistant ceramic components are crucial in producing sectors. These elements deal with extreme conditions. They work well in reducing and welding processes. Alumina ceramic deals high heat resistance. It stays steady at temperature levels over 1600 ° C. This makes it suitable for environments with intense thermal anxiety. The material resists wear and deterioration. It lasts longer than steel or plastic parts. This minimizes downtime and replacement costs.
In cutting applications, alumina ceramic tubes secure devices from abrasion. They line reducing tools and machinery. This prevents damage from difficult products. The tubes keep precision under high heat. They ensure tidy cuts in metalworking and laser systems. Wear-resistant ceramic components secure parts like nozzles and blades. They deal with rubbing throughout grinding or slicing. This enhances effectiveness and item quality.
For welding, alumina ceramic parts manage heat efficiently. They insulate soldering iron and components. This prevents overheating. The product does not perform electrical power. It avoids interference in arc welding. Ceramic tubes assist welding cords efficiently. They resist spatter and slag accumulation. This keeps procedures regular. Workers rely on these components for repeatable cause automated systems.
Personalized shapes and sizes fit details equipment. Manufacturers tailor alumina ceramic components to special needs. This flexibility supports complicated layouts. Industries like aerospace and vehicle use these solutions. They meet strict efficiency criteria. The porcelains adjust to high-speed production lines. They handle heavy loads without breaking.
Various other applications consist of heater cellular linings and thermal processing equipment. Alumina porcelains protect sensors in extreme atmospheres. They make sure accurate measurements. The product works in chemical handling also. It resists acids and alkalis. This adaptability makes it useful across industries.
Sturdiness and modification drive demand. Factories focus on components that reduce maintenance. Alumina ceramic parts meet these demands. They enhance performance popular procedures. Their reliability sustains advanced manufacturing methods.
Company Introduction
Advanced Ceramics founded on October 17, 2014, is a high-tech enterprise committed to the research and development, production, processing, sales and technical services of ceramic relative materials and products.. Since its establishment in 2014, the company has been committed to providing customers with the best products and services, and has become a leader in the industry through continuous technological innovation and strict quality management.
Our products includes but not limited to Silicon carbide ceramic products, Boron Carbide Ceramic Products, Boron Nitride Ceramic Products, Silicon Carbide Ceramic Products, Silicon Nitride Ceramic Products, Zirconium Dioxide Ceramic Products, Quartz Products, etc. Please feel free to contact us.(nanotrun@yahoo.com)
Payment Methods
T/T, Western Union, Paypal, Credit Card etc.
Shipment Methods
By air, by sea, by express, as customers request.
5 FAQs of Customizable High Temperature Alumina Ceramic Tube Wear-Resistant Ceramic Parts for Manufacturing Include Cutting Welding
What are the main uses of high-temperature alumina ceramic tubes? These tubes handle extreme heat in manufacturing. They work in furnaces, kilns, and high-temperature machinery. Their strength resists wear during cutting or welding processes. They protect equipment from heat damage.
How high a temperature can these ceramic parts withstand? Alumina ceramics tolerate up to 1700°C. They keep their shape and strength under prolonged heat. This makes them ideal for metal processing or glass manufacturing.
Can these parts be customized for specific machinery? Yes. Sizes, shapes, and thicknesses adjust to fit different machines. Holes, grooves, or threads are added as needed. Custom parts match exact requirements for cutting or welding tools.
Why choose alumina ceramic over metal or plastic parts? Alumina resists wear better. It lasts longer in abrasive environments. It doesn’t rust or corrode. It performs reliably in high friction or high heat areas where metals fail.
How do I maintain alumina ceramic parts? Little maintenance is needed. Clean surfaces regularly to remove debris. Avoid sudden temperature changes to prevent cracks. Check for chips or cracks during use. Replace parts if damage affects performance.
(Customizable High Temperature Alumina Ceramic Tube Wear-Resistant Ceramic Parts for Manufacturing Include Cutting Welding)
REQUEST A QUOTE
RELATED PRODUCTS
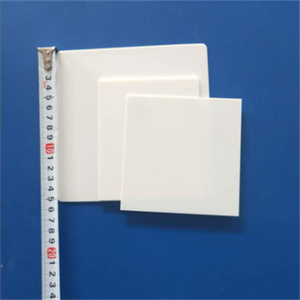
Alumina Microporous Ceramics Product
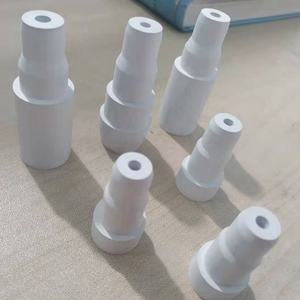
96% Alumina Al2o3 Ceramic Substrate Laser Cutting Customized Ceramic Disc
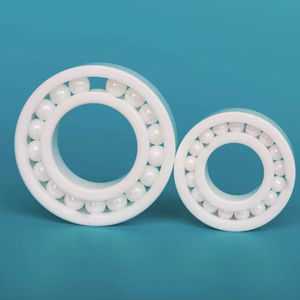
0.3um–100um Alumina Ceramic Powder
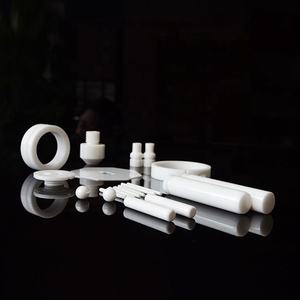
High Temperature Wear Resistant Alumina Textiles Ceramic Eyelet
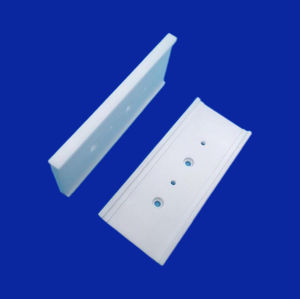
Alumina Ceramics Whole High Quality Industrial Ceramic Textile Ceramic Eco-friendly Winner Textile Knitting
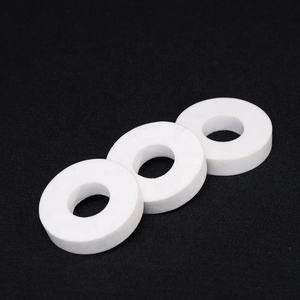