Discover Premium Ceramic Products | Durability & Elegance United | Advanced Ceramics
PRODUCT PARAMETERS
Description
Introduction to Alumina Ceramics
Alumina ceramics are known for their high hardness, wear resistance, corrosion resistance, good electrical insulation and high temperature stability. According to the different alumina content, it can be divided into different grades, such as 95 porcelain, 99 porcelain, etc., among which 99 porcelain refers to ceramic materials with an alumina content of 99%. As the alumina content increases, its mechanical strength and electrical insulation properties will also increase accordingly.
Characteristics of Alumina Ceramics
High Hardness: Alumina ceramics have extremely high hardness, which makes it very wear-resistant and suitable for manufacturing abrasive tools and parts that require wear resistance.
Wear resistance: Due to its high hardness, alumina ceramics show excellent wear resistance and are suitable for manufacturing parts for long-term use.
Corrosion resistance: Alumina ceramics have good resistance to most acids and alkalis, making them widely used in the chemical industry.
Good electrical insulation: As an excellent electrical insulating material, alumina ceramics are widely used in electronic and electrical products.
High temperature stability: Ability to withstand extremely high temperatures without significant physical or chemical changes, which makes it an ideal choice for applications in high temperature environments.
Biocompatibility: In the medical field, certain grades of alumina ceramics are used to make medical devices such as artificial joints due to their good biocompatibility.
(OEM High Temperature 96% 99% 99.5% Al2O3 Alumina Precision Ceramics Insulating Spare Parts)
Specifications of OEM High Temperature 96% 99% 99.5% Al2O3 Alumina Precision Ceramics Insulating Spare Parts
OEM High Temperature Alumina Accuracy Ceramics Insulating Spare Parts are designed for requiring industrial applications. These components are made from high-purity Al2O3 (alumina) ceramic material, readily available in 96%, 99%, and 99.5% pureness grades. The material makes certain superb thermal security, electrical insulation, and resistance to use. These buildings make the parts suitable for use in extreme environments with temperature levels reaching up to 1800 ° C.
The 96% alumina ceramic offers a balance of price and efficiency. It gives good mechanical strength and thermal shock resistance. This grade is frequently used in furnace linings, kiln furnishings, and warmth treatment devices. The 99% alumina ceramic delivers greater density and improved deterioration resistance. It is perfect for semiconductor manufacturing, laser elements, and high-voltage insulators. The 99.5% alumina ceramic is the premium option. It includes very little contaminations, exceptional surface area finish, and maximum longevity. This grade is liked in aerospace, medical devices, and accuracy design applications.
All variants exhibit low thermal expansion, making sure dimensional stability under rapid temperature level changes. The dielectric toughness exceeds 15 kV/mm, making them reputable for electric insulation. Hardness levels vary in between 80-90 HRA, supplying resistance to abrasion. The product’s chemical inertness avoids reactions with acids, alkalis, and molten steels.
Custom sizes and shapes are offered to satisfy particular OEM demands. Elements consist of tubes, rods, plates, washing machines, and intricate machined parts. Limited resistances ( ± 0.1 mm or better) are achievable because of innovative sintering and machining procedures. Surface coatings can be brightened or ground for enhanced performance.
Quality control follows strict criteria. Basic material are evaluated for purity and uniformity. Finished products go through assessments for density, porosity, and mechanical buildings. X-ray and ultrasonic screening guarantee internal honesty. Accreditations consist of ISO 9001 and RoHS conformity.
These alumina porcelains are compatible with sectors such as metallurgy, energy, electronics, and chemical processing. They replace metal elements in high-heat areas to lower power loss. Their light-weight nature reduces system lots while preserving architectural reliability. Service life surpasses traditional products, reducing downtime and upkeep expenses.
Product packaging makes use of anti-static and shock-absorbent products to prevent damages during transportation. Custom labeling and mass order choices are readily available. Technical assistance aids with product option and layout optimization. Examples can be attended to screening before major production.
(OEM High Temperature 96% 99% 99.5% Al2O3 Alumina Precision Ceramics Insulating Spare Parts)
Applications of OEM High Temperature 96% 99% 99.5% Al2O3 Alumina Precision Ceramics Insulating Spare Parts
OEM high-temperature 96% 99% 99.5% Al2O3 alumina precision ceramics are utilized extensively in industries requiring strong warm resistance and insulation. These porcelains take care of extreme temperature levels up to 1800 ° C. They stay steady under thermal anxiety. Their high pureness levels mean far better efficiency in severe conditions.
In electronics, these porcelains serve as protecting parts for circuits and sensors. They stop electrical leaks. They manage warmth in gadgets like power modules. Their low thermal expansion protects against cracks during temperature level shifts.
Metallurgical procedures make use of these ceramics for heater linings and thermocouple tubes. They safeguard tools from molten steels. They last much longer than steel parts. This minimizes downtime and maintenance expenses.
The auto market depends on alumina porcelains for spark plugs and sensing units. They make it through high engine temperatures. They withstand wear and chemical rust. This enhances engine efficiency and life expectancy.
Aerospace applications consist of heat shields and engine parts. The porcelains secure components from extreme warm during trip. Their lightweight nature helps in reducing gas use. They keep toughness under stress.
