Discover Premium Ceramic Products | Durability & Elegance United | Advanced Ceramics
PRODUCT PARAMETERS
Description
Introduction to Alumina Ceramics
Alumina ceramics are known for their high hardness, wear resistance, corrosion resistance, good electrical insulation and high temperature stability. According to the different alumina content, it can be divided into different grades, such as 95 porcelain, 99 porcelain, etc., among which 99 porcelain refers to ceramic materials with an alumina content of 99%. As the alumina content increases, its mechanical strength and electrical insulation properties will also increase accordingly.
Characteristics of Alumina Ceramics
High Hardness: Alumina ceramics have extremely high hardness, which makes it very wear-resistant and suitable for manufacturing abrasive tools and parts that require wear resistance.
Wear resistance: Due to its high hardness, alumina ceramics show excellent wear resistance and are suitable for manufacturing parts for long-term use.
Corrosion resistance: Alumina ceramics have good resistance to most acids and alkalis, making them widely used in the chemical industry.
Good electrical insulation: As an excellent electrical insulating material, alumina ceramics are widely used in electronic and electrical products.
High temperature stability: Ability to withstand extremely high temperatures without significant physical or chemical changes, which makes it an ideal choice for applications in high temperature environments.
Biocompatibility: In the medical field, certain grades of alumina ceramics are used to make medical devices such as artificial joints due to their good biocompatibility.
(Industrial Wear Resistant 99% Alumina Al2O3 Ceramic Plates)
Specifications of Industrial Wear Resistant 99% Alumina Al2O3 Ceramic Plates
Industrial Put On Immune 99% Alumina Al2O3 Porcelain Plates are crafted for severe sturdiness in extreme atmospheres. The product consists of over 99% aluminum oxide, making certain high purity and optimal performance. These plates excel in applications needing resistance to abrasion, effect, and deterioration. Their solidity gets to 9 on the Mohs range, going beyond most metals and polymers. This makes them excellent for securing tools in mining, cement manufacturing, and power generation.
The density of these ceramic plates varies in between 3.8 and 3.9 g/cm FIVE, contributing to their structural integrity. They maintain security under high anxiety, with a compressive toughness surpassing 2500 MPa. Thermal properties include a maximum solution temperature level of 1650 ° C, ideal for high-heat industrial procedures. Low thermal expansion protects against breaking throughout fast temperature level adjustments.
Surface area coating choices differ from smooth to distinctive, customized to particular friction demands. Basic thicknesses extend 5mm to 30mm, with customized measurements available. Installment approaches include bonding with epoxy adhesives or mechanical fastening making use of screws. The light-weight nature decreases lots on machinery contrasted to steel options.
Chemical inertness enables these plates to withstand acids, antacid, and solvents. Electrical insulation properties avoid conductivity-related failures in delicate devices. Use prices are dramatically less than standard materials like manganese steel, expanding part life-span. Area examinations reveal a life span approximately five times much longer in slurry transport systems.
Typical applications consist of lining chutes, hoppers, and pipes. They protect fan blades, cyclones, and grinding mills from particle erosion. Compatibility with welding and machining enables very easy assimilation into existing setups. Customized shapes, such as hexagons or rectangular shapes, address complicated geometric demands.
Price performance comes from reduced downtime and upkeep expenditures. Efficiency continues to be regular in temperature levels from -50 ° C to 1600 ° C. Minimal porosity avoids product infiltration, preserving surface area high quality. These plates meet ISO 9001 criteria, making sure dependable quality assurance.
(Industrial Wear Resistant 99% Alumina Al2O3 Ceramic Plates)
Applications of Industrial Wear Resistant 99% Alumina Al2O3 Ceramic Plates
Industrial wear-resistant 99% alumina Al2O3 ceramic plates are widely utilized in harsh atmospheres where products encounter severe abrasion, influence, or corrosion. These plates are made from high-purity alumina, offering outstanding firmness and durability. They outmatch typical metals in several applications due to their resistance to wear and chemical damage.
In mining and mineral processing, these ceramic plates protect devices like chutes, hoppers, and pipes. Ore, gravel, and various other abrasive materials cause fast endure metal surfaces. Alumina plates expand equipment life by protecting surfaces from direct contact with extreme materials. This minimizes upkeep expenses and downtime.
The steel sector depends on these plates for taking care of resources and finished products. They line blast furnaces, conveyors, and transfer factors. High temperatures and heavy loads degrade average products swiftly. Alumina ceramics hold up against these problems, preserving structural stability. This makes certain consistent manufacturing effectiveness.
Nuclear power plant use alumina plates in coal handling systems and ash disposal systems. Coal fragments and ash are highly abrasive. Ceramic cellular linings avoid erosion in ducts, cyclones, and followers. This improves system integrity and decreases the danger of unanticipated failings.
Concrete manufacturing involves grinding and transporting basic materials with sharp sides. Equipment like crushers, mixers, and separators benefit from alumina ceramic linings. The plates reduce wear from continuous rubbing, keeping machinery functional for longer durations.
Chemical processing devices encounters corrosion from acids, alkalis, and solvents. Alumina ceramics withstand chemical assault while handling aggressive materials. They line reactors, pumps, and shutoffs, guaranteeing risk-free and lasting operation.
In the automotive field, these plates are utilized in shot blasting equipments and surface therapy systems. They withstand high-speed abrasive bits, keeping performance in time. This assists makers achieve consistent surface area coatings on steel parts.
