Discover Premium Ceramic Products | Durability & Elegance United | Advanced Ceramics
PRODUCT PARAMETERS
Description
Introduction to Alumina Ceramics
Alumina ceramics are known for their high hardness, wear resistance, corrosion resistance, good electrical insulation and high temperature stability. According to the different alumina content, it can be divided into different grades, such as 95 porcelain, 99 porcelain, etc., among which 99 porcelain refers to ceramic materials with an alumina content of 99%. As the alumina content increases, its mechanical strength and electrical insulation properties will also increase accordingly.
Characteristics of Alumina Ceramics
High Hardness: Alumina ceramics have extremely high hardness, which makes it very wear-resistant and suitable for manufacturing abrasive tools and parts that require wear resistance.
Wear resistance: Due to its high hardness, alumina ceramics show excellent wear resistance and are suitable for manufacturing parts for long-term use.
Corrosion resistance: Alumina ceramics have good resistance to most acids and alkalis, making them widely used in the chemical industry.
Good electrical insulation: As an excellent electrical insulating material, alumina ceramics are widely used in electronic and electrical products.
High temperature stability: Ability to withstand extremely high temperatures without significant physical or chemical changes, which makes it an ideal choice for applications in high temperature environments.
Biocompatibility: In the medical field, certain grades of alumina ceramics are used to make medical devices such as artificial joints due to their good biocompatibility.
(Premium High Alumina Perforated Ceramic Balls for Chemical Processing)
Specifications of Premium High Alumina Perforated Ceramic Balls for Chemical Processing
Premium High Alumina Perforated Ceramic Balls are made for chemical handling applications. These ceramic rounds have 85-95% alumina. They handle severe temperatures approximately 1600 ° C. Their high density guarantees sturdiness in aggressive environments. The perforated design boosts gas or fluid flow in activators or towers. The uniform holes decrease pressure drop. This enhances effectiveness in catalytic processes.
The rounds have low porosity. This stops contamination in delicate responses. They withstand acids, alkalis, and natural solvents. Mechanical toughness is high. They stand up to heavy tons without breaking. Surface solidity reduces abrasion gradually. This prolongs service life contrasted to common ceramic rounds.
Requirement sizes vary from 3mm to 50mm in diameter. Personalized sizes are available. The opening pattern is flexible based on circulation demands. Each round goes through strict quality checks. Measurements, roundness, and opening uniformity satisfy industrial criteria.
These ceramic spheres match packed beds, purification columns, and catalytic changing units. They disperse heat evenly in exothermic or endothermic reactions. The thermal shock resistance protects against damages throughout rapid temperature shifts. They work well in petrochemical, fertilizer, and pharmaceutical markets.
Setup is basic. The rounds fill reactors or towers like traditional packaging materials. Upkeep requirements are low. Routine assessments make certain optimum performance. Replacements are unusual as a result of their wear-resistant homes.
The material structure adheres to environmental laws. No harmful compounds seep during procedure. Recycling alternatives exist for spent balls. This minimizes waste in chemical plants.
Expense efficiency originates from lasting usage. High preliminary financial investment is countered by minimized downtime. Energy savings result from boosted circulation characteristics. Process stability improves product high quality constantly.
Performance data is readily available for certain applications. Technical assistance assists pick the ideal size and configuration. Samples can be examined before mass orders. Preparations differ based upon modification needs. Global shipping guarantees prompt distribution.
This item satisfies the demands of modern-day chemical processing. Dependability and adaptability make it a favored selection for engineers.
(Premium High Alumina Perforated Ceramic Balls for Chemical Processing)
Applications of Premium High Alumina Perforated Ceramic Balls for Chemical Processing
Costs high alumina perforated ceramic balls serve critical roles in chemical processing. These ceramic spheres stand up to severe temperature levels and aggressive chemical settings. Their high alumina material makes sure toughness and resistance to rust. They work well in catalytic activators, distillation columns, and absorption towers. The perforated style permits reliable gas or liquid circulation. This enhances get in touch with in between catalysts and drivers. It additionally reduces stress drop across systems.
These ceramic spheres work as catalyst sustains in chemical reactors. They keep catalysts equally dispersed. This protects against clumping and keeps regular response rates. The openings let gases or liquids travel through without blocking active sites. In stuffed beds, they develop organized layers. This stops smaller fragments from shifting during operation. Their solidity resists wear from continuous rubbing.
High-temperature procedures take advantage of their thermal stability. They deal with abrupt temperature adjustments without cracking. This makes them suitable for changing units or pyrolysis systems. The material does not react with most acids or alkalis. It remains intact in destructive setups like sulfuric acid production. Their reduced thermal growth prevents voids from creating in heated devices.
Contrasted to metal or plastic choices, these ceramic spheres last longer. They reduced downtime for substitutes. Their inert nature stays clear of infecting sensitive chemical streams. Upkeep costs go down as a result of their long service life.
The openings enhance surface area for reactions. They improve heat transfer in exothermic or endothermic processes. This accelerate production cycles. Their uniform shapes and size make sure foreseeable flow patterns. Engineers depend on this uniformity for system style.
