Discover Premium Ceramic Products | Durability & Elegance United | Advanced Ceramics
PRODUCT PARAMETERS
Description
Introduction to Alumina Ceramics
Alumina ceramics are known for their high hardness, wear resistance, corrosion resistance, good electrical insulation and high temperature stability. According to the different alumina content, it can be divided into different grades, such as 95 porcelain, 99 porcelain, etc., among which 99 porcelain refers to ceramic materials with an alumina content of 99%. As the alumina content increases, its mechanical strength and electrical insulation properties will also increase accordingly.
Characteristics of Alumina Ceramics
High Hardness: Alumina ceramics have extremely high hardness, which makes it very wear-resistant and suitable for manufacturing abrasive tools and parts that require wear resistance.
Wear resistance: Due to its high hardness, alumina ceramics show excellent wear resistance and are suitable for manufacturing parts for long-term use.
Corrosion resistance: Alumina ceramics have good resistance to most acids and alkalis, making them widely used in the chemical industry.
Good electrical insulation: As an excellent electrical insulating material, alumina ceramics are widely used in electronic and electrical products.
High temperature stability: Ability to withstand extremely high temperatures without significant physical or chemical changes, which makes it an ideal choice for applications in high temperature environments.
Biocompatibility: In the medical field, certain grades of alumina ceramics are used to make medical devices such as artificial joints due to their good biocompatibility.
(High Temperature Resistant Semiconductor Alumina Ceramics Parts)
Specifications of High Temperature Resistant Semiconductor Alumina Ceramics Parts
High-temperature-resistant semiconductor alumina ceramics parts handle extreme heat and harsh conditions. These parts are made from high-purity aluminum oxide. The material purity ranges from 95% to 99.9%. This ensures strong performance in demanding environments. Alumina ceramics stay stable at temperatures up to 1700°C. They outperform metals and plastics in high-heat situations.
The parts show excellent mechanical strength. They resist wear, corrosion, and chemical reactions. Compressive strength exceeds 2000 MPa. Flexural strength ranges between 300 and 400 MPa. This makes them reliable under heavy loads. Electrical insulation properties are strong. Dielectric strength reaches 15-20 kV/mm. Volume resistivity stays high even above 1000°C. This prevents current leakage in semiconductor devices.
Thermal conductivity is low. Heat spreads slowly through the material. Thermal expansion rates match metals like steel. This reduces stress during temperature changes. Precision machining allows tight dimensional control. Tolerances can be within ±0.1 mm. Custom shapes and sizes are possible. Surface finishes reach Ra 0.2 μm. Smooth surfaces reduce friction and particle buildup.
These ceramics work in semiconductor manufacturing equipment. They are used for wafer carriers, insulators, and plasma-resistant components. High-power electronics rely on them for substrates and heat sinks. Automotive sensors and aerospace components benefit from their stability.
Alumina ceramics parts resist thermal shock. Rapid temperature shifts cause minimal damage. They operate in oxidizing and reducing atmospheres. Chemical inertness prevents reactions with acids, alkalis, and molten metals. Long service life cuts downtime and replacement costs.
Customization options include coatings and metallization. This improves bonding with metals or other materials. Joints and seals stay secure under stress. Testing meets industry standards for performance and safety. Each batch undergoes quality checks. Parameters like density and hardness are verified.
Applications span semiconductors, energy, aerospace, and automotive fields. These parts support advanced technologies needing heat resistance and electrical insulation.
(High Temperature Resistant Semiconductor Alumina Ceramics Parts)
Applications of High Temperature Resistant Semiconductor Alumina Ceramics Parts
High-temperature resistant semiconductor alumina ceramics parts play a vital role in modern technology. These components handle extreme heat and harsh conditions. They are widely used in semiconductor manufacturing. Alumina ceramics provide electrical insulation. This prevents short circuits in high-power devices. Semiconductor equipment operates at high temperatures. Alumina parts maintain stability under thermal stress. They do not warp or crack easily. This ensures long-term reliability in production processes.
The electronics industry relies on alumina ceramics for wafer processing. They are used in etching and deposition chambers. These parts resist corrosion from aggressive chemicals. Plasma environments demand materials with high purity. Alumina ceramics meet these requirements. They minimize contamination during chip fabrication. This improves product yield and performance.
Power electronics benefit from alumina ceramic substrates. These substrates support circuits in high-voltage applications. They dissipate heat efficiently. This prevents overheating in devices like inverters and converters. Electric vehicles use such components for battery management. Alumina ceramics ensure safety and durability in demanding conditions.
Aerospace and defense sectors use these ceramics for sensors and ignition systems. Engine components face extreme temperatures during operation. Alumina parts withstand thermal shock without degrading. This reliability is critical for mission-critical systems.
Medical devices incorporate alumina ceramics for imaging and diagnostic tools. X-ray tubes generate intense heat. Alumina insulators keep these systems operational. They also shield sensitive electronics from radiation.
Industrial heating systems use alumina components in furnaces and reactors. These parts endure repeated thermal cycles. Their low thermal expansion reduces wear over time. This cuts maintenance costs and downtime.
