Discover Premium Ceramic Products | Durability & Elegance United | Advanced Ceramics
PRODUCT PARAMETERS
Description
Introduction to Alumina Ceramics
Alumina ceramics are known for their high hardness, wear resistance, corrosion resistance, good electrical insulation and high temperature stability. According to the different alumina content, it can be divided into different grades, such as 95 porcelain, 99 porcelain, etc., among which 99 porcelain refers to ceramic materials with an alumina content of 99%. As the alumina content increases, its mechanical strength and electrical insulation properties will also increase accordingly.
Characteristics of Alumina Ceramics
High Hardness: Alumina ceramics have extremely high hardness, which makes it very wear-resistant and suitable for manufacturing abrasive tools and parts that require wear resistance.
Wear resistance: Due to its high hardness, alumina ceramics show excellent wear resistance and are suitable for manufacturing parts for long-term use.
Corrosion resistance: Alumina ceramics have good resistance to most acids and alkalis, making them widely used in the chemical industry.
Good electrical insulation: As an excellent electrical insulating material, alumina ceramics are widely used in electronic and electrical products.
High temperature stability: Ability to withstand extremely high temperatures without significant physical or chemical changes, which makes it an ideal choice for applications in high temperature environments.
Biocompatibility: In the medical field, certain grades of alumina ceramics are used to make medical devices such as artificial joints due to their good biocompatibility.
(Customized Alumina Ceramic Grading Rotor Wheel For Airflow Pulverizer/Air Classifier Mill Parts)
Specifications of Customized Alumina Ceramic Grading Rotor Wheel For Airflow Pulverizer/Air Classifier Mill Parts
Personalized alumina ceramic grading rotor wheels are made for air movement pulverizers and air classifier mills. These elements take care of high-speed material classification and grinding. The blades wheel is made from high-purity alumina ceramic. This product makes certain exceptional wear resistance and thermal security. It carries out accurately in harsh atmospheres with unpleasant products and extreme temperatures. The alumina web content exceeds 95%. This boosts hardness and rust resistance. The item operates efficiently in temperatures approximately 1600 ° C. It preserves structural honesty under rapid thermal adjustments.
The rotor wheel’s dimensions are customized to fit details mill designs. Requirement external diameters range from 200 mm to 800 mm. Thickness varies between 20 mm and 100 mm. Custom sizes are offered based upon machine demands. The surface is precision-machined to a smooth surface. This decreases friction and prevents material accumulation. Tight tolerances ensure balanced turning at speeds surpassing 3000 RPM. Resonance is reduced for constant performance.
Secret requirements consist of a Vickers hardness of 15-18 Grade point average. This avoids contortion throughout extended usage. The thickness is 3.6-3.9 g/cm SIX. This balances stamina and weight for efficient operation. The blades wheel’s layout features enhanced edges. These stand up to breaking and breaking under impact. Numerous blade configurations are optional. These maximize particle dimension circulation and category performance.
Installment compatibility covers most air movement pulverizer brands. Custom installing holes and center styles are provided. The blades wheel incorporates seamlessly with existing systems. Upkeep requirements are reduced. The ceramic product stands up to chemical disintegration from acidic or alkaline products. Long life span lowers downtime and replacement prices.
Applications consist of processing minerals, drugs, and chemicals. The rotor wheel is suitable for fine-grinding jobs in sectors calling for precise bit control. Customized inscribing or classifying is readily available for traceability. Examining protocols include dimensional checks and high-speed balance verification. Each system goes through rigorous quality control prior to shipment.
The product is packaged firmly to avoid transit damage. Preparations rely on personalization intricacy. Mass orders get concern organizing. Technical support is provided for installation and troubleshooting.
(Customized Alumina Ceramic Grading Rotor Wheel For Airflow Pulverizer/Air Classifier Mill Parts)
Applications of Customized Alumina Ceramic Grading Rotor Wheel For Airflow Pulverizer/Air Classifier Mill Parts
Custom-made alumina ceramic grading rotor wheels are essential components in air movement pulverizers and air classifier mills. These components handle grinding and categorizing materials into fine powders. Alumina ceramic is picked for its high solidity, use resistance, and sturdiness. It executes well in harsh conditions. Industries like drugs, chemicals, and minerals processing count on these blades wheels.
In pharmaceutical production, the rotor wheel ensures specific fragment dimension control. This is essential for drug formulation. Alumina ceramic stands up to chain reaction. It maintains products pure. Contamination threats decline. Upkeep requires decrease. Functional efficiency boosts.
Chemical processing involves harsh compounds. Alumina ceramic withstands aggressive environments. Damage reduce. Element life expectancy expands. Downtime lowers. Manufacturing prices reduced. Constant outcome high quality remains high.
Minerals processing manage rough materials. Typical steel components wear out fast. Alumina ceramic rotor wheels last much longer. They preserve performance gradually. Energy consumption decreases. Handling speeds remain stable.
Food-grade applications require non-toxic materials. Alumina ceramic satisfies safety criteria. It deals with ingredients without altering preference or high quality. Fine powders like flavors or additives require uniform fragment distribution. The rotor wheel delivers this dependably.
Electronic devices making usages these rotor wheels for producing ceramic powders. Precise bit sizing makes sure optimum performance in elements. Alumina’s thermal security avoids deformation during high-temperature processes.
