Discover Premium Ceramic Products | Durability & Elegance United | Advanced Ceramics
PRODUCT PARAMETERS
Description
Introduction of Boron Carbide Ceramics
Boron carbide ceramics is an inorganic, non-metallic material with carbon and boron as its main components, and its chemical formula is B4C. Since its discovery in the early 20th century, this material has attracted a great deal of attention because of its unique physical and chemical properties. Boron carbide ceramics have an extremely high hardness, second only to diamond and cubic boron nitride, which makes it important in the field of wear-resistant materials. It also exhibits excellent corrosion resistance, high-temperature stability and low-density properties, attributes that make it ideal for the manufacture of bullet-proof vests, nozzles, bearings and other mechanical components that require high wear resistance. Boron carbide ceramics can also be prepared in a variety of shapes and sizes through different processes to meet the needs of different industries.
Characteristics of Boron Carbide Ceramics
Boron carbide ceramics are known for their excellent performance characteristics, starting with their ultra-high hardness and strength, which makes them resistant to severe abrasion and scratching, making them ideal for use in cutting tools and abrasives. Secondly, the material possesses excellent chemical stability and is less likely to react with chemicals such as acids and alkalis, even in extreme environments, making it widely used in certain key components in the chemical industry. In addition, the superior thermal stability of boron carbide ceramics and their ability to maintain structural and property stability at extremely high temperatures makes them one of the key materials in the aerospace and nuclear industries. Finally, it is worth mentioning its lightweight properties, which, due to its low density, make boron carbide ceramics an ideal option for application scenarios that require light weight but high strength. Together, these characteristics give boron carbide ceramics a wide range of applications.
(Customized High Hardness Boron Carbide B4C Ceramic Block for Sand Mill)
Specification of Customized High Hardness Boron Carbide B4C Ceramic Block for Sand Mill
Our Customized High Solidity Boron Carbide B4C Porcelain Block for Sand Mills provides unrivaled toughness and performance in rough settings. Boron carbide ranks among the hardest products internationally, 2nd only to diamond and cubic boron nitride. This property guarantees phenomenal resistance to wear, making it ideal for sand mills requiring extended procedure with minimal material loss. The ceramic block resists impacts and erosion brought on by high-speed grinding media, keeping architectural stability under severe stress and anxiety.
The item is tailored to fulfill details customer needs. Personalized sizes, forms, and surface coatings are readily available to fit varied sand mill designs. Precision machining assurances tight resistances, making sure smooth assimilation into existing systems. The material’s reduced thickness reduces power consumption throughout milling, improving functional performance.
Boron carbide ceramics master high-temperature atmospheres. They withstand temperatures approximately 1,400 ° C without derogatory, guaranteeing steady performance sought after applications. The material’s chemical inertness stops reactions with acids, antacid, or solvents, making it appropriate for refining corrosive compounds.
A dense, non-porous framework reduces contamination threats during grinding. This attribute is important for markets such as pharmaceuticals or electronics, where item pureness is vital. The ceramic block’s fine-grained microstructure enhances solidity while lowering surface area friction, extending service life.
Production includes innovative sintering techniques to attain high thickness and harmony. Extensive high quality checks validate solidity, crack strength, and dimensional accuracy. The blocks are compatible with upright and straight sand mills, serving sectors such as mining, layers, and chemical handling.
This boron carbide ceramic block minimizes downtime by surpassing conventional products like alumina or silicon carbide. Its combination of solidity, thermal security, and corrosion resistance guarantees trusted operation in rough problems. Consumers benefit from lower substitute expenses and enhanced process consistency.
Applications include grinding pigments, porcelains, and advanced nanomaterials. The item supports great bit size distribution, crucial for high-grade output. Custom-made remedies resolve one-of-a-kind operational challenges, guaranteeing optimum performance throughout diverse commercial settings.
(Customized High Hardness Boron Carbide B4C Ceramic Block for Sand Mill)
Applications of Customized High Hardness Boron Carbide B4C Ceramic Block for Sand Mill
Custom-made high hardness boron carbide (B4C) ceramic blocks are commonly utilized in sand mills due to their phenomenal performance popular commercial environments. Sand mills run by grinding and spreading materials with extreme mechanical action. The components inside face extreme wear from unpleasant particles. Boron carbide ceramic blocks address this difficulty effectively. Their severe firmness ranks amongst the highest of all crafted products. This building minimizes wear even under extended friction.
Sand mills in sectors like paints, finishes, and chemicals rely upon boron carbide obstructs for important components. These include grinding chambers, blades, and liners. These components endure consistent influence and abrasion throughout product handling. Typical metals or other ceramics deteriorate quicker under such problems. Boron carbide extends the life span of these parts. This reduces downtime for substitutes and maintenance. Operational prices drop as a result.
The chemical security of boron carbide includes worth. It withstands corrosion from acids, antacid, and solvents generally utilized in milling processes. This makes certain regular efficiency without contamination. Industries calling for ultra-pure products, such as pharmaceuticals or electronic devices, advantage substantially. The product’s inertness avoids responses with processed substances.
Modification enables boron carbide blocks to fit details sand mill designs. Manufacturers tailor dimensions, shapes, and surface area coatings to optimize grinding performance. Precision-engineered blocks improve bit size circulation in final products. This is vital for attaining uniform high quality in layers or advanced ceramics.