Alumina ceramic plates likewise offer in aerospace for safeguarding elements from erosion throughout high-speed operations. Their lightweight nature and toughness make them perfect for applications where both sturdiness and weight matter.
These plates are adjustable fits and sizes. They can be adhered to steel supports for simple installation. This versatility enables them to fit different industrial arrangements, offering affordable services for wear-related obstacles.
Company Introduction
Advanced Ceramics founded on October 17, 2014, is a high-tech enterprise committed to the research and development, production, processing, sales and technical services of ceramic relative materials and products.. Since its establishment in 2014, the company has been committed to providing customers with the best products and services, and has become a leader in the industry through continuous technological innovation and strict quality management.
Our products includes but not limited to Silicon carbide ceramic products, Boron Carbide Ceramic Products, Boron Nitride Ceramic Products, Silicon Carbide Ceramic Products, Silicon Nitride Ceramic Products, Zirconium Dioxide Ceramic Products, Quartz Products, etc. Please feel free to contact us.(nanotrun@yahoo.com)
Payment Methods
T/T, Western Union, Paypal, Credit Card etc.
Shipment Methods
By air, by sea, by express, as customers request.
5 FAQs of Industrial Wear Resistant 99% Alumina Al2O3 Ceramic Plates
What are Industrial Wear Resistant 99% Alumina Ceramic Plates?
These plates are made from high-purity aluminum oxide (Al2O3). The material reaches 99% alumina content. This makes the plates extremely hard. They resist wear, corrosion, and high temperatures. They are used in mining, cement plants, and power industries. Their main job is to protect machinery from damage caused by friction or abrasive materials.
Why choose alumina ceramic plates over steel or other metals?
Alumina ceramic plates last longer than steel in harsh conditions. They are lighter. They do not rust. They handle temperatures up to 1600°C without breaking down. Steel wears out faster under heavy abrasion. Ceramic plates reduce maintenance costs. They keep equipment running longer without replacements.
Where are these ceramic plates commonly used?
They are installed in equipment exposed to wear. Examples include conveyor systems, chutes, hoppers, and pipelines. Mining screens and crushers use them to handle rocks and ores. Cement plants apply them to grinding mills. Power plants fit them in coal-handling systems. Any industry needing wear protection benefits from these plates.
How are alumina ceramic plates installed?
They are attached using epoxy adhesives or mechanical fasteners like bolts. The method depends on the surface and operating conditions. Epoxy works for flat surfaces. Bolting is better for high-impact areas. Proper installation ensures strong bonding. This prevents plates from loosening during operation.
Can these plates be customized for specific needs?
Yes. They come in different sizes and shapes. Thickness ranges from 5mm to 30mm. Custom shapes fit curved surfaces or complex equipment. Some plates have holes or grooves for easier fixing. Manufacturers adjust alumina content slightly for specific hardness or thermal stability requirements.
(Industrial Wear Resistant 99% Alumina Al2O3 Ceramic Plates)
REQUEST A QUOTE
RELATED PRODUCTS
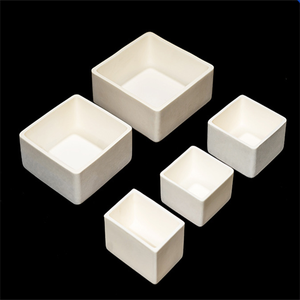
Custom Alumina Ceramic Al2o3 Boats
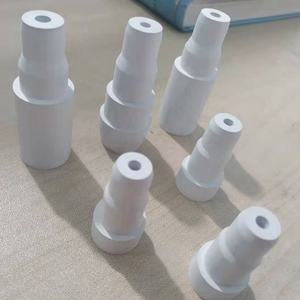
95% 96% 99% Alumina Aluminum Oxide Al2O3 Ceramic Bulk Round Plate Disc
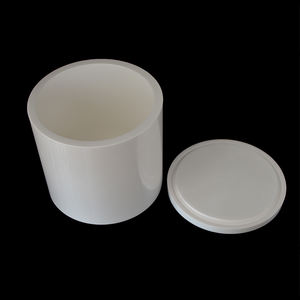
99 Al2O3 Alumina Ceramic Zirconia Porous Ceramic Wick
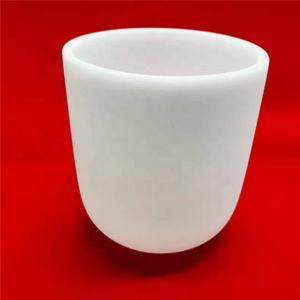
Chinese High Purity Calcined/Reactive Alumina Powder Ceramic Powder Aluminium Oxide For Refractory Raw Material
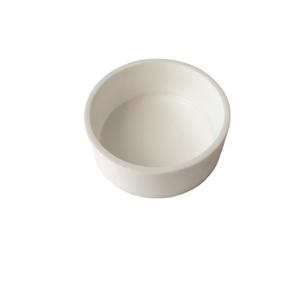
99% 99.7% Alumina Ceramic Tube For Thermocouple Ceramic Tube For Thermocouple
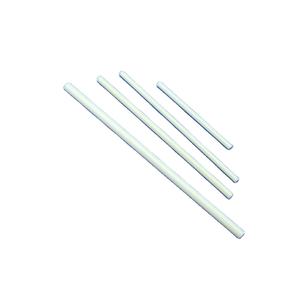