Discover Premium Ceramic Products | Durability & Elegance United | Advanced Ceramics
PRODUCT PARAMETERS
Description
Introduction to Alumina Ceramics
Alumina ceramics are known for their high hardness, wear resistance, corrosion resistance, good electrical insulation and high temperature stability. According to the different alumina content, it can be divided into different grades, such as 95 porcelain, 99 porcelain, etc., among which 99 porcelain refers to ceramic materials with an alumina content of 99%. As the alumina content increases, its mechanical strength and electrical insulation properties will also increase accordingly.
Characteristics of Alumina Ceramics
High Hardness: Alumina ceramics have extremely high hardness, which makes it very wear-resistant and suitable for manufacturing abrasive tools and parts that require wear resistance.
Wear resistance: Due to its high hardness, alumina ceramics show excellent wear resistance and are suitable for manufacturing parts for long-term use.
Corrosion resistance: Alumina ceramics have good resistance to most acids and alkalis, making them widely used in the chemical industry.
Good electrical insulation: As an excellent electrical insulating material, alumina ceramics are widely used in electronic and electrical products.
High temperature stability: Ability to withstand extremely high temperatures without significant physical or chemical changes, which makes it an ideal choice for applications in high temperature environments.
Biocompatibility: In the medical field, certain grades of alumina ceramics are used to make medical devices such as artificial joints due to their good biocompatibility.
(Wear Resistance 99 Alumina Ceramic Tube Porcelain Insulators For )
Specifications of Wear Resistance 99 Alumina Ceramic Tube Porcelain Insulators For
Wear Resistance 99 Alumina Ceramic Tube Porcelain Insulators are engineered for high-performance applications requiring durability and reliability. The product is made from 99% alumina ceramic, ensuring exceptional purity and structural integrity. This composition delivers superior hardness and resistance to abrasive environments, making it ideal for heavy-duty industrial use.
The material’s wear resistance stands out due to its high alumina content. It withstands prolonged friction and mechanical stress without significant surface degradation. This property makes the tubes suitable for machinery parts, cutting tools, and protective sleeves in harsh conditions.
Thermal stability is another key feature. The insulators operate effectively in temperatures up to 1600°C. They resist thermal shock, maintaining performance even under rapid temperature changes. This stability prevents cracking or warping, ensuring long-term functionality in high-heat settings.
Electrical insulation capabilities are critical. The alumina ceramic provides excellent dielectric strength, preventing current leakage in high-voltage environments. This makes the tubes reliable for use in power transmission systems, electronic components, and insulating barriers.
Mechanical strength is prioritized. The tubes exhibit high compressive and flexural strength, handling heavy loads without deformation. Their hardness rating on the Mohs scale exceeds 9, rivaling materials like tungsten carbide. This toughness ensures minimal wear over time, reducing replacement frequency.
Dimensions are customizable. Standard outer diameters range from 5mm to 150mm, with lengths up to 500mm. Wall thickness varies based on application needs, balancing strength and weight. Precision machining guarantees tight tolerances for consistent performance.
Applications span multiple industries. These insulators are used in industrial machinery, semiconductor manufacturing, chemical processing, and aerospace systems. They serve as thermocouple sheaths, furnace linings, and protective housings in corrosive or high-wear environments. Customization options include surface polishing, threaded ends, and specific dimensional adjustments.
The product undergoes rigorous quality testing. Each batch is inspected for density, porosity, and dimensional accuracy. This ensures compliance with international standards for ceramic components. Packaging is designed to prevent damage during shipping, with protective padding and secure stacking.
Material sourcing emphasizes sustainability. High-purity raw materials are selected to minimize environmental impact. Production processes prioritize energy efficiency, aligning with modern industrial sustainability goals.
(Wear Resistance 99 Alumina Ceramic Tube Porcelain Insulators For )
Applications of Wear Resistance 99 Alumina Ceramic Tube Porcelain Insulators For
Wear resistance 99 alumina ceramic tube porcelain insulators are widely used in industries requiring high durability and reliability. These insulators are made from 99% pure aluminum oxide, giving them exceptional hardness and mechanical strength. Their resistance to wear makes them ideal for harsh environments where friction, abrasion, or particle erosion occur.
In industrial machinery, these ceramic tubes protect components like pumps, valves, and bearings from rapid degradation. They handle abrasive slurries in mining or chemical processing equipment. Unlike metal or plastic parts, they maintain shape and function under heavy loads and repeated stress. This reduces downtime and replacement costs.
The electronics and electrical sectors use these insulators for their excellent electrical insulation properties. They prevent current leakage in high-voltage applications like power transmission lines, circuit breakers, and transformers. Their stability at high temperatures ensures safety in devices exposed to heat. They also serve as protective housings for sensors and thermocouples in extreme conditions.
Energy production systems rely on alumina ceramics for thermal and chemical resistance. In oil and gas operations, they withstand corrosive fluids and high-pressure environments. Solar panels and nuclear reactors use them to insulate components exposed to radiation or intense heat. Their low thermal expansion prevents cracking during temperature shifts.
Medical equipment manufacturers use these tubes for their biocompatibility and sterilization resistance. They are found in imaging devices, surgical tools, and laboratory instruments. Their smooth surface resists bacterial growth, meeting strict hygiene standards.
