Discover Premium Ceramic Products | Durability & Elegance United | Advanced Ceramics
PRODUCT PARAMETERS
Description
Introduction to Alumina Ceramics
Alumina ceramics are known for their high hardness, wear resistance, corrosion resistance, good electrical insulation and high temperature stability. According to the different alumina content, it can be divided into different grades, such as 95 porcelain, 99 porcelain, etc., among which 99 porcelain refers to ceramic materials with an alumina content of 99%. As the alumina content increases, its mechanical strength and electrical insulation properties will also increase accordingly.
Characteristics of Alumina Ceramics
High Hardness: Alumina ceramics have extremely high hardness, which makes it very wear-resistant and suitable for manufacturing abrasive tools and parts that require wear resistance.
Wear resistance: Due to its high hardness, alumina ceramics show excellent wear resistance and are suitable for manufacturing parts for long-term use.
Corrosion resistance: Alumina ceramics have good resistance to most acids and alkalis, making them widely used in the chemical industry.
Good electrical insulation: As an excellent electrical insulating material, alumina ceramics are widely used in electronic and electrical products.
High temperature stability: Ability to withstand extremely high temperatures without significant physical or chemical changes, which makes it an ideal choice for applications in high temperature environments.
Biocompatibility: In the medical field, certain grades of alumina ceramics are used to make medical devices such as artificial joints due to their good biocompatibility.
(Factory Alumina Ceramic Plate 95% 96% 99.5%al2o3 Insulating Machinable Ceramic Plate)
Specifications of Factory Alumina Ceramic Plate 95% 96% 99.5%al2o3 Insulating Machinable Ceramic Plate
Factory Alumina Ceramic Plate 95% 96% 99.5% Al2O3 Insulating Machinable Ceramic Plate Specifications. These high-purity alumina ceramic plates serve industrial applications requiring insulation, heat resistance, and mechanical stability. Available in 95%, 96%, and 99.5% Al2O3 compositions, each grade meets specific performance needs.
The 95% alumina ceramic plate offers strong mechanical strength and thermal stability. It operates in temperatures up to 1600°C. Its electrical insulation properties make it ideal for electronic components and furnace parts. The material resists chemical corrosion and wear, suitable for harsh environments. Applications include furnace linings, electrical insulators, and wear-resistant surfaces.
The 96% alumina ceramic plate provides higher density and improved performance. It features better mechanical strength and thermal shock resistance compared to 95% alumina. This grade suits high-stress applications like semiconductor manufacturing equipment and laser components. It maintains stability under rapid temperature changes, ensuring long-term reliability.
The 99.5% alumina ceramic plate delivers premium performance. With minimal porosity and exceptional hardness, it excels in extreme conditions. This grade withstands temperatures exceeding 1700°C, making it suitable for aerospace, medical implants, and advanced electronics. Its ultra-high purity ensures minimal ionic contamination, critical for precision applications.
All grades are machinable in the pre-sintered state, allowing custom shapes and sizes. After firing, the plates achieve full hardness and stability. Standard thickness ranges from 1mm to 50mm, with diameters or lengths tailored to customer requirements. Surface finishes include polished, glazed, or as-fired options.
Key properties include low thermal expansion, high dielectric strength, and resistance to acids and alkalis. The material remains non-reactive in most chemical environments, ensuring durability. Its lightweight structure compared to metals reduces energy consumption in high-temperature processes.
Common uses span electronics, metallurgy, chemical processing, and automotive industries. Examples include circuit carriers, crucibles, pump components, and heat shields. Customized solutions accommodate specialized industrial needs.
These alumina ceramic plates ensure reliability in demanding settings. Their combination of thermal, electrical, and mechanical properties supports efficient operations across multiple sectors. The availability of multiple purity levels allows users to balance cost and performance based on application requirements.
(Factory Alumina Ceramic Plate 95% 96% 99.5%al2o3 Insulating Machinable Ceramic Plate)
Applications of Factory Alumina Ceramic Plate 95% 96% 99.5%al2o3 Insulating Machinable Ceramic Plate
Factory alumina ceramic plates with 95%, 96%, and 99.5% Al2O3 content serve many purposes across industries. These plates handle high heat, resist wear, and insulate electricity well. Their strength and durability make them suitable for tough environments.
The 95% Al2O3 ceramic plate works in industrial settings. It handles high temperatures in furnace parts, kiln linings, and heat treatment equipment. It resists chemical corrosion in chemical processing units. It serves as a reliable barrier in high-wear areas like conveyor systems.
The 96% Al2O3 ceramic plate fits electronics and electrical systems. Its insulation properties prevent current leakage in circuit boards, sensors, and insulators. It withstands high voltages in power distribution components. It works in semiconductor manufacturing for wafer-handling tools.
The 99.5% Al2O3 ceramic plate suits high-purity applications. Its low impurity level meets medical and laboratory needs. It creates surgical tools, dental implants, and lab equipment requiring sterility. It functions in precision machinery parts needing minimal friction.
These ceramic plates aid metallurgy. They line crucibles and molds for melting metals. They endure molten metal splashes without degrading. They insulate induction heating systems to improve energy efficiency.
In machinery, alumina plates act as wear-resistant components. They protect pump seals, valve seats, and cutting tools from abrasion. They extend equipment life in mining and construction.
