Discover Premium Ceramic Products | Durability & Elegance United | Advanced Ceramics
PRODUCT PARAMETERS
Description
Introduction to Alumina Ceramics
Alumina ceramics are known for their high hardness, wear resistance, corrosion resistance, good electrical insulation and high temperature stability. According to the different alumina content, it can be divided into different grades, such as 95 porcelain, 99 porcelain, etc., among which 99 porcelain refers to ceramic materials with an alumina content of 99%. As the alumina content increases, its mechanical strength and electrical insulation properties will also increase accordingly.
Characteristics of Alumina Ceramics
High Hardness: Alumina ceramics have extremely high hardness, which makes it very wear-resistant and suitable for manufacturing abrasive tools and parts that require wear resistance.
Wear resistance: Due to its high hardness, alumina ceramics show excellent wear resistance and are suitable for manufacturing parts for long-term use.
Corrosion resistance: Alumina ceramics have good resistance to most acids and alkalis, making them widely used in the chemical industry.
Good electrical insulation: As an excellent electrical insulating material, alumina ceramics are widely used in electronic and electrical products.
High temperature stability: Ability to withstand extremely high temperatures without significant physical or chemical changes, which makes it an ideal choice for applications in high temperature environments.
Biocompatibility: In the medical field, certain grades of alumina ceramics are used to make medical devices such as artificial joints due to their good biocompatibility.
(High Quality and Advanced Precision Insulation Ceramics Ceramic Alumina Ceramic Plate)
Specifications of High Quality and Advanced Precision Insulation Ceramics Ceramic Alumina Ceramic Plate
High-quality advanced precision insulation ceramics ceramic alumina ceramic plates deliver exceptional performance in demanding industrial environments. These plates consist of high-purity alumina (Al₂O₃) with content ranging from 95% to 99.5%. The material ensures superior electrical insulation, thermal resistance, and mechanical durability. Alumina ceramic plates withstand temperatures up to 1600°C. They maintain stability under extreme heat, preventing deformation or cracking.
The plates feature a dense structure with low porosity. This minimizes moisture absorption and enhances corrosion resistance. Surface hardness reaches HRA 80-90, making them resistant to wear and abrasion. Their flexural strength exceeds 300 MPa, allowing reliable load-bearing capacity in high-stress applications.
Thermal conductivity remains low, around 20-30 W/m·K. This property ensures effective heat insulation, reducing energy loss in high-temperature systems. The coefficient of thermal expansion matches most metals, enabling secure bonding in composite structures. Electrical insulation strength exceeds 15 kV/mm, preventing current leakage in electronic components.
Standard thickness ranges from 1 mm to 50 mm. Custom sizes accommodate specific requirements, with precision machining maintaining dimensional accuracy within ±0.1 mm. Surface finishes vary from polished to matte, tailored for applications needing smooth interfaces or friction control.
These ceramic plates suit furnace linings, semiconductor processing equipment, laser components, and high-voltage insulators. They perform reliably in aerospace, automotive, and energy sectors. Chemical inertness allows use in corrosive environments, including exposure to acids, alkalis, and molten metals.
Advanced manufacturing techniques ensure consistent quality. Each batch undergoes rigorous testing for density, hardness, and dielectric properties. The plates meet international standards like ASTM F2888 and ISO 6474. Customizable features include drilled holes, grooves, or complex geometries via CNC machining.
High-purity alumina ceramics resist oxidation and UV degradation. They operate effectively in vacuum conditions or high-pressure systems. Minimal maintenance is required due to non-reactive surfaces and long-term structural integrity. Compatibility with brazing, metallization, and epoxy bonding simplifies integration into existing assemblies.
The material’s lightweight nature reduces overall system weight compared to metal alternatives. It eliminates electromagnetic interference in sensitive electronic applications. Strict quality control guarantees defect-free surfaces and uniform material composition across all products. Custom solutions address unique thermal management or electrical isolation challenges.
(High Quality and Advanced Precision Insulation Ceramics Ceramic Alumina Ceramic Plate)
Applications of High Quality and Advanced Precision Insulation Ceramics Ceramic Alumina Ceramic Plate
High-quality advanced precision insulation ceramics made from ceramic alumina are essential in many industries. These materials are strong. They handle high heat. They resist wear. They insulate electricity well. These traits make them ideal for tough conditions.
In electronics, ceramic alumina plates protect parts from overheating. They insulate circuits. This stops electrical issues. They work in power devices and sensors. They keep performance steady. They last long even with heavy use.
Industrial machinery uses these ceramics in high-heat areas. They line furnaces and reactors. They handle extreme temperatures. They resist chemical damage. They cut downtime. They make equipment last longer. This saves money on repairs.
Aerospace and defense need reliable materials. Ceramic alumina plates shield parts from intense heat. They protect spacecraft and jet engines. They handle stress and temperature changes. They are light. This helps keep aircraft efficient.
The automotive industry uses these plates in engines and exhaust systems. They manage heat. They lower emissions. They improve fuel efficiency. Electric cars use them in battery systems. They prevent overheating. They ensure safety.
