Discover Premium Ceramic Products | Durability & Elegance United | Advanced Ceramics
PRODUCT PARAMETERS
Description
Introduction to Alumina Ceramics
Alumina ceramics are known for their high hardness, wear resistance, corrosion resistance, good electrical insulation and high temperature stability. According to the different alumina content, it can be divided into different grades, such as 95 porcelain, 99 porcelain, etc., among which 99 porcelain refers to ceramic materials with an alumina content of 99%. As the alumina content increases, its mechanical strength and electrical insulation properties will also increase accordingly.
Characteristics of Alumina Ceramics
High Hardness: Alumina ceramics have extremely high hardness, which makes it very wear-resistant and suitable for manufacturing abrasive tools and parts that require wear resistance.
Wear resistance: Due to its high hardness, alumina ceramics show excellent wear resistance and are suitable for manufacturing parts for long-term use.
Corrosion resistance: Alumina ceramics have good resistance to most acids and alkalis, making them widely used in the chemical industry.
Good electrical insulation: As an excellent electrical insulating material, alumina ceramics are widely used in electronic and electrical products.
High temperature stability: Ability to withstand extremely high temperatures without significant physical or chemical changes, which makes it an ideal choice for applications in high temperature environments.
Biocompatibility: In the medical field, certain grades of alumina ceramics are used to make medical devices such as artificial joints due to their good biocompatibility.
(High Pure 95 99 Alumina Combustion Crucible in Ceramic for Metal Melting)
Specifications of High Pure 95 99 Alumina Combustion Crucible in Ceramic for Metal Melting
High Pure 95-99 Alumina Burning Crucibles in ceramic are developed for metal melting applications. These crucibles are made from costs alumina ceramic. The alumina web content ranges in between 95% and 99%. This high pureness ensures exceptional thermal stability. The product resists extreme temperatures up to 1800 ° C. It does reliably in extended high-heat environments. The structure is dense. This decreases porosity. Low porosity protects against chemical erosion. Molten metals do not pass through the crucible walls.
The crucibles include solid thermal shock resistance. Quick temperature level adjustments do not create cracking. They cool or heat promptly without damage. This durability expands service life. Customers save prices on constant replacements. The mechanical toughness is high. The crucibles withstand heavy tons. They manage hostile mixing or scraping during steel handling.
These crucibles can be found in numerous dimensions. Typical sizes vary from 50mm to 300mm. Custom-made measurements are offered. Wall thickness is enhanced for even heat circulation. Warmth transfers successfully. Power intake lowers during melting. The smooth internal surface area stops metal attachment. Clean-up is easier. Recurring waste lowers.
Chemical inertness is a crucial advantage. The alumina ceramic stands up to acidic and alkaline deterioration. It does not respond with a lot of molten metals. Thawed examples stay uncontaminated. This is crucial for precision applications. Labs and foundries benefit from constant outcomes.
Managing standards are straightforward. Preheat the crucible before initial use. Stay clear of unexpected temperature level jumps. Steady home heating protects against stress fractures. Store in a completely dry atmosphere. Dampness absorption is very little but feasible. Proper care guarantees optimum life expectancy.
These crucibles collaborate with electrical, gas, and induction heating systems. They match gold, silver, copper, and alloy melting. Industrial and research setups use them widely. The combination of high pureness, thermal efficiency, and architectural stability makes them a sensible choice.
(High Pure 95 99 Alumina Combustion Crucible in Ceramic for Metal Melting)
Applications of High Pure 95 99 Alumina Combustion Crucible in Ceramic for Metal Melting
High-purity 95-99% alumina burning crucibles offer crucial duties in ceramic applications for steel melting. These crucibles manage extreme heat in industrial processes. They are ideal for thawing steels like steel, iron, copper, and light weight aluminum. The high alumina web content ensures thermal security. It resists wear also under extended direct exposure to temperature levels as much as 1800 ° C. This makes them ideal for duplicated use popular environments.
The ceramic framework of these crucibles avoids contamination throughout metal melting. Alumina does not respond with the majority of molten steels. This keeps the final product pure. The product’s reduced porosity decreases the risk of contaminations seeping into the thaw. This is crucial for applications calling for precise metal make-up.
High-purity alumina crucibles carry out well in both ferrous and non-ferrous steel handling. They endure fast temperature level changes without cracking. This thermal shock resistance decreases downtime in production cycles. Manufacturing facilities gain from lowered equipment substitute prices. The crucibles maintain architectural honesty over lots of home heating and cooling cycles.
These crucibles are extensively made use of in foundries and metalworking stores. They collaborate with induction furnaces, gas-fired kilns, and electric melters. Their longevity makes them a sensible option for high-volume operations. They additionally suit small-scale laboratories or precious jewelry manufacturers thawing rare-earth elements like silver or gold.
The chemical inertness of alumina protects against slag formation. This lowers cleaning between sets. Operators save time and sources. The smooth surface of the crucibles allows very easy elimination of solidified metal. This attribute enhances workflow in hectic commercial setups.
High-purity alumina crucibles outmatch typical graphite or clay options. Graphite deteriorates quicker in oxidizing atmospheres. Clay lacks the exact same thermal endurance. Alumina offers a longer life-span. This lowers long-lasting operational prices.