The machinable feature allows custom shapes. Manufacturers cut, drill, and polish the plates to fit specific designs. This flexibility supports prototyping and specialized industrial tools.
Alumina ceramic plates support energy sectors. They insulate components in solar panels and wind turbines. They manage heat in nuclear reactor parts.
These plates work in automotive applications. They insulate spark plugs and sensors. They reduce friction in engine parts.
The 95%, 96%, and 99.5% Al2O3 grades balance cost and performance. Higher purity offers better performance for critical tasks. Lower purity remains cost-effective for general industrial use.
Company Introduction
Advanced Ceramics founded on October 17, 2014, is a high-tech enterprise committed to the research and development, production, processing, sales and technical services of ceramic relative materials and products.. Since its establishment in 2014, the company has been committed to providing customers with the best products and services, and has become a leader in the industry through continuous technological innovation and strict quality management.
Our products includes but not limited to Silicon carbide ceramic products, Boron Carbide Ceramic Products, Boron Nitride Ceramic Products, Silicon Carbide Ceramic Products, Silicon Nitride Ceramic Products, Zirconium Dioxide Ceramic Products, Quartz Products, etc. Please feel free to contact us.(nanotrun@yahoo.com)
Payment Methods
T/T, Western Union, Paypal, Credit Card etc.
Shipment Methods
By air, by sea, by express, as customers request.
5 FAQs of Factory Alumina Ceramic Plate 95% 96% 99.5%al2o3 Insulating Machinable Ceramic Plate
What is the Factory Alumina Ceramic Plate? This product is a high-purity ceramic plate made from alumina (Al2O3). It comes in three purity levels: 95%, 96%, and 99.5%. These plates excel in electrical insulation and thermal resistance. They can be machined into precise shapes. Common applications include electronics, machinery parts, and high-temperature industrial settings.
How do the 95%, 96%, and 99.5% versions differ? Higher purity improves performance. The 99.5% plate has better thermal stability and insulation. It is denser and resists wear more effectively. The 95% and 96% plates are more affordable. They work well in less extreme conditions. The choice depends on specific needs and budget.
What are the main benefits of these plates? They withstand temperatures up to 1600°C. They block electrical currents and resist chemical damage. Their machinability allows custom designs. They last longer in tough environments. These traits make them useful in aerospace, medical devices, and heavy industry.
Can these ceramic plates be machined easily? Yes, but specialized tools are required. Diamond or carbide tools are recommended. Standard tools wear down quickly. Higher purity plates are harder to shape. Careful machining avoids cracks and ensures accuracy.
Where are these alumina plates commonly used? They appear in electronic components like circuit boards. They line high-temperature furnaces. They are used in laser systems and medical imaging devices. Industrial applications include seals and insulating parts. They fit any scenario demanding heat resistance and electrical insulation.
(Factory Alumina Ceramic Plate 95% 96% 99.5%al2o3 Insulating Machinable Ceramic Plate)
REQUEST A QUOTE
RELATED PRODUCTS
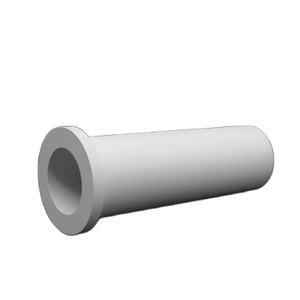
99% Al2O3 Ceramic Spacer Ring Alumina Thermal Insulation Washer
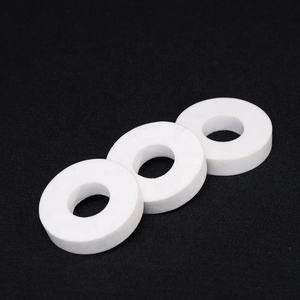
High Hardness Refractory Alumina Ceramic Disc Heating Wire Ceramic Plates With Custom Cutting And Moulding Processing Services
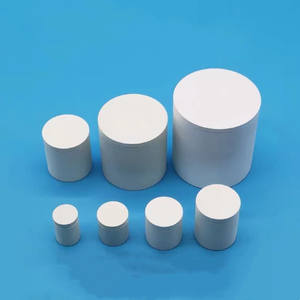
Excellent Performance Alumina Ceramic China Factory Customized Size Refractory
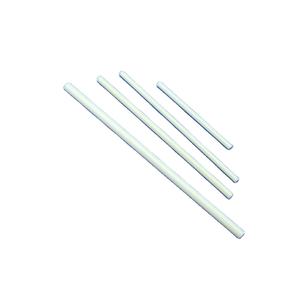
92% 95% Al2o3 Alumina Ceramic Hex Tiles , Hexagonal Ceramic Tiles
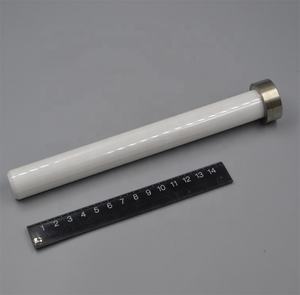
Low-cost Alumina Ceramic Raw Material Powder – Refractory Castable, Spot Whole with Large
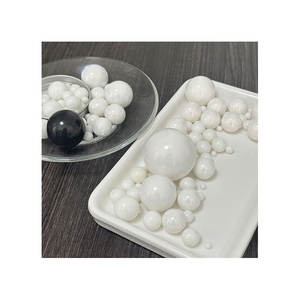