Energy production relies on these ceramics. They insulate parts in power plants. They work in turbines and nuclear reactors. They handle high heat and radiation. Renewable energy systems use them in solar panels and wind turbines. They boost efficiency. They reduce energy loss.
Medical devices benefit from ceramic alumina. It is safe for implants and tools. It resists body fluids. It stays stable during sterilization. It is reliable for long-term use.
These ceramics are versatile. They meet strict industry needs. They improve performance. They lower costs. They are vital in modern technology and manufacturing.
Company Introduction
Advanced Ceramics founded on October 17, 2014, is a high-tech enterprise committed to the research and development, production, processing, sales and technical services of ceramic relative materials and products.. Since its establishment in 2014, the company has been committed to providing customers with the best products and services, and has become a leader in the industry through continuous technological innovation and strict quality management.
Our products includes but not limited to Silicon carbide ceramic products, Boron Carbide Ceramic Products, Boron Nitride Ceramic Products, Silicon Carbide Ceramic Products, Silicon Nitride Ceramic Products, Zirconium Dioxide Ceramic Products, Quartz Products, etc. Please feel free to contact us.(nanotrun@yahoo.com)
Payment Methods
T/T, Western Union, Paypal, Credit Card etc.
Shipment Methods
By air, by sea, by express, as customers request.
5 FAQs of High Quality and Advanced Precision Insulation Ceramics Ceramic Alumina Ceramic Plate
High-quality insulation ceramics use alumina as the main material. Alumina offers excellent electrical insulation and heat resistance. These ceramics contain over 95% aluminum oxide. This makes them strong and durable. Additives improve their performance in extreme conditions. The manufacturing process involves high-temperature sintering. This ensures a dense structure with minimal pores.
These ceramic plates handle temperatures up to 1600°C. They stay stable under rapid heating or cooling. Their low thermal expansion prevents cracking. This makes them ideal for furnaces and high-heat machinery. They resist chemical corrosion from acids and alkalis. This extends their lifespan in harsh industrial environments.
Common uses include electronics, aerospace, and energy systems. They insulate components in circuit breakers and sensors. Semiconductor manufacturing relies on them for heat management. High-voltage equipment uses these ceramics to prevent electrical leaks. They also protect machinery parts from wear in heavy industries.
Advanced precision ceramics outperform metals and plastics in insulation. Metals conduct electricity and heat, causing energy loss. Plastics melt under high temperatures. Ceramics provide better mechanical strength and durability. They last longer in extreme conditions. Their dimensional stability ensures precise performance in technical applications.
Handle ceramic plates carefully during installation. Avoid dropping them or applying sudden force. Use tools designed for brittle materials. Check the surface for cracks before use. Follow manufacturer guidelines for cutting or drilling. Proper installation prevents damage and ensures safety. Clean surfaces with non-abrasive materials to avoid scratches. Store them in dry areas to maintain insulation properties.
(High Quality and Advanced Precision Insulation Ceramics Ceramic Alumina Ceramic Plate)
REQUEST A QUOTE
RELATED PRODUCTS
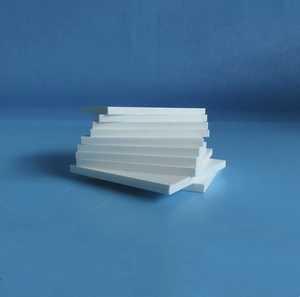
99% Alumina Electric Ceramics
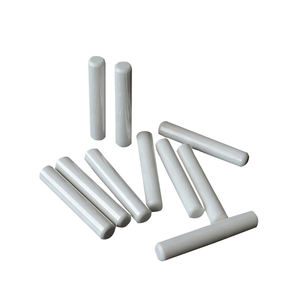
White Color Adsorbent Activated Alumina Activated Alumina Ceramic Ball
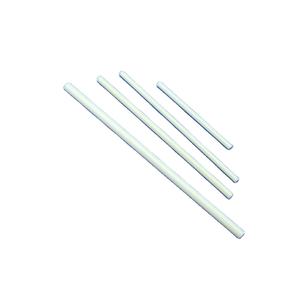
Industrial Polished 99 Alumina Ceramic Sleeve
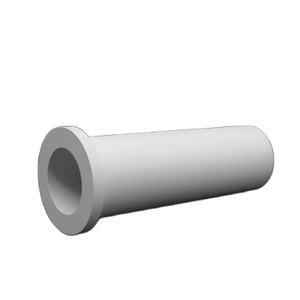
99% Al2O3 Ceramic Spacer Ring Alumina Thermal Insulation Washer
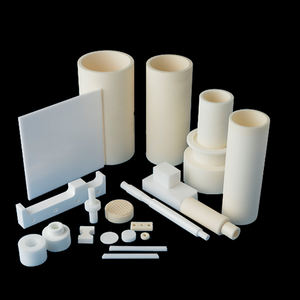
Polished 99.7% Alumina Ceramic Sheet Al2O3 Plate Aluminum Oxide Ceramic Board
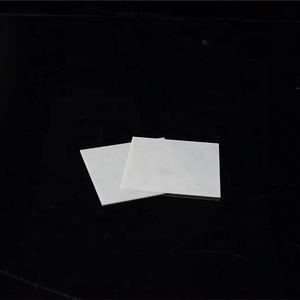