Aerospace and automotive industries apply alumina ceramic insulators in engines and exhaust systems. They tolerate extreme temperatures and reduce wear in moving parts. Their lightweight nature improves fuel efficiency without sacrificing performance.
These insulators are also used in everyday applications like heating elements, kiln furniture, and protective sleeves for industrial lasers. Their versatility comes from combining hardness, thermal stability, and resistance to both chemical and physical wear. Businesses choose them to enhance product lifespan and operational safety across diverse fields.
Company Introduction
Advanced Ceramics founded on October 17, 2014, is a high-tech enterprise committed to the research and development, production, processing, sales and technical services of ceramic relative materials and products.. Since its establishment in 2014, the company has been committed to providing customers with the best products and services, and has become a leader in the industry through continuous technological innovation and strict quality management.
Our products includes but not limited to Silicon carbide ceramic products, Boron Carbide Ceramic Products, Boron Nitride Ceramic Products, Silicon Carbide Ceramic Products, Silicon Nitride Ceramic Products, Zirconium Dioxide Ceramic Products, Quartz Products, etc. Please feel free to contact us.(nanotrun@yahoo.com)
Payment Methods
T/T, Western Union, Paypal, Credit Card etc.
Shipment Methods
By air, by sea, by express, as customers request.
5 FAQs of Wear Resistance 99 Alumina Ceramic Tube Porcelain Insulators For
What are Wear Resistance 99 Alumina Ceramic Tube Porcelain Insulators made of?
They are made of 99% alumina ceramic. This material is high-purity. It gives the insulators strong wear resistance. It also ensures durability in tough conditions. The manufacturing process uses high-temperature sintering. This makes the structure dense and stable.
Where are these insulators commonly used?
They work in electrical systems, chemical plants, and industrial equipment. They protect parts from wear, corrosion, and high heat. Examples include power transmission lines, furnace parts, and machinery in harsh settings. They handle heavy friction and extreme temperatures.
How do these insulators handle high temperatures?
The 99% alumina content lets them resist heat up to 1600°C. They keep their shape and strength even under thermal stress. Their low thermal expansion reduces cracking risks. This makes them reliable for long-term use in hot environments.
What advantages do they have over metal or plastic insulators?
They last longer under wear and tear. Metals can corrode or deform. Plastics melt or degrade. Alumina insulators stay stable. They resist chemicals, electricity, and physical abrasion. This cuts replacement costs and downtime.
How are these insulators installed and maintained?
Installation is simple. They fit into standard setups using brackets or clamps. Check alignment and secure connections during setup. Maintenance is minimal. Clean surfaces regularly to prevent dirt buildup. Inspect for cracks or chips. Replace damaged units quickly to avoid failures.
(Wear Resistance 99 Alumina Ceramic Tube Porcelain Insulators For )
REQUEST A QUOTE
RELATED PRODUCTS
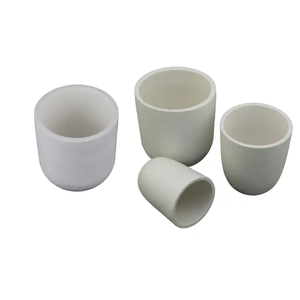
New Product Factory Alumina Ceramic Tube Alumina Ceramic Tubes High Temperature Alumina Tube
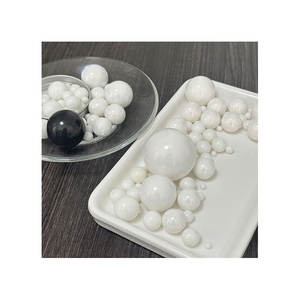
Factory Manufactured 3mm~50mm 99%95%92%alumina Inert Ceramic Ball/sphere
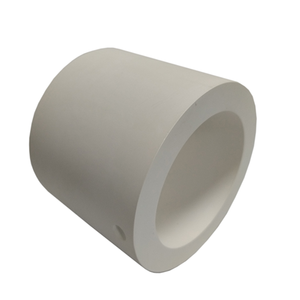
Diameter Size 2mm 19mm 20mm 30mm Grinding Media Alumina Ceramic Balls
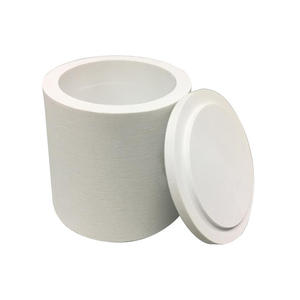
s Custom Alumina Ceramic Tubes Pipes High Temperature Resistant 95% 97% 99% Alumina Industrial Ceramic Tube
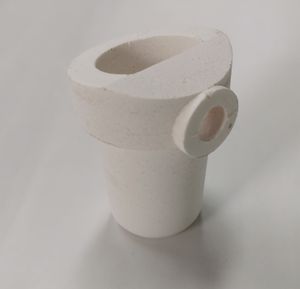
Heat-resistant and Impact-resistant Alumina Ceramics for Sintering Kilns
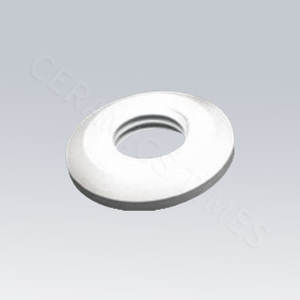