These ceramic balls deal with abrasive slurries in damp chemical procedures. They resist erosion from strong fragments in fluid streams. This works in plant food production or wastewater treatment. Their smooth surface area stops fouling. This maintains systems running successfully between cleansings.
Chemical plants utilize them as tower packaging for gas scrubbing up. They improve call in between gases and rubbing liquids. This improves contamination removal rates. Their mechanical stamina sustains hefty tons in high columns.
In recap, costs high alumina perforated ceramic balls optimize chemical handling through integrity, effectiveness, and adaptability. Their style takes on typical market difficulties while lowering operational costs.
Company Introduction
Advanced Ceramics founded on October 17, 2014, is a high-tech enterprise committed to the research and development, production, processing, sales and technical services of ceramic relative materials and products.. Since its establishment in 2014, the company has been committed to providing customers with the best products and services, and has become a leader in the industry through continuous technological innovation and strict quality management.
Our products includes but not limited to Silicon carbide ceramic products, Boron Carbide Ceramic Products, Boron Nitride Ceramic Products, Silicon Carbide Ceramic Products, Silicon Nitride Ceramic Products, Zirconium Dioxide Ceramic Products, Quartz Products, etc. Please feel free to contact us.(nanotrun@yahoo.com)
Payment Methods
T/T, Western Union, Paypal, Credit Card etc.
Shipment Methods
By air, by sea, by express, as customers request.
5 FAQs of Premium High Alumina Perforated Ceramic Balls for Chemical Processing
What are Premium High Alumina Perforated Ceramic Balls used for?
These ceramic balls work in chemical reactors, distillation towers, and catalytic systems. They support catalysts, spread gases or liquids evenly, and protect catalyst beds from damage. Industries like petrochemicals, oil refining, and chemical manufacturing use them for stable, efficient processing.
Why pick high alumina ceramic balls over other materials?
High alumina ceramic balls handle extreme heat and resist chemicals better than metal or plastic options. They stay strong under high pressure, last longer, and reduce downtime. Their hardness prevents wear even in rough conditions.
How do the holes in these ceramic balls help?
The holes let gases or liquids pass through easily. This cuts pressure buildup, boosts contact between materials, and speeds up reactions. The design spreads heat evenly, preventing hot spots that harm catalysts.
What temperatures and chemicals can these balls handle?
They work in temperatures up to 1600°C without breaking down. They resist most acids, alkalis, and solvents. This makes them safe for harsh processes like sulfuric acid production or ammonia synthesis.
How should these ceramic balls be maintained?
Avoid dropping or hitting them during installation. Clean them regularly to remove blockages. Check for cracks or wear during shutdowns. Replace damaged balls quickly to keep the system running smoothly. Pack them tightly in the reactor to prevent shifting.
(Premium High Alumina Perforated Ceramic Balls for Chemical Processing)
REQUEST A QUOTE
RELATED PRODUCTS
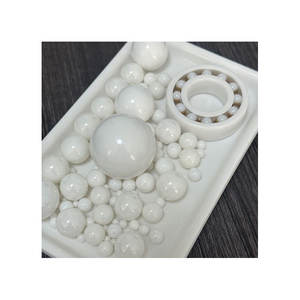
Black 99% Alumina Ceramic Honeycomb Ceramic for Electric Appliance
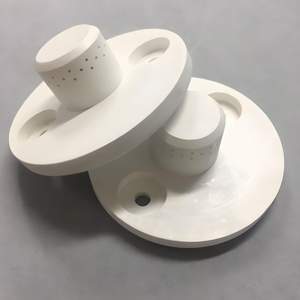
Wear Resistance 99 Alumina Ceramic Tube Porcelain Insulators For
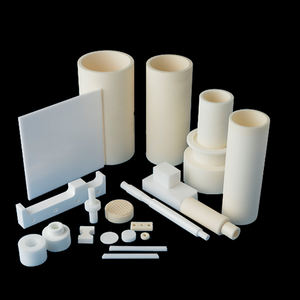
High Quality and Advanced Precision Insulation Ceramics Ceramic Alumina Ceramic Plate
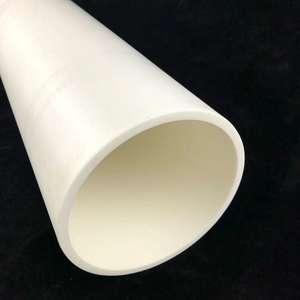
Alumina Ceramic Nails for Furnace Insulation
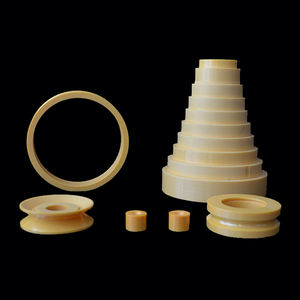
Alumina Ceramic Balls 65% Al2O3 High Temp Resistance for Industrial Furnaces-Heat & Cool Storage
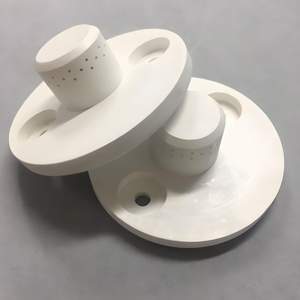