High-temperature resistance further supports boron carbide’s suitability. Sand mills produce warm throughout high-speed procedures. The product preserves architectural honesty even under thermal tension. This avoids bending or cracking that can interrupt manufacturing.
Toughness and dependability make boron carbide obstructs an affordable option for industrial milling. They outperform choices like tungsten carbide or alumina in severe conditions. Business embracing this material see enhanced productivity and reduced waste. The demand for frequent part replacements diminishes. This supports lasting procedures by reducing product consumption.
Company Introduction
Advanced Ceramics founded on October 17, 2014, is a high-tech enterprise committed to the research and development, production, processing, sales and technical services of ceramic relative materials and products.. Since its establishment in 2014, the company has been committed to providing customers with the best products and services, and has become a leader in the industry through continuous technological innovation and strict quality management.
Our products includes but not limited to Silicon carbide ceramic products, Boron Carbide Ceramic Products, Boron Nitride Ceramic Products, Silicon Carbide Ceramic Products, Silicon Nitride Ceramic Products, Zirconium Dioxide Ceramic Products, Quartz Products, etc. Please feel free to contact us.(nanotrun@yahoo.com)
Payment Methods
T/T, Western Union, Paypal, Credit Card etc.
Shipment Methods
By air, by sea, by express, as customers request.
5 FAQs of Customized High Hardness Boron Carbide B4C Ceramic Block for Sand Mill
What are customized high hardness boron carbide B4C ceramic blocks?
Boron carbide B4C ceramic blocks are advanced industrial materials made through high-temperature sintering. They are designed for extreme wear resistance. These blocks are customized in shape, size, and surface finish to fit specific sand mill equipment. Their primary role is to handle intense friction and impact during grinding processes.
Why use boron carbide B4C in sand mills?
Boron carbide is one of the hardest materials available. It outperforms metals and other ceramics in abrasive environments. Sand mills grind particles using high-speed rotating discs. B4C blocks reduce wear on mill components. This extends equipment lifespan. It also maintains consistent grinding efficiency over time.
How are these ceramic blocks customized?
Customization focuses on matching the sand mill’s operational needs. Dimensions are tailored to fit exact machine specifications. Surface treatments like polishing or coatings are added for extra smoothness. Holes, grooves, or threads can be integrated for secure installation. Custom designs ensure optimal performance in specific applications.
Does high hardness affect durability?
Yes. High hardness directly improves durability. B4C blocks resist chipping, cracking, and erosion from abrasive slurries. This reduces maintenance frequency. It also prevents contamination of ground materials. Industries like mining, coatings, and chemicals rely on this durability for long-term cost savings.
How to maintain boron carbide blocks in sand mills?
Maintenance is minimal. Regular inspections check for surface damage or wear. Cleaning removes slurry buildup. Avoid sudden temperature changes to prevent thermal shock. Proper installation ensures even stress distribution. If wear occurs, replacements restore grinding precision. No complex upkeep is needed.
(Customized High Hardness Boron Carbide B4C Ceramic Block for Sand Mill)
REQUEST A QUOTE
RELATED PRODUCTS
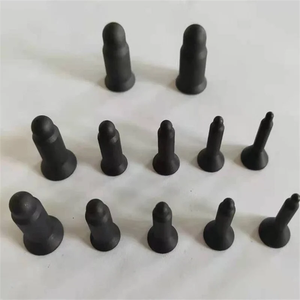
Hot Pressed R400 Single Curved Boron Carbide B4c Ceramic Tile
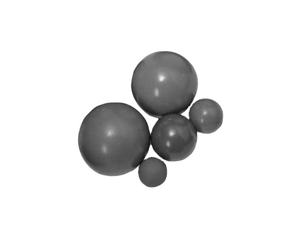
Boron Carbide Venturi Sand Blasting Ceramic Nozzle
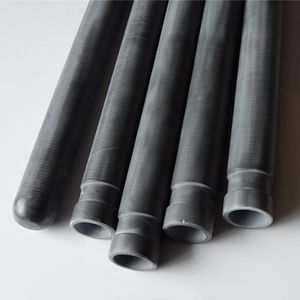
F400 F600 F800 Boron Carbide Powder for Ceramic Einforcement
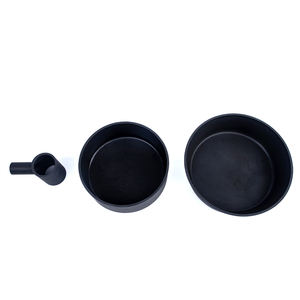
Chinese 45 Micron Boron Carbide Ceramics Nano Boron B4c Powder
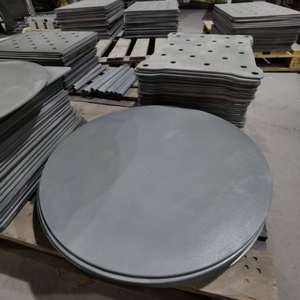
Customized Boron Carbide Sand Blasting B4C Ceramic Nozzle
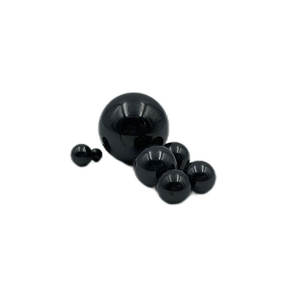