Chemical plants utilize these porcelains for pumps and shutoffs managing corrosive liquids. They withstand acid and antacid strikes. They stop contamination in delicate procedures. This makes sure item purity and safety.
Clinical equipment makes use of alumina ceramics for protecting parts in devices like MRI devices. They offer electrical security. They remain non-reactive in sterile environments. This sustains trustworthy clinical treatments.
Industrial heaters and kilns make use of these porcelains as heating elements and sustains. They disperse warm evenly. They prevent power loss. This increases heating effectiveness and reduces prices.
High-purity 99.5% Al2O3 porcelains match semiconductor production. They make sure clean settings by decreasing fragment launch. They take care of precise processes in chip production.
These porcelains are adjustable in shapes and dimensions. They fit details equipment demands. Their convenience makes them necessary for advanced industrial applications.
Company Introduction
Advanced Ceramics founded on October 17, 2014, is a high-tech enterprise committed to the research and development, production, processing, sales and technical services of ceramic relative materials and products.. Since its establishment in 2014, the company has been committed to providing customers with the best products and services, and has become a leader in the industry through continuous technological innovation and strict quality management.
Our products includes but not limited to Silicon carbide ceramic products, Boron Carbide Ceramic Products, Boron Nitride Ceramic Products, Silicon Carbide Ceramic Products, Silicon Nitride Ceramic Products, Zirconium Dioxide Ceramic Products, Quartz Products, etc. Please feel free to contact us.(nanotrun@yahoo.com)
Payment Methods
T/T, Western Union, Paypal, Credit Card etc.
Shipment Methods
By air, by sea, by express, as customers request.
5 FAQs of OEM High Temperature 96% 99% 99.5% Al2O3 Alumina Precision Ceramics Insulating Spare Parts
What are OEM high-temperature alumina ceramics used for? These parts handle extreme heat and insulation needs. Industries like aerospace, electronics, and manufacturing rely on them. They work in furnaces, sensors, and cutting tools. Their main job is to block heat and electricity while staying stable under stress.
How do 96%, 99%, and 99.5% Al2O3 grades differ? Higher purity means better performance. The 96% grade suits general high-temperature tasks. The 99% and 99.5% grades handle tougher conditions. They resist wear, corrosion, and thermal shock better. Pick higher purity for critical applications needing precision.
Can these ceramics be customized for specific machinery? Yes. OEM parts are made to fit exact sizes and shapes. Manufacturers use advanced molding and machining. This ensures parts match equipment requirements. Custom designs improve efficiency and reduce downtime.
What temperatures can these alumina parts withstand? They handle up to 1750°C (3182°F). Their structure stays stable even with rapid heating or cooling. This makes them ideal for environments where metals or plastics fail.
How do I maintain alumina ceramic components? They need little upkeep. Check for cracks or wear during routine inspections. Clean with non-abrasive methods to avoid surface damage. Their hardness and chemical resistance reduce degradation over time. Proper handling during installation prevents chips or breaks.
(OEM High Temperature 96% 99% 99.5% Al2O3 Alumina Precision Ceramics Insulating Spare Parts)
REQUEST A QUOTE
RELATED PRODUCTS
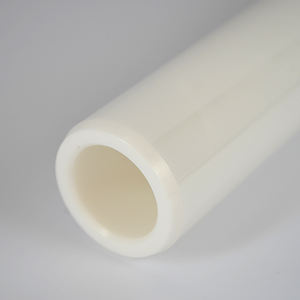
Alumina Ceramic 1000board Ceramic Fiber Board
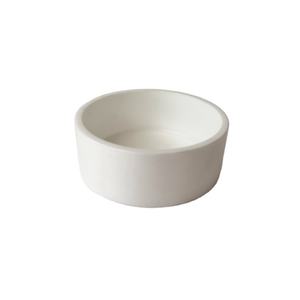
CNC Machining High Strength 99% Alumina Ceramic Spacer Al2O3 Ceramic Part
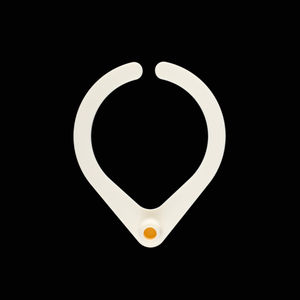
96 Alumina Ceramic Substrate
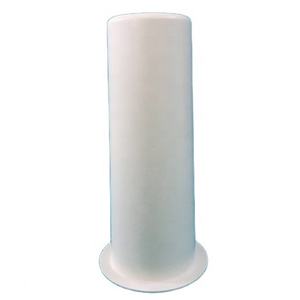
Factory Made 95% Glazed Alumina Ceramic Tube High Temperature Resistance
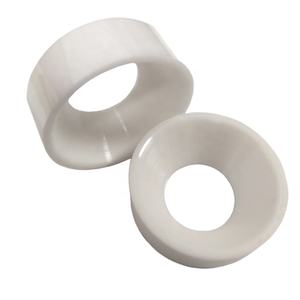
High Quality and Advanced Precision Insulation Ceramics Ceramic Alumina Ceramic Plate
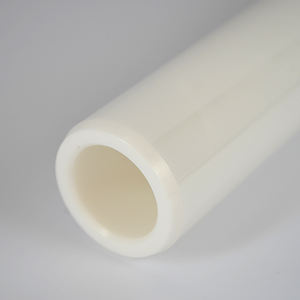