Alumina ceramics are cost-effective for mass production. They are manufactured with precision using advanced techniques. Custom shapes and sizes are achievable. This flexibility suits diverse industrial needs.
Environmental applications include exhaust gas sensors. Alumina ceramics detect pollutants in high-temperature exhaust streams. They help monitor emissions in automotive and manufacturing sectors. This supports compliance with environmental regulations.
Research continues to improve alumina ceramic properties. Innovations focus on enhancing thermal conductivity and mechanical strength. These advancements will expand their use in next-generation technologies.
Company Introduction
Advanced Ceramics founded on October 17, 2014, is a high-tech enterprise committed to the research and development, production, processing, sales and technical services of ceramic relative materials and products.. Since its establishment in 2014, the company has been committed to providing customers with the best products and services, and has become a leader in the industry through continuous technological innovation and strict quality management.
Our products includes but not limited to Silicon carbide ceramic products, Boron Carbide Ceramic Products, Boron Nitride Ceramic Products, Silicon Carbide Ceramic Products, Silicon Nitride Ceramic Products, Zirconium Dioxide Ceramic Products, Quartz Products, etc. Please feel free to contact us.(nanotrun@yahoo.com)
Payment Methods
T/T, Western Union, Paypal, Credit Card etc.
Shipment Methods
By air, by sea, by express, as customers request.
5 FAQs of High Temperature Resistant Semiconductor Alumina Ceramics Parts
High Temperature Resistant Semiconductor Alumina Ceramics Parts FAQs
What are alumina ceramics? Alumina ceramics are materials made mainly from aluminum oxide. They handle high heat, resist wear, and insulate electricity well. These parts are common in electronics, machinery, and semiconductors. Their strength and stability make them ideal for tough environments.
How much heat can these parts handle? These ceramics work in temperatures up to 1800°C. They keep their shape and function even under extreme heat. This makes them suitable for furnaces, engines, and semiconductor tools. They won’t melt or crack easily compared to metals or plastics.
Why use alumina ceramics in semiconductors? Semiconductors need materials that insulate, resist heat, and last long. Alumina ceramics block electrical currents, stop parts from overheating, and handle chemical exposure. They reduce failure risks in devices like circuit boards or sensors. Their smooth surface also helps with precise manufacturing.
Do these parts need special care? Alumina ceramics require minimal maintenance. Clean them with mild detergents or compressed air. Avoid harsh chemicals or rough scrubbing. Check for cracks or chips regularly. Replace damaged parts quickly to prevent system issues. Proper handling ensures they last longer.
Can these ceramics be customized? Yes. Manufacturers shape alumina ceramics into tubes, plates, or complex designs. Sizes, thicknesses, and surface finishes are adjustable. Custom parts meet specific heat resistance or electrical needs. Testing ensures they perform as required. Share your specs with suppliers for tailored solutions.
(High Temperature Resistant Semiconductor Alumina Ceramics Parts)
REQUEST A QUOTE
RELATED PRODUCTS
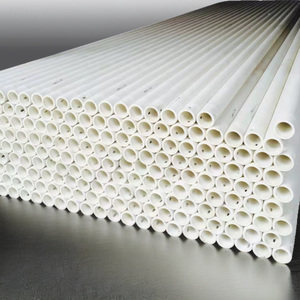
Alumina Al2o3 Ceramic Crucible/boat Container Ceramic Products
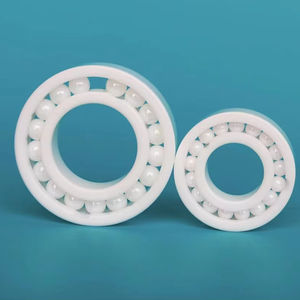
Industrial High Purity High Temperature Resistance 99% Alumina Ceramic Structural Component
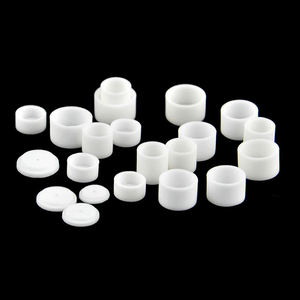
s Custom Supply Alumina Glazed Ceramic Smoking Accessories
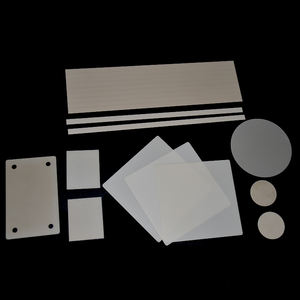
Calcined Alumina Glazing Powder for Ceramics , CAS: 1344-28-1, Refractory Raw Material
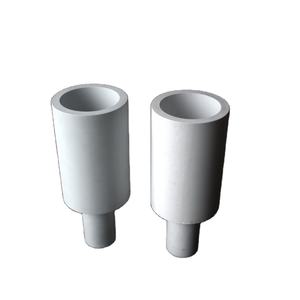
Wear Resistant High Purity White Ceramic Custom Alumina Ceramic Plunger
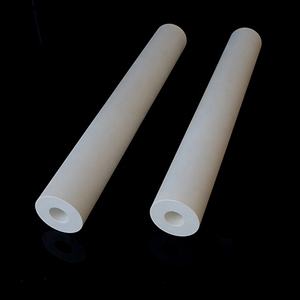