Discover Premium Ceramic Products | Durability & Elegance United | Advanced Ceramics
PRODUCT PARAMETERS
Description
Introduction to Alumina Ceramics
Alumina ceramics are known for their high hardness, wear resistance, corrosion resistance, good electrical insulation and high temperature stability. According to the different alumina content, it can be divided into different grades, such as 95 porcelain, 99 porcelain, etc., among which 99 porcelain refers to ceramic materials with an alumina content of 99%. As the alumina content increases, its mechanical strength and electrical insulation properties will also increase accordingly.
Characteristics of Alumina Ceramics
High Hardness: Alumina ceramics have extremely high hardness, which makes it very wear-resistant and suitable for manufacturing abrasive tools and parts that require wear resistance.
Wear resistance: Due to its high hardness, alumina ceramics show excellent wear resistance and are suitable for manufacturing parts for long-term use.
Corrosion resistance: Alumina ceramics have good resistance to most acids and alkalis, making them widely used in the chemical industry.
Good electrical insulation: As an excellent electrical insulating material, alumina ceramics are widely used in electronic and electrical products.
High temperature stability: Ability to withstand extremely high temperatures without significant physical or chemical changes, which makes it an ideal choice for applications in high temperature environments.
Biocompatibility: In the medical field, certain grades of alumina ceramics are used to make medical devices such as artificial joints due to their good biocompatibility.
(Industrial Alumina Ceramic Accessories with High Quality and Advanced Technology)
Specifications of Industrial Alumina Ceramic Accessories with High Quality and Advanced Technology
Industrial alumina ceramic accessories are produced difficult environments. They take care of high warmth, stand up to wear, last lengthy. The material is high-purity light weight aluminum oxide. It gives solid mechanical efficiency. These porcelains operate in temperatures approximately 1800 ° C. They remain stable. They do not fracture under unexpected temperature modifications. The solidity mores than HRA 85. They resist abrasion much better than steels. Their surface areas remain smooth also after heavy usage.
The manufacturing process makes use of sophisticated technology. Precise sintering controls density. It ensures regular top quality. The final products have tight tolerances. Sizes match precise specifications. No warping or flaws. This precision suits equipment components. It fits seals, shutoffs, bearings, cutting tools.
These porcelains withstand chemicals. Acids, alkalis do not damage them. They operate in destructive setups. They protect electrical power well. No conductivity also at high voltages. This makes them safe for electronic devices. They protect against short circuits.
Industrial makes use of include aerospace, auto, chemical plants. They cut downtime. They lower upkeep expenses. Custom-made shapes are offered. Dimensions, densities, surface area finishes can be tailored. Layouts satisfy details needs.
Quality checks happen at every step. Basic material are checked first. Completed products get X-ray scans. They undergo hardness tests. Each piece meets worldwide criteria. No compromises.
The ceramics are lightweight. They replace hefty steel parts. Machines run smoother. Energy make use of decreases. They’re eco-friendly. No hazardous coverings. No heavy steels.
Efficiency stays dependable in rough conditions. Thermal shock resistance prevents fractures. High stress doesn’t use them out. They’re excellent for heavy market.
Industrial alumina porcelains enhance efficiency. They’re built for requiring tasks. They last longer than choices. They’re a wise option for modern-day design.
(Industrial Alumina Ceramic Accessories with High Quality and Advanced Technology)
Applications of Industrial Alumina Ceramic Accessories with High Quality and Advanced Technology
Industrial alumina ceramic devices are widely used throughout different sectors because of their exceptional efficiency and dependability. These items are used sophisticated technology, making sure excellent quality and longevity. Alumina ceramics excel in settings requiring resistance to severe warm, corrosion, and put on. Their applications extend electronic devices, machinery, chemical processing, and more.
In the electronics market, alumina ceramics act as insulators, substratums, and circuit parts. Their high thermal stability avoids getting too hot, maintaining gadget performance. They additionally give outstanding electrical insulation, minimizing threats of short circuits. Machinery fields utilize these ceramics in reducing tools, bearings, and seals. Their hardness expands equipment lifespan, minimizing downtime and upkeep expenses.
The automobile market benefits from alumina ceramic parts in sensors, shutoffs, and engine components. These accessories endure heats and corrosive exhaust gases, improving engine performance. Their lightweight nature contributes to fuel performance, straightening with contemporary automobile criteria.
Chemical processing plants rely upon alumina porcelains for pumps, linings, and reactor parts. The product’s resistance to acids and alkalis guarantees secure handling of aggressive chemicals. This reduces contamination risks and enhances operational security. Clinical tools makers use alumina ceramics for medical devices and implants. Their biocompatibility and sterilizability make them ideal for critical healthcare applications.
Advanced production techniques like precision molding and sintering create alumina ceramics with consistent structures and marginal flaws. Stringent quality assurance measures assure each element fulfills industry specs. Checking methods consist of thermal shock resistance checks and mechanical toughness assessments. These actions make certain integrity under demanding conditions.