Customization allows blades wheels to fit certain machine layouts. Customized measurements and forms enhance material flow. Effectiveness increases. Output consistency boosts. Suppliers adjust the rotor wheel to different products. Changes in blade angle or groove pattern improve category accuracy.
The product’s reduced friction coefficient minimizes warmth generation. This stops thermal damages to delicate powders. Functional security rises. Upkeep periods lengthen. Replacement prices decrease.
Alumina ceramic grading rotor wheels use a cost-effective option. They stabilize efficiency and durability. Industries attain higher productivity. Product quality fulfills strict criteria.
Company Introduction
Advanced Ceramics founded on October 17, 2014, is a high-tech enterprise committed to the research and development, production, processing, sales and technical services of ceramic relative materials and products.. Since its establishment in 2014, the company has been committed to providing customers with the best products and services, and has become a leader in the industry through continuous technological innovation and strict quality management.
Our products includes but not limited to Silicon carbide ceramic products, Boron Carbide Ceramic Products, Boron Nitride Ceramic Products, Silicon Carbide Ceramic Products, Silicon Nitride Ceramic Products, Zirconium Dioxide Ceramic Products, Quartz Products, etc. Please feel free to contact us.(nanotrun@yahoo.com)
Payment Methods
T/T, Western Union, Paypal, Credit Card etc.
Shipment Methods
By air, by sea, by express, as customers request.
5 FAQs of Customized Alumina Ceramic Grading Rotor Wheel For Airflow Pulverizer/Air Classifier Mill Parts
What is a customized alumina ceramic grading rotor wheel used for in an airflow pulverizer or air classifier mill? It helps separate fine particles from coarse ones during grinding. The rotor wheel spins at high speeds to create airflow. This airflow sorts materials by size. The wheel ensures precise classification for consistent product quality. Alumina ceramic is chosen for its hardness and resistance to wear.
Why use alumina ceramic for the rotor wheel instead of metal? Alumina ceramic lasts longer under harsh conditions. Metal parts wear down faster from constant friction with abrasive materials. Ceramic resists corrosion and high temperatures better. This reduces downtime for replacements. Maintenance costs drop over time.
Can the rotor wheel be customized for specific milling needs? Yes. Size, shape, and thickness can be adjusted. Custom designs match different machine models and processing goals. Some applications need tighter particle size control. Others focus on higher throughput. Tailoring the rotor wheel optimizes performance for each case.
What benefits does a ceramic rotor wheel offer compared to standard options? It improves classification accuracy. Smoother surfaces reduce airflow turbulence. This boosts efficiency in separating particles. Energy consumption lowers as a result. The material’s durability cuts replacement frequency. Less downtime means higher productivity.
How do you maintain an alumina ceramic grading rotor wheel? Clean it regularly to prevent material buildup. Check for cracks or chips during routine inspections. Avoid impacts during handling or installation. Proper alignment in the machine ensures even wear. No lubrication is needed. Follow the manufacturer’s guidelines for specific care steps.
(Customized Alumina Ceramic Grading Rotor Wheel For Airflow Pulverizer/Air Classifier Mill Parts)
REQUEST A QUOTE
RELATED PRODUCTS
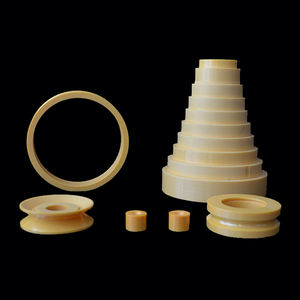
Insulating Al2o3 Ceramic Thin Plate Alumina Ceramic Substrate 95
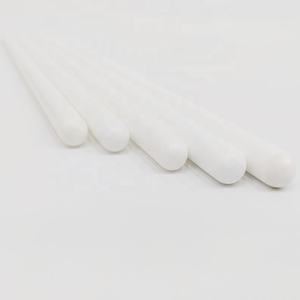
Customizable Alumina 99 Porcelain Ceramic Tube Insulated Al2O3 Ceramic Tubes Moulded Ceramic Plates
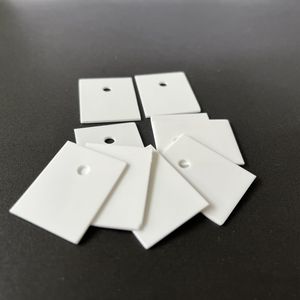
Wear Resistant Alumina Ceramic Thin Sheets Zirconia Tounghness Alumina ZTA Ceramic Plate
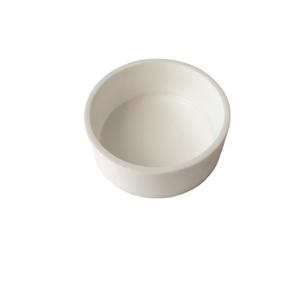
Industrial Porous Alumina Honeycomb Ceramic Multi-color Customization
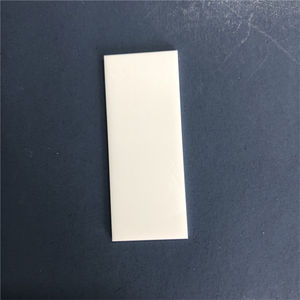
High-Purity 95% Alumina Ceramic Balls for Chemical Processing and Catalyst Support
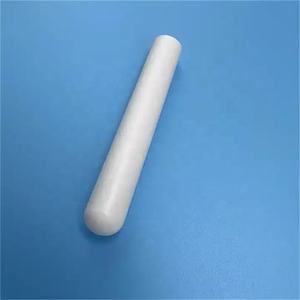