Industries calling for precise temperature control rely on these crucibles. Aerospace, automotive, and electronics manufacturing use them for alloy production. They make certain constant results in developing parts with limited resistances. The crucibles’ integrity sustains high-grade output in critical applications.
Maintenance is simple. The crucibles stand up to most chemical reactions. Easy cleaning after usage keeps them in ideal condition. Correct handling extends their service life better. This makes them an economical remedy for metal melting procedures.
Company Introduction
Advanced Ceramics founded on October 17, 2014, is a high-tech enterprise committed to the research and development, production, processing, sales and technical services of ceramic relative materials and products.. Since its establishment in 2014, the company has been committed to providing customers with the best products and services, and has become a leader in the industry through continuous technological innovation and strict quality management.
Our products includes but not limited to Silicon carbide ceramic products, Boron Carbide Ceramic Products, Boron Nitride Ceramic Products, Silicon Carbide Ceramic Products, Silicon Nitride Ceramic Products, Zirconium Dioxide Ceramic Products, Quartz Products, etc. Please feel free to contact us.(nanotrun@yahoo.com)
Payment Methods
T/T, Western Union, Paypal, Credit Card etc.
Shipment Methods
By air, by sea, by express, as customers request.
5 FAQs of High Pure 95 99 Alumina Combustion Crucible in Ceramic for Metal Melting
What is the maximum temperature the crucible can handle? The High Pure 95-99 Alumina Combustion Crucible works reliably up to 1700°C. It handles most metal melting processes. Higher purity grades (like 99%) withstand temperatures near 1800°C. Always check the product specs for exact limits based on alumina content. Exceeding these temperatures risks cracking or damage.
Does it resist thermal shock? Yes, the alumina ceramic material resists sudden temperature changes better than many alternatives. Rapid heating or cooling still stresses the crucible. Avoid moving it directly from extreme heat to cold environments. Preheating it slowly before use improves performance. This reduces cracks caused by instant expansion.
How long does the crucible last? Lifespan depends on usage conditions. Frequent exposure to very high temperatures or corrosive metals shortens it. Proper handling prevents early wear. Avoid mechanical impacts or abrasive cleaning. With care, it typically lasts multiple melting cycles. Replace it if cracks, warping, or severe surface erosion appear.
Which metals can I melt in it? The crucible works with common metals like gold, silver, copper, and iron alloys. Avoid metals requiring extreme heat beyond 1800°C, like tungsten. Some reactive metals (e.g., titanium) may interact with alumina. Check compatibility charts for specialty metals. Acidic fluxes or strong alkalis also risk damaging the crucible.
How do I clean and maintain it? Let the crucible cool completely after use. Remove residue with a soft brush or non-abrasive tool. Soak stubborn debris in mild detergent solution. Never use harsh chemicals or metal scrapers. Dry thoroughly before reheating. Store it in a dry area to prevent moisture absorption. Inspect for cracks before each use.
(High Pure 95 99 Alumina Combustion Crucible in Ceramic for Metal Melting)
REQUEST A QUOTE
RELATED PRODUCTS
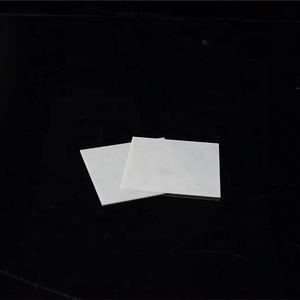
Hot ing Alumina Ceramic Tubes Used in Mining Metallurgy Chemical Industry and Electric Power
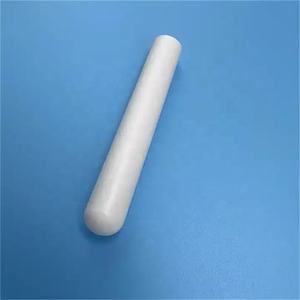
KERUI 99% Aluminum Alumina Ceramic Corundum Tube Thermocouple Protection For Refractory Applications Fiberglass Moulded
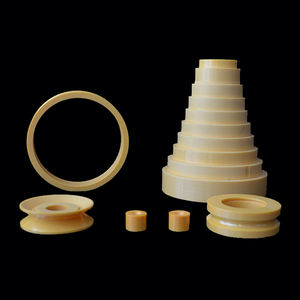
High-Strength Alpha Alumina Ceramic Balls Industrial Catalyst Support and Covering Media
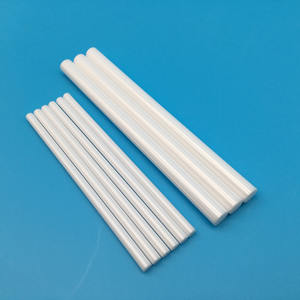
Customization Plate 99% Alumina Ceramic Plate High Quality Ceramic Product with 205*140*4mm
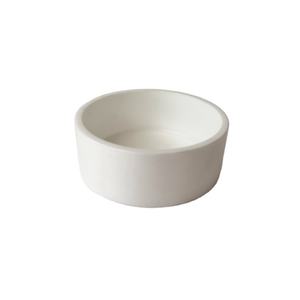
Industrial Alumina or Zirconia High Quality Ceramic Corrugated Tube
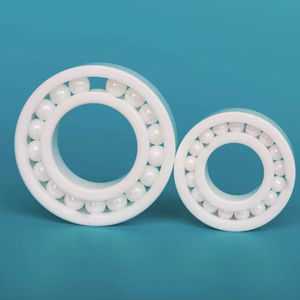