Customization choices enable tailoring ceramic devices to certain industrial demands. Designers adjust structure and measurements to enhance efficiency for special applications. This flexibility sustains technology across markets, from aerospace to energy manufacturing.
Industrial alumina ceramics integrate cutting-edge modern technology with robust material homes. Their convenience addresses difficulties in high-stress environments, delivering cost-effective solutions for contemporary sectors.
Company Introduction
Advanced Ceramics founded on October 17, 2014, is a high-tech enterprise committed to the research and development, production, processing, sales and technical services of ceramic relative materials and products.. Since its establishment in 2014, the company has been committed to providing customers with the best products and services, and has become a leader in the industry through continuous technological innovation and strict quality management.
Our products includes but not limited to Silicon carbide ceramic products, Boron Carbide Ceramic Products, Boron Nitride Ceramic Products, Silicon Carbide Ceramic Products, Silicon Nitride Ceramic Products, Zirconium Dioxide Ceramic Products, Quartz Products, etc. Please feel free to contact us.(nanotrun@yahoo.com)
Payment Methods
T/T, Western Union, Paypal, Credit Card etc.
Shipment Methods
By air, by sea, by express, as customers request.
5 FAQs of Industrial Alumina Ceramic Accessories with High Quality and Advanced Technology
What are industrial alumina ceramic accessories made of?
They are made of alumina (aluminum oxide). The material is over 95% pure. This high purity gives strength, hardness, resistance to wear and corrosion. Advanced sintering technology ensures dense, reliable structures. These properties make them ideal for harsh industrial environments.
Why choose alumina ceramics over metal or plastic parts?
Alumina ceramics handle extreme temperatures better. They work in environments up to 1600°C without melting or deforming. Metals corrode faster. Plastics degrade under high heat. Alumina resists chemical attacks, abrasion, and electrical conductivity. This reduces downtime and replacement costs.
How is advanced technology used in production?
Precision molding and sintering techniques create uniform microstructures. Automated systems control temperature and pressure during manufacturing. This eliminates defects. Laser cutting and CNC machining ensure exact dimensions. Quality checks use X-rays and ultrasonic testing. Every step focuses on consistency and performance.
What industries use these accessories?
Mining, chemical processing, power generation, and aerospace rely on them. Common applications include pump seals, valve components, grinding media, and electrical insulators. They protect machinery from wear in abrasive or corrosive settings. Electronics use them for substrates and insulating parts due to their non-conductive nature.
How long do alumina ceramic accessories last?
Lifespans depend on operating conditions. They outlast metals and plastics in high-stress environments. Proper installation and avoiding mechanical shocks help. Regular inspections prevent sudden failures. Most users report years of service without significant wear. This durability lowers long-term costs despite higher initial prices.
(Industrial Alumina Ceramic Accessories with High Quality and Advanced Technology)
REQUEST A QUOTE
RELATED PRODUCTS
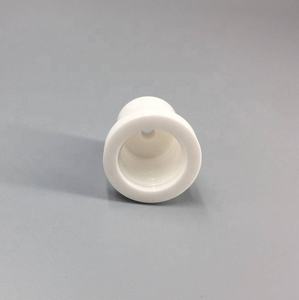
High Temperature Resistance Alumina Ceramic Plate
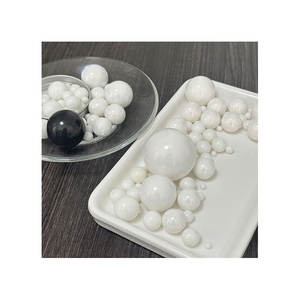
High Quality Alumina Ceramic Ceramic Protection Tubes High Temperature Aluminum Oxide
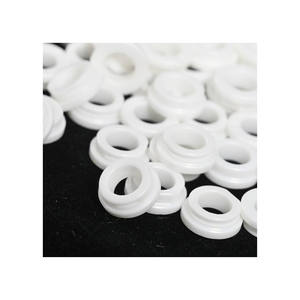
White Porcelain Insulators 95 Alumina Ceramic Tube Promotional
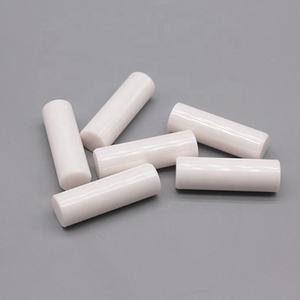
Ceramic thermocouple Protection alumina pipe
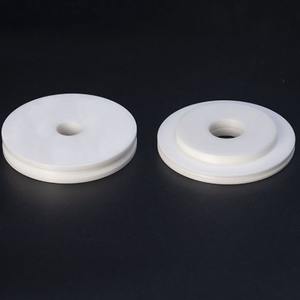
0.05mm 99% Alumina Ceramic Tube
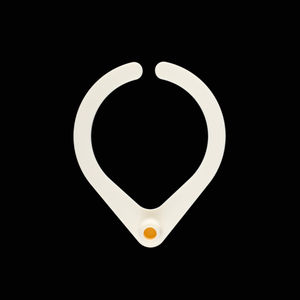